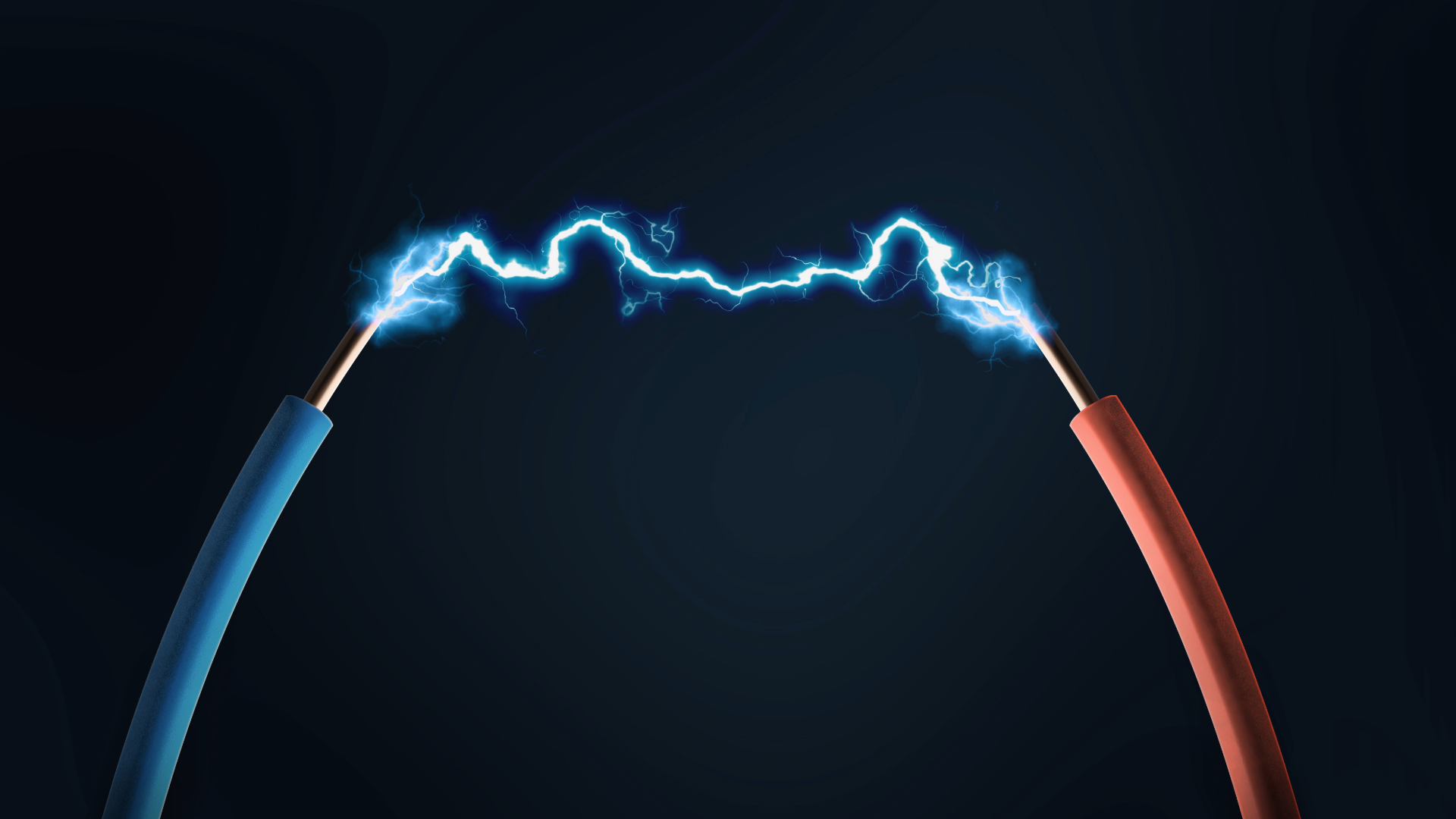
Thermosetting laminates are widely used for electrically insulating components due to their excellent dielectric strength, even under challenging environmental conditions. But how do these materials hold up over time and under continuous electrical stress? This article explores dielectric fatigue testing, shedding light on how these laminates perform over both short and long periods.
What is Dielectric Strength?
Dielectric strength refers to the voltage level at which electrical breakdown occurs in a material. In other words, it is the maximum voltage a material can withstand without failing. Several factors affect dielectric strength, including:
- Material thickness
- Temperature
- Time of voltage application
- Humidity and surrounding conditions
- Frequency and wave shape of the applied voltage
- Electrode size and shape
Short-Term vs. Long-Term Testing
Short-time dielectric tests are commonly used to verify material quality because they are quick and straightforward. These tests measure how much voltage it takes to cause immediate electrical failure.
However, design engineers need to go beyond short-term testing. They want to know:
- How long can an insulating material safely operate under voltage without breaking down?
- What voltage levels are sustainable over time?
Understanding long-term dielectric endurance helps engineers design reliable components. While short-time test data offers a snapshot of performance, endurance testing provides insights into dielectric fatigue—the gradual deterioration of material strength under repeated electrical stress.
Experimental Setup and Methodology
Our study examines how dielectric fatigue impacts five ANSI/NEMA material grades under both dry and moist atmospheres. The materials used were cut into 6” x 6” test plaques with a thickness of 0.062 inches and tested at 73°F. Two of the grades were also tested after being conditioned in high humidity and warm water. Below is a summary of the conditioning and testing process:
Specimen Conditioning:
- Test plaques were dried at 220°F for one hour.
- After drying, they were cooled to 73°F in a desiccator.
Short-Time Testing:
- Three specimens of each material grade were tested using ASTM D149 standards.
- Specimens were immersed in an oil bath with electrodes placed perpendicular to the laminations.
- Voltage was applied at 10 kV per second until electrical failure occurred.
Long-Term Dielectric Fatigue Testing:
- Additional specimens were tested at reduced voltage levels—targeting 85%, 70%, 60%, 55%, 50%, and 45% of their short-time breakdown values.
- These voltages were applied until the material failed, and the time to rupture was recorded.
Key Findings from the Fatigue Tests
The study revealed several important trends:
- Short Time to Failure: At higher voltages (above 60% of the short-time breakdown level), failure occurred within seconds.
- Rapid Increase in Endurance: When voltage levels dropped to 60% or below, the time to failure extended significantly—sometimes taking hours or even days.
- Threshold for Long-Term Stability: If a specimen did not fail within 100 minutes, it often remained stable for days or weeks under the same conditions.
These findings suggest that lowering operational voltage significantly increases the endurance of insulating materials. For engineers, this highlights the importance of operating below the critical voltage threshold to ensure long-term reliability.
Results Summary for Different Material Grades
The graph in Figure 1 (referenced separately) shows the fatigue test data for the following ANSI/NEMA material grades:
- X, XX, XXXP, LE, and G5
These materials exhibited similar trends, though slight variations were observed depending on humidity conditioning and material composition.
Implications for Components Fabricated from Thermosetting Laminates
The behavior of thermosetting laminates in tubes, rods, and molded parts aligns with the trends observed in sheet materials. However, slight differences in performance can occur due to variations in construction and shape. These findings emphasize the need for customized testing when designing insulating components with non-sheet materials.
Applications and Practical Takeaways
Dielectric fatigue testing plays a crucial role in industries that rely on high-performance insulating materials, such as:
- Aerospace: Ensuring long-term electrical insulation in critical systems.
- Power Systems: Designing transformers and switchgear components with reliable dielectric properties.
- Electric Vehicles: Optimizing insulation in battery systems and power electronics.
By identifying the safe operating voltage thresholds, engineers can avoid premature material failures and extend the service life of critical components.
Future Work
This study highlights the importance of long-term dielectric endurance testing for thermoset laminates. While short-time tests are useful for quality control, endurance tests provide critical insights for reliable component design. Future research should explore additional variables, such as frequency effects and more extreme environmental conditions.
Understanding how composite materials behave under real-world stress ensures that components maintain their insulating performance over time, helping industries avoid costly downtime and failures.
Summary of Key Points
- Short-term dielectric tests are useful for quality verification, but long-term endurance tests reveal critical information about component reliability.
- Operating below 60% of short-time breakdown voltage can significantly extend the material’s lifespan.
- Customized testing is needed for components made from tubes, rods, and molded parts, as their performance may vary from sheet materials.