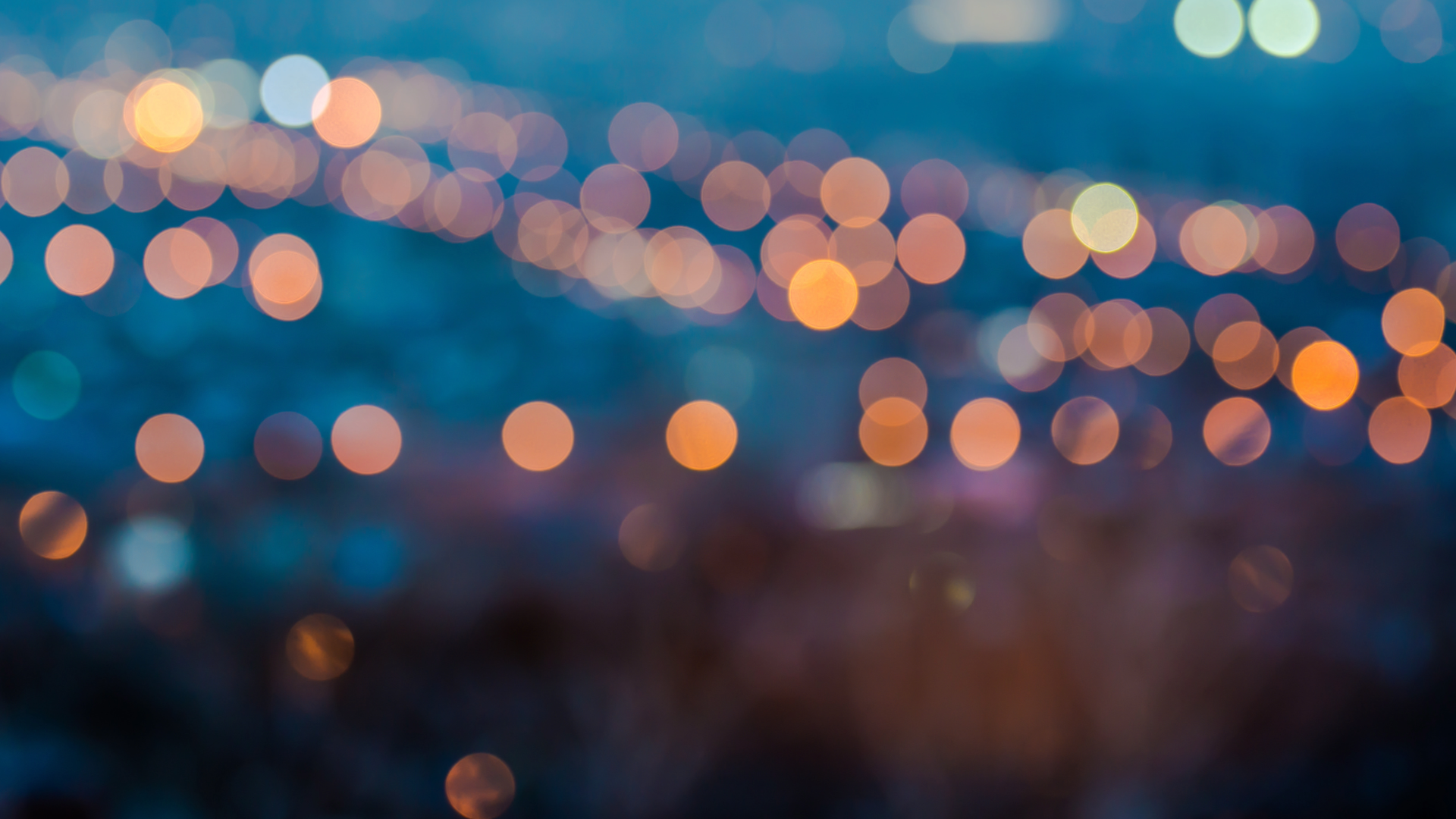
Outgassing is a crucial phenomenon in the world of materials science, especially for thermoset composites used in extreme environments like aerospace and space technology. Simply put, outgassing refers to the release of gases from materials under certain conditions. When thermoset composites, which are commonly used for their strength and durability, experience reduced pressure or high temperatures, they can emit trapped gases. Here’s an approachable look at what outgassing is, why it matters, and how it impacts thermoset composites in challenging applications.
KEY TAKEAWAYS
- Outgassing in thermoset composites can impact structural stability and performance, especially in extreme environments like space and aerospace applications.
- Key contributors to outgassing include the material’s composition, manufacturing process, and environmental conditions, such as high heat or reduced pressure.
- Testing and standards help determine whether a material’s outgassing is within acceptable limits, safeguarding sensitive equipment from contamination or interference.
- Mitigation strategies, like material selection and optimized manufacturing, can reduce outgassing risks and ensure thermoset composites maintain their integrity in demanding conditions.
What is Outgassing?
Outgassing occurs when gases escape from a solid or liquid, typically due to exposure to low pressure or high temperatures. In the case of thermoset composites, this can happen in several ways:
- Surface vaporization: The top layer of the composite material releases gases.
- Desorption: Gases that were previously absorbed on the surface are released.
- Diffusion: Gases move from within the material to its surface.
- Permeation: Gases pass through the material itself.
Why Does Outgassing Occur?
Outgassing in thermoset composites can be influenced by several factors:
- Manufacturing Process: Small amounts of water vapor or other gases can become trapped during production.
- Environmental Conditions: In space or high-temperature settings, the pressure and heat conditions can trigger outgassing.
- Material Composition: Different types of filaments and resins have different outgassing properties, impacting how much gas a material might release over time.
How is Outgassing Measured?
Engineers measure outgassing through standardized tests like ASTM E595, which assesses materials used in space environments. These tests focus on three main indicators:
- Total Mass Loss (TML): The percentage of a material’s mass lost due to outgassing.
- Collected Volatile Condensable Materials (CVCM): The portion of outgassed materials that condenses on a cooler surface, often a critical factor for sensitive equipment.
- Water Vapor Regained (WVR): The amount of moisture reabsorbed after testing.
For aerospace applications, a material is generally considered suitable if it has a CVCM ≤ 0.10% and TML ≤ 1.00%.
Why Does Outgassing Matter?
Outgassing can impact thermoset composites and the systems that rely on them in a few significant ways:
Dimensional Instability: When gases escape, it can cause small changes in the material’s structure, which is critical in precision components like satellite optical systems.
Performance Degradation: Outgassed materials can deposit on sensitive surfaces, potentially interfering with the performance of nearby components or instruments.
Material Properties Alteration: The release of volatile elements can change the thermal or mechanical properties of the composite, impacting its durability and reliability.
Reducing Outgassing: What Engineers Can Do
To minimize outgassing, engineers use various strategies:
- Material Selection: Choosing materials specifically designed to have low outgassing properties.
- Manufacturing Optimization: Adjusting production processes to reduce the likelihood of trapping gases.
- Post-Curing or Pre-Conditioning: Applying treatments that remove trapped gases before the material is used.
- Design Considerations: Accounting for potential dimensional shifts during the design phase.
Minimizing the Threat of Outgassing
Outgassing is a natural phenomenon that requires careful attention in high-stakes applications. By understanding its causes, effects, and mitigation strategies, engineers can ensure thermoset composites perform as expected, even in the most extreme environments. For industries like aerospace and space technology, this knowledge helps maintain the reliability and functionality of mission-critical components, safeguarding both equipment and performance.