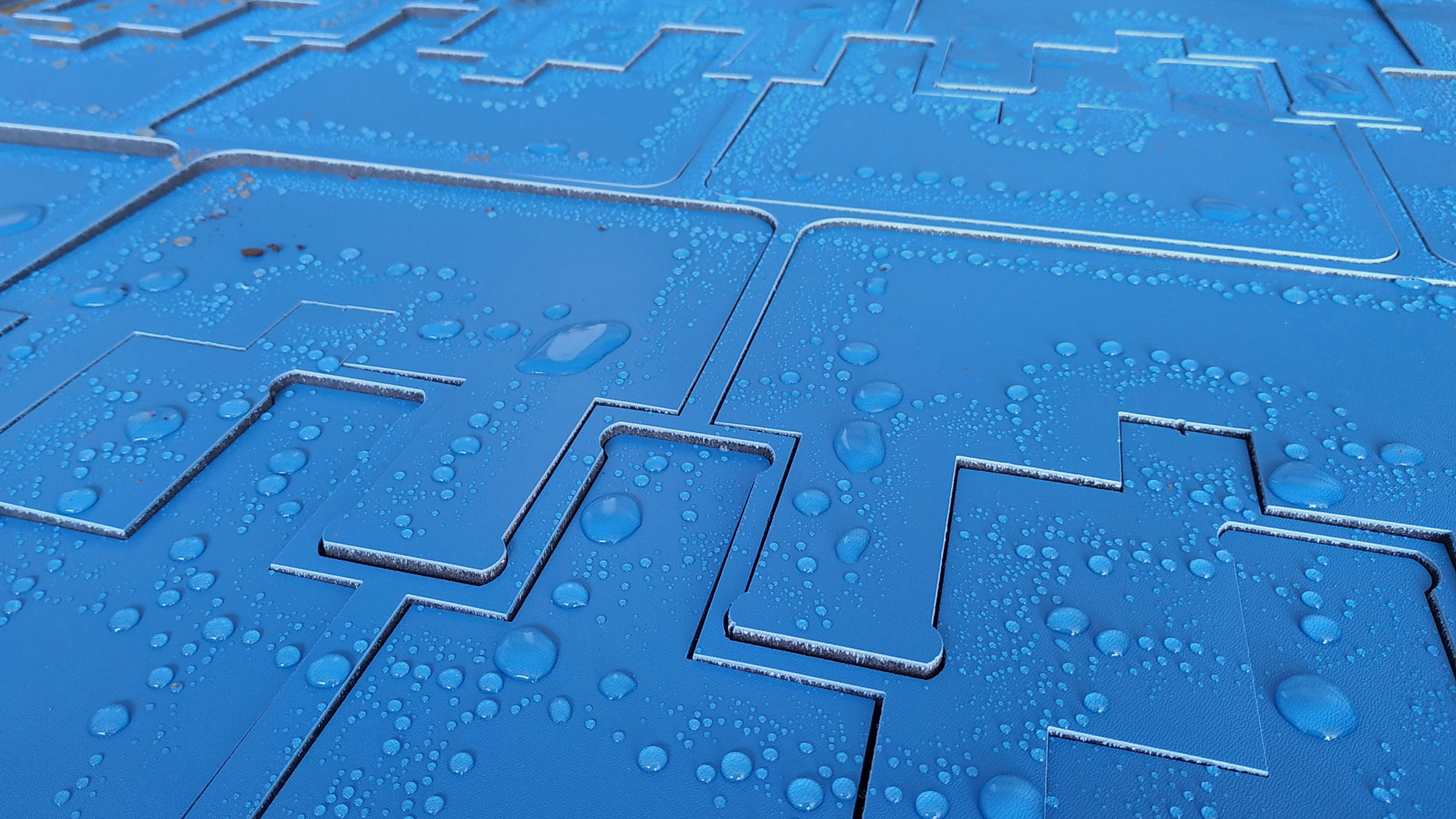
Building Trust and Loyalty Through a Reliable Thermoset Supply Chain
In the fast-paced world of manufacturing, consistency is king. For plastics distributors and OEMs, a reliable thermoset supply chain isn’t just a convenience—it’s essential to operational success. When production hinges on the availability of composite materials, even minor delays can ripple through a supply chain, resulting in costly downtime, missed deadlines, and strained customer relationships.
At Atlas Fibre, we understand that reliability is more than just delivering materials on time. It’s about creating a seamless experience and process that ensures quality, transparency, and adaptability at every step. By prioritizing supply chain dependability, we’ve built lasting relationships with plastics distributors who trust us to support their growth and protect their reputations.
The Critical Role of Supply Chain Reliability
Plastics distributors operate in an environment where precision and predictability matter. Disruptions in material supply can jeopardize not only production schedules but also the performance and quality of the end products. When fabricators and OEMs depend on thermoset materials to meet stringent industry standards, the margin for error is slim.
A reliable thermoset supply chain mitigates these risks by ensuring that materials are consistently available, meet exact specifications, and are delivered punctually. For plastics distributors, this translates to uninterrupted production cycles and the ability to meet client demands with confidence. When distributors have access to high-quality thermoset composites, they can pass that reliability down the line, reinforcing their own value proposition to customers.
How Atlas Fibre Ensures Supply Chain Reliability
Vertical Integration for Full Control: Atlas Fibre’s vertically integrated operation allows us to oversee every stage of the production process, from sourcing raw materials to final fabrication. This control minimizes the likelihood of bottlenecks, enhances lead times, and ensures consistency across batches.
By managing production in-house, we eliminate dependency on external suppliers, reducing potential supply chain vulnerabilities. For distributors, this means predictable access to the sheets, rods, and tubes they need without unexpected disruptions.
Transparent Communication and Real-Time Performance Tracking: We believe that transparency is a cornerstone of trust. Atlas Fibre’s RPM (Repeat Production Maximization) model offers plastics distributors real-time insights into production performance and supply chain activity. This level of visibility not only allows for better planning but also fosters a collaborative relationship where potential issues are addressed before they impact delivery.
By keeping distributors informed every step of the way, we create a more proactive and responsive supply chain, reinforcing trust and loyalty through consistent performance.
Inventory Management and Demand Forecasting: Anticipating customer needs is key to maintaining supply chain reliability. At Atlas Fibre, we stock a wide range of thermoset composite materials to ensure quick fulfillment, even for complex or high-volume orders. Our forecasting systems analyze past demand patterns and market trends, enabling us to adjust inventory in preparation for future needs.
For plastics distributors, this forward-looking approach eliminates long lead times and ensures that critical materials are always available when needed.
The Link Between Reliability and Long-Term Loyalty
Reliability is more than a transactional benefit—it’s a foundation for lasting loyalty. Plastics distributors are more likely to return to a supplier they know they can count on. Consistent quality, dependable deliveries, and proactive communication create a relationship that extends beyond individual orders.
Moreover, when distributors can rely on Atlas Fibre’s supply chain, they can, in turn, position themselves as reliable partners to their own customers. This trust cascades through the supply chain, strengthening the distributor’s reputation and fostering deeper client relationships.
A Competitive Advantage Beyond Pricing
While competitive pricing is always a factor, supply chain reliability offers plastics distributors a differentiator that goes beyond cost. In industries where downtime or quality lapses carry significant financial implications, the value of dependable material supply often outweighs the marginal savings from lower-cost suppliers.
Atlas Fibre’s commitment to reliability allows distributors to focus on growth and client service without the distraction of material shortages or delays. By aligning with our supply chain, distributors gain not just a vendor, but a strategic resource capable of supporting their long-term success.
Building for the Future
As the manufacturing landscape continues to evolve, supply chain resilience will become even more critical. Atlas Fibre is committed to continuously refining our processes and expanding our capabilities to stay ahead of industry demands. Our goal is to provide plastics distributors with the stability and confidence they need to thrive in competitive markets.
For distributors seeking a supply chain partner they can depend on, Atlas Fibre stands ready to deliver precision without compromise—consistently, reliably, and with the future in mind.