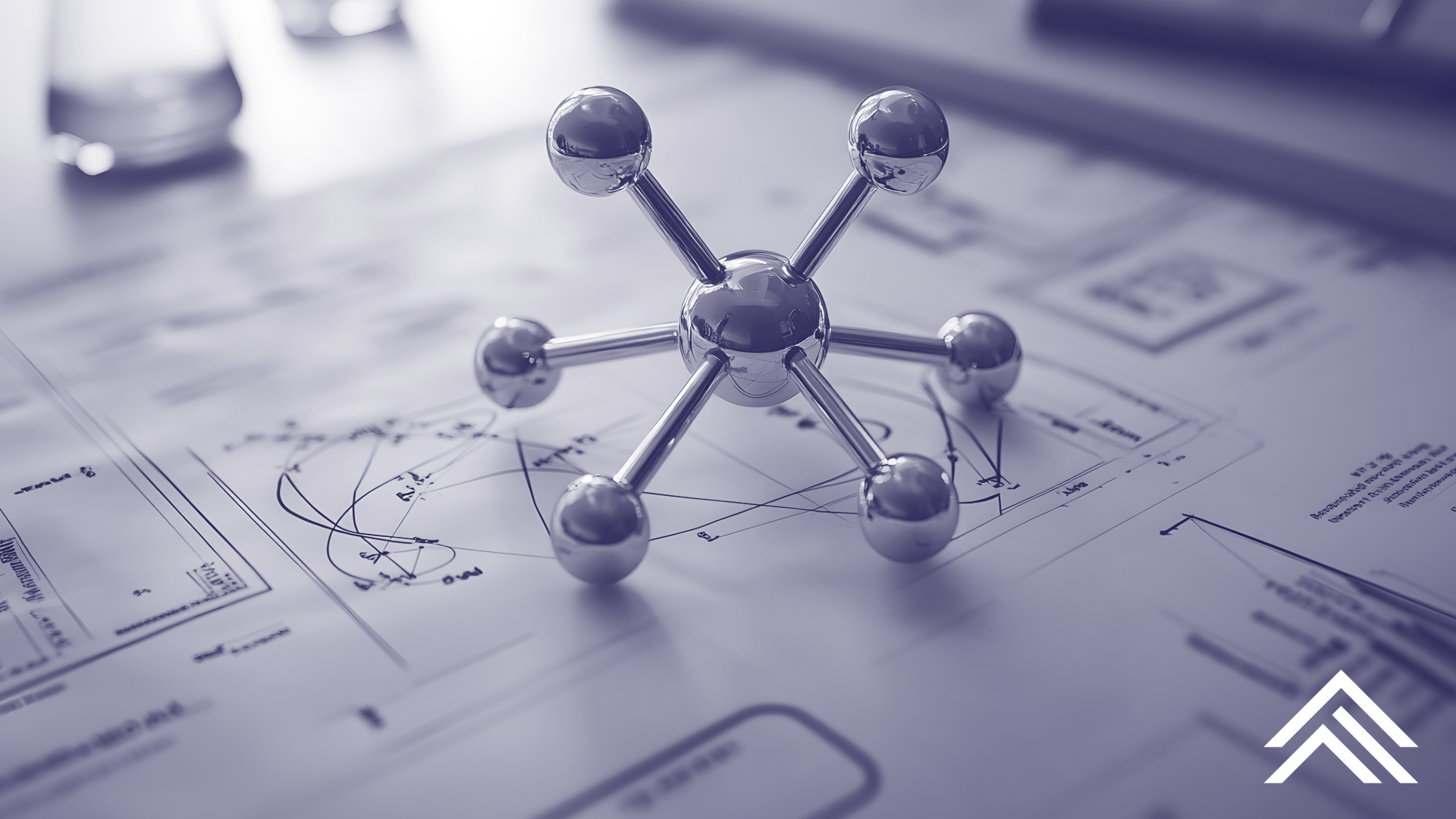
For decades, metal has been the foundation of manufacturing, engineering, and industrial applications. However, as industries demand stronger, lighter, and more efficient materials (compare material properties here), thermoset composites have emerged as a superior alternative.
Unlike metals, which are often limited by weight, corrosion, and mechanical fatigue, thermoset composites provide exceptional strength, durability, and resistance to environmental stresses. As companies seek better performance and long-term cost savings, these materials are proving to be the smarter choice.
Lighter and Stronger for Greater Efficiency
One of the biggest advantages of thermoset composites is their high strength-to-weight ratio. While metals such as steel and aluminum provide durability, they are significantly heavier, which can limit efficiency in transportation, aerospace, and industrial applications.
By using thermoset composites, manufacturers can achieve the same level of strength at a fraction of the weight. In industries such as automotive and marine, reducing weight leads to improved fuel efficiency, higher payload capacity, and easier handling. The ability to maintain structural integrity while being lightweight allows engineers to design more efficient, high-performance components that wouldn’t be possible with metal alone.
Corrosion and Chemical Resistance for Longer Lifespans
Metals are highly susceptible to corrosion, rust, and oxidation, which weakens their structure over time. Even with protective coatings, exposure to moisture, saltwater, and harsh chemicals can lead to degradation, costly maintenance, and reduced reliability.
Thermoset composites, on the other hand, do not corrode and remain stable in extreme environments. This makes them ideal for marine applications, chemical processing plants, and infrastructure exposed to the elements. Materials such as phenolic laminates are widely used in high-corrosion environments because of their ability to withstand chemical exposure without breaking down.
By eliminating the risk of rust and chemical degradation, thermoset composites offer a longer service life with less need for repairs or replacements, making them a smarter investment for industries that prioritize durability.
Heat Resistance and Dimensional Stability
One of the fundamental challenges with metals is their susceptibility to heat expansion and warping. Under high temperatures, metal components can weaken, deform, or lose structural integrity, leading to failures in critical applications.
Thermoset composites, however, maintain dimensional stability across a wide range of temperatures. This makes them particularly valuable in environments where thermal resistance is essential, such as automotive engine components, aerospace interiors, and industrial insulation.
Unlike metals, which require additional heat treatments or reinforcements to withstand high temperatures, thermoset composites naturally provide superior resistance to thermal stress, ensuring reliable performance even in extreme conditions.
Exceptional Fatigue Resistance for Long-Term Durability
Metals are prone to fatigue failure, especially under repeated stress. Over time, constant mechanical loads can cause cracks, deformation, or complete material failure, leading to unexpected downtime and costly replacements.
Thermoset composites, in contrast, have a rigid molecular structure that resists fatigue and wear far better than metals. This makes them particularly effective in high-vibration applications such as rail systems, industrial machinery, and structural components that endure repeated mechanical stress.
By offering better fatigue resistance and longer-lasting durability, thermoset composites reduce the risk of material failure, ensuring greater reliability and lower long-term costs.
Electrical Insulation and Fire Resistance for Safer Applications
One of the unique properties of thermoset composites is their non-conductive nature, making them a superior choice in electrical and electronic applications. Metals, by contrast, require additional insulation and protective measures to prevent electrical conductivity risks.
Thermoset composites are widely used in power transmission, circuit boards, and electrical enclosures, where electrical insulation is essential for safety. Additionally, certain thermoset materials, such as phenolic and epoxy laminates, are naturally flame-resistant, making them a preferred option for fire-resistant applications in aerospace, mass transit, and industrial settings.
By combining electrical insulation and fire resistance, thermoset composites provide greater protection in high-risk environments, reducing the chances of failure due to heat or electrical hazards.
Cost-Effective Manufacturing with Greater Design Flexibility
Metals require multiple machining, welding, and finishing processes, all of which add cost and complexity to manufacturing. Thermoset composites, on the other hand, can be molded into complex shapes in a single step, significantly reducing production time and costs.
This flexibility allows manufacturers to:
- Eliminate the need for secondary machining
- Reduce assembly costs by consolidating multiple parts into one
- Create intricate, lightweight designs that would be difficult or impossible with metal
Since thermoset composites do not require welding or fasteners, manufacturers can develop seamless, structurally optimized components that improve efficiency while minimizing material waste. The ability to produce customized, high-performance parts at a lower cost makes thermoset composites an attractive choice for industries that rely on precision and efficiency.
Expanding Use Across Industries
Thanks to their lightweight strength, durability, and resistance to harsh environments, thermoset composites are being rapidly adopted across aerospace, automotive, energy, and infrastructure sectors.
In automotive manufacturing, thermoset materials are used in everything from body panels to under-the-hood components to reduce weight while maintaining impact resistance. In construction, glass fiber-reinforced composites are increasingly being used in bridges, pipelines, and industrial structures, providing corrosion-resistant, long-lasting alternatives to traditional steel and concrete.
Even the renewable energy sector has embraced thermoset composites, using them in wind turbine blades and solar panel supports, where their strength-to-weight advantage improves efficiency and longevity.
The Future of High-Performance Materials
The shift from metals to thermoset composites is more than a trend—it is a fundamental transformation in materials engineering. As industries demand lighter, stronger, and more cost-effective solutions, thermoset composites continue to push the boundaries of what is possible.
Their unmatched combination of strength, thermal stability, corrosion resistance, and design flexibility makes them the material of the future. Whether in transportation, infrastructure, or energy, thermoset composites are proving to be more than just an alternative to metals—they are the next generation of high-performance materials.