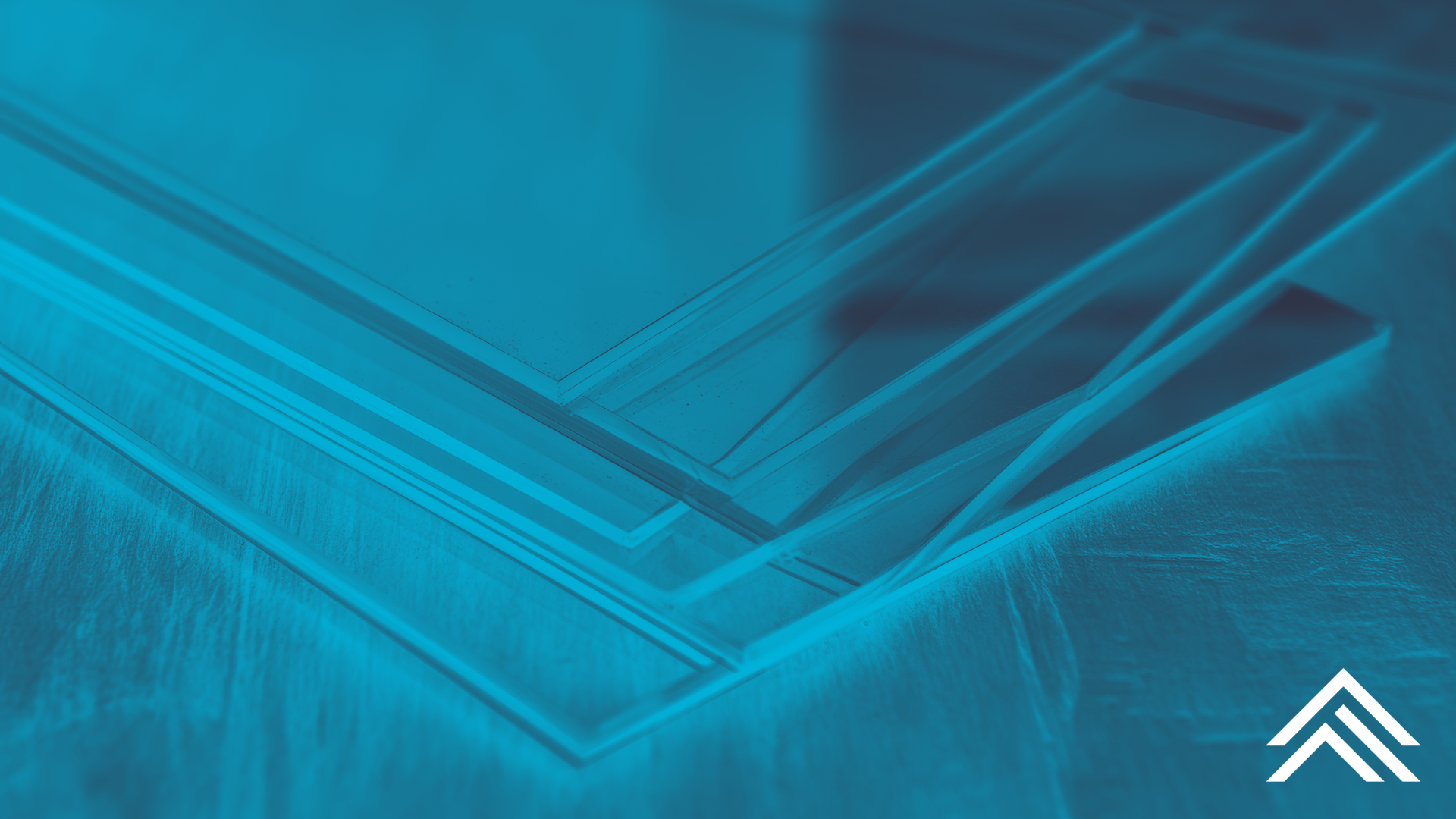
Selecting the right material is one of the most critical steps in manufacturing precision components. Whether you’re machining parts for aerospace, defense, industrial equipment, or high-performance electrical applications, understanding the physical and mechanical properties of thermoset composite materials can make or break your project.
At Atlas Fibre, we’ve developed a Comparative Data Sheet that puts key material specs side by side, giving engineers and sourcing professionals the hard numbers they need to make informed decisions. But what do these properties actually mean in practical terms? Here’s a breakdown of the specifications and why they matter in real-world applications.
Key Material Properties and Why They Matter
Understanding key material properties is essential for selecting the right thermoset composite for your application. From strength and hardness to electrical performance and thermal stability, these properties determine how a material will perform under real-world conditions, ensuring durability, machinability, and compliance with industry standards.
Specific Gravity: Specific gravity measures density relative to water. Lower values mean a lighter material—crucial in weight-sensitive applications like aerospace and automotive, where every ounce counts.
Tensile Strength: Indicates how much pulling force a material can handle before it fails. If your parts see high tension loads—think fasteners, brackets, or structural supports—you want a material with a high tensile strength. Read more about tensile strength.
Compressive Strength: How much force can a material take before it crushes? For load-bearing parts, like bases, mounts, or spacers, high compressive strength prevents failure under extreme stress.
Flexural Strength: A material’s ability to withstand bending forces without breaking. This is a key factor for machined components that experience flexing, such as housings, covers, and enclosures. Read more about the flexural strength of thermoset composite laminates.
Hardness: The higher the hardness rating, the more resistant a material is to wear, scratching, and indentation. If your parts see high friction—like sliding surfaces or wear plates—you’ll need a material with superior hardness.
Bond Strength: For laminated composites, bond strength measures how well the layers hold together. If delamination is a concern, particularly in multi-layer electrical insulation or structural components, bond strength is critical.
Shear Strength: How much force can a material handle before its layers slide apart? If your parts will experience complex loads—like in structural assemblies or fastened joints—high shear strength prevents failure.
Dissipation Factor: For electrical applications, the dissipation factor measures how much energy a material loses when exposed to an electric field. The lower the value, the better the insulation.
Dielectric Constant: Also known as relative permittivity, this property determines how well a material stores electrical energy. It’s crucial for dielectric applications in circuit boards, transformers, and other electrical components.
Electric Strength: This is the max voltage a material can withstand before breaking down. If you’re working with high-voltage applications, electric strength is a critical safety metric.
Flammability Rating: Some materials self-extinguish, while others can sustain combustion. If you’re machining parts for aerospace, defense, or transportation, flammability ratings must be considered for compliance and safety. Learn more about the flammability rating of composites.
Max Operating Temperature: At what temperature does the material maintain its mechanical and electrical properties? If your parts will be exposed to extreme heat—such as in high-temperature industrial or electronic environments—this spec is critical for longevity.
Coefficient of Thermal Expansion (CTE): Materials expand and contract with temperature changes. If your application has tight tolerances or requires stability under temperature fluctuations, a low CTE is essential.
Water Absorption: Moisture can degrade material properties over time. If your components are exposed to humidity or outdoor conditions, choosing a low-absorption material ensures dimensional stability and performance.
IZOD Impact Strength: This measures how much energy a material can absorb before it fractures upon impact. If your parts experience sudden forces—like machine guards or aerospace components—high impact strength is a must.
Why This Matters for Machining and Performance
Thermoset material selection isn’t just about specs—it’s about ensuring performance in the real world. The right thermoset composite can mean the difference between a part that lasts and one that fails prematurely. By understanding these properties, you can optimize material selection for machining efficiency, mechanical performance, and cost-effectiveness.
Download the Comparative Data Sheet
Want to see how different materials stack up? Download Atlas Fibre’s Comparative Data Sheet for a full breakdown of physical and mechanical properties. Whether you need maximum strength, high heat resistance, or precision tolerances, this resource helps you make the right call.
Need additional information? Connect and consult with Atlas Fibre’s material and machining specialists.