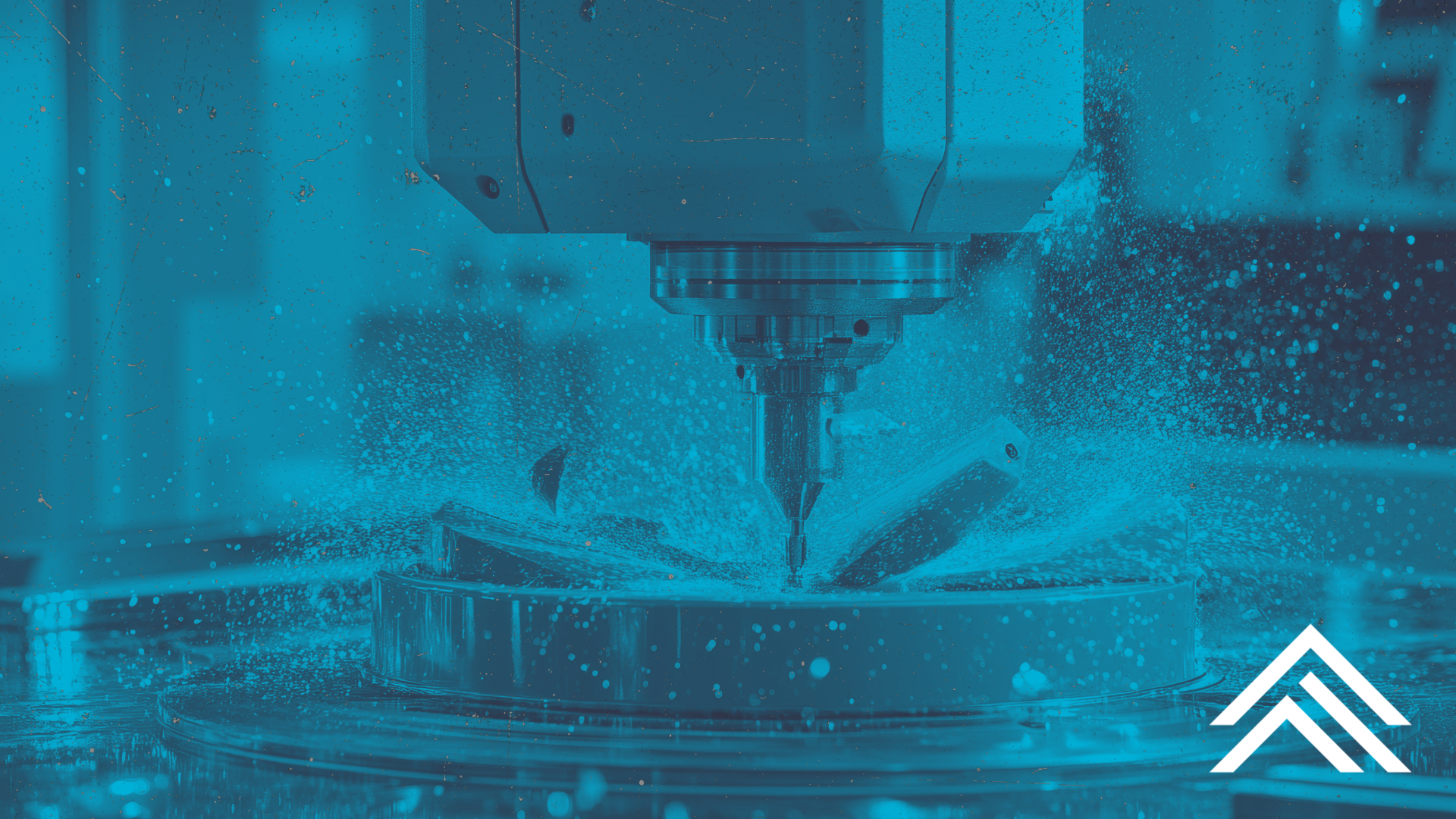
Integrating Material-Specific Considerations in CNC Machining
Five-axis milling stands at the forefront of modern machining, offering unprecedented flexibility and precision compared to traditional three-axis operations.
Through the integration of advanced tool path optimization techniques, manufacturers can significantly improve machining efficiency, surface quality, and tool longevity. However, the choice of material—particularly when machining thermoset composite laminates—plays a crucial role in shaping these optimization strategies. This article explores both the innovative methods used in five-axis milling and how material-specific factors influence these approaches.
Advanced Tool Path Optimization Techniques
Modern five-axis milling leverages a suite of advanced techniques designed to streamline machining processes and enhance outcomes. Key methods include:
Guiding Curves
By following the natural flow of a part’s surface topography, guiding curves generate smoother tool paths that reduce machining time and enhance surface finish. This technique is especially valuable for free-form surfaces where traditional linear movements might lead to uneven finishes or increased tool wear.
3-to-5 Axis Tilt
This method allows programming in a conventional 3-axis mode while the system automatically adjusts the tool vector in real time to avoid collisions. Using shorter tools and more aggressive cutting, this technique reduces vibration and improves the quality of the machined surface.
Multi-Axis Adaptive Roughing
Maintaining a constant cutting force is critical, particularly when working with challenging materials. Multi-axis adaptive roughing adjusts the tool path automatically to maintain a uniform chip load, which not only promotes smoother cutting but also increases productivity—vital when machining materials with variable properties.
Curvature Matching
Curvature matching optimizes tool orientation by aligning the curvature of the cutting tool with that of the workpiece. This dynamic adjustment minimizes engagement issues and reduces surface imperfections, ensuring a superior finish, especially on complex free-form surfaces.
Arc-Length Parameterized NURBS Tool Path Generation
Using Non-Uniform Rational B-Spline (NURBS) curves allows for highly accurate and efficient tool paths. Parameterizing these curves by arc length ensures the generated path closely mirrors the true shape of the part, which is particularly beneficial for precision 3-axis curve milling.
Spatial Optimization
Focusing on the three-dimensional dynamics of the machining process, spatial optimization employs advanced algorithms to minimize non-productive movements and avoid potential collisions. This holistic approach ensures that tool paths are not only efficient but also safe, maximizing overall productivity.
Impact of Material Choice: The Case of Thermoset Composite Laminates
When machining thermoset composite laminates—materials widely used for their strength, durability, and lightweight properties—several material-specific factors must be considered to further refine tool path optimization strategies.
Mechanical Properties: Thermoset composites such as glass epoxy (e.g., NEMA Grades FR4, G-10, G-11) and glass silicone (e.g., NEMA Grade G-7) exhibit varying mechanical strengths. These differences dictate adjustments in milling parameters and tool path strategies, as each material may require a unique approach to balance cutting forces and tool wear.
Heat Sensitivity: Although thermoset materials do not melt under high temperatures, they do display varying degrees of heat sensitivity. Five-axis milling strategies must be tailored to manage heat generation and dissipation effectively—often necessitating optimized cutting speeds and feed rates to maintain material integrity and prevent thermal damage.
Fiber Orientation: Many thermoset composites incorporate fiber reinforcements, and the orientation of these fibers (such as in glass mat substrates found in low-pressure laminates) significantly impacts machining outcomes. Optimized tool paths must account for fiber direction to minimize delamination and achieve the best possible surface finish.
Resin System: The type of resin used in a composite (epoxy, melamine, silicone, etc.) affects machinability. Milling strategies need to be adjusted accordingly to optimize tool life and ensure high-quality parts. Variations in resin properties may require changes in cutting speed, feed rates, or even the choice of tool path technique.
Filler Additives: Fillers and additives, often introduced to improve flame retardance or resistance tracking, can alter the material’s behavior during milling. These changes necessitate further adjustments in tool path planning to accommodate variations in chip formation and cutting dynamics.
Surface Finish Requirements: Different thermoset composites may demand distinct surface finish qualities. Techniques such as guiding curves and curvature matching become even more critical in these cases, as they can be specifically tuned to achieve the desired finish while optimizing the overall tool path.
Tool Selection: The physical properties of thermoset composites influence not only the machining parameters but also the selection of cutting tools. Tool geometry and material must be chosen to complement the specific characteristics of the laminate, thereby enhancing both tool performance and part quality.
Chip Formation: Chip formation in thermoset composites can vary significantly with material composition. Techniques like multi-axis adaptive roughing must be fine-tuned to maintain a consistent chip load and stable cutting forces, ensuring efficient material removal and prolonged tool life.
Structural Response: In fiber-reinforced thermoset composites, the structural response of the material is heavily influenced by fiber orientation. Optimizing tool paths to align with these orientations—especially in variable stiffness composites (VSC)—can enhance the overall structural integrity of the machined part.
Material Removal Rate: The machinability of thermoset composites directly affects the achievable material removal rate. Advanced milling strategies, such as trochoidal milling or high-speed machining, may need to be adjusted based on the specific material properties to balance productivity with surface quality.
Combining advanced five-axis milling techniques with material-specific considerations creates a robust framework for achieving superior machining outcomes. Techniques such as guiding curves, 3-to-5 axis tilt, multi-axis adaptive roughing, and curvature matching offer significant advantages in tool path optimization. When these strategies are tailored to account for the unique challenges posed by thermoset composite laminates—such as variable mechanical properties, heat sensitivity, fiber orientation, and resin systems—the result is a finely tuned process that maximizes productivity, surface quality, and tool life.
By integrating these advanced methodologies with thoughtful material selection and process adaptation, manufacturers can push the boundaries of precision machining, ensuring high-quality results even in the most challenging applications.