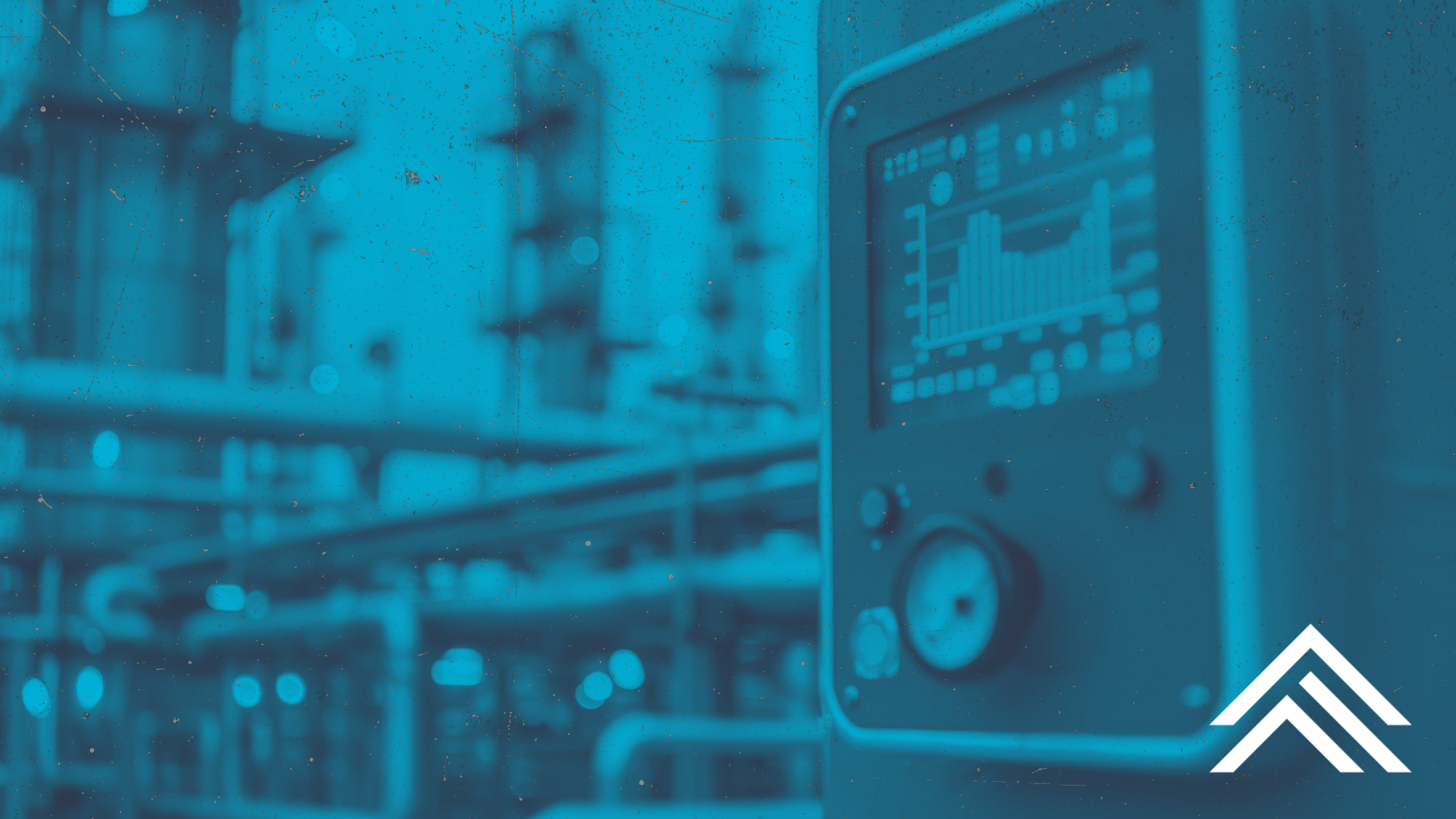
CNC milling is a cornerstone of modern manufacturing, prized for its precision and efficiency. However, the process is not without its challenges. One of the most critical issues encountered during milling operations is chatter—unwanted vibrations or oscillations that can significantly impair the quality and integrity of the machined parts. This issue is particularly pronounced when working with thermoset composite laminate materials, which due to their inhomogeneous and anisotropic nature, are more susceptible to chatter-induced damage.
Understanding Chatter in CNC Milling
Chatter detection is the process of identifying and monitoring these disruptive vibrations during machining operations. In the context of CNC milling, chatter not only affects the surface finish but also has profound implications on dimensional accuracy, tool life, and the overall structural integrity of the material being machined. The complexity of thermoset composites amplifies these issues, making chatter detection an essential component of the milling process.
Importance of Chatter Detection
Implementing effective chatter detection methods offers several key benefits:
Quality Control: Chatter can lead to poor surface finishes and dimensional inaccuracies, ultimately compromising the quality of the finished part. Early detection of chatter allows manufacturers to intervene promptly, ensuring that the final product meets stringent quality standards.
Tool Life: Excessive vibrations are a major cause of premature tool wear or even tool failure. By identifying chatter early, operators can adjust machining parameters to reduce vibration levels, thereby extending the life of cutting tools and reducing overall production costs and downtime.
Material Integrity: Thermoset composite laminates are particularly vulnerable to issues like delamination and fiber breakage. Chatter exacerbates these problems, potentially compromising the structural integrity of the final product. Effective chatter detection thus plays a crucial role in maintaining the robustness and reliability of composite components.
Process Optimization: By monitoring and addressing chatter, manufacturers can optimize critical cutting parameters—such as spindle speed, feed rate, and depth of cut—to create a more stable and efficient machining process. This not only improves product quality but also enhances overall operational efficiency.
Methods of Chatter Detection
Several methods have been developed to detect chatter in real-time during CNC milling operations, particularly when working with challenging materials like thermoset composites:
Force Measurement: Analyzing the cutting force components can provide insights into the onset of chatter. Fluctuations in force measurements often indicate the beginning of unstable cutting conditions.
Acoustic Emission: High-frequency stress waves are generated during the cutting process. By monitoring these acoustic emissions, it is possible to detect the signatures of chatter before they adversely affect the machining process.
Vibration Analysis: Using accelerometers or other vibration sensors, operators can monitor tool or workpiece vibrations. This method allows for the detection of irregular oscillatory behavior that signifies chatter.
Time-Frequency Analysis: Advanced signal processing techniques, such as time-frequency analysis, are employed to identify specific chatter signatures within the machining process. This method provides a detailed insight into the frequency components of the vibration signals, aiding in precise detection.
Sensory Tool Holders: An emerging approach involves integrating sensors directly into tool holders. These sensory tool holders can monitor the milling process in real-time, providing immediate feedback on vibration levels and enabling rapid corrective actions.
Chatter detection is a critical component in CNC milling, especially when dealing with thermoset composite laminate materials. Its role in ensuring quality control, prolonging tool life, preserving material integrity, and optimizing machining processes cannot be overstated. By leveraging advanced detection methods—ranging from force measurement and acoustic emission to vibration analysis and sensory tool holders—manufacturers can significantly mitigate the risks associated with chatter, ensuring the production of high-quality composite components while maintaining efficient and cost-effective operations.