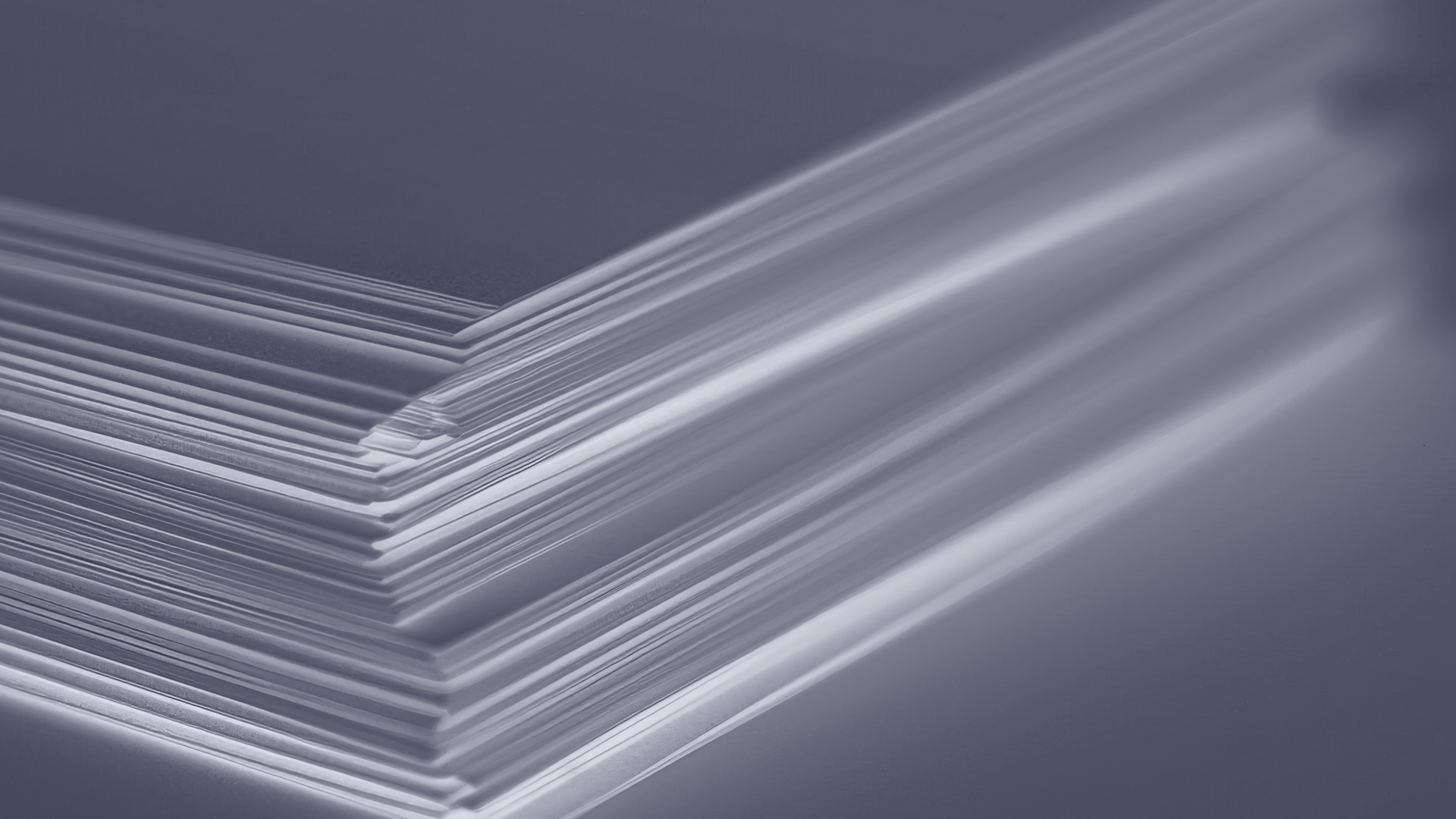
When sourcing materials for high-performance industries such as aerospace, automotive, industrial machinery, and electronics, precision, reliability, and consistency are key concerns.
Thermoset composites are widely used in structural supports, electrical insulation, braking systems, and wear-resistant applications, but standard sheet tolerances don’t always meet strict performance requirements.
For purchasing managers and distributors, understanding when and why to specify sanded thermoset materials can help ensure better part performance, improved manufacturability, and fewer production challenges.
How Sanded Materials Improve High-Precision Manufacturing
Sanding removes surface irregularities and ensures tighter tolerances, making it a valuable process for sourcing materials in industries where precision is critical. Here’s why:
Achieving Industry-Specific Thickness Tolerances
- Standard industry tolerances may not be tight enough for critical applications in aerospace, automotive, or electronics.
- Sanding can achieve tolerances as close as ±.003” on sheets up to .25” thick and ±.0015” on strips up to 12 inches wide.
- Uniform thickness improves manufacturing efficiency and reduces costly rework across multiple industries.
Reducing Material Variability & Improving Quality Control
- Sanding minimizes low spots and inconsistencies, ensuring consistent part performance.
- Fewer defects and scrap material mean cost savings for manufacturers and suppliers.
- Customers in regulated industries like aerospace and medical devices rely on strict quality standards—sanded materials help meet these expectations.
Better Adhesion for Laminating & Bonding
- Many industrial and electronic applications require adhesively bonded structures.
- Sanded surfaces create a better mechanical bond, reducing the risk of adhesive failure.
- Consistent bonding leads to stronger, more reliable components in automotive, aerospace, and manufacturing applications.
Friction-Optimized Materials for Braking & Wear Resistance
- Braking systems in aerospace, rail, and industrial machinery often rely on thermoset composites.
- Sanded sheets provide a higher coefficient of friction, improving braking efficiency and wear resistance.
What to Consider When Ordering Sanded Thermoset Materials
To ensure you’re getting the right materials for your needs, consider:
- Thickness Tolerances – Ensure that the material meets your required precision.
- Surface Condition – If bonding or laminating, specify sanded finishes for better adhesion.
- Potential Warpage – Thin sheets (< .031”) may warp if sanded one-sided.
- OD Sanding for Tubes – If your application requires tightly controlled outer diameters, confirm sanding specs upfront.
Sourcing the Right High-Performance Composites
For distributors and buyers, sanded thermoset composites offer higher precision, improved quality control, and enhanced performance across multiple industries. By specifying sanded materials upfront, you can ensure greater manufacturing efficiency, fewer defects, and better overall material consistency.
Looking for high-precision thermoset composites for your industry? Contact us to discuss your requirements today.