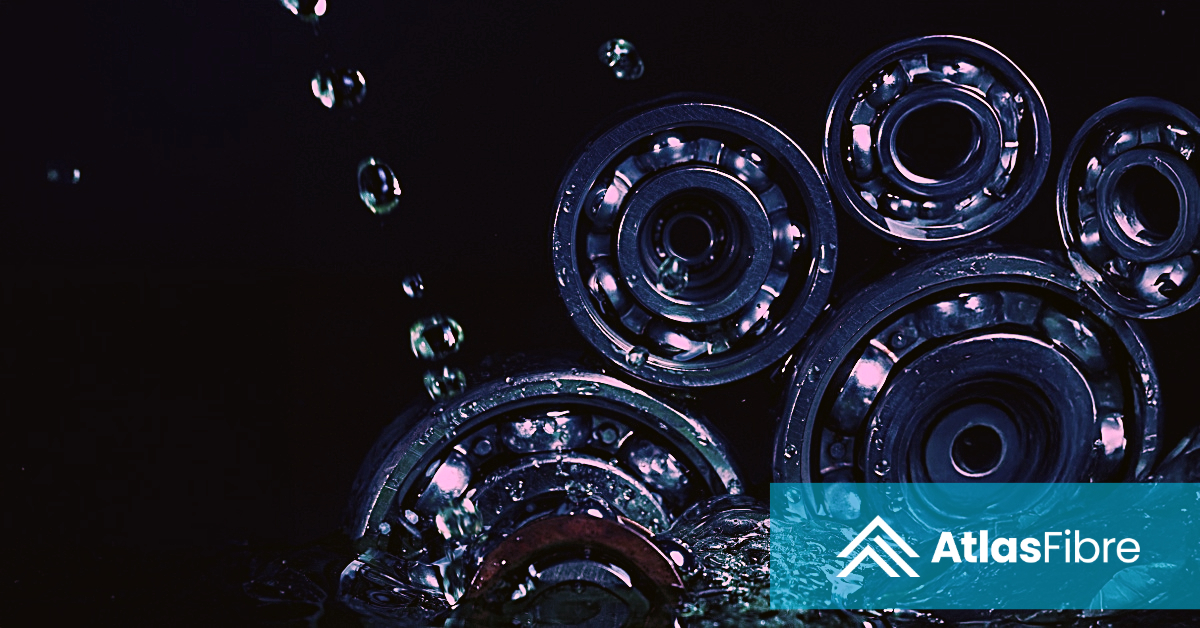
Understanding Friction in Thermoset Laminates
Friction is a double-edged sword. It keeps our cars from skidding off the road, allows a bolt to stay firmly in place, and helps us stop on a dime when we need to. But friction is also the villain of efficiency, robbing gears, bearings, and moving parts of their smooth operation, wearing down components over time.
For engineers working with thermoset composite laminates, understanding friction is more than an academic exercise—it’s essential for designing better bearings, insulators, and high-performance components. So, how does friction behave in these advanced materials? And what happens when they meet steel, bronze, or brass? Let’s break it down.
Friction: A Crash Course
At its core, friction is the resisting force that occurs when two surfaces slide (or try to slide) against each other. The coefficient of friction (CoF), represented by the Greek letter μ (mu), is the measure of how much force is needed to slide one surface over another relative to the force pressing them together.
Static friction (μs): The force required to start motion.
Dynamic friction (μk): The force required to maintain motion.
Imagine a 20kg block sitting on a table. Gravity exerts a normal force of 196N (20kg × 9.8m/s²). If it takes 20N to start sliding, its static CoF is 0.102 (20N ÷ 196N). If it takes 15N to keep moving, its dynamic CoF is 0.0765.
This ratio stays the same no matter the weight—meaning engineers can reliably predict how materials will behave under different forces.
Friction and Thermoset Laminates
When working with industrial laminates, the CoF isn’t a fixed number—it depends on surface finish, lubrication, vibration, and what material the laminate is in contact with. However, in general, laminated plastics offer relatively low friction, making them ideal for applications where wear resistance and smooth operation matter.
For instance, plate-finish laminates against smooth metal surfaces typically have a CoF between 0.25 and 0.36. However, a sanded finish can significantly alter friction, sometimes increasing the CoF by 40% or more.
Here’s how different laminate grades compare when in contact with common engineering metals:
Engineering Applications: When Friction Matters
Understanding CoF isn’t just about picking numbers from a table. Engineers designing bearing surfaces, insulators, and sliding components need to weigh trade-offs:
Low-friction laminates (plate finish) are ideal for smooth-motion applications like precision slides, bushings, or electrical insulators where minimal resistance is desired.
Higher-friction laminates (sanded finish) provide more grip, which may be useful in applications such as brake linings, high-friction pads, or clamping mechanisms.
Contact material matters—a laminate may behave differently when sliding against steel versus brass or bronze. Fine-ground finishes tend to reduce friction, while rougher surfaces increase it.
Friction as a Design Tool
Friction isn’t just a force to fight against—it’s a variable that engineers can use to their advantage. Whether designing a bearing that glides effortlessly or a component that stays firmly in place, the coefficient of friction of thermoset laminates plays a critical role in performance.
By understanding how laminates interact with different metals and surface finishes, engineers can make smarter material choices, extending the life of components and improving efficiency.
Want to know more about how thermoset laminates can optimize your application? Let’s talk friction.