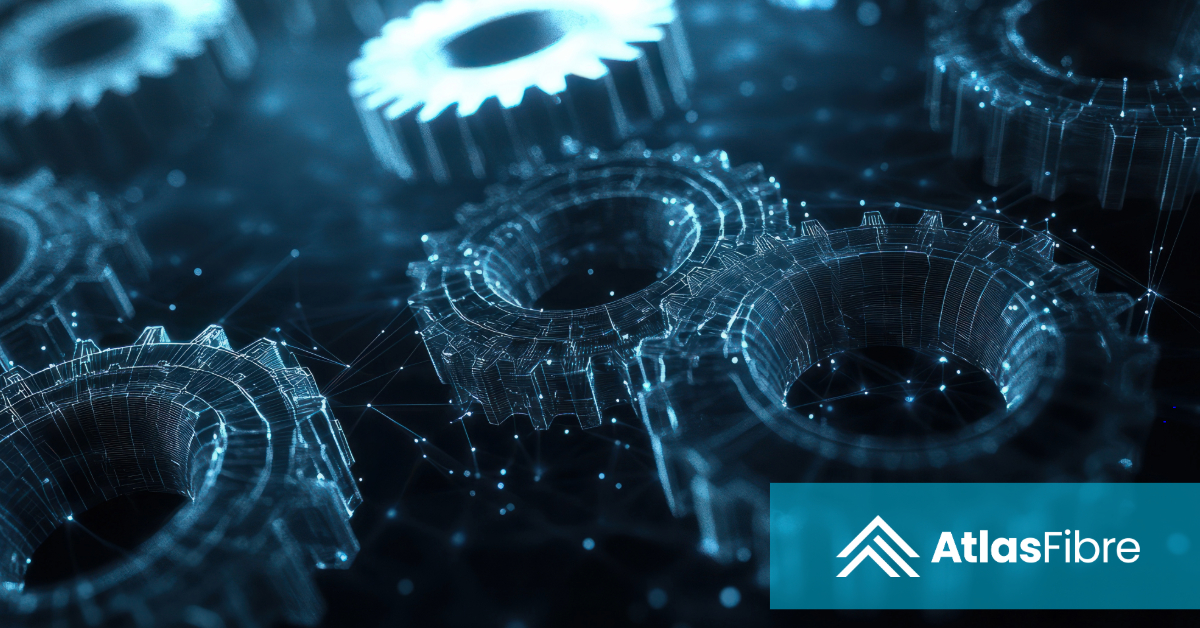
Composite materials are revolutionizing engineering by offering greater customization of components for applications (use cases) ranging from aerospace and automotive to electrification and other critical infrastructure.
The ability of these different advanced materials to achieve specific design objectives—such as high stiffness-to-weight ratios, targeted thermal properties, or electrical performance—opens up nearly limitless possibilities for innovation. However, this flexibility comes with the challenge of navigating a complex design landscape that extends beyond the traditional mechanics of materials.
Explore some of the foundational concepts and structured design processes essential to composite material design.
Get Familiar with Composites
Designing a composite part is, in many ways, a designer’s dream. The nearly infinite combinations of available materials allow engineers a high-level of customization to meet very specific performance goals. Yet, this abundance of choice demands a disciplined approach. Even when starting with assumptions regarding material properties or geometry, a systematic framework is necessary to decide on the optimal combination of inputs.
Key Drivers for Composite Adoption
Enhanced Specific Properties: Composites offer superior specific stiffness and strength (stiffness or strength per unit weight), making them ideal for applications where reducing weight is critical. This is why aerospace and automotive industries are increasingly integrating composites.
Data-Driven Design: Designers now have unprecedented access to empirical data from coupon-level tests, allowing them to base decisions on rigorous experimental evidence.
Advanced Analysis Tools: Modern software makes it possible to model complex composite behaviors quickly and cost-effectively, providing insights into failure modes and stress distributions that were once the domain of extensive hand calculations.
Proven Track Record: The growing list of successful composite applications in high-performance environments has built confidence in these materials, even for large and critical components such as entire fuselages.
Fundamental Characteristics
Heterogeneity: Composites consist of different materials—typically a matrix and a reinforcement—each contributing unique properties. This mix results in a material whose properties vary at the microscale.
Anisotropy: Unlike isotropic materials, composites have directionally dependent properties. The mechanical and electrical responses can vary dramatically with orientation, necessitating more advanced analysis techniques than those used for traditional materials.
In the sections that follow, we delve into how these unique characteristics inform both the design and analysis of composites.
How Composites Are Built
At their core, composite materials are constructed by combining two or more distinct materials, usually categorized as the matrix and the reinforcement.
The Matrix
The matrix serves several vital roles:
- Binding Agent: It holds the reinforcement in place.
- Protection: It shields the reinforcement from environmental and mechanical damage.
- Load Transfer: In many cases, the matrix helps distribute loads among the reinforcements.
While matrices can be polymers, metals, or ceramics, this discussion focuses on thermoset polymer matrix composites. Thermosets are favored in many high-performance applications because their curing process creates a cross-linked network that does not melt under high temperatures—ensuring consistent performance under load.
The Reinforcement
The reinforcement provides the primary load-bearing capabilities:
- Strength and Stiffness: Materials such as carbon fibers, glass fibers, aramids, and even unconventional options like paper or cotton fabrics, can be used.
- Customization: Reinforcement materials can be selected or even modified (for instance, by changing fiber orientation) to achieve desired directional properties.
Levels of Composite Construction
Understanding composite design is easier when broken down into hierarchical levels:
Molecular Level: Although adjustments at the chemical level (e.g., altering the resin chemistry) can affect performance, this scale is usually managed by materials scientists rather than by the composite designer directly.
Constituent Level: Here, the focus is on the discrete materials (matrix, reinforcement, and any additives). Their individual engineering constants provide the necessary inputs for higher-level analyses.
Lamina (or Ply) Level: A lamina is a single layer composed of the constituents. Analysis at this level adapts traditional stress-strain relationships to account for the combined behavior of the matrix and reinforcement.
Laminate Level: By stacking multiple lamina—often with varying fiber orientations—designers can tailor overall properties to better match the loading conditions and desired performance characteristics of the final product.
Part Level: This is the stage where the composite material is integrated into the final geometry, ready to meet the external loads and service conditions of its intended application.
Each level builds upon the previous one, adding complexity but also offering more precise control over the final material properties.
A Framework for Analyzing Heterogeneity
Due to the inherent heterogeneity of composites, properties can vary on a microscopic scale. However, when analyzing a region large enough relative to the size of the reinforcement and matrix constituents, engineers often use the concept of an effective modulus—a homogenized property that represents the average behavior of the composite.
The Rule of Mixtures
The rule of mixtures is a foundational approximation tool in composite design. It assumes that the properties of a lamina (such as stiffness and strength) can be approximated as the volume fraction-weighted average of its constituents’ properties.
While this rule provides a valuable first estimate—especially for properties like the longitudinal modulus—it remains an approximation. Designers must validate these estimates through experimental testing and more refined analyses.
Designing with Anisotropy
Anisotropy introduces unique challenges into composite design. In isotropic materials, stress and strain responses are straightforward: normal stresses produce only normal strains, and shear stresses produce only shear strains. In anisotropic composites, however, the situation is more complex due to shear coupling.
Understanding Shear Coupling
Coupled Behavior: In composites, a normal stress can induce both normal and shear strains, and a shear stress might cause both types of deformation. This coupling arises from the anisotropic nature of the reinforcement, especially in unidirectional lamina where fibers primarily carry loads in one direction.
Thermal Effects: Thermal strains in composites can also be directionally dependent. Differential expansion or contraction between the matrix and reinforcement can lead to internal stresses and distortions that must be carefully considered in the design phase.
Anisotropy at Different Scales
Lamina Level: Each lamina exhibits five independent stress-strain relationships. These include:
- longitudinal tension and compression (along the fiber direction),
- transverse tension and compression (perpendicular to the fiber direction), and
- In-plane shear
Typically, the transverse direction is the weakest due to the limited contribution of the fibers to load-bearing in that orientation.
Laminate Level: When stacking lamina to form a laminate, the directional properties interact. Even if all lamina are of the same material, the overall behavior can vary dramatically based on fiber orientation, stacking sequence, and the interaction between layers. Classical Lamination Theory (CLT) provides closed-form solutions for many of these scenarios, offering insight into how stresses and strains are distributed across the laminate.
Although CLT assumes continuity of displacements across lamina interfaces (thus neglecting interlaminar shear stresses), it remains a critical tool in predicting and optimizing the behavior of composite laminates under load.
A Starting Point for Designing Components from Composites
Designing composite components begins with a clear understanding of the external loads, boundary conditions, and service environment. However, composite design differs significantly from traditional materials because the reinforcement orientation plays a pivotal role in performance.
The Structured Design Process
Load and Condition Analysis: Begin by detailing the expected loads, strain rates, service temperatures, and any environmental exposures (e.g., humidity, UV radiation).
Geometry and Design Window: Understand the spatial constraints and required geometrical features of the component. This includes considering how the composite’s layered structure can be integrated into the design.
Failure Modes: Identify all potential failure modes such as fracture (strength), excessive deformation (stiffness), buckling (stability), fatigue and creep (life/durability), environmental degradation (hygrothermal effects), and manufacturing issues (warping, cost)
Stress Evaluation: Calculate the expected stresses in the composite, keeping in mind the directional dependencies and coupling effects.
Material Selection: Consult technical databases to identify candidate materials and verify their performance through empirical data.
Modeling and Simulation: Use Finite Element Analysis (FEA) tools capable of handling the anisotropic behavior and shear coupling to simulate the component under realistic loading conditions.
Prototyping and Testing: Fabricate prototypes and subject them to rigorous testing—including coupon tests and full-scale tests—to validate the design. This experimental phase is indispensable due to the complexity and potential unpredictability of composite behavior.
By iteratively following these steps, designers can build confidence in their composite designs and optimize them for both performance and manufacturability.
How Stock Laminate Shapes Can Accelerate the Design and Development Process
In many industries, rapid prototyping and production are essential. Traditionally, composites have been fabricated using net-shape processes (like autoclave molding for aerospace parts), but using stock laminate shapes such as sheets, rods, and tubes offers several advantages:
Tooling and Molding: Stock shapes eliminate the need for specialized molds, enabling faster turnaround times for prototyping and early-stage development.
High-Volume Consistency: Automated production of stock laminates ensures repeatability and consistent material properties, which are crucial for validating design models.
Baseline Performance Data: Using widely available stock materials allows designers to leverage established performance data and empirical insights. This “off-the-shelf” approach can simplify initial design iterations and reduce the risks associated with developing entirely new composite formulations.
Ultimately, the availability of stock laminate shapes can significantly reduce development time and cost, allowing engineers to focus on tailoring the composite structure for specific performance requirements rather than reinventing the manufacturing process.
Integrating Composites Into Existing Applications
The art and science of designing with composites require a deep understanding of both material behavior and structural mechanics. By embracing the layered complexity—from molecular interactions to full-scale parts—and accounting for the inherent heterogeneity and anisotropy, engineers can exploit the full potential of composites. Modern analytical tools, combined with a structured design process and robust experimental validation, ensure that composite designs not only meet but often exceed the performance criteria required for today’s demanding applications.
In summary, while composites introduce challenges not encountered with traditional materials, their unique benefits—customizability, lightweight strength, and high specific performance—make them indispensable in modern engineering design. As technology advances, the integration of composites into new and existing applications will only continue to grow, driven by ongoing research and the development of ever more sophisticated design and manufacturing methods.