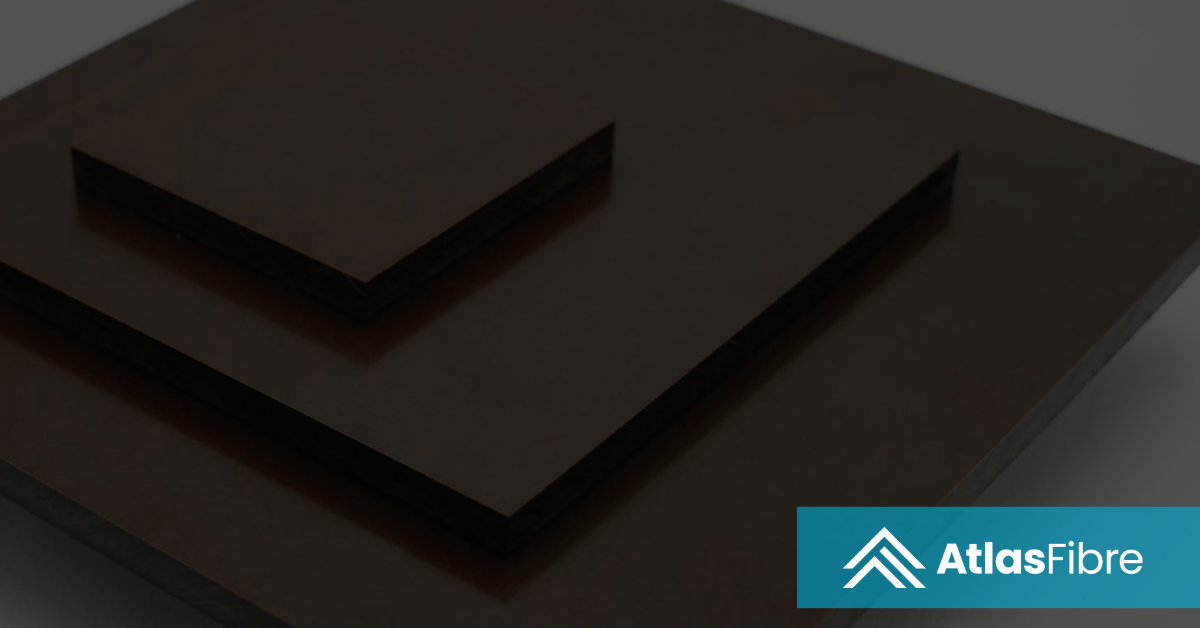
The story of phenolic materials begins with the rise of electricity—and the need to insulate it safely.
Early attempts relied on shellac applied to materials like wood, amber, glass, or slate—each limited by cost, performance, or both. That changed in 1905 when Swiss inventor Emil Haefely introduced a breakthrough process to the U.S., combining shellac with paper and mica to create sheets and tubes. Though initially without an application, these materials soon found their place—serving as insulation in Westinghouse generator coils.
At the same time, across the Atlantic, Dr. Leo Baekeland was deep in experimentation. His goal? To tame the unpredictable reaction between phenol and formaldehyde—not for insulation, but to create durable pipe stems that wouldn’t crack or crumble under pressure. His work caught the attention of C.E. Skinner, an engineer at Westinghouse. A collaboration was born, and within a year, the first commercial drum of phenolic resin—Bakelite—was produced. It was stronger than shellac, and thanks to new coating machinery, overcame the dielectric limitations that plagued early versions.
With the world’s first synthetic thermoset polymer now in hand, innovation exploded.
By 1910, J. Dow had developed a condenser bushing for transformers using conductive ink on phenolic-impregnated paper. In 1912, H. Conrad discovered that gears cut from cotton fabric-reinforced phenolic laminates ran quietly and handled moisture—making them ideal for tough environments. A year later, the first decorative phenolic laminates hit the market.
The gear breakthrough led to even bigger advances. By 1917, phenolic compounds were being used in aircraft propellers—millions of which powered American planes through WWII and the Korean War. That same year, aircraft pulleys molded from cotton phenolic composites began guiding control cables inside planes. The formulation is still produced today, proving phenolic’s staying power in critical applications.
By the 1920s, phenolic parts were everywhere: from the iconic black rotary phones found in nearly every home, to restaurant trays, furniture, and architectural materials.
Innovation kept coming. In 1927, a patent was granted for ship propeller bearings made from 4-inch-thick cotton phenolic laminate. Water-lubricated, they ran quietly and efficiently—quickly adopted by hot rolling and paper mills, where they replaced costly metal bearings and dramatically reduced downtime.
From 1915 through the 1930s, the use of phenolic laminates and molding compounds skyrocketed—fueling the growth of entire industries and supporting the rise of new technologies. Many of those same formulations are still in use today.
Even in safety equipment, phenolics led the way. With coal mining booming, the Mine Safety Appliance Company used cotton phenolic to mold the first industrial hard hats—millions of which were produced over the following decades.
During WWII, phenolics again played a vital role. In response to a request from the U.S. Army, manufacturers adapted mining helmet technology to create a lightweight liner for infantry helmets. By the war’s end, Bryant Electric Corp in Bridgeport, CT had delivered 26 million of these cotton phenolic liners to support the war effort.
Still Evolving, Still Essential
Today—more than 120 years later—phenolic resins remain a cornerstone of custom material formulations. Cost-effective, incredibly versatile, and performance-proven, phenolics continue to power innovation across industries. From critical infrastructure and industrial equipment to hobbies and high-end products, phenolics are still delivering solutions—and still pushing boundaries.