High-performance thermoplastics are a critical component in today’s advanced industries, and none more so than Torlon polyamide imide (PAI). Renowned for its exceptional mechanical and tribological properties, Torlon PAI has become the go-to material for a wide range of demanding applications. So, what makes it stand out from the crowd, and how can you ensure the best possible results when machining this versatile material? Read on to find out about machining Torlon PAI.
In this comprehensive guide, we’ll explore the unique properties of Torlon PAI, the different machining techniques used to create components, and the various grades available for specific applications. We’ll also discuss the key industries utilizing Torlon PAI and provide expert tips on achieving dimensional control and quality during the machining Torlon PAI process. Finally, we’ll delve into the importance of partnering with experienced Torlon PAI machining experts to ensure the highest quality results for your project.
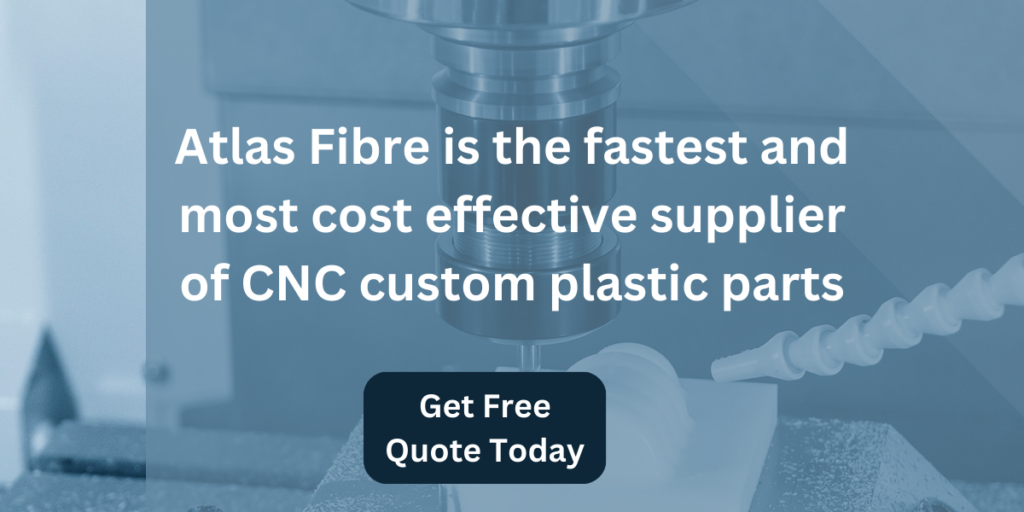
Key Takeaways
- Torlon PAI is a high-performance thermoplastic with superior wear and shock resistance, excellent creep resistance, and exceptional chemical/thermal characteristics.
- CNC plastic machining offers repeatability, stress reduction & high quality parts for specific application demands.
- Partnering with experienced professionals ensures successful Torlon PAI machining solutions through expertise & advanced automation capabilities.
Understanding Torlon PAI: A High-Performance Thermoplastic
Torlon PAI, classified as an amorphous high-performance thermoplastic, is considered one of the most advanced engineering plastics available today. Its remarkable mechanical and tribological characteristics make it an ideal material for a wide range of high performance plastics applications. Torlon PAI offers superior wear and shock resistance, with particular glass-reinforced and carbon-fiber-reinforced grades enhancing stiffness and thermal expansion properties.
Torlon polyamide imide (PAI) offers the following benefits:
- High creep resistance
- Exceptional resistance to chemicals, high-energy radiation, hydrolysis, and UV
- Ability to maintain physical properties under extreme temperatures
These attributes make Torlon PAI a robust choice for applications exposed to harsh conditions, where other materials may falter. Its versatility and durability set it apart from other engineering plastics.
Linear Thermal Expansion and Glass Transition Temperature
One of the key properties that make Torlon PAI suitable for high-temperature applications is its extremely low coefficient of linear thermal expansion and high glass transition temperature. The linear thermal expansion coefficient of Torlon PAI is estimated to be around 50-60 x 10^-6/°C. This low thermal expansion offers various advantages, such as:
- Minimizing dimensional changes
- Maintaining dimensional stability at elevated temperatures
- Helping prevent warping, distortion, and other issues that can impact the performance and precision of components made from Torlon PAI.
The high glass transition temperature of Torlon PAI is another key feature, enabling the material to uphold its mechanical properties like strength and stiffness under high temperatures. This makes Torlon PAI an exceptional choice for applications where temperature stability and resistance to thermal degradation are critical.
From aerospace to automotive, the unique thermal properties of Torlon PAI make it an invaluable material for demanding applications.
Mechanical and Tribological Properties
Compared to other high-performance thermoplastics, Torlon PAI exhibits the following superior mechanical properties:
- Superior toughness and impact strength
- High heat deflection temperature
- Retention of higher strength at elevated temperatures
- Compressive strength that is twice as great as PEEK
- 30% higher compressive strength than ULTEM PEI
These impressive mechanical properties make Torlon PAI a reliable choice for components subjected to significant stress and strain.
In addition to its mechanical strength, Torlon PAI offers excellent wear resistance, making it an ideal material for applications where reduced friction and long-lasting performance are crucial. From thrust washers to bearings, Torlon PAI’s unique combination of mechanical and tribological properties make it a go-to material for industries seeking high-performance, durable components.
Machining Techniques for Torlon PAI
Creating Torlon PAI components involves two primary machining techniques: injection molding and CNC plastic machining. Each method offers its own advantages and challenges, making it essential to select the best process for your specific application. By understanding these techniques and their unique benefits, you can ensure optimal results when machining Torlon PAI.
Examining both injection molded components and CNC plastic machining reveals how they can be used to create high-quality Torlon PAI components for various applications.
Injection Molding and Compression Molding
Injection molding and compression molding are the most common techniques for producing Torlon PAI parts. The injection molding process for Torlon PAI requires preventing chain extension and crosslinking during the molding process. This thermoset polymer can be effectively used to create parts with complex industrial applications, providing superior compressive strength, high hardness characteristics, and efficient production. However, it can generate excess scraps and necessitate careful design considerations to avoid material waste.
Compression molding for Torlon PAI also offers superior compressive strength, high hardness characteristics, and chemical resistance as advantages. However, its hygroscopic nature necessitates thorough drying before molding, thus presenting a challenge. Understanding the benefits and challenges of both injection molding and compression molding will assist in choosing the most appropriate technique for creating Torlon PAI components.
CNC Plastic Machining
CNC plastic machining offers a precise and efficient production process for Torlon PAI components. Turning, milling, and drilling are commonly used in the CNC machining of Torlon PAI. For CNC plastic machining of Torlon PAI, computer numerical control (CNC) machines, such as CNC mills and CNC lathes, are typically used to precisely shape and cut the material into the desired form. Additionally, specialized cutting tools, such as carbide end mills, are employed for machining Torlon PAI due to its high strength and heat resistance properties.
The advantages of CNC plastic machining for Torlon PAI include a consistently precise procedure that can be repeated infinitely and post-machining annealing to reduce stress and prevent early failure. Taking advantage of the precision and efficiency of CNC plastic machining can ensure the production of high-quality Torlon PAI components suitable for specific application demands.
Grades of Torlon PAI: Selecting the Right Material
Torlon PAI is available in a variety of grades, each tailored to specific application requirements. These grades can be broadly categorized into wear-resistant grades and high-strength grades, offering unique combinations of mechanical and tribological properties, chemical resistance, and thermal stability. Understanding the specific requirements of your application can guide the selection of the most appropriate Torlon PAI grade, ensuring optimal performance and longevity.
We will now examine the differences between wear-resistant and high-strength grades of Torlon PAI, and their respective ideal applications, to assist in making the best material selection for your needs.
Wear-Resistant Grades
Wear-resistant grades of Torlon polyamide imide PAI are designed to provide superior performance over a broad range of temperature and PV conditions. These grades boast high compressive and flexural strength, as well as remarkable resistance to wear. Wear-resistant grades of Torlon PAI are ideally suited for applications that demand superior performance in both dry and wet environments, as well as outstanding strength and hardness retention.
Examples of these applications include bearings, rollers, and components in high PV applications. Choosing a wear-resistant grade of Torlon PAI can guarantee the creation of components with exceptional wear resistance, durability, and performance in demanding conditions.
High-Strength Grades
High-strength grades of Torlon PAI offer outstanding mechanical strength and stiffness, making them ideal for demanding applications. They provide excellent retention of mechanical strength, stiffness, and creep resistance over a wide temperature range, competing with metals such as titanium and steel in terms of high strength. Reinforced Torlon PAI grades with carbon fiber or glass fiber demonstrate improved fatigue resistance and reduced creep, making them suitable for applications that require exceptional strength and durability.
Typical applications for high-strength grades of Torlon PAI include:
- Aircraft hardware and fasteners
- Automotive transmission and powertrain components
- Industrial equipment that requires high-strength components capable of withstanding harsh conditions
Choosing a high-strength grade of Torlon PAI can guarantee the creation of components with superior mechanical strength and durability, even in the most demanding environments.
Key Applications of Torlon PAI in Different Industries
Torlon PAI is highly sought-after in various industries, such as aerospace, automotive, oil & gas, and electrical, due to its advantageous properties. Its exceptional mechanical and tribological properties, combined with its ability to withstand extreme temperatures and resist chemicals, make Torlon PAI an invaluable material for a wide range of applications in these industries.
From aircraft hardware to automotive transmission components and oil & gas exploration equipment, Torlon PAI’s versatility and high-performance capabilities make it a go-to material for industries seeking durable, reliable components. Now, let’s examine some of the primary uses of Torlon PAI in these sectors.
Aerospace and Automotive Applications
In the aerospace and automotive industries, Torlon PAI is an essential material for critical components in engines, vehicles, and equipment. Its properties make it ideal for use in various applications, including:
- Thermal isolators
- Sector gears
- Bushings
- Screws
- Transmission parts
- Hydraulic ring seals
- Axial thrust bearings
- Check balls for transmissions
Torlon PAI offers superior wear resistance, low friction properties, and can withstand high temperatures and chemicals.
Torlon PAI’s unique combination of properties enables it to offer exceptional performance and longevity in these demanding applications, making it an invaluable material for the aerospace and automotive industries.
Oil & Gas and Electrical Applications
Torlon PAI is well-suited for oil & gas and electrical applications due to its resistance to extreme temperatures, high pressure, and corrosion. In the oil & gas industry, Torlon PAI is used for components such as pumps, valve seals, bearings, rollers, and parts that require high temperatures. Its ability to withstand high temperatures up to 275 °C (527 °F) makes it an ideal choice for components exposed to elevated temperatures in these industries.
In electrical applications, Torlon PAI offers excellent retention of mechanical strength, stiffness, and creep resistance over a wide temperature range, making it a dependable choice for components that may be exposed to elevated temperatures. Overall, Torlon PAI’s unique combination of properties makes it a valuable material for oil & gas and electrical applications, where components must withstand extreme conditions and maintain their performance.
Tips for Achieving Dimensional Control and Quality in Machining Torlon PAI
To guarantee the highest quality and precision in machining Torlon PAI, it’s important to follow these steps:
- Choose the appropriate material, tooling, and cutting parameters.
- Select the right Torlon PAI grade and stock shape for your application to achieve optimal machining results.
- Use appropriate tooling, such as carbide or polycrystalline diamond (PCD) tools.
- Optimize cutting parameters to prevent overheating and maintain dimensional accuracy during the machining process.
By following these steps, you can ensure the best results when machining Torlon PAI.
Adhering to expert advice on material selection, tooling, and cutting parameters can enable the achievement of supreme dimensional control and quality in machined Torlon PAI components. This will ensure that your final product meets the exacting demands of your application and offers the best possible performance and durability.
Material Selection and Stock Shapes
Choosing the right Torlon PAI grade and stock shape for machining is key to achieving optimal results. Different grades of Torlon PAI possess distinct properties like:
- Impact resistance
- High temperature tolerance
- Rigidity
- Dimensional stability
These properties can influence the machinability of the material. It is essential to pick the appropriate Torlon PAI grade based on the specific machining requirements to attain desired precision and durability.
The most suitable Torlon PAI stock shapes for machining are TORLON 4203, which is the unfilled or natural grade of Torlon PAI. When selecting an appropriate Torlon PAI stock shape for a particular machining process, it is essential to take into account the abrasiveness of the material on tooling. Carbide tools are often recommended for machining Torlon PAI due to its abrasive nature.
Tooling and Cutting Parameters
Appropriate tooling and cutting parameters are key to ensuring precision and durability in machined Torlon PAI components. Carbide or polycrystalline diamond (PCD) tooling is recommended for machining Torlon PAI, as it provides a sharp cutting edge and requires relief. Maintaining tool sharpness is essential to prevent a rough surface from forming during machining.
Cutting parameters, such as tooling material and feed rate, can significantly influence the quality of machined Torlon PAI parts. For optimal tool life, it is recommended to use carbide tools as Torlon PAI is abrasive on tooling. Moreover, optimizing the feed rate can help to avoid overheating and maintain dimensional accuracy during the machining process. By carefully considering tooling and cutting parameters, you can ensure the production of high-quality Torlon PAI components that meet the demands of your application.
Partnering with Experts for Torlon PAI Machining Solutions
Collaborating with experienced Torlon PAI machining experts is key to ensuring high-quality results and comprehensive engineering support. By partnering with professionals who possess expertise in machining Torlon PAI, you can benefit from their knowledge and experience in optimizing the machining process, ensuring accuracy, and achieving the desired outcomes.
Next, we discuss:
- The importance of assessing potential machining partners
- The benefits of collaborative engineering support
- The advantages of partnering with companies like Atlas Fibre, which specialize in state-of-the-art plastics-only machining.
Evaluating Machining Partners
In evaluating a Torlon PAI machining partner, consider factors such as:
- Experience and proficiency in machining this material
- Tooling capabilities
- Quality control measures
- Flexibility and customization
- Approach to communication and collaboration
A dependable Torlon PAI machining partner should possess expertise in machining intricate components from Torlon PAI, alongside a comprehensive understanding of the various grades of Torlon PAI and the ability to machine them efficiently.
Additionally, a reliable machining partner should have:
- Access to advanced machining equipment, such as high-quality tooling and CNC machining centers
- Dedication to excellence
- Strong communication and teamwork abilities
By carefully evaluating potential machining partners, you can ensure the highest quality results for your Torlon PAI components.
Collaborative Engineering Support
Collaborative engineering support is key in machining Torlon PAI, requiring close collaboration with engineers and experts to optimize the machining process, ensure accuracy, and achieve the desired outcomes. This support includes providing advice on tool selection, machining parameters, and techniques specific to Torlon PAI. Collaborative engineering support also assists in detecting potential issues and finding solutions to address them, leading to enhanced efficiency and quality in machining Torlon PAI.
By partnering with a Torlon PAI machining partner that offers collaborative engineering support, you can benefit from the expertise and knowledge of multiple engineers and stakeholders, ultimately leading to improved precision, durability, and performance of your final product.
Atlas Fibre, state-of-the art plastics only machining
Partnering with a company that specializes in state-of-the-art plastics-only machining, like Atlas Fibre, can offer numerous advantages. Atlas Fibre utilizes fully automated flexible manufacturing systems and brand new CNC machining centers, ensuring high-quality results for your Torlon PAI components. Additionally, Atlas Fibre employs techniques such as washing parts, immersion cleaning, coolant use, and surface wiping to ensure cleanliness in its plastic-only machining facilities.
By working with a dedicated plastics-only machining partner like Atlas Fibre, you can reduce the risk of contamination from metal machining and ensure the highest quality results for your Torlon PAI components.
What automation to look for in a partner
When choosing a Torlon PAI machining partner, look for:
- Advanced automation capabilities, like fully automated flexible manufacturing systems and modern CNC machining centers
- High production rates
- Rapid adaptation to fluctuations in demand
- Cost-efficiency for both low and high production quantities
- High levels of precision and performance
These advanced systems offer a range of benefits for your machining needs, with technical data sheets available for further information.
Moreover, modern CNC machining centers provide a variety of advanced features for processing Torlon PAI, including:
- High-speed machining
- Multi-axis machining
- Advanced tooling systems
- Precision control systems
- Coolant and chip management
By partnering with a Torlon PAI machining expert that employs advanced automation capabilities, you can ensure the highest quality results for your components.
Summary
In conclusion, Torlon PAI is a high-performance thermoplastic that offers exceptional mechanical and tribological properties, making it an ideal material for a wide range of demanding applications. From aerospace to automotive, oil & gas, and electrical industries, Torlon PAI’s versatility and durability make it a go-to material for components that require high strength, wear resistance, and low friction.
By understanding the unique properties of Torlon PAI and the various machining techniques available, and by partnering with experienced Torlon PAI machining experts, you can ensure the production of high-quality components that meet the exacting demands of your application. With the right knowledge, tools, and partners, the possibilities for Torlon PAI are truly limitless.
Frequently Asked Questions
What makes Torlon PAI unique among high-performance thermoplastics?
Torlon PAI is unique among high-performance thermoplastics for its exceptional mechanical and tribological properties, superior wear and shock resistance, and ability to retain its physical properties in extreme temperatures, making it ideal for demanding applications.
What machining techniques are used for Torlon PAI components?
Injection molding and CNC plastic machining are the primary machining techniques used for producing Torlon PAI components.
How can I choose the right grade of Torlon PAI for my application?
Choose the right grade of Torlon PAI for your application by considering its specific needs and selecting a grade that offers the optimal combination of properties.
What are some key applications of Torlon PAI in the aerospace, automotive, oil & gas, and electrical industries?
Torlon PAI is widely used across the aerospace, automotive, oil & gas, and electrical industries for aircraft hardware and fasteners, automotive transmission and powertrain components, oil & gas exploration and recovery equipment, and electrical and electronic components.
How can I ensure the highest quality and precision when machining Torlon PAI components?
To ensure the highest quality and precision when machining Torlon PAI components, use the proper material, tooling, and cutting parameters; enlist the help of experienced Torlon PAI machining experts; and partner with companies specialized in plastics-only machining.