When it comes to materials that are strong, durable, and versatile, g10 sheet stands out as a top choice. These thermoset epoxy fiberglass sheets have a broad range of applications, from electrical insulation to mechanical components and even specialty items. In this guide, we will uncover the secrets behind the strength and resilience of g10 sheet and learn how to choose the right form, size, and thickness for your project.
Key Takeaways
- G10 sheets are composed of epoxy resin and fiberglass for strength, durability & electrical insulation.
- They offer exceptional features such as low moisture absorption & chemical resistance suitable for many applications.
- Available in full sheets, rods or custom cut options with fast delivery and stock availability to suit any project.
Understanding G10 Sheets: Composition and Features
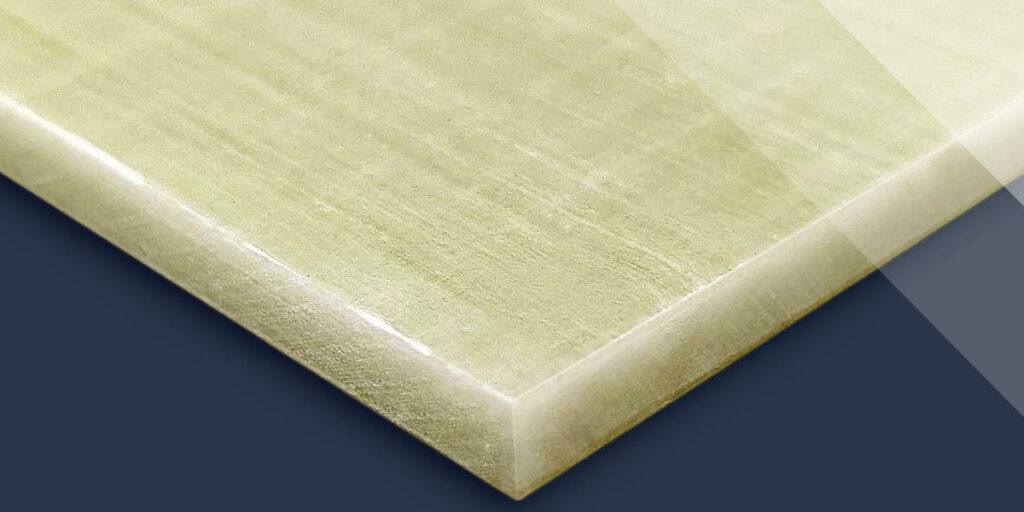
G10 sheets, also known as g 10 fr4 glass epoxy sheets, are constructed using a combination of solid laminates of fiberglass prepreg and epoxy resin with high strength properties. This unique composition results in a material that is not only strong and durable but also possesses excellent electrical insulating properties, making it suitable for a wide array of applications.
Epoxy Resin Binder
The epoxy resin binder is a significant component of G10 sheets, contributing the following properties:
- Insulation
- Wear resistance
- Corrosion resistance
- Superior insulation properties
- Robust mechanical strength
- Good dielectric properties
- Resistance to corrosion and flame
- Heat and moisture resilience
Due to these properties, epoxy resin is well-suited for G10 sheets.
The process of embedding epoxy resin into G10 sheets involves:
- Soaking layers of glass cloth in the resin, which has superior adhesive properties.
- Compressing the layers under heat and pressure.
- Ensuring a secure bond and enhanced strength and durability for the final product.
Fiberglass Reinforcement
Fiberglass reinforcement, another significant component of G10 sheets, lends extra strength and rigidity to the material. Continuous filament fiberglass cloth, specifically plain weave e-glass, is commonly used for G10 sheet reinforcement.
This reinforcement not only enhances the mechanical properties of G10 sheets but also contributes to their good electric strength properties and excellent electrical insulation properties, making them suitable for various industries and applications.
Key Features
Some of the most notable features of G10 sheets include their high strength, low moisture absorption, and chemical resistance. The tensile strength of G10 sheets is approximately 40,000 psi lengthwise and 35,000 psi crosswise. Their resistance to moisture is outstanding, ensuring rust-free performance when exposed to moist conditions.
G10 sheets also demonstrate outstanding chemical resistance. These key features make G10 sheets an ideal material for a variety of applications, where strength, durability, and resistance to various environmental factors are crucial.
G10 Sheet Forms and Sizes
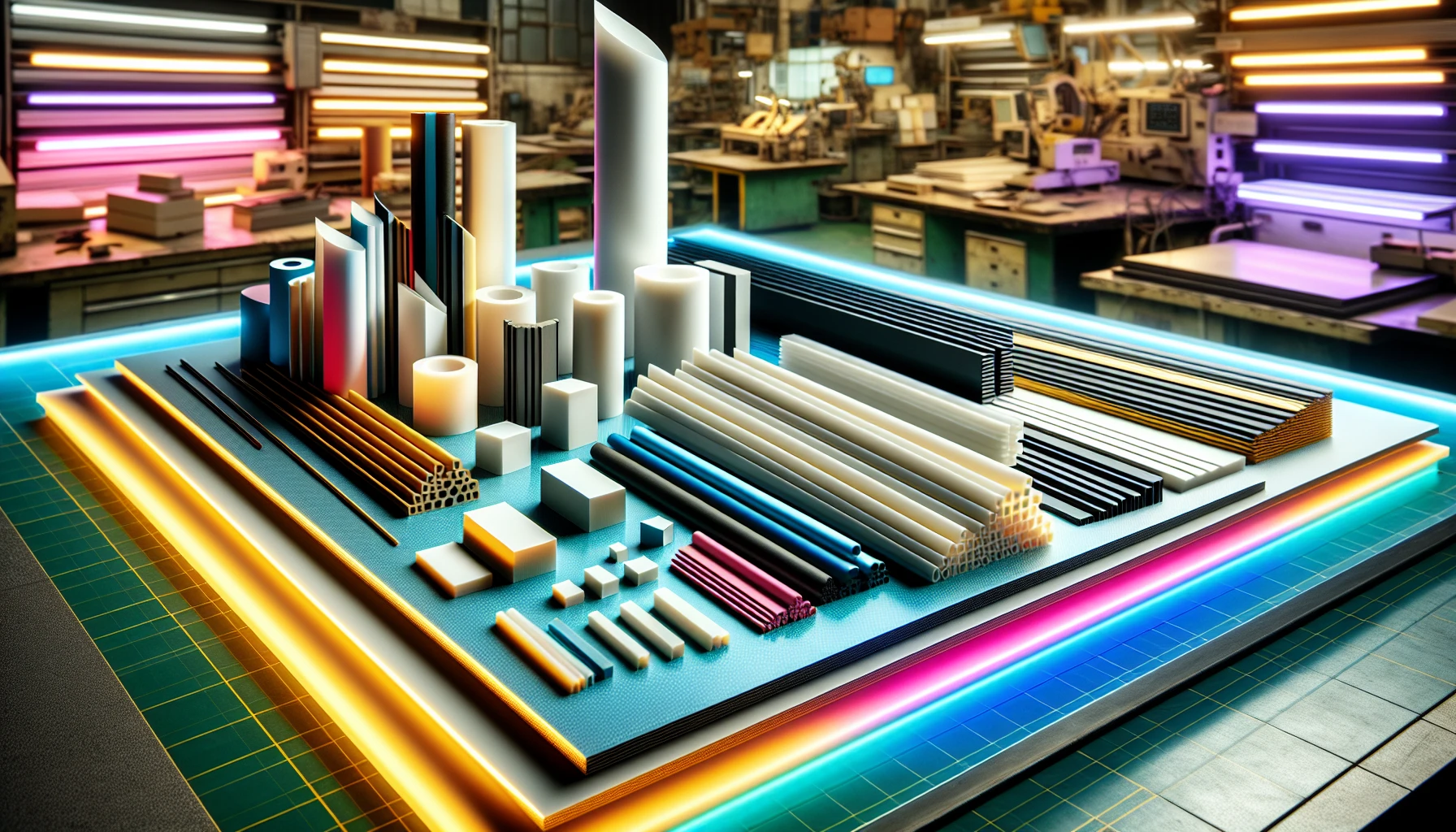
G10 sheets can be purchased in various forms and sizes to suit specific project requirements, including the popular FR 4 variant. They are available as full sheets, rods, and custom cut configurations.
While the standard sizes for full G10 sheets can differ based on the manufacturer and supplier, common measurements include 36” x 48” and 48” x 96”.
Full Sheets
The dimensions of full G10 sheets can vary by manufacturer and supplier, with common sizes including 48 inches by 96 inches (4 feet by 8 feet) and 36 inches by 48 inches (3 feet by 4 feet). Customized sizes can also be provided to meet specific requirements, guaranteeing the right fit for your project.
Full G10 sheets are regularly employed in a variety of projects, including CNC machining, fabrication, and 3D printing. The strong and rigid nature of G10 sheets makes them a robust and dependable material for constructing structures in these applications.
G10 Sheet Rods
G10 sheets are also available in rod form, apart from full sheets. These cylindrical rods resemble solid rods or bars and are typically produced by turning and grinding from sheet stock. G10 rods are available in a range of sizes, including:
- 1/8 inch in diameter
- 1/4 inch in diameter
- 1/2 inch in diameter
- 1 inch in diameter
- 2 inches in diameter
G10 rods are commonly used in various industries, including:
- Electrical and electronics industry
- Aerospace and defense
- Marine
- Automotive
- Industrial equipment
- Sports and recreation
Their high strength-to-weight ratio and great dimensional stability make them an attractive alternative to other materials, such as glass-filled Nylon.
Custom Cut Options
Custom cut options offer further versatility for G10 sheets, with CNC cutting, die cutting, and laser cutting being popular choices. These cutting methods ensure a precise and clean cut, tailored to your specific project requirements. It is important to remember that the edges of custom cut G10 sheets may have sharp edges, and proper finishing or smoothing techniques should be employed to achieve a professional result.
Choosing custom cut options enables you to tailor G10 sheets to your project, be it for electrical insulation, mechanical components, or unique specialty items.
Applications of G10 Sheets
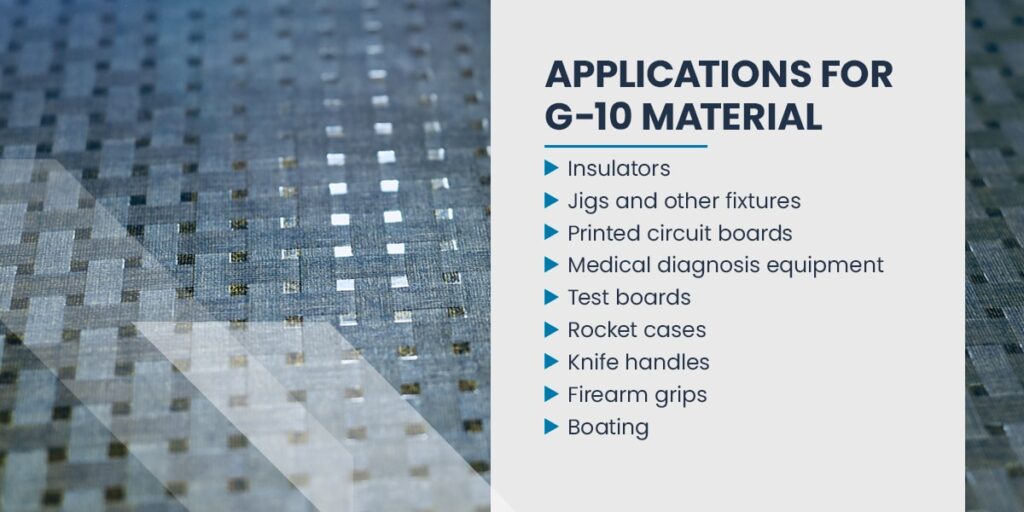
The adaptability of G10 sheets allows their use across a broad range of applications, from electrical insulation to mechanical components and specialty items. Here are some frequent uses for G10 sheets across various sectors.
Electrical Insulation
One of the most common uses for G10 sheets is in the realm of electrical insulation. Their strong insulation performance in both wet and dry states makes them an ideal choice for this purpose. G10 sheets are widely employed in the electrical insulation industry for:
- Insulators
- Jigs and fixtures
- Circuit boards
- Spacers and standoffs
- Transformer components
The excellent electrical properties of G10 sheets, including their good dielectric loss properties and excellent electrical insulation, along with their continuous operating temperature, not only provide a reliable and safe solution for various electrical applications but also contribute to their versatility and usefulness in other industries.
Mechanical Components
G 10 sheets are also frequently used for the fabrication of mechanical components, such as electronic, mechanical, and robotic parts. The high strength to weight ratio, superior tensile strength, durability, and excellent dielectric properties make G 10 sheets a popular choice for these applications.
Industry-wise, G10 sheet mechanical components are especially common in electronics, robotics, and mechanical applications industries. The use of G10 sheets in these components can greatly improve their durability and longevity, ensuring optimal performance and reliability.
Specialty Items
G10 sheets can also be employed to create a variety of specialty items, such as knife handles, terminal boards, washers, sleeves, structural components, and parts for electronics, robotics, and mechanical applications. In addition, they can be used in the production of musical instruments, automotive components, and even art installations or sculptures.
The adaptability and versatility of G10 sheets make them an attractive material for crafting unique items. Whether you’re working on a small-scale project or a large, commercial endeavor, G10 sheets can provide the strength, durability, and customization options you need.
Purchasing and Working with G10 Sheets
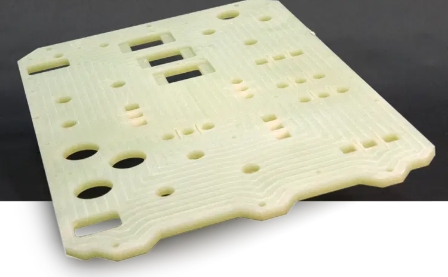
When it comes to purchasing and working with G10 sheets, there are several key factors to consider. These include selecting the right thickness and size, cutting and finishing techniques, and the importance of fast delivery and stock availability.
This section will address considerations, including humid or moist conditions, aiding you in making optimal choices for your project when materials can be safely substituted.
Selecting the Right Thickness and Size
Selecting the right thickness and size of G10 sheets is key to achieving the best performance and durability for your project. To determine the optimal thickness, it is important to consider the intended purpose or application, strength requirements, and the desired level of flexibility or rigidity. Consulting with experts or suppliers can provide guidance based on your specific project needs.
G10 sheets are available in various sizes and thick options, such as 1/4 inch (6.35mm) and 5mm thickness variations, or size variations from 12 x 24 inches to 600mm x 1200mm. By carefully selecting the right size and thickness, you can ensure that your G10 sheet will meet the requirements of your project and perform reliably.
Cutting, Drilling, and Finishing
Using suitable cutting, drilling, and finishing techniques is important when working with G10 sheets to achieve a professional outcome. G10 sheets can be cut with various tools, such as a grinder, table saw, hacksaw, or bandsaw, but for optimal results, it’s recommended to use a diamond blade on a wet tile saw or a high-quality bi-metal band saw. For drilling, a carbide drill bit specifically designed for G10 material is recommended, along with proper safety measures and techniques to prevent cracking.
Proper finishing is necessary after cutting or drilling the G10 sheets. This includes cleaning the area with acetone, smoothing out any rough edges, and applying a protective coating or finish. By following these procedures, you’ll achieve a professional and polished result that can enhance the overall appearance and performance of your G10 sheet.
Fast Delivery and Stock Availability
Fast delivery and stock availability are significant considerations when purchasing G10 sheets. Timely delivery ensures that you have access to the required materials quickly, minimizing waiting time and allowing your project to progress more efficiently. Inventory availability is essential for ensuring that the desired quantity of G10 sheets is readily available for purchase, avoiding delays and ensuring a seamless workflow.
When purchasing G10 sheets, consider the following factors:
- Price
- Quality
- Size
- Supplier
- Application
By prioritizing fast delivery and stock availability, you can ensure that your project progresses smoothly and stays on track.
Summary
In conclusion, G10 sheets are an incredibly versatile and durable material with a wide range of applications, from electrical insulation to mechanical components and specialty items. By understanding the composition, features, forms, sizes, and applications of G10 sheets, as well as best practices for purchasing and working with them, you can make informed decisions that will lead to successful projects. So, embrace the power and versatility of G10 sheets and elevate your projects to new heights.
Frequently Asked Questions
What is the main difference between G10 and FR4?
FR4 is fire-retardant, which G10 does not possess, so FR4 is better suited for certain applications.
What are some common sizes for full G10 sheets?
Full G10 sheets typically come in 36″ x 48″ and 48″ x 96″ sizes.
What tools can be used to cut G10 sheets?
For optimal results, it is recommended to cut G10 sheets with a diamond blade on a wet tile saw or a high-quality bi-metal band saw.
Can G10 sheets be used for electrical insulation applications?
Yes, G10 sheets can be used for electrical insulation applications due to their strong insulation performance in both wet and dry states.
What is the tensile strength of G10 sheets?
G10 sheets have a tensile strength of approximately 40,000 psi in the lengthwise direction and 35,000 psi in the crosswise direction.