When precision and customization are paramount, finding the right plastic machine shop is essential. Discover the versatility and precision of modern plastic machining, and learn what to look for in a shop to ensure your project objectives are seamlessly met.
Key Takeaways
Custom plastic machining incorporates techniques like cutting, turning, milling, and drilling to create high-precision parts, benefiting from the cost-effectiveness and versatility of plastics.
CNC machining, especially 5-axis CNC machining, is crucial for creating intricate designs with tight tolerances, suitable for various industries including aerospace, automotive, and medical.
Selection of a plastic machine shop should be based on factors such as expertise in translating project specifications, material selection assistance, quality assurance, and their ability to provide quick turnarounds.
The Art of Plastic Machining
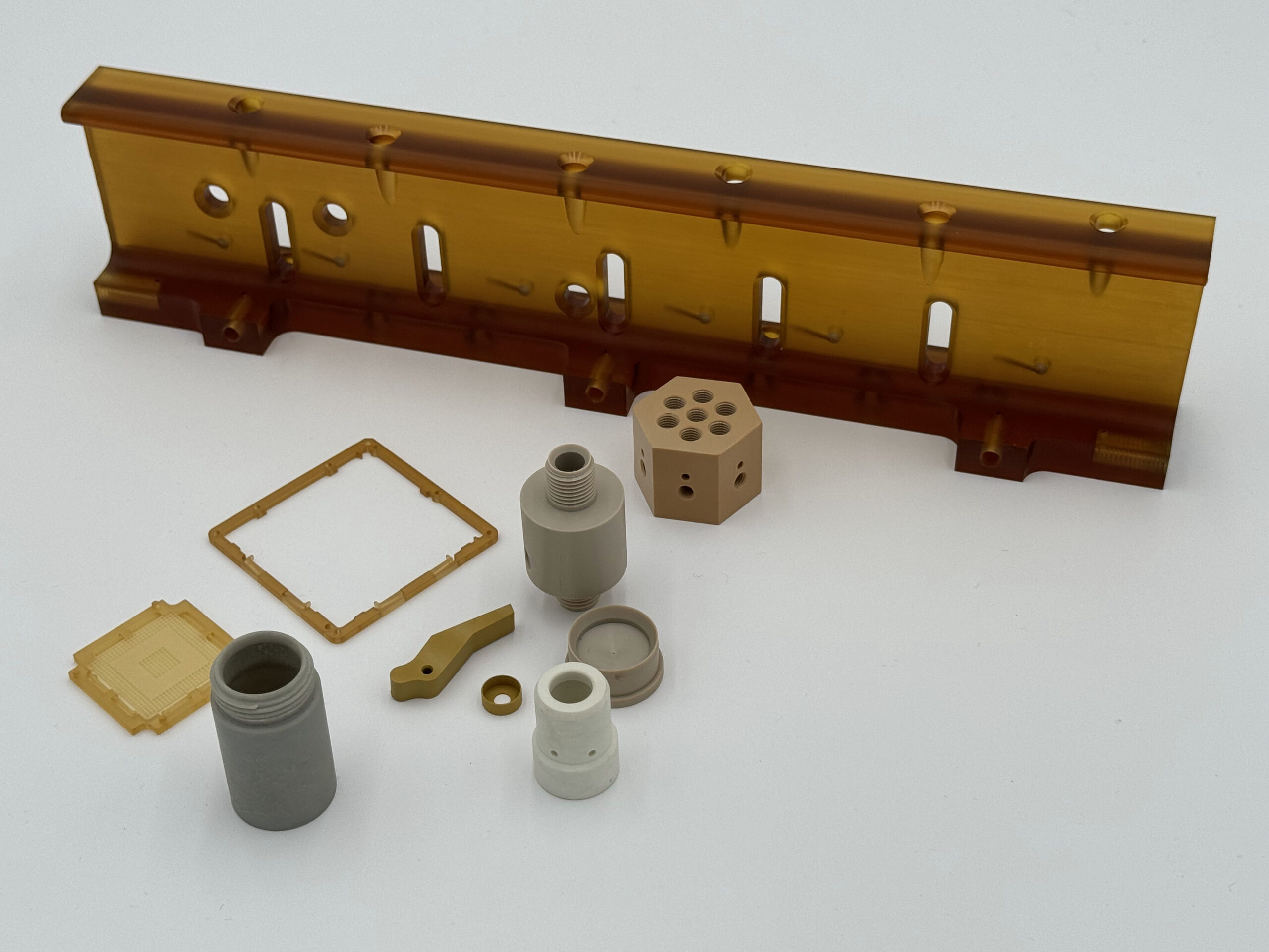
Custom plastic machining is a fundamental process in manufacturing specialty products, playing an indispensable role in producing high-quality, custom parts for various applications. With plastic machining solutions, this process involves a plethora of techniques, including:
Cutting
Turning
Milling
Drilling
Grinding
Each technique contributes to the creation of the final product.
Understanding Plastic Machining
Plastic machining at its fundamental level is a subtractive process. It involves carving out desired shapes and sizes from a solid plastic block through techniques such as:
Cutting
Turning
Milling
Drilling
Grinding
For instance, the turning process involves using a lathe to cut material away from a rotating workpiece, while milling and routing use rotating cutting tools to remove chips from a stationary workpiece. However, as straightforward as it may sound, plastic machining is not without its challenges. Drilling can present issues such as shearing and overheating, necessitating careful tool selection and management to prevent damage to the workpiece.
Additionally, grinding and lapping are essential finishing processes that produce smoother finishes on machined plastic parts.
Advantages of Plastic Machining
Many factors contribute to the popularity of plastic machining, not least of which are the numerous benefits it offers. Precision, cost-effectiveness, versatility, and efficient production are among the key advantages. For instance, the use of plastics in machining facilitates high-precision work on complex applications such as gears and bearings, further enhanced by the use of advanced CAD-CAM software to optimize tool paths.
Moreover, compared to metals, the total cost of machining plastics is lower due to both the precision of CNC machining and the availability of affordable materials like ABS and Nylon. Furthermore, plastic materials offer versatility in machining, allowing for the production of complex and intricate components that require high precision.
Customized CNC Machining Solutions
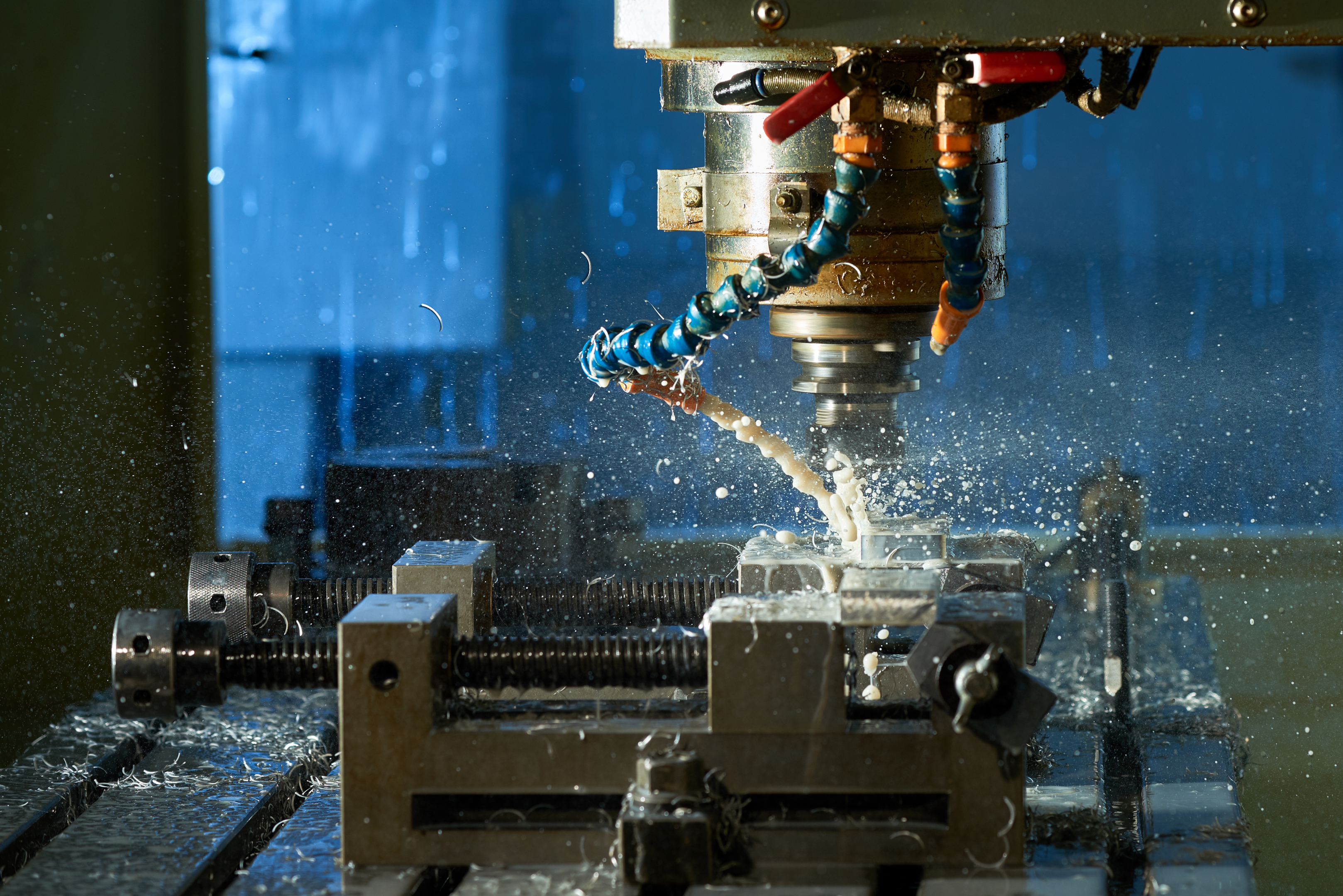
Let’s examine CNC plastic machining, a notable process that yields components with impressive tight tolerances and precise dimensions. The uniformity and accuracy provided by CNC machining, using a cnc machine, make it versatile for a multitude of applications. It’s the preferred choice for high-precision part requirements, distinguished by its capability to create intricate designs and complex shapes with high precision.
Furthermore, 5-axis CNC machining enables:
The efficient production of complex shapes, eliminating the need for multiple setups and thus saving time
The efficient production of prototypes
High-volume output of identical products
CNC Milling and Turning
CNC milling and turning play a pivotal role in the plastic machining process. CNC milling involves using a rotating cutting tool to remove material from a workpiece, enabling the creation of parts with complex geometries and fine details. On the other hand, CNC turning operates by rotating a workpiece on a lathe against a cutting tool, ideal for creating symmetrical components like rods, shafts, and spindles, and is adaptable for straight or taper turning operations.
Both milling and turning can maintain tighter tolerances and produce high precision parts essential for high-precision applications such as aerospace, medical, and automotive industries. Furthermore, 5-axis CNC machining enables simultaneous movement along multiple axes, creating highly detailed and complex parts with consistent quality, which ultimately improves project efficiency by reducing costs and enhancing part quality.
Material Considerations
Choosing the right material is crucial for successful CNC machinability. It influences aspects such as cutting speed, feed rates, and tool choice, while also considering environmental factors like exposure to sunlight and temperature.
Plastics, as a type of plastic material, include:
Polycarbonate
ABS
Nylon
PEEK
Acetal (Delrin)
HDPE
G10/FR4
CE
PMMA
offer a range of properties including strength, impact resistance, temperature tolerance, optical clarity, wear resistance, and chemical resistance, catering to diverse industry needs.
Experts provide critical assistance in selecting various materials, ensuring a balance between mechanical and thermal properties, cost, and the specific requirements of the application.
In high-volume production, high-performance plastics such as PEEK, PEI (Ultem), Torlon, and PPS are vital, as they can withstand extreme environments and conditions.
Expertise in Diverse Industries
A wide array of industries benefit from plastic machining services, including food and beverage, aerospace and automotive, as well as medical and pharmaceutical sectors. These services are essential for creating precision components used in these industries. For instance, Atlas Fibre has achieved success with high-volume plastic machining projects, showcasing their expertise in CNC milling for automotive and medical devices, alongside semiconductor and construction components through injection molding.
Industrial-grade materials like PEEK, Ultem, and Torlon are utilized to craft high-performance parts for demanding applications including medical implants, aerospace equipment, and automotive parts.
Food and Beverage
In the food and beverage industry, plastic components are integral to maintaining strict hygiene standards and adhering to food safety regulations. Ultra-high-molecular-weight polyethylene (UHMWPE) is commonly employed in this sector for its strength and adherence to food safety regulations. Plastic components resist corrosion and are easy to sanitize, making them crucial for food processing equipment.
Food packaging machinery also benefits from the use of machined plastics, which uphold durability standards and prevent contamination of foodstuffs during packaging. Companies like Atlas Fibre have made significant contributions to the food processing industry by designing specialized components tailored to the unique needs of their clients.
Aerospace and Automotive
The aerospace and automotive industries heavily rely on plastic machining, including nylon machining. CNC milling and turning are essential in these industries due to their ability to maintain tight tolerances required for high-precision applications. Polyamide, known for its low-friction, high impact strength, chemical and abrasion resistance, is a favored material in the automotive industry and is also fit for medical applications.
In the aerospace sector, precision-machined plastics are utilized for components such as interior cabin parts, insulation, and structural elements to achieve weight reduction and enhanced fuel efficiency.
Medical and Pharmaceutical
In the medical and pharmaceutical sectors, precision-machined plastic parts are crucial. These parts are required for their biocompatibility, sterilizability, and tight tolerance manufacturing. Medical equipment is often subjected to frequent sterilization, making the high durability and precision offered by CNC machining indispensable. Moreover, machined plastics are favored in pharmaceutical equipment for their excellent chemical resistance, which helps avoid drug reactions and ensures patient safety.
Engineering plastics are widely used in pharmaceutical manufacturing, providing robustness and precision for creating equipment, drug delivery systems like inhalers and syringes, and secure drug packaging.
Choosing the Right Plastic Machine Shop
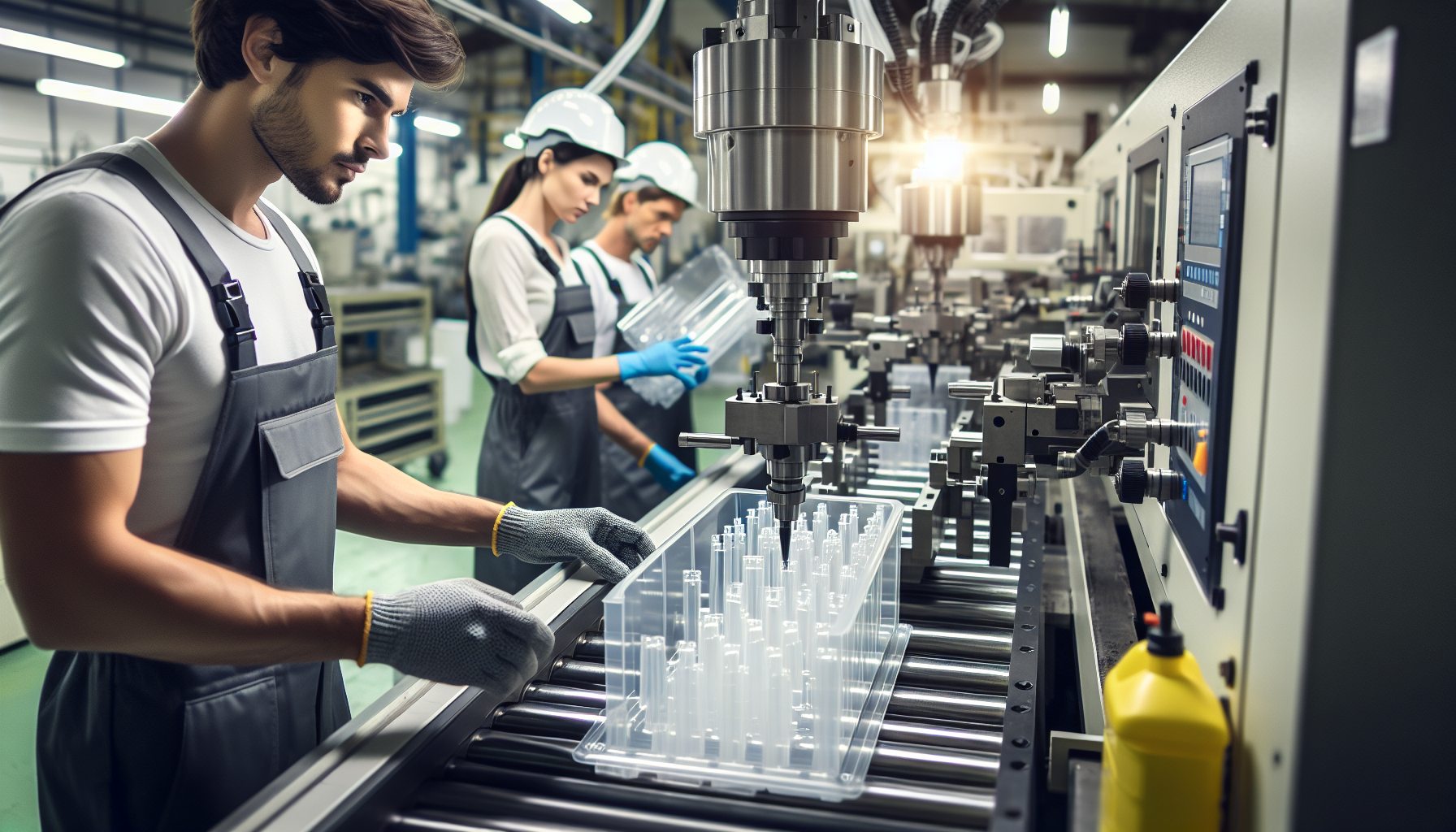
Selecting an appropriate plastic machine shop requires careful consideration of various factors. These include:
How well they can translate project specifications into the final product
Whether they understand client budgets and offer a range of applications for plastic parts
Their commitment to building lasting partnerships with clients
Selecting the most appropriate material within budget constraints is essential, needing a balance between cost and project requirements. Material selection assistance plays a vital role in reducing costs by finding economical materials that still fulfill the required specifications and performance needs.
Quality Assurance
Quality assurance is a significant consideration when selecting a plastic machine shop. Here are some benefits of choosing an ISO-certified plastic machine shop:
Enhanced product quality
Customer satisfaction
Access to new markets
Competitive edge
Efficient processes
Choosing a machine shop with ISO 9001 certification ensures established processes for quality management, skilled and competent employees, and well-documented procedures contributing to streamlined operations.
Moreover, quality control measures and the use of advanced machinery and techniques are key to producing precise, durable, and reliable plastic components that meet customers’ expectations, made from high quality materials.
Experienced Professionals
The team’s proficiency in plastic machining is another vital consideration. A skilled team is vital to creating high-quality products and providing solutions and advice for common manufacturing issues. Access to a wide array of advanced machinery enables experienced staff to produce diverse and intricate plastic machined parts.
Knowledgeable staff play a critical role in the material selection process, offering insights into material properties and their impacts on the machining process.
Quick Turnaround and Flexibility
Rapid service and flexibility also constitute important elements to consider when selecting a plastic machine shop. CAD-CAM software significantly reduces the time required for planning and task distribution, providing quicker project turnarounds. CNC machining is especially beneficial for rapid prototyping in industries like automotive and defense, helping to iterate designs swiftly and bring innovations to market faster.
Plastic machine shops like Atlas Fibre offer:
Full-range machining services
Rapid turnaround for prototyping
Competitive pricing for production
Flexibility to adapt to project demands
Innovative Techniques and Technologies
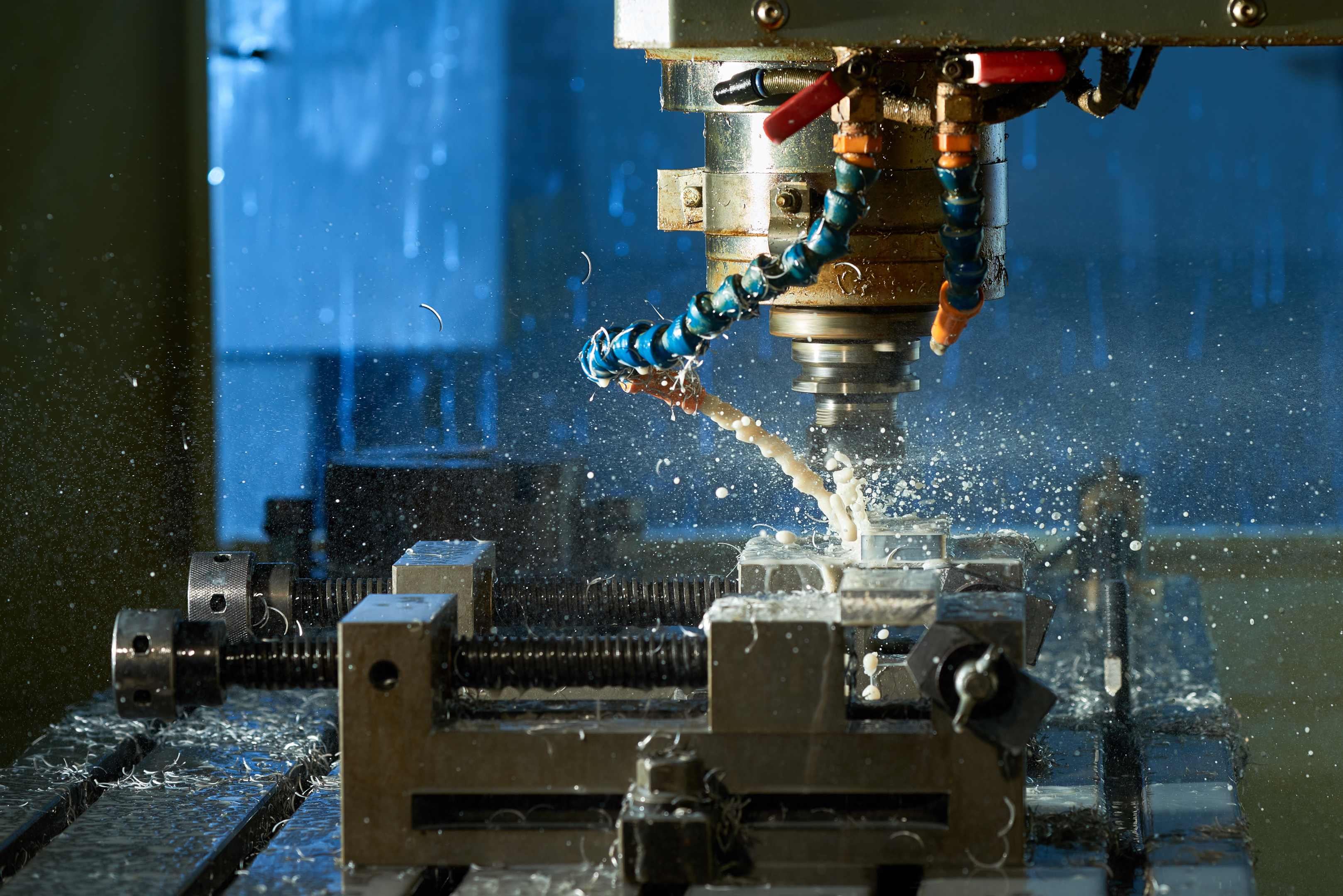
Innovation remains vital in the fast-paced world of manufacturing. Leading plastic machine shops specialize in high-performance plastic machining, addressing the sophisticated challenges it presents through innovative techniques. The incorporation of advanced CAD-CAM software into plastic machining processes allows for the crafting of more precise and complex designs while providing flexibility in design modification.
Material selection assistance is another critical service offered by top plastic machine shops, aiding clients in choosing appropriate materials that meet the specific strength, durability, and resistance requirements of their projects.
5-Axis CNC Machining
5-axis CNC machining is a notable innovative technique utilized in plastic machining. This technique enables the production of highly complex shapes and intricate details that are not possible with conventional machining techniques. With fewer setups required, 5-axis machining increases the overall accuracy and precision of the plastic parts being manufactured. Moreover, the CNC machining process on a 5-axis machine can produce smoother finishes on plastic parts, leading to components that effectively function within their intended assemblies without additional finishing.
High-quality surface finishes from 5-axis machining might eliminate the requirement for additional post-processing steps, contributing to cost savings. Furthermore, the rapid production capabilities associated with 5-axis CNC machining allow for quicker time-to-market for new products and a responsive adaptation to customer needs. However, precision work in 5-axis plastic machining necessitates careful handling techniques, appropriate tooling, and attentive thermal management to prevent warping and maintain quality.
Advanced CAD-CAM Software
Another pioneering technology in plastic machining is the use of advanced CAD-CAM software. This software provides improved job programming control which contributes to more efficient modification and enhancement of CNC machining processes. Integrating CAD-CAM software into manufacturing ensues better control and monitoring, leading to higher accuracy and precision, as well as fewer errors in the production of CNC milled parts.
CAD-CAM systems aid in enhancing productivity by enabling CNC machines to operate autonomously, which allows the exploration of more advanced techniques and designs. Moreover, the simulation capabilities of CAD-CAM technology enable the visualization and optimization of the machining process before actual production, saving time and reducing waste by identifying issues early on.
Lastly, the compatibility of CAD-CAM software with widely-used CAD platforms, often as plug-ins, simplifies the CAM machining process, streamlining workflow for users already familiar with CAD software.
Material Selection Assistance
Top plastic machine shops offer essential service in the form of material selection assistance. Technical staff provide professional recommendations based on the application requirements, guiding clients through selecting materials that align with the desired machining processes and the end use of the manufactured parts.
Consultants can offer valuable insights into new materials and their advantages for particular industries or applications, fostering innovation and giving clients a competitive edge.
Case Studies: Success Stories in Plastic Machining
Real-life success stories provide the best insight into the capabilities of plastic machining. These case studies demonstrate the plastic machining process’s success in creating components that fit the exact needs of clients. Custom plastic machined parts are instrumental in achieving the performance expected from specialty applications across various industries.
These success stories underscore the capability of machine shops to engineer and manufacture parts that satisfy even the most demanding criteria.
Custom Component Design
Designing custom components forms an integral part of plastic machining. The objective of precision plastic machining is to produce items according to individual specifications, ensuring unique requirements are met. The result is parts that are perfect fits for their intended uses, fulfilling the exact needs of clients.
High-Volume Production
Moving on to the topic of high-volume production, Automation and robotics enhance efficiency, precision, and maintain consistent quality control in high-volume plastic machining operations. To ensure economic manufacturing of variable workpieces in both small and repeatable batches, Flexible Manufacturing Systems (FMS) are employed.
These systems offer adaptability from initial prototyping to full-scale production.
Summary
In conclusion, plastic machining and CNC machining play a pivotal role in the manufacturing process, offering precision, cost-effectiveness, and versatility. Whether it’s creating high-quality, custom parts for various applications or catering to diverse industries, these processes make it all possible. With the help of innovative techniques and technologies, plastic machine shops can deliver products that precisely match specific specifications and unique industry or application requirements. Choosing the right plastic machine shop involves considering factors such as quality assurance, experienced professionals, and quick turnaround times. Whether you are in the food and beverage, aerospace and automotive, or medical and pharmaceutical industry, there’s a plastic machining solution for you.
Frequently Asked Questions
What is plastic machining?
Plastic machining is a vital process involving cutting, turning, milling, drilling, and grinding to produce high-quality, custom parts for various applications.
How does CNC milling and turning work?
CNC milling uses a rotating cutting tool to shape materials for complex parts, while CNC turning involves rotating a workpiece against a cutting tool to create symmetrical components.
What industries benefit from plastic machining services?
Plastic machining services benefit industries such as food and beverage, aerospace and automotive, and medical and pharmaceutical sectors.
What factors should I consider when choosing a plastic machine shop?
When choosing a plastic machine shop, consider factors such as quality assurance, experienced professionals, and quick turnaround times. An ISO 9001 certification is a good indicator of a shop’s commitment to quality assurance.
What innovative techniques are used in plastic machining?
In plastic machining, innovative techniques like 5-axis CNC machining and advanced CAD-CAM software are used to improve precision and efficiency. These technologies enhance the overall machining process.