If you’re trying to determine whether silicone is a match for your chemical exposure needs, knowing its silicone chemical compatibility is crucial. This unambiguous guide examines the relationship between silicone and a variety of aggressive chemicals like acids, bases, solvents, oils, and fuels. We highlight the conditions that influence silicone’s resilience and point out when it falls short. By the end, you’ll possess the insights necessary to make a well-informed choice about using silicone in any project or application.
Key Takeaways
Silicones, due to their unique molecular structure, exhibit low chemical reactivity and maintain properties across a wide temperature range, making them suitable for various applications such as medical devices, cooking utensils, and insulation materials.
Chemical compatibility of silicone varies with conditions such as temperature, concentration, and duration of exposure; it offers good resistance to many chemicals, with certain types like fluorosilicone showing enhanced resistance, though some substances like chloroform and hydrofluoric acid adversely affect it.
Silicone is used across diverse industries, including aerospace, automotive, and medical, for its flexibility, durability, and resistance to extreme temperatures and environmental conditions; however, specific applications require thorough testing and validation for optimal performance.
Silicone Material Overview
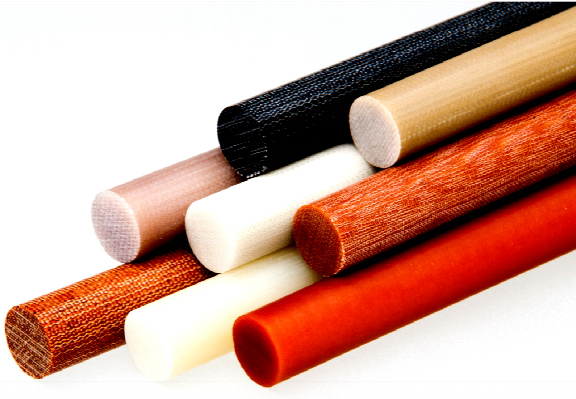
Silicones, these fascinating polymers also known as polysiloxanes, consist of alternating silicon and oxygen atoms. This unique configuration, often combined with carbon and hydrogen, bestows upon silicones a versatile framework, enabling the creation of materials with a broad spectrum of properties. Characterized by low chemical reactivity, low thermal conductivity, and the ability to maintain their properties across a wide temperature range, silicones find themselves suitable for challenging applications.
For instance, Polydimethylsiloxane (PDMS) is versatile, finding its way into various products and applications, including:
Oils
Rubber-like substances
Medical devices
Cooking utensils
Insulation materials
Furthermore, the inherent low thermal conductivity of silicones can be tailored to specific uses by incorporating thermally conductive fillers, thus meeting the requirements of different applications.
Advantages of Silicone
Silicones have earned their place in the world of materials science due to their ability to resist extreme temperatures and harsh environmental conditions such as heat, water, and UV light. This makes them indispensable in industries like construction and automotive, where materials are often subjected to rigorous conditions. But that’s not all! The mechanical properties of silicone can be customized to meet a variety of needs. They can exhibit a wide spectrum of hardness, tensile strength, and elasticity, making them perfect for water-based products and ensuring user comfort. Furthermore, their lightweight nature and natural water repellency add to their appeal.
The insulation properties of silicone make it standout in the electrical industry. It’s a favored choice for a multitude of applications – from simple wires to complex electronic devices – as it can be engineered to be either electrically insulative or conductive.
Types of Silicone
Diverse applications demand a variety of silicone forms. Among the most common are High Consistency Rubber (HCR) and Room-Temperature Vulcanizing (RTV) silicones. HCR, also known as high consistency silicone rubber (HCSR), is favored for products requiring a harder, more durable material. For instance, industrial seals and gaskets benefit immensely from the resilience offered by HCR.
On the other hand, when a durable, flexible, and high-adhesion material is the need of the hour, RTV silicone steps up to the plate. It is especially favored for sealants and adhesives in the construction industry, ensuring a strong bond that can withstand the test of time and environmental influences.
Chemical Compatibility of Silicone
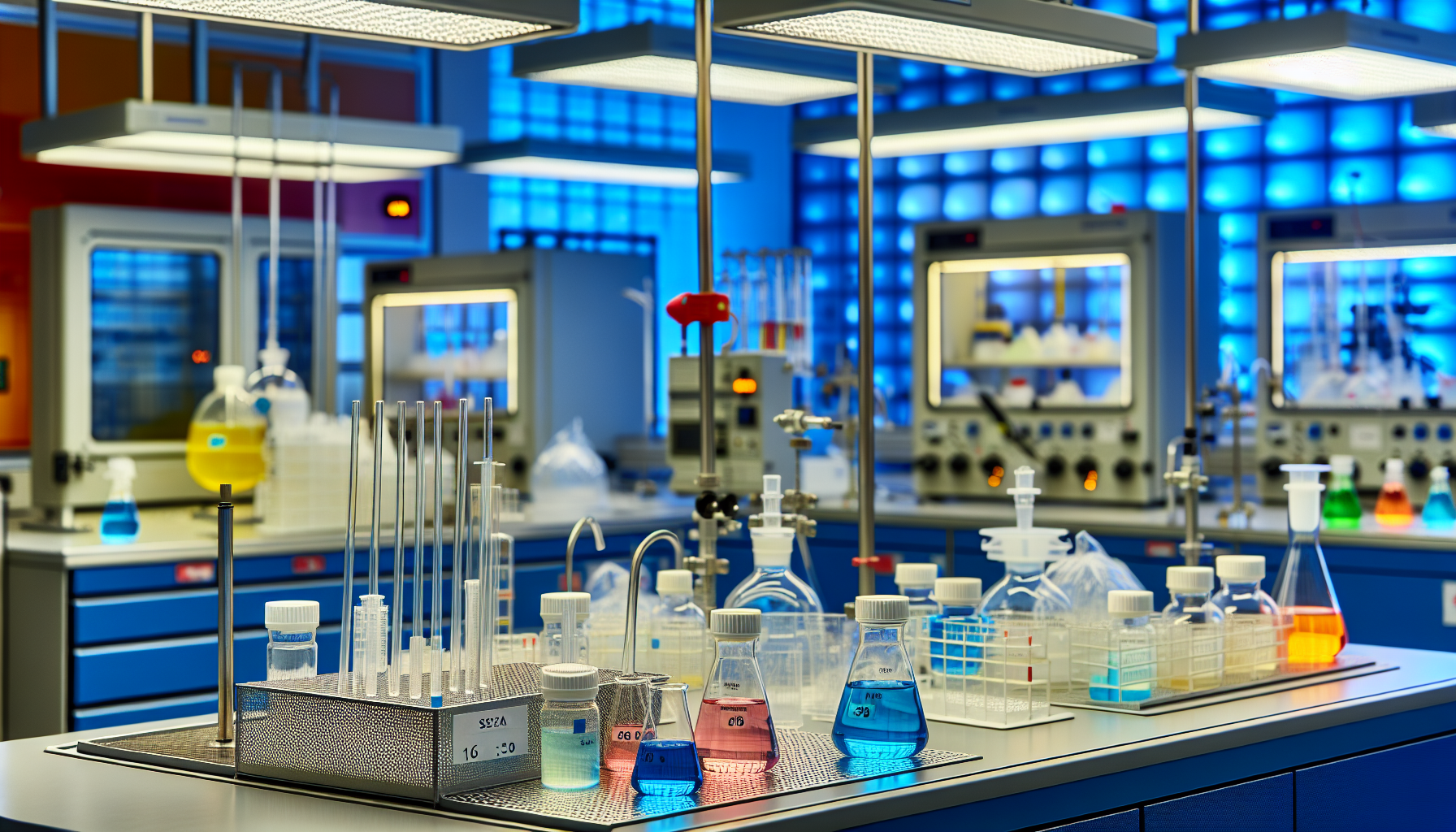
The excellent resistance of silicone to oxygen, ozone, and UV light, largely due to its robust silicon-oxygen bonds, is a crucial aspect of its versatility. Specialty silicone types, such as fluorosilicone, offer enhanced chemical resistance, proving beneficial in extreme chemical environments. Silicone’s resistance to a broad spectrum of chemicals, including but not limited to acetic acid, aluminum sulfate, arsenic acid, and benzoic acid, is noteworthy, especially at room temperature. It is also highly compatible with ammonia and shows good compatibility with several alcohols, such as butyl alcohol, isopropyl alcohol, and methyl alcohol.
However, silicone’s compatibility with substances is not universal. It exhibits conditional resistance to substances like concentrated ammonium hydroxide and severe incompatibility with chloroform and aromatic hydrocarbons. Furthermore, it is not resistant to hydrofluoric acid or compatible with acetone, which can have severe effects on the material.
Acids and Bases
Silicone demonstrates impressive resistance when exposed to acids and bases. It holds its own against acetic acid at room temperature and performs well with citric acid. Yet, not all acids are treated equally by silicone. It does not resist hydrofluoric acid at 5% concentration, and its resistance to nitric, sulfuric, and hydrochloric acid is limited, especially at higher concentrations. However, when faced with phosphoric acid at 30% at room temperature, silicone stands strong.
On the base front, silicone resists ammonium hydroxide even in concentrated form and potassium hydroxide, even at a significant concentration of 50%. It also displays good compatibility with barium hydroxide, potassium bicarbonate, potassium carbonate, sodium carbonate, sodium hydroxide, potassium nitrate, and sodium nitrate, demonstrating its viability in various alkaline environments. Additionally, sodium benzoate is another substance that silicone can resist. However, silicone’s resistance to certain acids and bases can be conditional, as is the case with 10% nitric or sulfuric acid at room temperature, but not their concentrated forms.
The compatibility of silicone goes beyond just acids, such as oxalic acid, and bases. It is also compatible with aluminum potassium sulfate and zinc sulfate in all concentrations and shows good compatibility with aluminum chloride. Even though its compatibility with acetic anhydride and acetyl chloride (dry) is only fair, this demonstrates silicone’s potential use in environments with various chemical exposures, including calcium chloride.
Solvents
Silicon’s compatibility with solvents varies significantly. Here are some examples:
It works well with butyl alcohol and carbitol
Its resistance to butanol is conditional at a temperature of 117°C
Silicone displays conditional resistance to acetone at 20°C, but it demonstrates excellent compatibility with diacetone alcohol
Chloroform at 20°C, however, is a no-go for silicone.
Some solvents, like carbon tetrachloride at 20°C, butyl acetate at 20°C, methanol at 65°C, methyl chloride at 20°C, and toluene at 20°C, can only be tolerated by silicone under certain conditions. Nonetheless, silicone maintains good compatibility with ethyl acetoacetate and ethyl benzene, and with diethylene glycol, although it has severe incompatibility with dioxane and methyl ethyl ketone peroxide.
Oils and Fuels
The resistance of silicone to oils and fuels fluctuates. It demonstrates resistance to various oils like:
olive oil
vaseline
coconut oil
corn oil
soybean oil
at high temperatures, and to mineral oil and transformer oil under certain conditions. Diesel oil is where silicone’s resistance becomes conditional, while it presents severe incompatibility with oils derived from diesel and unleaded gasoline, as well as fuel oils.
However, Fluorosilicone Rubber (FSR) enhances silicone’s resistance to oils and fuels, making it particularly useful in industries like aviation.
Factors Affecting Chemical Resistance
The chemical compatibility of silicone is not fixed and varies with changing conditions. Temperature plays a significant role, with silicone materials remaining satisfactory for use up to specific temperature thresholds, such as 72°F (22°C) or 120°F (48°C). Extreme temperatures can dramatically influence chemical reactions and the performance of silicone seals. Even compatibility charts for silicone may indicate different resistance ratings for a single substance at various temperatures, reflecting changes in resistance with temperature fluctuations.
The concentration of the substance also significantly impacts the chemical compatibility of silicone membranes, as different concentrations can affect silicone’s suitability for certain applications. Furthermore, the length of exposure to a chemical substance impacts the chemical resistance of silicone materials, with prolonged contact with certain substances potentially deteriorating silicone over time. Even pressure can affect the chemical resistance of silicone materials.
Guidelines for Selecting the Right Silicone Material
Choosing the right silicone material is not a straightforward process. It entails considering operational conditions such as the type of application (static or dynamic), temperature range, and pressure levels. Industry-specific requirements or regulations, particularly those concerning environmental factors, must also be taken into account.
A reliable method for finding silicone materials with the necessary resistance to specific media involves utilizing industry leader charts, like the Parker chemical compatibility chart.
Material Selection Criteria
A few important considerations need to be made when selecting a silicone material. Silicone’s chemical resistance is a key factor, as demonstrated by its excellent resistance to acetic acid and carbonic acid in concentrations up to 80%. The application type—whether static or dynamic—significantly influences the silicone material’s longevity and ability to resist chemical degradation.
Pressure conditions within a given application are also critical, as higher pressures may compromise the chemical resistance of silicone materials.
Testing and Validation
It’s important to test and validate the material under real or simulated conditions as part of the selection process. It is recommended to verify the chemical compatibility of silicone seals in their intended application to ensure optimal performance. Since manufacturer compatibility charts are generalized, conducting your own tests under the specific conditions of your application is necessary for accurate material assessment. For specialized applications, testing silicone materials against specific industrial chemicals like fuels, oils, and acids can provide a more accurate evaluation of their compatibility.
Additionally, the assessment of material properties such as tensile, compression, and hardness is crucial, as these properties can be influenced by chemical interactions and are integral to material validation.
Common Applications and Industries
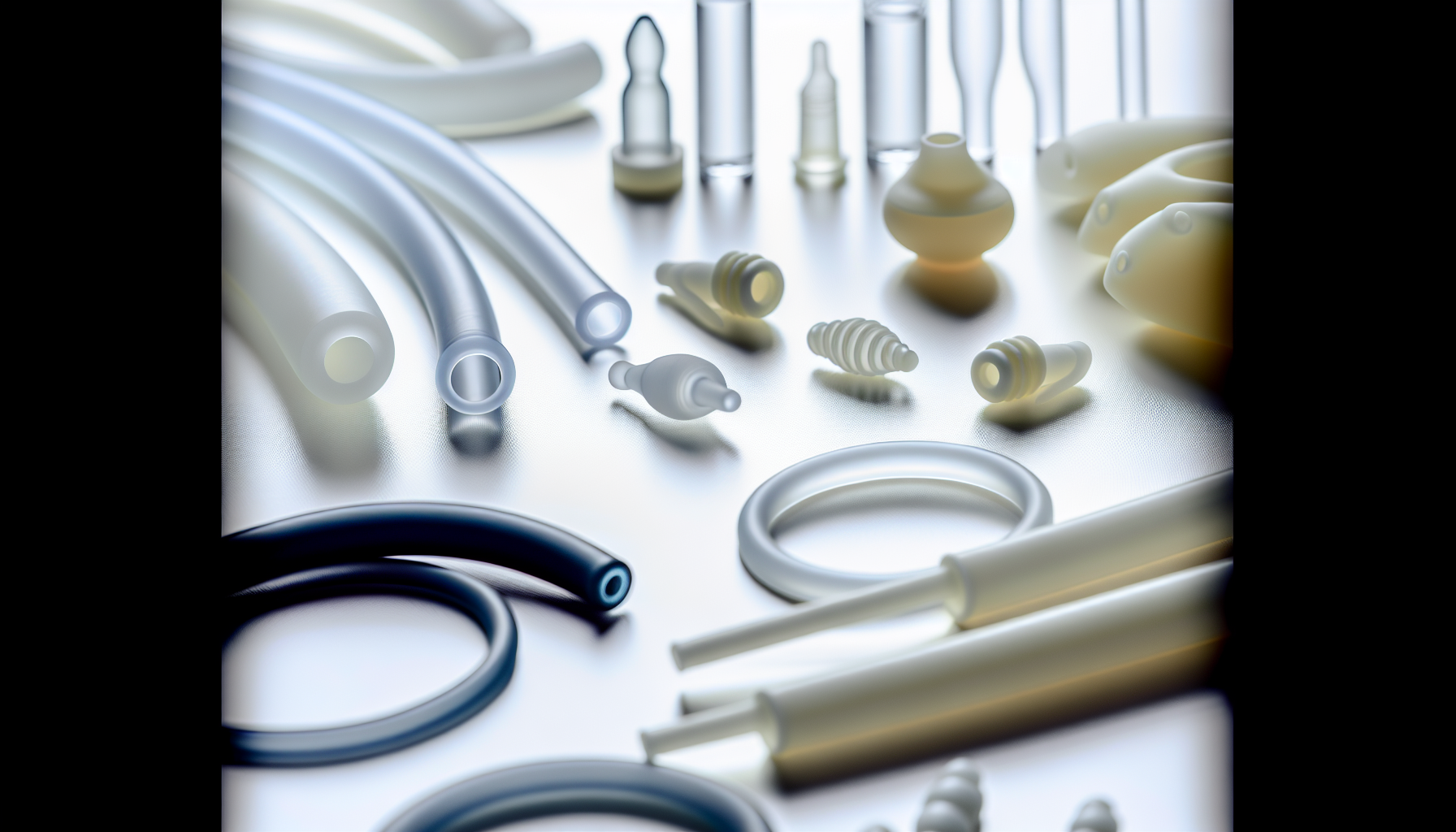
Silicone is utilized in a broad spectrum of applications and industries. Silicone-enhanced paints offer exceptional flexibility to exterior coatings for buildings, roads, and marine vessels, thus preventing cracking under harsh environmental conditions. Silicone resins are a prime choice for paints and coatings in various architectural applications because of their durability and resistance to environmental degradation.
In the aerospace sector, silicones are indispensable for bonding materials, sealing joints, and coating electronic components to safeguard against extreme temperatures and harsh weather. RTV silicones cater to aerospace needs with formulations ranging from low-viscosity types for thermal protection to high-viscosity options suited for application to overhead surfaces. Critical aerospace applications, such as bonding lenses to telescopes and securing optics on satellites, rely on silicone adhesives that maintain properties across extreme temperature ranges.
The food and beverage industry also utilizes silicones largely for foam control, as a manufacturing release aid, and to streamline production processes. Food-grade silicones, including antifoams, emulsions, and fluids, feature prominently in the production of pesticides, syrup processing, edible oil manufacturing, as well as brewing and fermentation.
Medical Devices
Given its resistance to microbiological growth and biocompatibility, silicone is a preferred material in the realm of medical devices. It can withstand prolonged contact with body tissues and is used in the production of items such as tubing, seals, and implants.
Two notable types of silicone used in medical devices include Liquid Silicone Rubber (LSR), which is used for molded products, and High Consistency Rubber (HCR), which accommodates fillers for various device characteristics like tubing and sheets. Silicone rubber’s high gas permeability is particularly beneficial for medical devices that require aeration, although it is not recommended for applications that need gas-tight seals.
Automotive Components
Due to its ability to endure high temperatures and harsh conditions, silicone is ideal for automotive applications like gaskets, hoses, and seals. Silicone materials like the Permatex 82180 Ultra Black Maximum Oil Resistance RTV Silicone Gasket Maker are specifically valued in the automotive sector for their exceptional oil resistance, suitable for use in oil pans and valve covers.
The high flexibility inherent to silicone materials ensures that automotive seals maintain integrity when subjected to vehicle movements and contact with oils.
Electronics and Electrical Insulation
In electronics, silicone is used for various purposes, including:
Sealing circuit components to protect them from heat, shock, and debris
Acting as an adhesive to bond different parts together
Coating circuit components to enhance energy efficiency and connectivity
Silicone rubber is particularly useful in electronics because of its insulation properties and moisture resistance. It is an effective encapsulant for electronic components and a sealant for electronic enclosures. Silicone is permeable to water vapor but not to liquid water, making it ideal for protecting electronic devices from moisture damage.
Silicones are also employed as conductive adhesives and encapsulants for solar panels, capitalizing on their environmental stability and transparency to improve the efficiency and longevity of the panels.
Summary
In this exploration of silicone chemical compatibility, we have traversed the landscape of silicone types, their properties, and their varied uses across industries. We have delved into the chemical compatibility of silicone with various substances, the factors affecting its resistance, and how to select the right silicone material for specific applications. As we conclude, remember that silicone’s versatility is its strength. It can be tailored to meet the needs of a wide array of applications, making it an invaluable asset in numerous industries. So, the next time you encounter a silicone product, pause and marvel at the science behind this remarkable material.
Frequently Asked Questions
What chemicals damage silicone?
Only a few common materials, such as concentrated sulfuric acid, hydrofluoric acid, and high pressure steam, can damage silicone. Be cautious when exposing silicone to these chemicals.
Is silicone resistant to solvents?
Yes, silicone is generally resistant to solvents and industrial chemicals, with only a few exceptions like concentrated sulphuric acid and hydrofluoric acid. Long-term exposure to high pressure steam can also affect silicone.
What are the advantages of using silicone?
The advantages of using silicone include resistance to extreme temperatures and environmental conditions, customizable mechanical properties, and electrical insulation, making it suitable for various industries.
How can I select the right silicone material?
To select the right silicone material, consider operational conditions, industry-specific requirements, and consult compatibility charts for guidance.
Where is silicone commonly used?
Silicone is commonly used in construction, aerospace, food and beverage, medical devices, automotive components, and electronics due to its durability, flexibility, and resistance to environmental degradation. These industries benefit from its versatile properties.