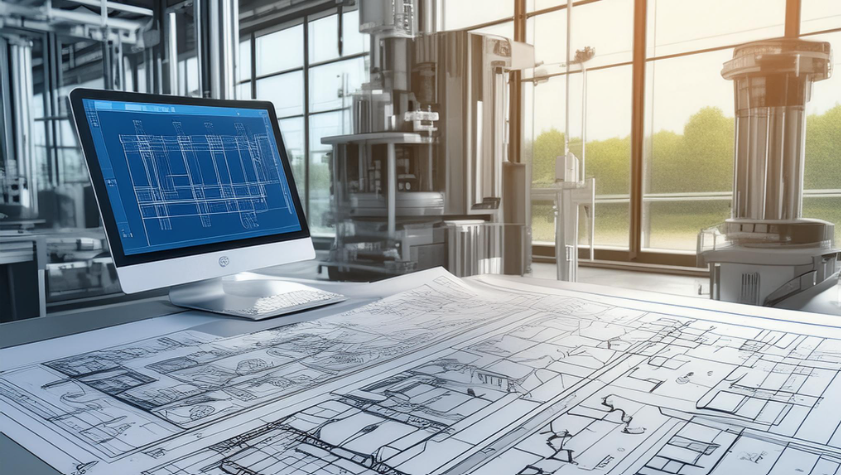
Working with thermoset composite materials requires an understanding of their unique properties and the extreme conditions they often experience.
At Atlas Fibre, our team of material specialists understands the critical importance of flexural strength in different applications and is experienced at guiding our clients towards the right material for the right project.
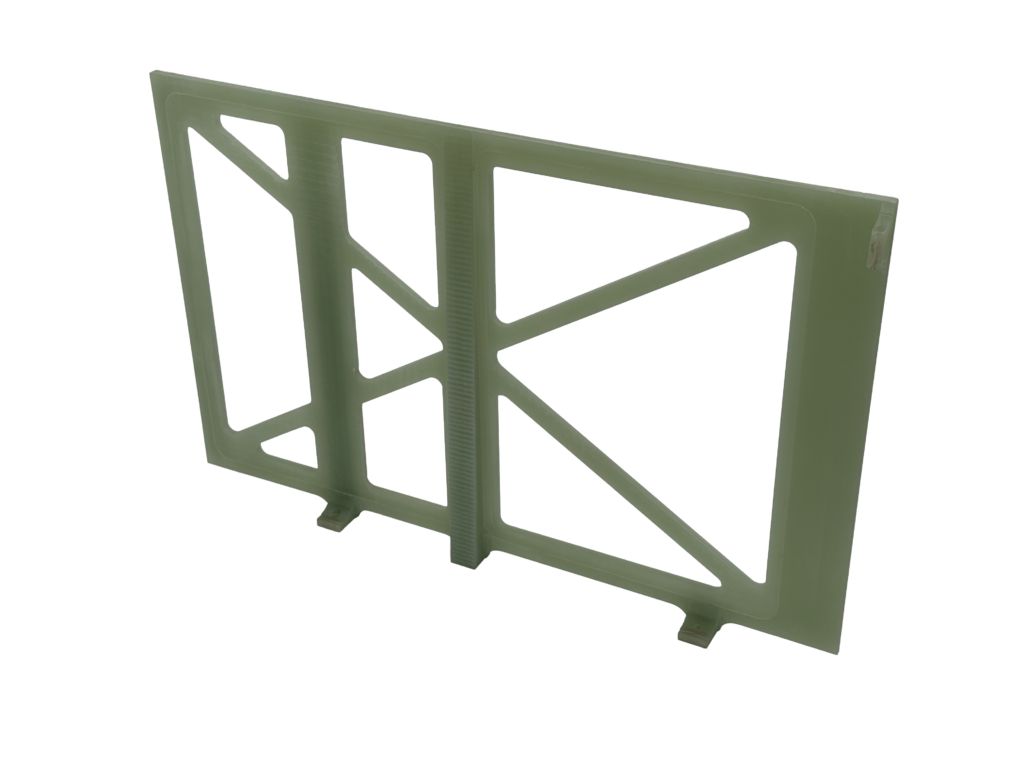
Flexural strength, also known as the modulus of rupture or bend strength, is a fundamental material property that indicates the maximum stress a material can withstand before yielding or fracturing under bending or flexural loads. Engineers responsible for selecting materials for applications such as beams, brackets, and structural components (components often experiencing the greatest bending or flexing loads in applications) find this property particularly pertinent.
To delve deeper into this subject, Atlas Fibre offers a comprehensive resource titled “Guide to Flexural Strength in Materials,” highlighting essential aspects of this property and its significance across various industry sectors and engineering practices. It’s a helpful guide and one that deserves closer examination, but if you’re new to thermosets start at the beginning with some of the basics including how flexural strength is actually determined, the factors that influence modulus of rupture in real-life applications, and the difference between flexural and tensile strength.
Determining the Flexural Strength of Thermoset Composites
Flexural strength is typically evaluated through a 3-point or 4-point bending test using a rectangular or circular cross-section of the material. In the 3-point test, the material rests on two cylindrical supports with a third loading cylinder applying force at the midpoint between them. Alternatively, the 4-point test positions two loading cylinders apart to better distribute the bending force, offering more accurate representation of material defect density.
Factors Influencing Flexural Strength
The flexural strength of thermoset composite materials is influenced by several factors, including the type, volume, and orientation of reinforcing fibers. As it relates to thermoset composites specifically, three of the more pronounced variables include:
- Fiber Type and Volume: The type of fibers (e.g., glass, carbon, natural fibers) and their volume fraction significantly impact the composite’s flexural strength.
- Matrix Material: The properties of the thermoset resin matrix (e.g., epoxy, phenolic) affect the overall flexural strength.
- Fiber-Matrix Interface: A strong bond between the fibers and matrix ensures effective load transfer and enhances flexural performance.
These variables, among many others including environmental conditions and temperature, collectively contribute to the material’s overall flexural performance.
Flexural Strength vs. Tensile Strength
It’s crucial to distinguish between flexural strength and tensile strength. Flexural strength pertains to a material’s ability to endure bending without breaking, whereas tensile strength measures its capacity to withstand pulling forces. This distinction is vital for engineers designing components that must endure specific types of mechanical stress.
Flexural strength plays a pivotal role in ensuring the longevity and durability of parts fabricated from thermoset composite materials. Components such as brackets, beams, and structural elements require high flexural strength to withstand bending and flexural loads without failure or deformation.
By focusing on these principles and applications, Atlas Fibre underscores its commitment to providing expertise and insight into the performance characteristics that define thermoset composite materials. For further exploration of this topic, consult our detailed guide on flexural strength in materials.