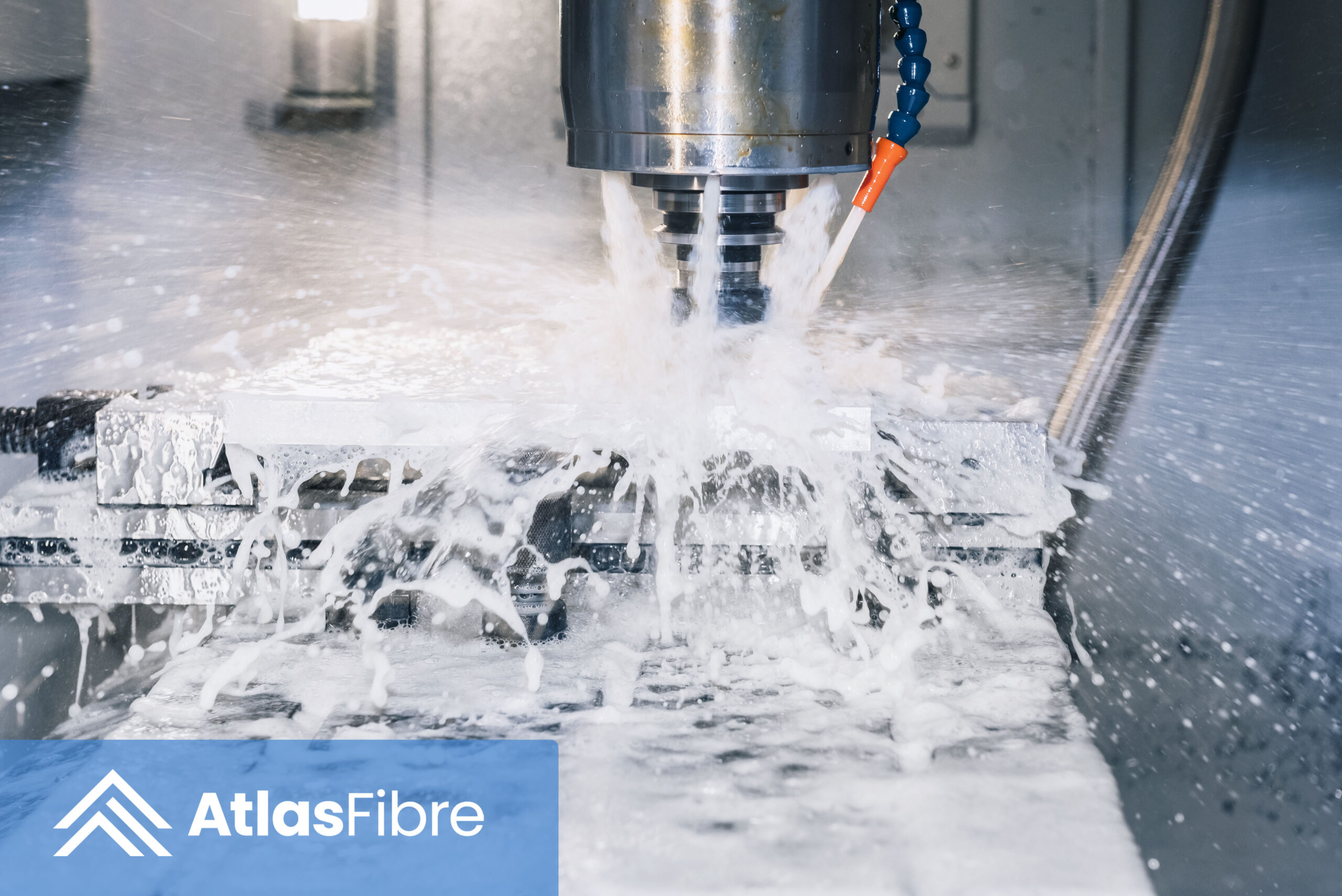
Spend long enough in a CNC machine shop, and you’ll hear the phrase “feeds and speeds” more than once. These terms refer to two critical parameters in CNC machining that significantly impact the cutting process, tool life, and overall machining quality.
Feeds vs Speeds
Speeds refer to the rotational speed of the cutting tool or workpiece, typically measured in revolutions per minute (RPM), also known as spindle speed.
Cutting speed can also be expressed as surface feet per minute (SFM), which represents the speed at which the tool’s cutting edge moves relative to the workpiece surface.
Feeds relate to the rate at which the cutting tool advances through the material being machined. Feed rate is usually measured in:
- Inches per minute (IPM) or millimeters per minute (mm/min): The linear speed of the tool’s movement.
- Inches per revolution (IPR) or millimeters per revolution (mm/rev): The distance the tool moves in one complete revolution of the spindle.
Key Points About Feeds and Speeds
Optimization
Finding the right balance between feeds and speeds is crucial for achieving optimal cutting performance, surface finish, and tool life. Machinists often start with recommendations from CNC machine manufacturers, which can serve as a valuable baseline. However, these recommendations are often conservative.
One effective method for optimizing feeds and speeds is to closely analyze tool wear patterns. These patterns indicate whether the speed or feed rate needs adjustment. For example:
At low speeds and feeds, you might see material adhesion.
High speeds can cause cratering, while low speeds might result in chipping and fracturing.
Material-Dependent Factors
Appropriate feeds and speeds vary depending on the material being machined, the cutting tool material, and other factors. These parameters must be adjusted based on the unique physical and mechanical properties of the material.
Hardness: Different materials have varying hardness levels, directly impacting cutting tool performance and wear rate.
Thermal Conductivity: Materials with low thermal conductivity retain more heat at the cutting edge, requiring slower speeds to avoid thermal damage.
Chip Formation: Brittle materials, which form short, discontinuous chips, can generally be machined at higher speeds. Ductile materials, forming long, continuous chips, may require slower speeds and higher feed rates for proper chip evacuation.
Machine Limitations
The capabilities of the CNC machine, including its rigidity and power, influence the selection of feeds and speeds.
Rigidity: More rigid machines can handle higher cutting forces without deflection or vibration, allowing for more aggressive feeds and speeds.
Vibration Damping: Machines with better vibration damping characteristics enable more aggressive cutting without inducing chatter or compromising surface finish.
Tool Holding System: More rigid and precise tool holding systems minimize tool runout and deflection, allowing for higher speeds and feeds.
By considering these machine capabilities, machinists can select optimal feeds and speeds that maximize productivity and part quality while staying within the machine’s performance envelope. This approach helps prevent issues like tool breakage, poor surface finish, or machine damage.
Cutting Tool Considerations
The type, size, and geometry of the cutting tool also play a role in determining suitable feeds and speeds.
Tool Material: Different tool materials (e.g., high-speed steel, carbide, ceramic) can withstand different cutting speeds and temperatures. For example, carbide tools can generally handle higher speeds than high-speed steel tools.
Tool Geometry: The shape and design of the cutting edges affect how efficiently the tool can remove material. Factors like rake angle, relief angle, and chip breakers influence optimal cutting parameters.
By considering these tool-specific factors, machinists can select feeds and speeds that maximize productivity and part quality while extending tool life, thereby optimizing the overall machining process and reducing costs associated with tool wear and replacement.
Understanding and correctly applying feeds and speeds is essential for CNC machinists to optimize their machining processes, improve part quality, and extend tool life. Connect with Atlas Fibre to learn more about our approach to feeds and speeds.