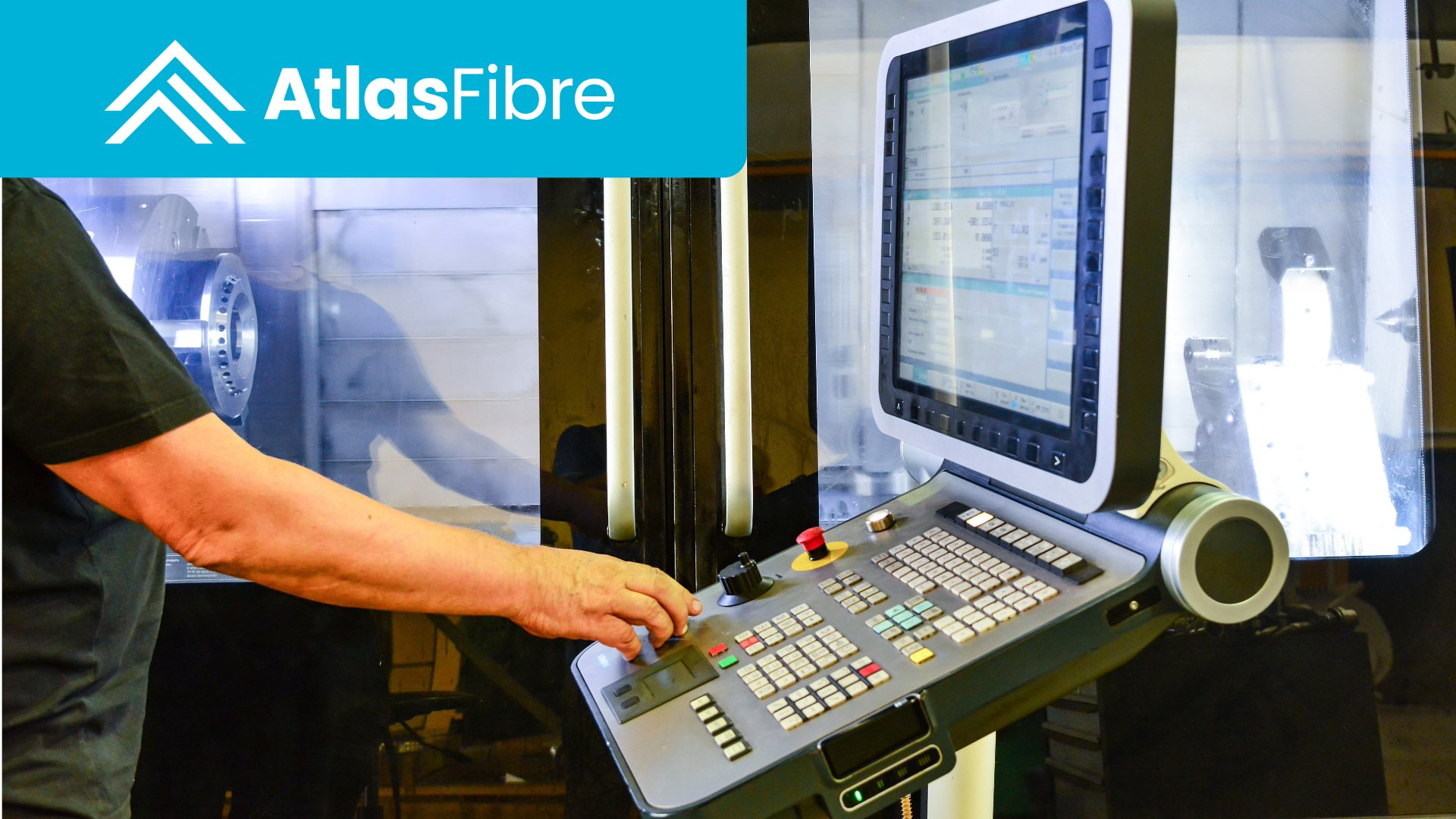
When it comes to machining, understanding the differences between 3-axis, 4-axis, and 5-axis machining can significantly impact your ability to produce precise, high-quality parts, especially with advanced materials like thermoset composites. Each type of machining offers unique capabilities and benefits that can cater to different complexities and requirements of your projects.
3-Axis Machining
3-axis machining is the most basic form of CNC machining. It utilizes three linear axes of motion: X, Y, and Z. This means the cutting tool can move in three directions, while the workpiece remains stationary.
Key Features:
- Movement: Linear motion in X, Y, and Z directions.
- Capabilities: Best suited for simpler parts with planar milled profiles, drilling operations, and threaded holes.
- Limitations: Limited in ability to machine complex geometries or deep cavities.
3-axis machining is ideal for thermoset composite parts that require straightforward milling and drilling. For instance, flat panels or components with simple cutouts can be effectively produced using 3-axis machines. The rigidity of thermoset composites allows for precise machining with minimal deflection, which is perfect for achieving accurate planar surfaces.
4-Axis Machining
4-axis machining adds a fourth rotational axis, typically the A-axis, which rotates around the X-axis. This additional axis allows the workpiece to rotate while the cutting tool moves in the X, Y, and Z directions.
Key Features:
- Movement: Linear motion in X, Y, Z plus rotational motion around the X-axis (A-axis).
- Capabilities: Can machine angled features and more complex geometries than 3-axis. Allows machining of four sides of a part in a single setup.
- Applications: Useful for parts with features on multiple sides or cylindrical shapes.
When working with thermoset composites, 4-axis machining can be highly beneficial for creating parts with features on multiple sides without repositioning. For example, it is particularly effective for producing components like brackets, housings, and other parts requiring precise angles and complex geometries. The enhanced capability of 4-axis machining reduces setup time and increases accuracy, which is crucial for maintaining the integrity and performance of thermoset composite materials.
5-Axis Machining
5-axis machining incorporates two rotational axes in addition to the three linear axes. This configuration typically uses either the A and C axes or B and C axes for rotation, allowing for simultaneous movement of all five axes or 3+2 positioning.
Key Features:
- Movement: Linear motion in X, Y, Z plus two additional rotational axes (A and C or B and C).
- Capabilities: Capable of producing highly complex 3D shapes and curved surfaces. Ideal for parts with intricate geometries or features at various angles.
- Applications: Commonly used in aerospace, medical, and other industries requiring complex parts.
For thermoset composites, 5-axis machining opens up possibilities for creating highly intricate and detailed components. This is essential for industries like aerospace and medical, where parts often have complex geometries and require precision. The ability to machine from multiple angles without repositioning the part ensures high accuracy and reduces the risk of errors. Components such as turbine blades, medical implants, and intricate housings can be efficiently produced using 5-axis machining, leveraging the superior properties of thermoset composites for high-performance applications.
Advantages and Considerations
Flexibility and Complexity: The increased axes in 4-axis and 5-axis machining allow for greater flexibility in part design and the ability to machine more complex geometries. This is particularly beneficial when working with thermoset composites, as these materials often require precise and intricate machining to achieve the desired performance characteristics.
Reduced Setup Time: With the additional rotational axes, 4-axis and 5-axis machines can reduce setup time by allowing multiple sides of a part to be machined in a single setup. This not only enhances efficiency but also improves accuracy by minimizing the need to reposition the workpiece.
Cost and Expertise: While 4-axis and 5-axis machines offer advanced capabilities, they are generally more expensive and may require more advanced programming skills. Investing in these machines can be justified by the increased precision, efficiency, and the ability to produce complex parts that are otherwise challenging with 3-axis machining.
Time to Machine to Components
Choosing the right type of machining for your thermoset composite parts depends on the complexity of the part, the required precision, and the production volume. While 3-axis machining is suitable for simpler parts, 4-axis and 5-axis machining provide enhanced capabilities for more complex and intricate components. Understanding these differences will help you make informed decisions, ensuring the highest quality and performance of your thermoset composite parts.