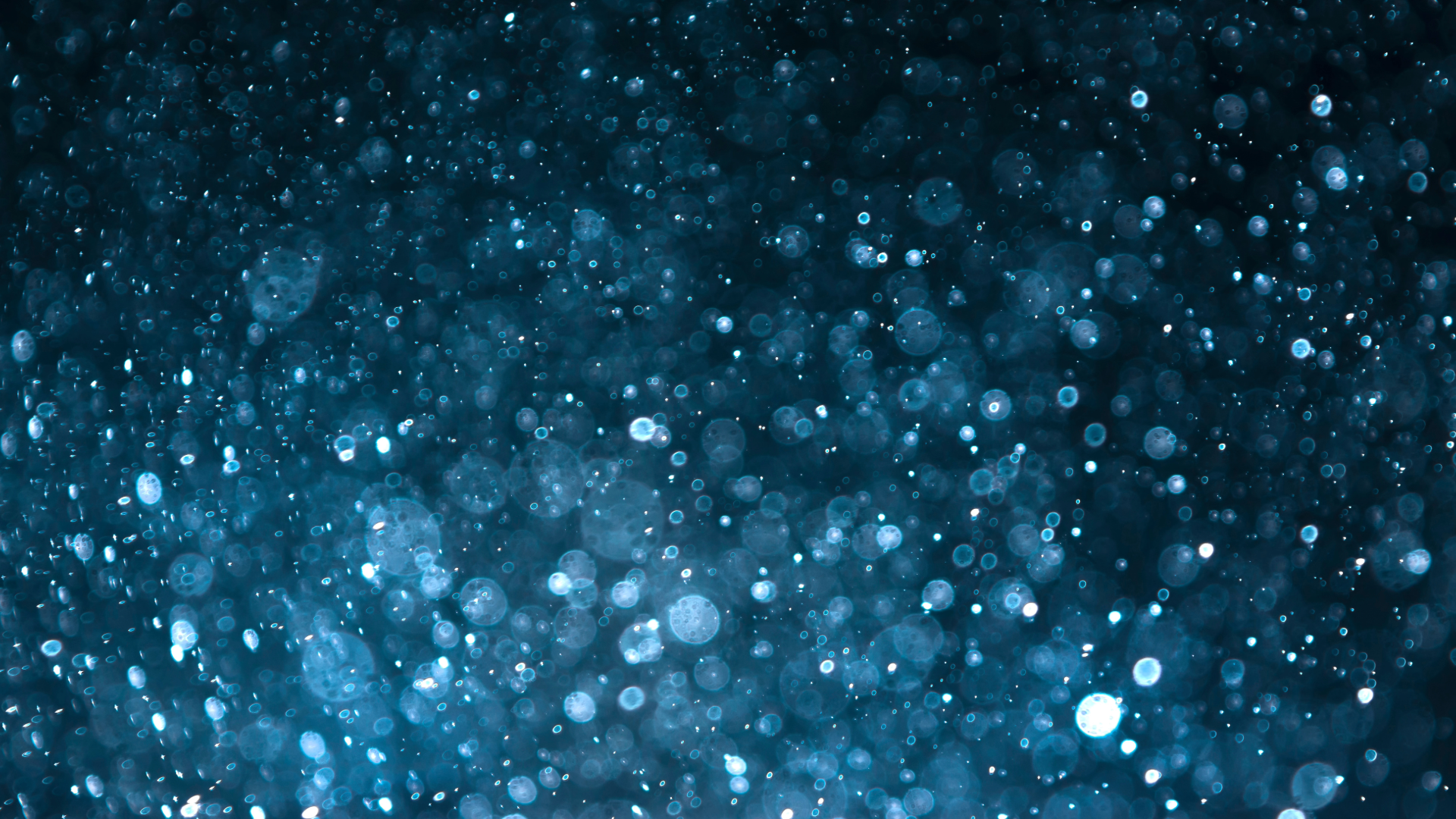
Atlas Fibre is proud to offer our “One Side Flat” service, which provides fabricators with precisely machined composite and plastic blanks that feature a perfectly flat surface.
This essential service ensures a stable foundation for all following machining processes, enhancing accuracy and minimizing errors in part dimensions. With Atlas Fibre’s commitment to quality and efficiency, this offering simplifies setup in CNC machines, allowing for quicker cycle times and improved production capabilities.
Trust Atlas Fibre to continue delivering the high-precision flat surfaces you need to achieve exceptional results in your manufacturing projects. Keep reading to discover why this service is so important to fabrication, machining and manufacturing today.
Defining “One-Side Flat”
The term “one side flat” refers to a machining process where one surface of a composite or plastic blank is precisely machined to create a flat, even surface. This flat surface is crucial because it serves as a reference point for subsequent machining operations. Here’s a breakdown of its significance:
- Starting Point for Machining: The flat surface provides a stable and accurate foundation for any further machining processes, such as milling, drilling, or cutting. This ensures that all other features are aligned correctly and produced to the desired specifications. Additionally, this service allows for the creation of a known flat surface for datums without requiring a fly cutting operation, streamlining setup and saving valuable time and resources in the machining process.
- Increased Accuracy: By machining one side flat, the risk of errors or inconsistencies in the part dimensions is minimized, leading to higher precision in the final product. Moreover, a flat surface provides an optimal vacuum seal, which is critical for ensuring secure part placement during machining processes that rely on vacuum fixtures, leading to easier part processing and better overall control during production.
- Preparation for Complex Shapes: For parts that require intricate geometries or additional machining, having a flat surface simplifies setup in CNC machines, improving efficiency and reducing cycle times.
- Quality Control: A flat surface can help in quality checks, as it can be used to measure and verify the straightness and flatness of the material before further machining.
- Versatility: This service is applicable to various materials, including different types of composites and plastics, making it valuable for diverse manufacturing applications.
Atlas Fibre is unwavering in its commitment to quality and efficiency. We are excited to offer our valued fabricators a “One Side Flat” service that ensures their starting material is always prepared to the highest standards, which is essential for achieving exceptional results in the machining process.