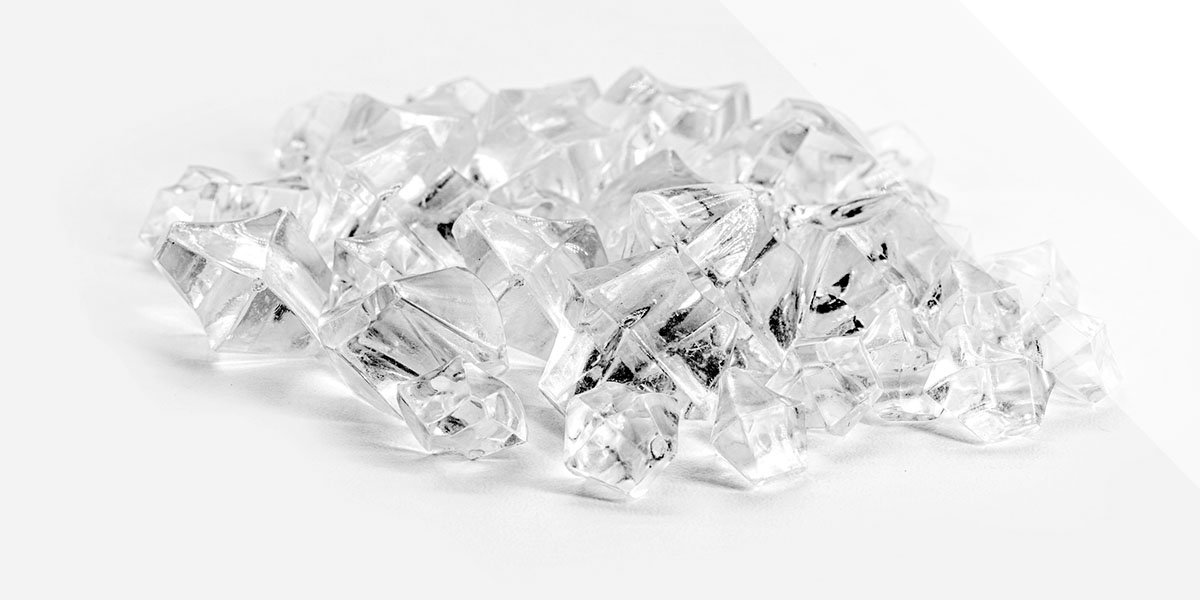
Chemical-resistant plastic sheets and other materials are essential for many industries. Unlike metals, most corrosive chemicals cannot permeate their surfaces and cause degradation. Materials like thermoset composites can complete many functions, regardless of the substances present in the working environment.
The global thermoset composites market is expected to reach $93.3 billion by 2030 as more users opt for chemical-resistant plastic for their applications. Although each has different properties, thermoset composites are resistant to most industrial solvents and corrosive chemicals across a broad range of temperatures and conditions, ideally positioned for industrial, food processing, medical, and automotive applications. Choosing the right chemical-resistant plastic is essential to maintaining product safety and quality.
Is Plastic Chemical Resistant?
A significant advantage of plastics is their chemical and corrosion resistance compared to metals. Each plastic’s chemical structure determines its chemical resistance.
Choosing the right polymer can create chemical resistance for even the harshest environments. Some of the primary factors that influence the chemical resistance of plastics beyond the basic polymer structure include:
- Length of exposure: Chemical reactions may not cause immediate visible damage but can appear over time.
- Temperature: High temperatures often accelerate chemical reactions.
- Surface area: The larger the exposed surface area, the higher the chances of degradation. Surface finish is also a factor.
- Chemical concentration: Harsh substances with high chemical concentrations are more likely to damage plastics.
Manufacturers must prioritize chemical-resistant properties as much as possible to meet demands for plastic components that come into contact with chemicals for prolonged periods. In short, some plastic is chemical resistant, and choosing the best composite for your application is critical.
Why Is Chemical Resistance Important?
Chemical resistance is essential for materials to perform their functions in harsh environments. Chemical-resistant materials can withstand exposure to various chemicals without surface treatment, maintaining their mechanical properties. Most composites have good resistance to highly active chemicals, and it’s rare for them to experience chemical damage at the same rate as metal alternatives.
Chemical damage could be catastrophic in many environments, including manufacturing, and chemical-resistant plastics are critical in various facilities. Chemical-resistant composites for the relevant application alleviate risks, promote product quality, and elevate workplace safety.
Top 5 Chemical-Resistant Plastic Composites
Contact with chemicals may seem rare at face value. However, many composites are exposed to prolonged or occasional contact with chemicals such as cleaning agents, alkalines, paint strippers, acids, fuels, and lubricants. They must withstand these chemicals to ensure operational safety and product quality. Their high thermal, mechanical, and chemical stability makes them ideal for structural and protective applications, such as aerospace materials.
Some of the most effective chemical-resistant plastic composites include:
1. Epoxy Resin
Glass epoxy material combines epoxy resin with a glass fiber matrix to create a composite material with outstanding electrical and thermal insulation. It’s an excellent choice for applications requiring dimensional stability, mechanical strength, and temperature resistance.
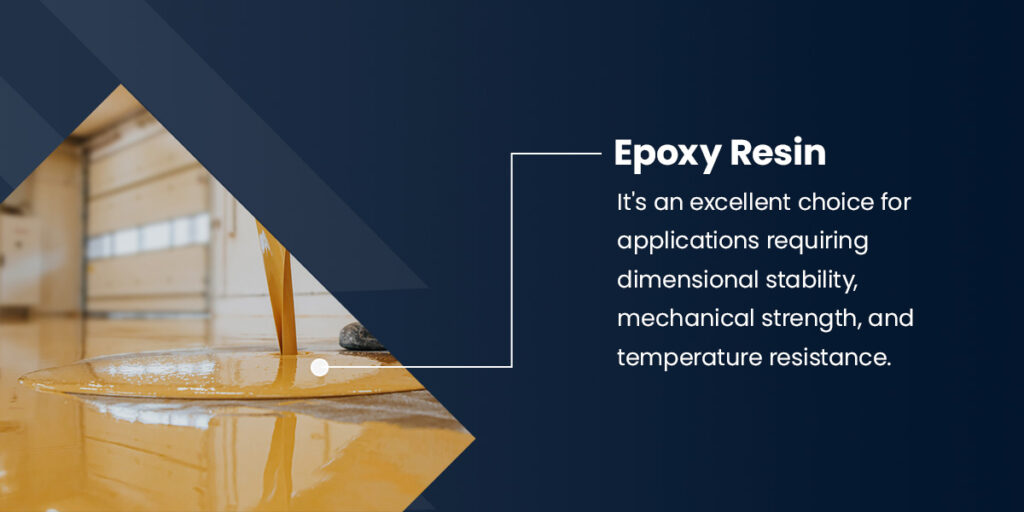
Different types of glass epoxy have various levels of chemical resistance, making certain types more suitable for environments with harsh chemicals. G-11 glass epoxy, for example, is made from a halogen-free epoxy resin and woven fiberglass substrate. Typical applications of glass epoxy include aerospace equipment, cryogenic insulation, medical diagnosing equipment, and rocket cases.
The properties of glass epoxy include:
- FR-4: This sheet boasts a flame-retardant epoxy resin, ideal for insulation in humid and dry conditions. It has excellent mechanical strength, low moisture absorption, chemical resistance, and fabricating properties.
- FR-5: This option is designed for higher operating temperatures than FR-4 and offers a range of material benefits, including high tensile strength, and superior chemical resistance.
- G-10: As the non-flame retardant version of FR-4, G-10 has excellent electrical insulation and high mechanical strength in wet and dry conditions. It can be relatively straightforward to fabricate and is versatile with high chemical resistance.
- G-11: This glass epoxy has higher insulation and temperature resistance properties than G-10. It’s notable for its chemical resistance and low moisture absorption.
2. Polyester Resin
Glass-reinforced polyester is a composite similar to phenolic composites. It’s made from fiberglass-reinforced polyester and available in rods, tubes, and sheets in various sizes and thicknesses. Three principal types of glass polyester exist, each providing multiple mechanical and insulative benefits.
- GPO-1: This range suits applications requiring good electrical properties and physical strength. It’s a general-purpose and cost-effective option.
- GPO-2: This option has excellent heat resistance and electrical and physical properties. It’s ideal for applications requiring flame and arc resistance.
- GPO-3: GPO-3 is the ideal choice for applications requiring chemical resistance. It’s highly flame-retardent and provides low smoke generation.
As GPO-3 is the most advanced material, it’s often the choice for high-voltage appliances, power distribution, and switchgear mounting panels.
3. Polyetherimide (PEI)
High-performance PEI materials like Ultem 1000 are ideal for various applications in some of the most challenging industries. Its superior electrical and dimensional characteristics under high temperatures make it suitable for aerospace, automotive, and medical applications.
Ultem 1000 is an amorphous material with high glass transition temperature and excellent mechanical properties, offering superior broad chemical resistance, ideal for medical devices and pharmaceutical applications.
4. Melamine Resin
Producing glass melamine involves coating woven glass fabric with melamine resin. Melamine is a common plastic manufacturing component known for its chemical resistance to alkali solutions. It has many applications across industries, including manufacturing, electronics, and insulation.
Two types of glass melamine exist — G-5, which is an older material with some flaws, and G-9, which is the general successor to the older G-5. G-9 offers heat, flame, arc, and alkali resistance. Using this material has many benefits, including dimensional stability and the ability to withstand humid and wet conditions.
5. Silicone Resin
The manufacturing process of this thermoset composite comprises coating glass fabric with a silicone resin. Its primary notable property is its heat resistance — up to 220 degrees Celsius (428 degrees Fahrenheit) — making it a popular choice in electronic, electrical, and mechanical applications. Silicone composites also resist various chemicals, including acids, alkalis, and organic solvents.
G-7 glass silicone sheet is constructed from high-performance silicone resin and a woven fiberglass substrate, producing superior heat and arc resistance. It’s also self-extinguishing, chemical resistant, and stable in humidity, making it ideal for applications such as arc barriers, heating systems, appliances, telecom equipment, and heating systems.
Find the Ideal Chemical-Resistant Plastic With Atlas Fibre
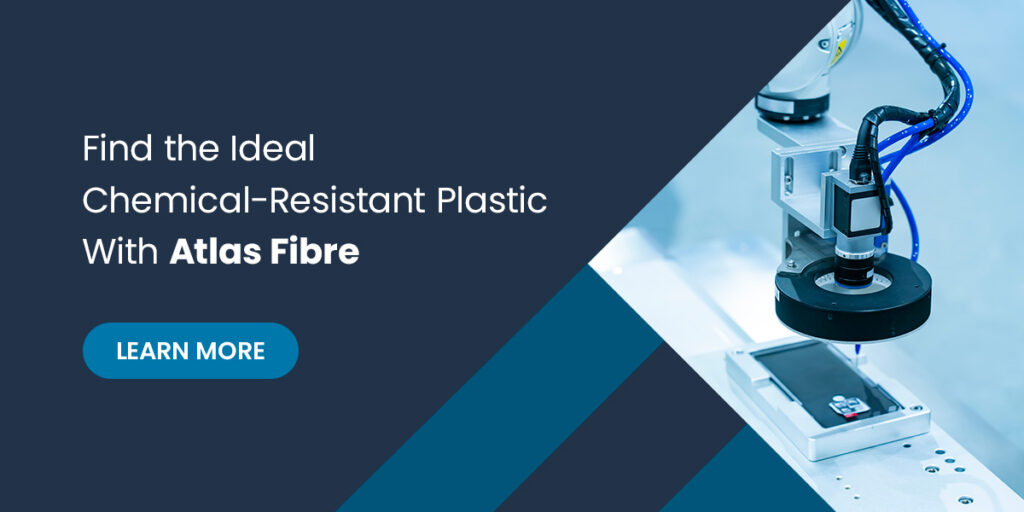
Chemical-resistant properties differ in plastics and composites depending on the formula, and selecting the best option for chemical exposure in your application is ideal for project safety and efficacy. Atlas Fibre offers North America’s most extensive range of thermoset materials. No matter your chemical resistance requirements, we can find a suitable option.
When you incorporate our materials into your application, you can achieve simple designs, lighter weight, service life longevity, and high reliability, even in harsh chemical conditions. Contact us today to learn more about our range of thermoset composites and related materials.