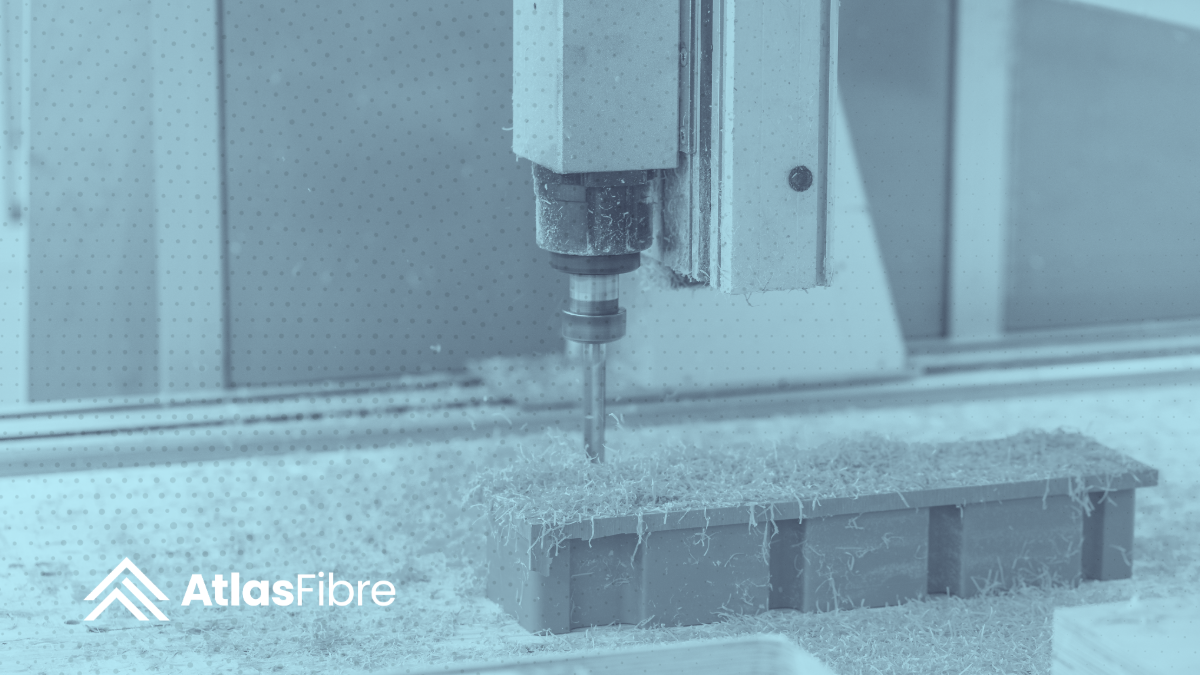
Machining nylon, known for its strength and chemical resistance, demands specific techniques. This article will guide you through the essential steps to prepare, machine, and finish nylon parts effectively for various industrial applications.
Key Takeaways
Nylon (polyamide) is a versatile thermoplastic with high strength, rigidity, and excellent chemical resistance, commonly used in various industries such as automotive and aerospace.
Proper preparation, including material selection and effective tool use, is critical for successful machining of nylon, with specific cutting parameters and cooling techniques necessary for optimal outcomes.
Machining nylon provides advantages such as wear resistance, cost-effectiveness, and lightweight properties, making it suitable for applications including gears, bushings, and consumer goods.
Understanding Nylon (Polyamide) Properties
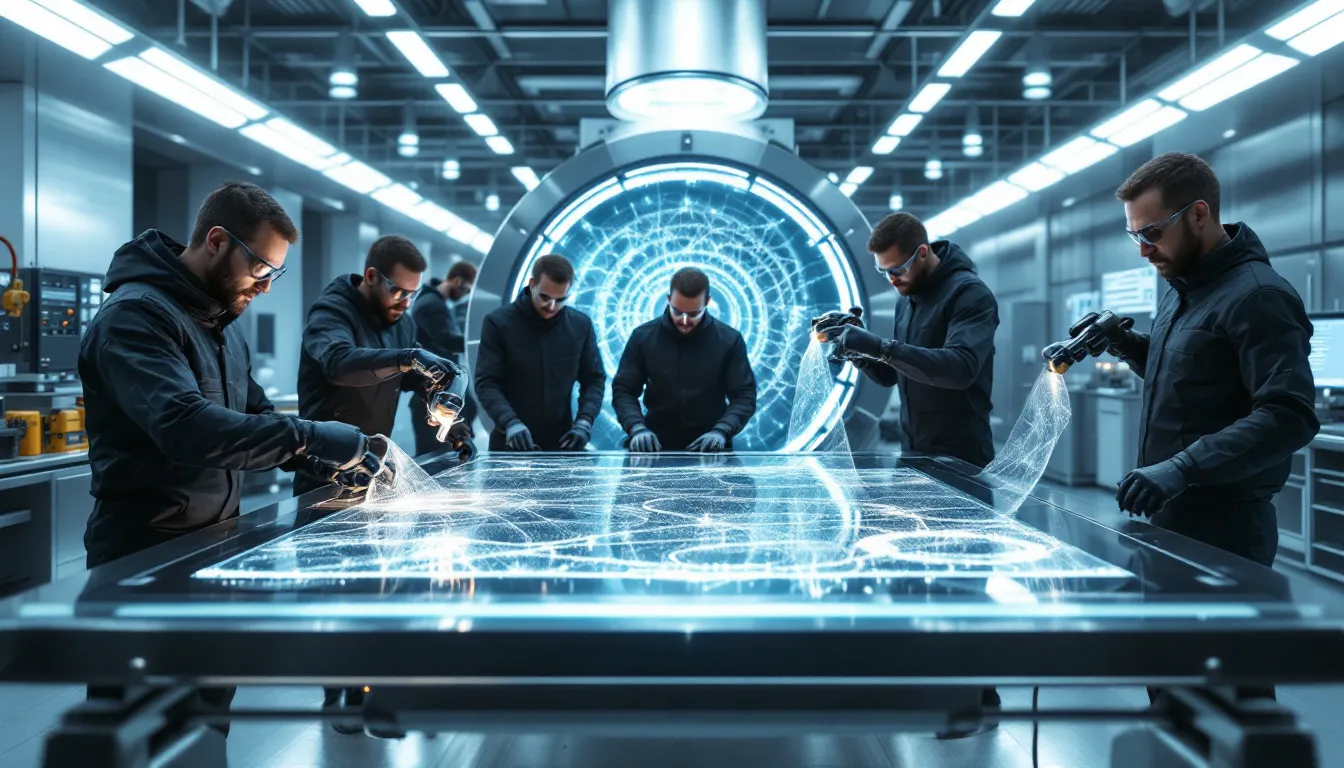
Nylon, often referred to by its chemical family name polyamide, is a semi-crystalline thermoplastic known for its high strength, rigidity, toughness, and excellent chemical resistance. These properties make nylon a preferred material in various demanding applications, from industrial machinery to everyday consumer products.
Understanding the types of nylon, their mechanical properties, and chemical resistance is crucial before considering machining techniques.
Types of Nylon
Nylon comes in several grades, with nylon 6 and nylon 66 being the most commonly used. Each type has unique properties that make it suitable for different applications. Nylon 66, for example, is more crystalline than nylon 6, offering higher strength, thermal stability, and corrosion resistance. This makes it ideal for thin-walled components and parts subjected to high wear, such as wear pads and bearings. On the other hand, nylon 6 is often used in applications requiring good mechanical properties but not necessarily the highest strength, such as tire cords and industrial cords.
The choice between nylon 6 and nylon 66 significantly impacts performance and durability across industries. The automotive industry, for example, uses nylon for components like sprockets and fuel tanks, while the aerospace sector employs it for electrical connectors and landing gear, benefiting from its balance of strength and weight.
Mechanical Properties
Nylon’s mechanical properties significantly influence its machinability and application. It retains strength and rigidity even in humid environments, making it reliable for engineering uses. Its high degree of crystallinity contributes to toughness and rigidity. Additionally, nylon withstands mechanical stress and maintains a low coefficient of friction, which is advantageous in dynamic applications like gears and bearings.
Moreover, nylon’s toughness and abrasion resistance ensure it can endure significant wear and tear, making it suitable for high-wear applications. The material’s inherent properties also allow it to adapt to complex geometries, which is crucial when machining intricate parts with tight tolerances.
Chemical Resistance
Nylon stands out for its excellent chemical resistance, withstanding various solvents, oils, and chemicals. This makes it ideal for harsh environments, as its chemical structure allows it to endure corrosive conditions, prolonging part lifespan and reducing maintenance costs.
Applications that benefit from nylon’s chemical resistance are abundant. In the automotive and aerospace industries, components exposed to oils, fuels, and other chemicals perform reliably over extended periods. Industrial applications also utilize nylon for parts that must resist chemical exposure, such as in chemical processing equipment and machinery.
Preparing for Machining Nylon
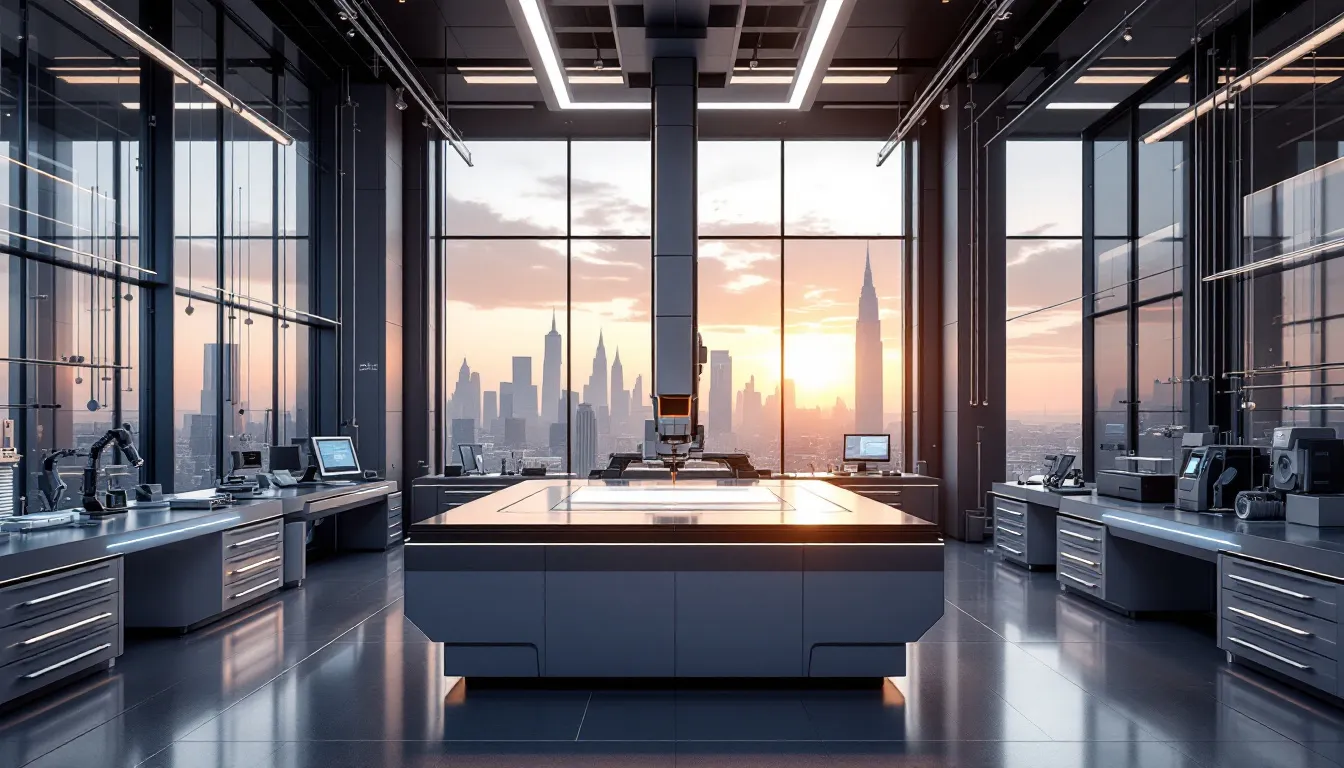
Proper preparation is crucial before machining nylon. Understanding its material properties involves selecting the right type and preparing tools to ensure precision and quality in the final product.
Material Selection
Choosing the right type of nylon is the first step. Nylon 6 and nylon 66 are the most common for machining. Nylon 6 offers good mechanical properties, while nylon 66 provides enhanced toughness and heat resistance, suitable for high-strength applications like automotive components.
Selecting the type based on specific application requirements is crucial for optimal performance.
Tool Preparation
Effective tool preparation is critical. Tools made from high-speed steel (HSS) or carbide are recommended for their durability and precision. Tungsten carbide alloy tooling is preferred for maintaining sharp edges and withstanding the stresses of machining nylon. Sharp hss tool geometry is also crucial, with a recommended angle range of 10 to 15 degrees for machining nylon PA66.
Keeping the nylon part cool during machining prevents deformation and ensures a smooth finish. Supporting the part well and using appropriate coolants helps manage heat and maintain workpiece integrity.
Machining Process for Nylon
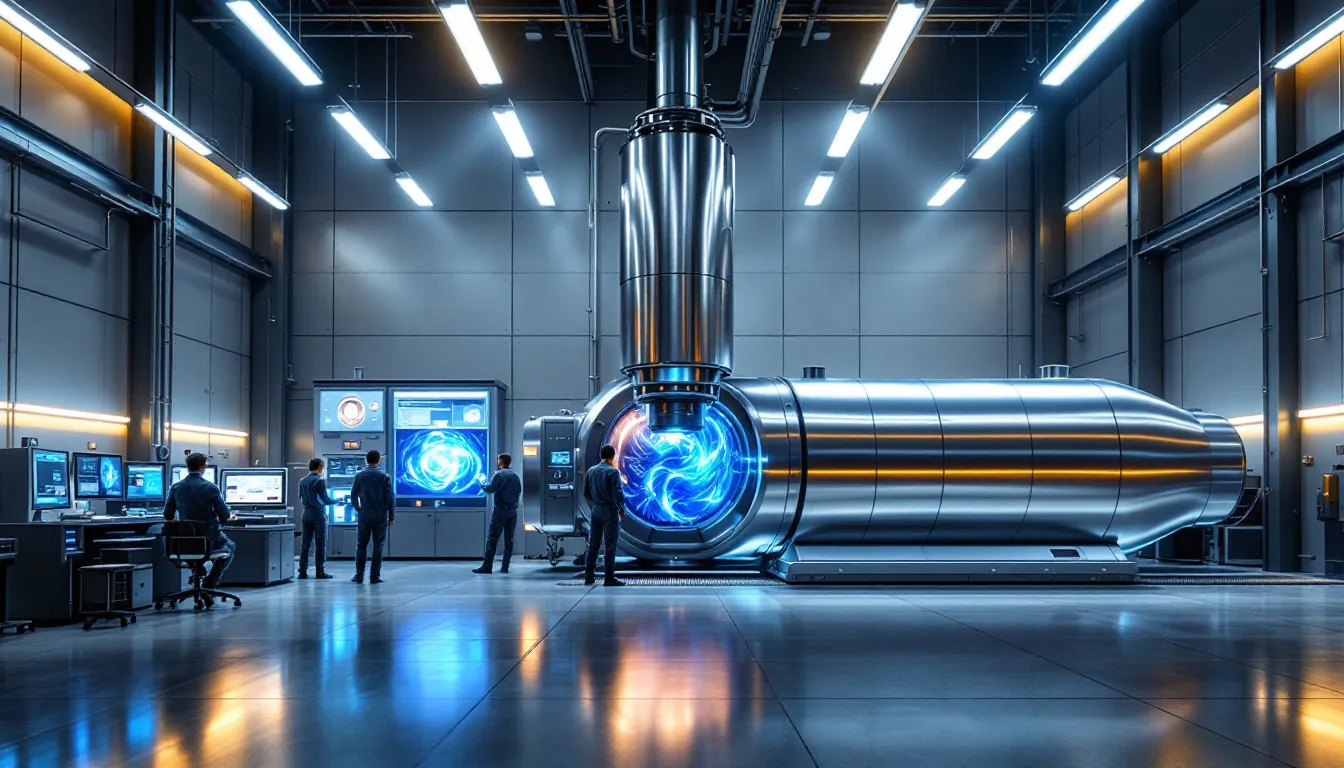
The actual cnc machining process involves understanding cutting parameters, fixturing techniques, and coolant usage. Properly executing these steps ensures the quality and precision of the machined nylon parts.
Cutting Parameters
Proper cutting parameters are vital for efficient machining. Recommended cutting speeds range from 200 to 300 feet per minute, with feed rates between 0.002 to 0.008 inches per tooth. The depth of cut should range from 0.020 to 0.050 inches, balancing material removal and surface finish.
Fixturing Techniques
Fixturing techniques are essential for securely holding the workpiece. Providing maximum support and stability prevents movement and ensures precision. Clamping and vacuum chucking are recommended methods to keep nylon workpieces stable for accurate and consistent machining.
Different nylon variants, such as glass-filled or oil-filled types, may require specific fixturing methods due to their varying machinability characteristics. Considering these factors helps achieve the best machining results.
Coolant Usage
Effective coolant usage is vital to managing heat during machining. Water-soluble coolants prevent deformation of the nylon workpiece. Maintaining a sharp cutting edge and using non-aromatic, air-based coolants help achieve a better surface finish and extend tool lifespan.
Post-Machining Operations
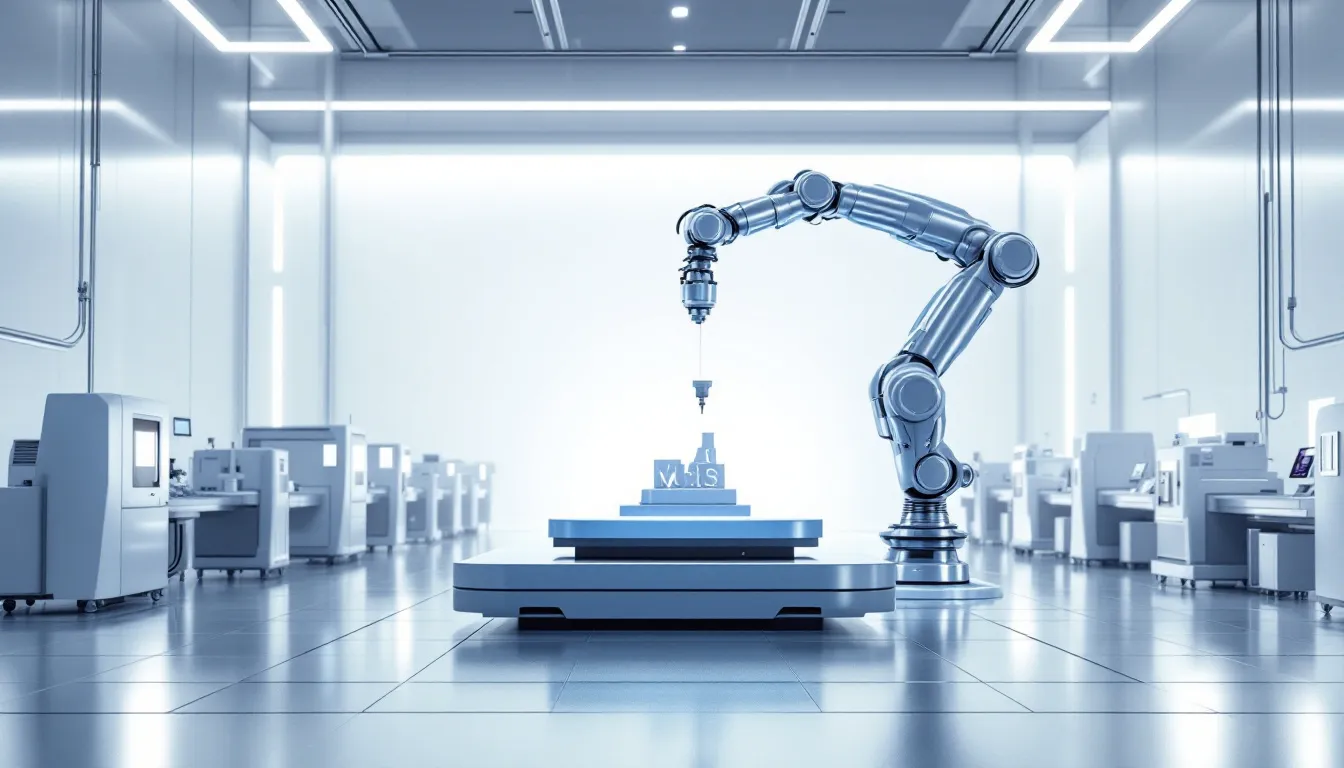
Post-machining operations ensure the final desired surface quality and functionality of nylon parts. These operations, including deburring, sanding, and polishing, enhance the appearance and performance of machined components.
Deburring
Deburring removes sharp edges and ensures the safety and functionality of nylon parts. Specialized tools designed for plastics, such as files or deburring tools, effectively smooth out rough edges, improving appearance and preventing potential injuries and performance issues.
Sanding and Polishing
Achieving a polished finish on nylon components involves a combination of sanding and polishing techniques. Using progressively finer sandpaper grits improves surface smoothness. Additionally, a buffing wheel with appropriate polishing compounds provides a glossy finish, enhancing aesthetic appeal and functionality.
Vibratory polishing eliminates tooling marks and achieves a high-quality surface finish.
Advantages of Machining Nylon
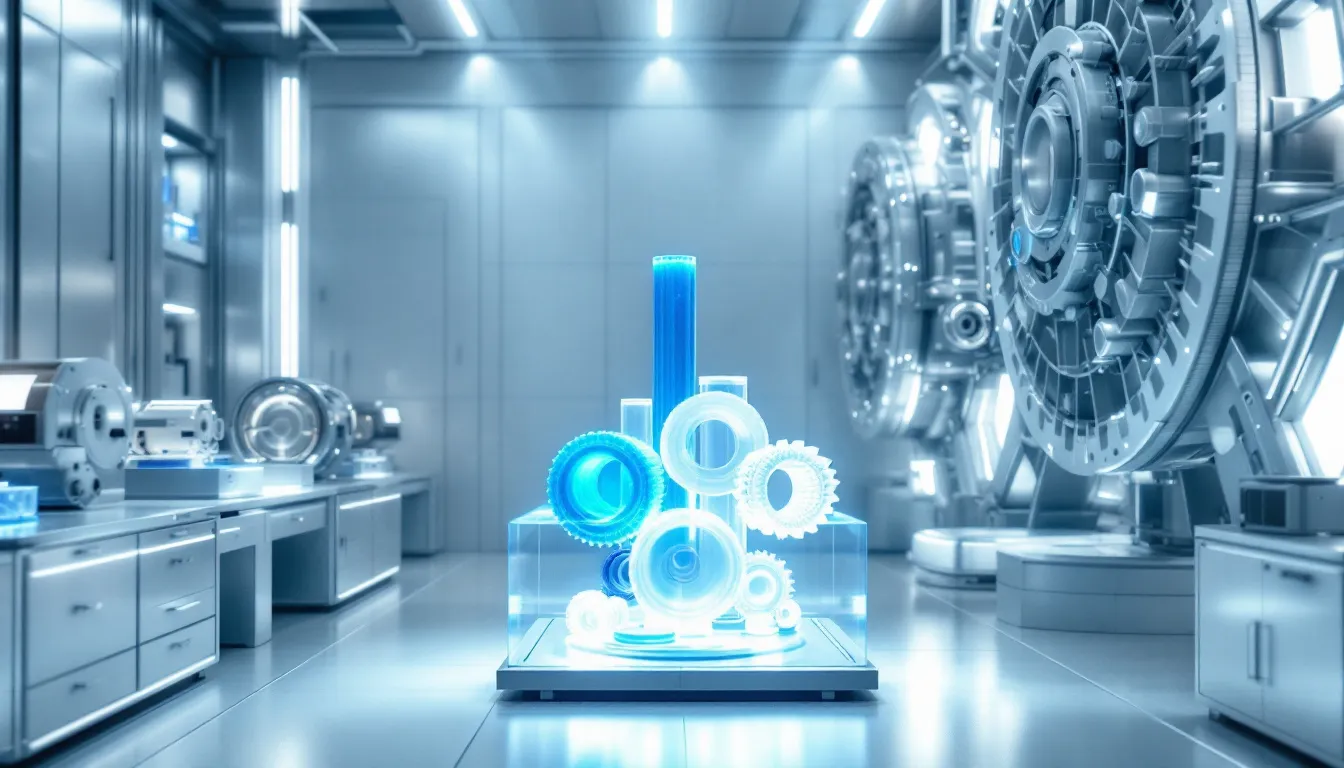
Machining nylon offers numerous advantages, making it a preferred material for many applications. Its excellent abrasion resistance, versatility, and high durability contribute to the longevity of machined components.
Nylon parts are lighter than traditional metals, enhancing performance and efficiency in various applications.
Wear Resistance
Nylon’s wear resistance is a significant advantage. Nylon 66, in particular, demonstrates superior wear resistance compared to many other materials, making it ideal for bearings, gears, and bushings. This minimizes wear on mating surfaces, prolonging the lifespan of moving parts and reducing maintenance needs.
Cost-Effectiveness
Using nylon instead of metals like aluminum can lead to significant cost savings. Nylon reduces manufacturing costs due to lower machining time and raw material costs. Additionally, cast nylon parts offer substantial savings in fabrication compared to metal components, making it a cost-effective choice for many applications.
Applications of Machined Nylon
Machined nylon is widely used across various industries due to its versatility and reliability. Typical applications include gears, bushings, cable binders, and hinges, showcasing its suitability for both mechanical and functional components.
Automotive Industry
In the automotive industry, nylon’s resistance to oil and greases makes it valuable for components like gears, bearings, and fuel tanks. Its durability and lightweight properties significantly enhance the efficiency and performance of automotive designs.
Aerospace Industry
The aerospace sector relies on nylon for parts requiring high strength and lightweight attributes. It is used to manufacture components like engine parts, landing gear, and electrical connectors, enhancing performance and reliability.
Consumer Goods
Nylon’s versatility extends to consumer goods, producing durable items like kitchen tools and sports gear. Everyday items such as kitchen utensils and sporting equipment benefit from nylon’s durability and functional properties.
Summary
Understanding and mastering the machining of nylon offers many benefits, from its excellent mechanical and chemical properties to its cost-effectiveness and versatility in various applications. By selecting the right type of nylon, preparing tools properly, and following effective machining processes, one can achieve high-quality, durable parts. Whether in the automotive, aerospace, or consumer goods sectors, machined nylon proves to be a reliable and efficient material choice.
Frequently Asked Questions
What are the main types of nylon used in machining?
The main types of nylon used in machining are nylon 6 and nylon 66, with nylon 66 offering superior strength and thermal stability, while nylon 6 delivers good mechanical properties for diverse applications.
What are the recommended cutting parameters for machining nylon?
For machining nylon, it is advisable to use cutting speeds of 200 to 300 feet per minute, with feed rates between 0.002 to 0.008 inches per tooth and a depth of cut ranging from 0.020 to 0.050 inches. These parameters will help achieve optimal results.
How important is coolant usage during the machining of nylon?
Coolant usage is crucial when machining nylon, as it effectively manages heat and prevents deformation. Employing water-soluble coolants can enhance surface finishes and prolong tool life.
Why is nylon considered cost-effective compared to metals?
Nylon is considered cost-effective compared to metals primarily due to lower manufacturing costs, including reduced machining time and raw material expenses. This can lead to significant savings, especially when using cast nylon parts instead of metal components.
What are the post-machining operations required for nylon parts?
Post-machining operations for nylon parts include deburring, sanding, and polishing, which improve both the surface quality and the aesthetic appeal of the final product. Implementing these steps is essential to achieve the desired functionality and precision.