Have you ever wondered what makes G-10 material such a popular choice for a wide range of applications? From electrical components to knife handles, G-10 offers a remarkable combination of strength, durability, and excellent electrical properties. In this comprehensive guide, we’ll explore the composition, characteristics, and applications of G-10 material, as well as its customization options and environmental factors affecting its performance.
Key Takeaways
- G-10 material is a strong and versatile composite composed of an epoxy resin binder and glass epoxy, offering impressive chemical resistance, excellent electrical properties, high strength, and rigidity.
- The material is compliant with MIL-I-24768/2 military specification for insulation plastic laminated thermosetting materials. It’s widely used in various applications due to its superior traits.
- FR-4 offers additional fire safety alongside other features such as high strength and good electrical insulation. Carbon fiber alternatives provide increased strength and weight benefits compared to G-10 and FR-4.
Exploring G10 Plastic Material: Composition and Characteristics
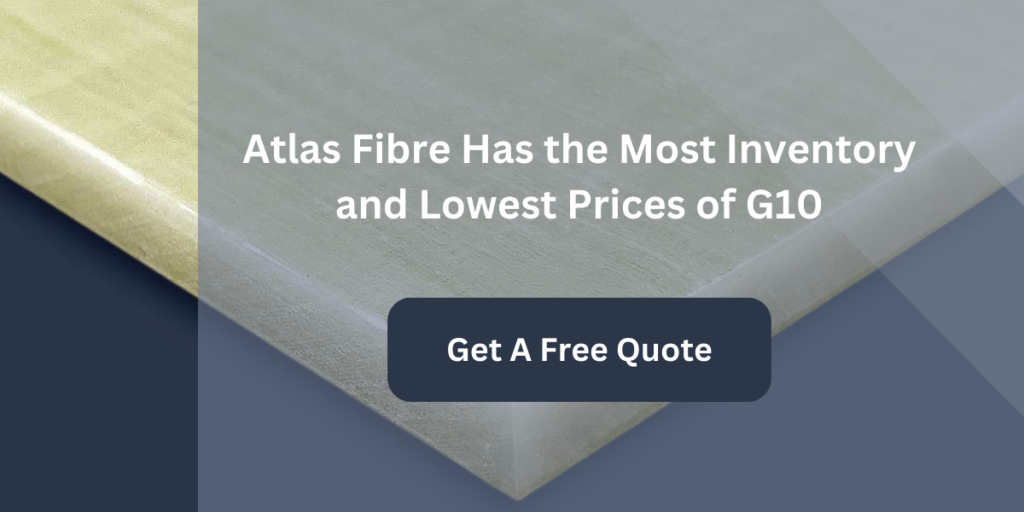
G10 material stands out as a versatile and widely used composite material, known for its impressive chemical resistance, excellent electrical properties, and high strength.
What Is G-10 Material?
G-10 is an industrial thermoset laminated plastic composed of an epoxy resin binder and a glass epoxy composite, making it a popular choice for various electrical applications, from circuit boards to high-voltage insulators. It’s readily available in sheet and rod form or as fabrication-ready precision blanks.
Its compositions and traits distinguish G-10 as a robust, high-performance plastic offering many benefits. Epoxy resin binder and glass epoxy composite play key roles in the properties and performance of G-10 material, which is a type of glass epoxy laminate. The combination of these components results in a material that is not only strong and durable but also offers exceptional electrical insulation and chemical resistance. These attributes make G-10 an ideal choice for a wide range of applications, from industrial laminates to cryogenic equipment.
Epoxy Resin Binder
The epoxy resin binder in G-10 material is responsible for its strength and durability. This robust and resilient material is known for its resistance to chemicals, heat, and UV light, making it an ideal component for various applications.
Its high strength, outstanding electrical properties, and resistance to chemicals make it well-suited for use in humid or moist conditions, where it can offer excellent performance without degradation.
Glass Epoxy Composite
The glass epoxy composite in G10 material is another crucial component, contributing to its electrical insulation and mechanical properties. This composite consists of woven glass fibers and epoxy resin, creating a strong and rigid structure that serves as an effective insulator. G10 material with a higher ratio of glass to epoxy tends to demonstrate higher mechanical strength, improved dielectric properties, and better resistance to chemicals, making it a versatile choice for a variety of applications.
MIL-I-24768/2
G-10 material meets the MIL-I-24768/2 standard, which is a specification for insulation, plastic, laminated, thermosetting materials. This standard outlines requirements for sheets, tubes, and rods that meet military specifications.
G-10’s compliance with the MIL-I-24768/2 standard, particularly in terms of the Type GEE requirements, guarantees that it conforms to particular criteria for mechanical strength, dielectric properties, and corrosion resistance, making it suitable for various industrial applications.
G-10 Material Applications
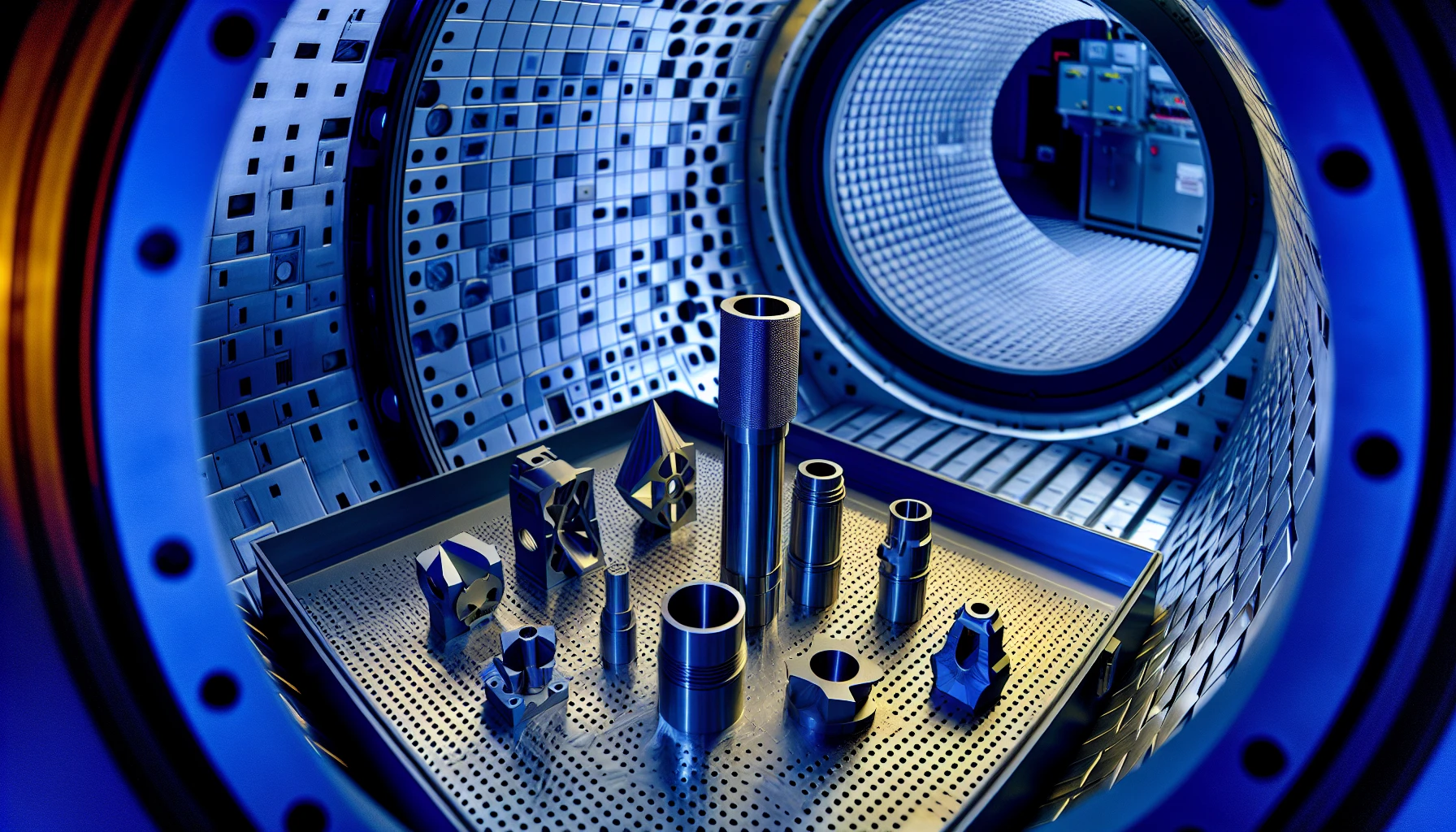
The exceptional qualities of G-10 material make it suitable for numerous applications, which include:
- Use in electrical components
- Knife handles
- Firearms manufacturing
- Cryogenic applications
- Electrical insulation
- Marine applications
These diverse applications showcase the versatility and adaptability of G10 material, enabling it to cater to a wide range of requirements and specifications.
Considering electrical applications, G10 is well-suited for numerous components, including:
- Terminal boards
- High humidity applications
- Electrical and electronic test equipment
- Electric rotor insulation
- Circuit boards
Its robustness, superior electrical traits, and chemical resistance make it an ideal choice. Additionally, its high modulus of elasticity and tensile strength provide durability and the ability to withstand mechanical stress. With its excellent electrical insulation properties, G10 is a favored material for electrical components.
Electrical Applications
The superior electrical properties of G10 material allow it to be utilized in a range of electrical applications, such as:
- Terminal boards
- High-voltage switchgear
- Transformers
- Printed circuit boards
Its non-conductive and insulation typical properties, as well as its resistance to wear and corrosion, make it suitable for use under high voltage.
However, it is worth noting that G10 material can be relatively expensive, so this factor should be considered when selecting materials for electrical applications.
Knife Handles
G10 material is a preferred choice for knife handles due to its durability, longevity, and aesthetic appeal. It is highly resistant to moisture and temperature changes, making it a reliable option. Moreover, G10’s texture can be modified to offer a firm grip, boosting safety and reducing accident risks, even under wet or slippery conditions.
G-10 handles are highly durable and suitable for outdoor and tactical knives, and they do not warp, rot, or absorb water over time.
Firearms Manufacturing
Firearms manufacturers nationwide are increasing G-10 use in their designs. The material is lightweight, strong, and durable, making it perfect for crafting essential components like stock and trigger sets and mainspring housing.
The material is also ideal for creating distinctive stock handles and grips because of its multilayer construction. G-10 material is easy to cut and shape, so manufacturers can produce visually appealing designs and variegated appearances for an extra boost of style. G-10 is simple to add texture to as well, resulting in improved grip.
Cryogenic Applications
G10 material presents a number of advantages in cryogenic applications. It has outstanding electrical properties, chemical resistance, and high strength, thus providing versatility. G10 is capable of withstanding subzero temperatures without physical degradation, rendering it suitable for cryogenic settings.
Additionally, it is a cost-effective insulation material and can be utilized as thermal insulating material in structural supports. In summary, G10 is a durable and dependable material for cryogenic applications.
Electrical Insulation
G10’s electrical insulation properties make it a popular choice for electrical insulation components. Its uses include:
- Terminal boards
- Busbar insulation
- Electronic test equipment
- Electric motor rotor insulation
Its low dielectric loss performance and high mechanical strength render it a reliable insulating and durable material even in humid environments.
Its excellent dielectric properties and resistance to wear and corrosion further contribute to its suitability for electrical insulation applications.
Marine Applications
Because G-10 does not contain metal, it can’t rust and can withstand harsh marine environments. Its lighter weight also helps promote better fuel economy. These properties make it a viable choice for seagoing vessel components like fixtures and jigs. Additionally, G-10 is perfect for use in the engine room since it’s resistant to moisture and oil and offers excellent electrical insulation.
Machining and Fabrication of G-10 Material
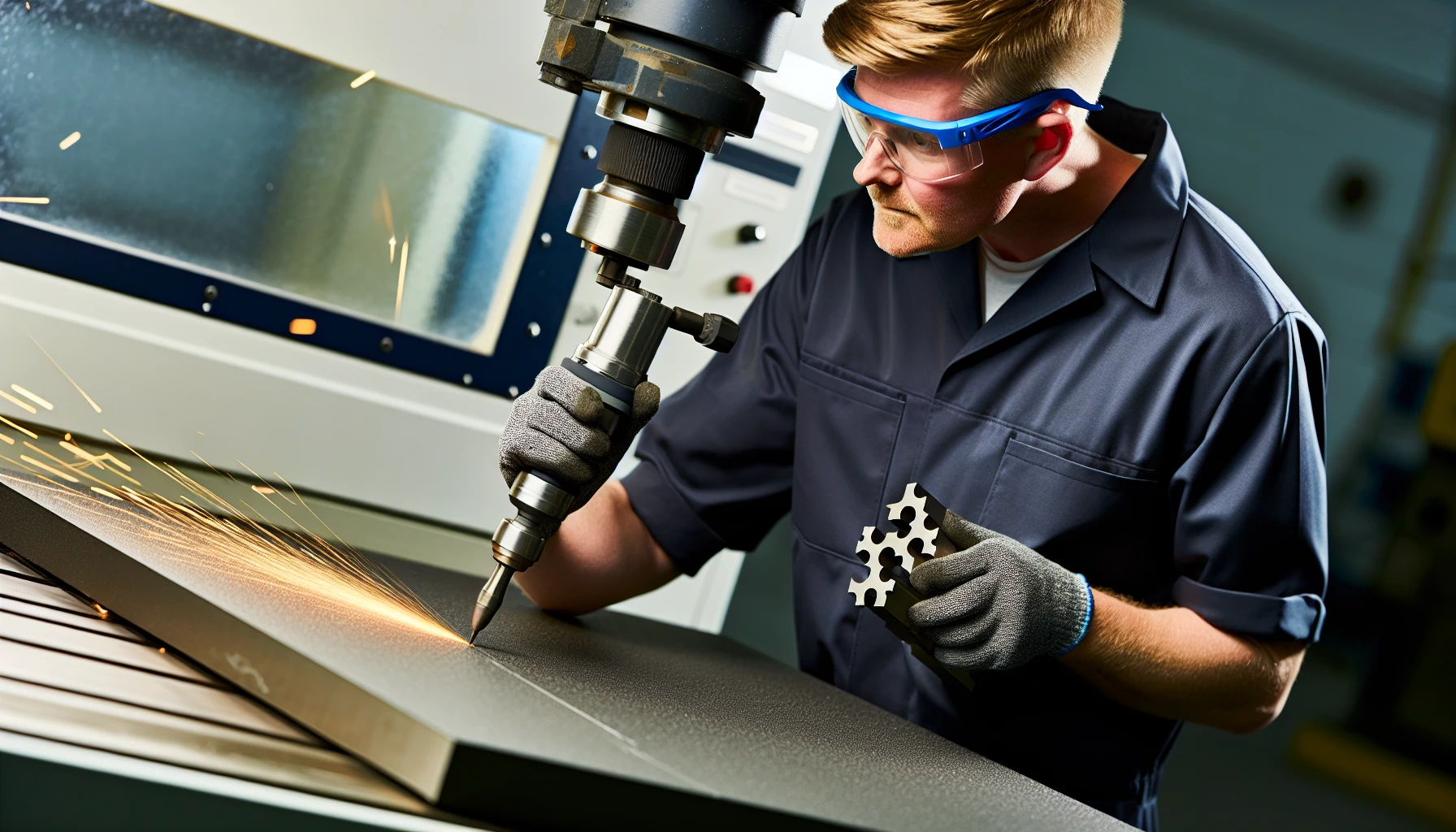
Machining and fabrication of G10 material require specific cutting tools and maintaining tool sharpness for optimal results. The abrasive nature of G10 material can cause cutting tools to wear down more quickly, and its composition may release substances that can chemically react with the cutting tools, exacerbating the wear and tear.
We will focus on the suggested cutting tools and optimal practices for preserving tool sharpness during the machining of G10 material.
Cutting Tools
For machining G10 material, the following recommendations should be followed:
- Use carbide or diamond tools, as well as sharp, hard-grade tools, to minimize delamination.
- Choose coated tools when possible.
- Use appropriate speeds and feeds.
- Use reduced rake and increased clearances on the cutting tools to maintain sharpness.
- Inspect cutting tools regularly to promote high-quality results — G-10 material has a lower shearing strength and can be abrasive to cutting tools.
Maintaining Tool Sharpness
Keeping tools sharp is essential for efficient machining of G10 material. A sharp tool ensures:
- Cleaner and more accurate cuts
- Minimizing the risk of delamination
- Enhancing the overall surface finish
- Producing less heat during the cutting process, avoiding the melting of the resin in the G10 material and avoiding potential issues.
To ensure optimal cutting tool sharpness when machining G10 material, it is recommended to:
- Use carbide or diamond tools
- Use appropriate speeds and feeds
- Consider using coolant
- Inspect tools regularly and promptly replace worn ones.
G-10 vs FR-4: Understanding the Differences
G10 and FR-4 materials share many similarities, but there are some key differences between the two. The primary difference is that FR-4 is a flame-retardant version of G10 material, making it more suitable for applications where fire resistance is a concern. We will outline the differences between G10 and FR-4 materials, along with the advantages of carbon fiber alternatives.
FR-4 material is a flame-retardant variant of G10 material, offering additional safety in applications where fire resistance is crucial. The manufacturing process for FR-4 involves the use of a fire-retardant epoxy resin blended with fiberglass fabric, resulting in a material with the following characteristics:
- Flame-retardant
- High strength
- Good electrical insulation properties
- Excellent dimensional stability
- Low water absorption
Carbon fiber alternatives, on the other hand, offer additional strength and lightweight properties compared to G10 and FR-4, making them suitable for a wider range of applications.
Flame Retardant Properties
FR-4 material’s flame retardant properties set it apart from standard G-10 material. This variation is achieved by incorporating a fire-retardant epoxy resin in the manufacturing process, which is blended with fiberglass fabric to generate the G-10 material with flame-retardant characteristics.
FR-4 material demonstrates resistance to flames, heat, and smoke, making it an ideal choice for applications where fire safety is a priority.
Carbon Fiber Alternatives
Carbon fiber alternatives offer several advantages over G-10 and FR-4 materials, such as:
- Higher strength-to-weight ratio
- Reduced weight
- Approximately five times stronger than steel
- Twice as rigid
- Significantly lighter
This makes carbon fiber alternatives an ideal choice for applications where strength and weight are important factors, and such information is crucial for decision-making.
However, carbon fiber is typically more costly than G10 and FR-4 due to its superior strength-to-weight ratio and the intricate manufacturing process.
Customization Options for G10 Material
G10 material can be customized to meet specific application requirements in terms of size and surface resistivity. This versatility allows G10 material to cater to a wide range of needs and specifications, ensuring optimal performance in various applications.
We will discuss the customization possibilities for G-10 material, which encompasses size variations and adjustments to surface resistivity.
Size Variations
G-10 material is available in various sizes to suit customer needs. Standard dimensions of G-10 sheets available in the market are 1020x1220mm (40×48 inches), 1020x2040mm (40×80 inches), and 1220x2440mm (48×96 inches). However, custom sizes can also be manufactured and cut to meet customer specifications.
Milling and cutting with tools such as a band saw or hacksaw are typically utilized to adjust the size of G10 material, ensuring the perfect fit for any application.
Surface Resistivity
Surface resistivity is a measure of a material’s ability to resist the flow of electric current across its surface. G10’s surface resistivity is important for electronic applications, as it provides effective electrical insulation, thus preventing the flow of current and minimizing the risk of short circuits or electrical damage.
The surface resistivity of G-10 material can be adjusted or customized by altering the composition of the material during the manufacturing process, ensuring optimal performance in a variety of applications.
Environmental Factors Affecting G10 Material Performance
Environmental factors such as moisture and temperature can affect the performance of G10 material. Understanding how these factors impact G10 material can help ensure optimal performance in various applications. We will cover:
- The impact of moisture on G10 material performance
- The appropriateness of G10 material for high heat applications
- The appropriateness of G10 material for cryogenic applications.
G10 material’s performance may be affected in moist conditions due to its ability to absorb a certain degree of water, liquids, and moisture. Although G10 is nearly waterproof, it can still take in some moisture due to the weave that forms the material. Nevertheless, G10 is resistant to water absorption and does not corrode when exposed to moisture, making it an ideal choice for applications in moist conditions.
Moist Conditions
Extended exposure to moisture does not have a significant effect on the physical properties of G-10 material. G-10 boasts:
- Excellent resistance to water absorption.
- High deterioration resistance when exposed to moisture.
- Consistent strength retention and durability in wet conditions.
Furthermore, G-10’s excellent electrical insulation properties make it a reliable insulating material even in humid environments.
Heat and Cryogenic Applications
G10 material can withstand high heat and cryogenic applications, making it suitable for a wide range of uses. Some characteristics of G10 material include:
- Withstanding high temperatures
- Resisting cryogenic conditions
- Maintaining mechanical properties
- Exhibiting minimal thermal expansion
- Experiencing minimal mass loss
However, at elevated temperatures, G-10 material may experience curing of the epoxy resin, thermal expansion, mass loss, and a decrease in mechanical properties. We recommend other thermoset composites, such as G-11 and G-7 materials, as a better solution for operating environments exceeding 140 degrees Celsius.
On the other hand, G-10 material is often employed in cryogenic applications due to its low thermal diffusivity at low temperatures, indicating its suitability for such extreme cold conditions. G-10 CR, a version of G-10 specifically designed for cryogenic applications, has been developed to further enhance its performance in low-temperature environments.
Summary
In summary, G10 material is a versatile and high-performing composite material with numerous advantages in a variety of applications. Its exceptional electrical properties, chemical resistance, and high strength make it an ideal choice for electrical applications, knife handles, cryogenic applications, and electrical insulation. With customization options for size and surface resistivity, G10 material can cater to a wide range of needs and specifications. Understanding the composition, characteristics, and environmental factors affecting G10 material performance is crucial for ensuring its optimal performance in various applications.
Request a Quote on G-10 From Atlas Fibre
Atlas Fibre is a North American leader in thermoset composite laminates and carries the industry’s most extensive in-stock material inventory. We’re also vertically integrated, which uniquely qualifies us to assist at every stage, from laminate manufacture to finished assembly. All materials come from our ISO 9001:2015-certified facility for exceptional quality assurance. Contact us for a quote.
Frequently Asked Questions
What is G-10 material equivalent to?
G-10 is a thermosetting industrial laminate composed of a woven glass cloth material and an epoxy resin matrix, often compared to Micarta and carbon fiber laminates. It has excellent electrical properties, chemical resistance, low coefficient of thermal expansion, and is widely used as an insulator for electrical and electronic applications.
What are the hazards of G-10 materials?
G-10 materials emit irritating fumes when burned or decomposed, and the dust generated by secondary operations is explosive. Eye and skin exposure to these fumes and dust should be avoided.
Is G-10 the same as fiberglass?
G-10 is a fiberglass laminate made up of woven fiberglass and an epoxy resin binder, similar to the way that fiberglass is created by stacking multiple layers of glass cloth soaked in epoxy resin. Thus, G-10 can be said to be the same as fiberglass.
What is the strength of G-10 material?
G-10 is a thermosetting composite material consisting of glass cloth and epoxy resin, known for its high tensile strength of 65,000 psi, compressive strength of 40,000 psi and flexural strength of 75,000 psi.
What are the main applications of G10 material?
G10 material is widely used in electrical applications, knife handles, cryogenic environments and for insulation purposes.