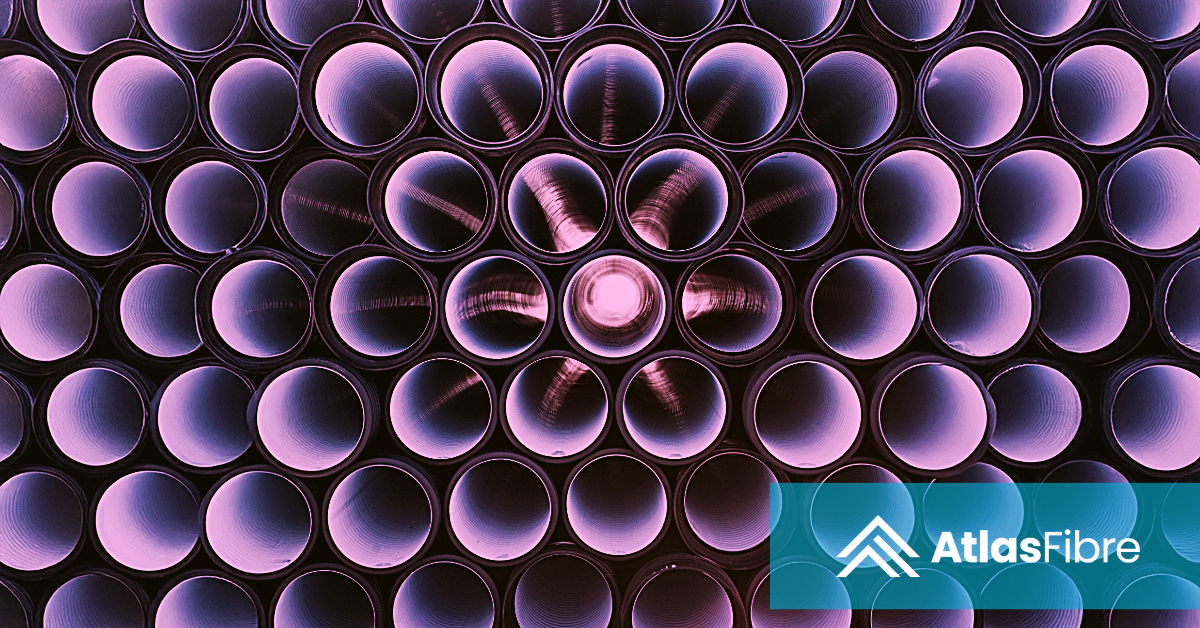
Which Thermosets are Preferred for Machinability and Performance?
In the world of high-performance materials, thermoset composite laminates are essential in industries ranging from aerospace to electrical insulation. But when it comes to choosing between glass epoxies (such as G10-FR4 and G11) and phenolics, which material comes out on top for machinability and performance in critical applications? While both have their strengths, glass epoxies are the preferred choice for applications requiring durability, precision, and resilience under demanding conditions.
Machinability: The Ultimate Test of Precision
Precision machining is key in manufacturing components for aerospace, electrical, and industrial applications. When comparing machinability, glass epoxies have the upper hand due to their structural integrity and stability during processing.
Glass Epoxy Composites (G10-FR4, G11)
- Offer exceptional dimensional stability over a wide temperature range, allowing for tight tolerances.
- Can be precisely machined with carbide or diamond-coated tools without excessive tool wear.
- Maintain high strength post-machining, reducing the risk of cracking or chipping.
- Demonstrate superior creep resistance, ensuring long-term stability under load.
Phenolics
- While easier to cut, they are more brittle, making them susceptible to chipping.
- NEMA LE (Linen Phenolic) is commonly used when better machinability is required, but standard phenolics can be challenging to process.
- Machining phenolics generates more dust and debris, which can require additional handling and filtration measures.
- For manufacturers requiring high-precision fabrication, glass epoxies outperform phenolics by offering superior structural integrity and machinability without sacrificing mechanical performance.
Performance in Critical Applications: Strength Meets Stability
When it comes to performance, the real question is: what are the conditions the material needs to withstand? Let’s break it down by key attributes:
Mechanical Strength
- Glass Epoxies have a higher tensile strength (67 MPa) compared to phenolics (48 MPa), making them better suited for applications requiring durability and impact resistance.
- These advanced materials also exhibit superior creep resistance, allowing them to maintain structural integrity under sustained loads.
Thermal Resistance
- Phenolics edge out epoxies with a higher glass transition temperature (170°C vs. 120°C), making them more heat-resistant in certain conditions.
- However, glass epoxies have superior thermal shock resistance, scoring 20 points compared to phenolics’ 7.5 points, allowing them to withstand rapid temperature fluctuations better.
Moisture and Chemical Resistance
- Glass epoxies absorb less moisture and remain stable even in high-humidity environments.
- G10-FR4 and G11 offer superior chemical resistance, making them ideal for harsh industrial and electrical settings.
- Phenolics, while still resistant, can degrade over time when exposed to certain chemicals and moisture.
Electrical Insulation
- G11 glass epoxy is a top-tier electrical insulator, widely used in power generation and transmission equipment.
- Glass epoxies outperform phenolics in insulation properties, ensuring low moisture absorption and stable dielectric properties even at high temperatures.
- Phenolics provide good arc and flame resistance, making them a viable alternative in environments where fire safety is a primary concern.
Specific Advantages of Glass Epoxies
Glass epoxies offer a range of advantages that make them the preferred choice for demanding applications.
Their higher tensile strength and elongation at break provide superior durability and flexibility compared to phenolics. G11 glass epoxy stands out as a leading electrical insulator, outperforming phenolics in power applications where stable dielectric properties and low moisture absorption are critical. Additionally, glass epoxies demonstrate exceptional thermal shock resistance, scoring significantly higher than phenolics in withstanding rapid temperature swings.
Beyond these core benefits, glass epoxy composites can be tailored with fillers and additives to improve flame retardance, moisture resistance, and overall durability, making them one of the most versatile thermoset materials available.
Which Composite Laminate Should You Choose?
If machinability, strength, and stability in critical applications are your top priorities, glass epoxies like G10-FR4 and G11 are the clear winners. They deliver unmatched performance in high-strength, high-precision applications while maintaining excellent electrical and chemical resistance.
However, if affordability, flame resistance, and moderate performance are sufficient for your needs, phenolics can still be a viable option.
For those pushing the boundaries of innovation, from next-gen aerospace components to cutting-edge electrical insulation, glass epoxies are the material of choice. Their resilience, reliability, and machinability make them an essential component in high-performance manufacturing.
Looking to learn more about machining high-performance composites? Connect with our technical project specialists for a deep dive into the machinability and performance of various thermoset composite laminates!