Are you trying to optimize your injection molding costs without sacrificing quality and wondering, “how expensive is injection molding?” In this blog post, we’ll dive into the factors that impact injection molding costs and share practical tips on how to reduce expenses while maintaining high-quality parts. We’ll also compare injection molding to alternative manufacturing processes and discuss the importance of selecting the right partner to maximize your project’s success.
Key Takeaways
- Injection molding costs can be managed effectively by understanding the various factors such as material selection, mold design complexity, production volume and labor/overhead expenses.
- Strategies for minimizing injection molding costs include simplifying part design, optimizing material usage and leveraging economies of scale.
- Selecting the right injection molding partner requires careful evaluation of factors such as location, experience & expertise and certifications to ensure optimal cost & product quality.
Breaking Down Injection Molding Costs
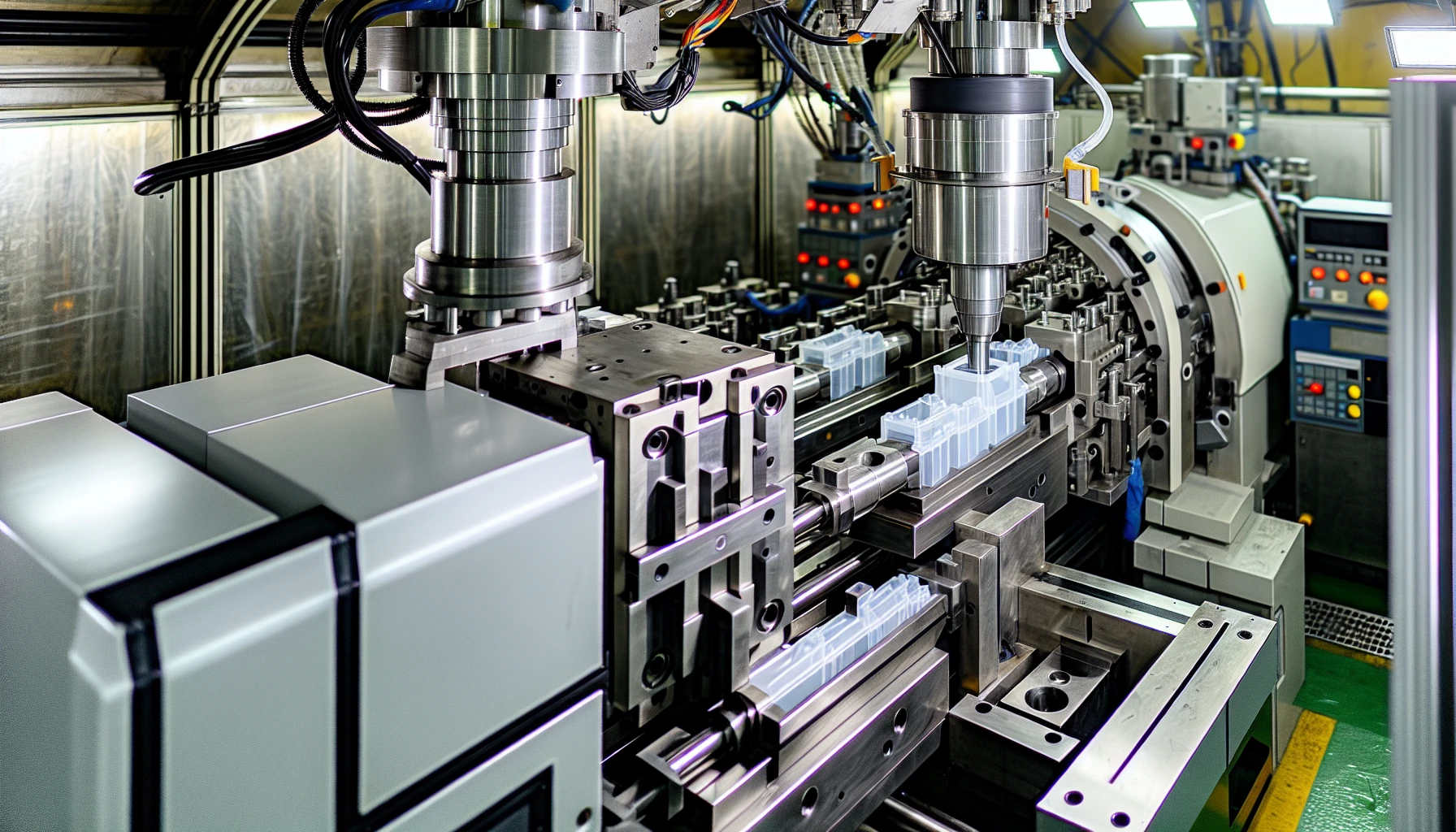
Injection molding is a popular manufacturing process for producing plastic components, but how expensive is it really? The cost of injection molding depends on several factors, including:
- Material selection
- Mold design complexity
- Production volume
- Labor and overhead expenses
By understanding these factors, you can make informed decisions about your injection molding project and optimize costs without compromising quality.
Next, we’ll examine each cost factor in detail and share some insights on how to manage them effectively to control your injection molding expenses.
Material Selection
One of the critical factors affecting injection molding costs is the choice of material. The cost of materials varies depending on their type and quantity. Engineering-grade plastics, for example, are more expensive due to their advanced manufacturing processes and specialized additives required to achieve desired performance characteristics.
Choosing a material for your injection molding project requires a careful balance between cost-effectiveness and the physical properties needed for the final product. This involves considering factors like the form of the resin, cost, and potential volume discounts.
The most commonly used materials in plastic injection molding, especially for cheap injection molding, include nylon, acrylic, polycarbonate, ABS plastic, and polyoxymethylene.
Mold Design Complexity
Another significant factor in injection molding costs is the complexity of the injection mold design. Complex mold designs typically require more intricate molds and longer machining times, resulting in increased injection mold cost. Features such as undercuts can add to the complexity and cost, as they create indentations or recesses that prevent the part from being easily ejected from the mold.
Costs can be trimmed by simplifying the mold design, such as using aluminum molds. This could imply refining the shape of the injection-molded part, reducing the number of features and details, and utilizing thinner walls in the mold.
Performing a mold flow analysis and optimizing the part design for simplicity and efficiency can also contribute to cost reduction.
Production Volume
Production volume is directly proportional to the cost per part in injection molding. Generally, higher production volumes result in lower costs per part. This is due to the economies of scale, where the initial tooling and setup costs can be distributed over a larger number of parts, reducing the cost per piece.
Taking advantage of these economies of scale could mean increasing the number of parts in your production run. This can help offset the initial costs and lead to significant cost savings compared to other manufacturing methods.
Labor and Overhead Expenses
Labor and overhead expenses are costs that can impact the overall cost of injection molding. These expenses include:
- Workforce costs
- Facility rent
- Utilities
- Equipment maintenance
- Administrative costs
The skill level and experience of the workforce can also play a significant role in labor costs. Highly skilled and experienced workers are typically more efficient and productive, resulting in lower labor costs.
Optimizing labor and overhead costs requires partnering with a seasoned manufacturer who can proficiently operate the machinery, resolve any issues, and streamline the production process. This will ensure that your injection molding project runs smoothly, efficiently, and cost-effectively.
Tips for Reducing Injection Molding Costs
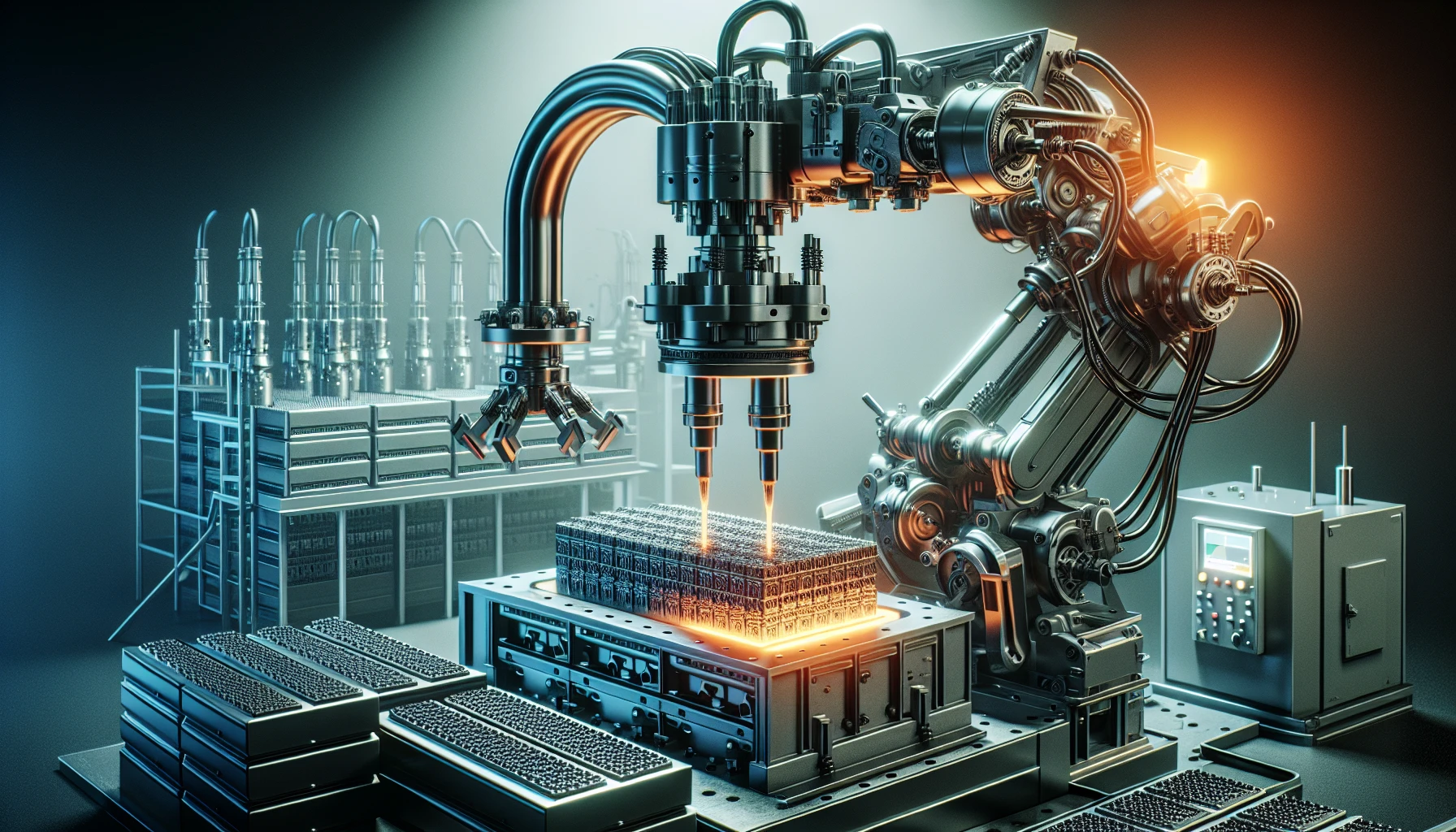
Now that we’ve discussed the main factors that influence injection molding costs let’s explore some practical tips for reducing expenses without sacrificing quality. The key strategies for minimizing injection molding costs include simplifying part design, optimizing material usage, and leveraging economies of scale.
Implementing these cost-saving strategies will allow you to maximize your injection molding project and produce high-quality parts at a more affordable price. We’ll now delve deeper into each of these strategies.
Simplify Part Design
The simplification of part design plays a key role in cutting down injection molding costs. As mentioned earlier, complex geometries and undercuts can increase the complexity and cost of the mold design. To minimize costs, consider streamlining the shape of the injection-molded part and reducing the number of features and details.
In some cases, it may be more cost-effective to produce separate parts and assemble them manually later, especially for overmolding applications. By simplifying the part design, you can decrease tooling costs and make your injection molding project more affordable without sacrificing the quality of the final product.
Optimize Material Usage
Optimizing material usage is another key factor in lowering injection molding costs. Here are some tips to help you achieve cost savings:
- Select cost-effective materials such as Polypropylene (PP), High-Density Polyethylene (HDPE), Acrylonitrile Butadiene Styrene (ABS), Polystyrene (PS), and Polyethylene Terephthalate (PET).
- Minimize waste by accurately calculating the required material quantities and avoiding overproduction.
- Consider using recycled or regrind materials, if suitable for your product.
- Optimize part design to reduce material usage without compromising functionality or strength.
- Work closely with your material supplier to explore options for cost-effective alternatives.
By implementing these strategies, you can effectively optimize material usage and achieve significant cost savings in injection molding.
In addition to choosing the right materials, employing various techniques can help optimize material usage during the injection molding process. These techniques include:
- Examining tool functionality
- Conducting short shot testing
- Performing gate seal studies
- Evaluating sample parts and recording data
- Implementing quality control
- Adjusting injection speed, melt temperature, injection pressure, cooling time, and packing pressure.
Leverage Economies of Scale
Taking advantage of economies of scale also serves as an effective cost reduction strategy in injection molding. As previously mentioned, higher production volumes can lead to lower per-piece costs due to the initial tooling and setup costs being distributed over a larger number of parts.
By increasing the production volume of your injection molding project, you can take advantage of economies of scale and achieve significant cost savings. This can make injection molding a more cost-effective option for your manufacturing needs, especially when compared to other manufacturing processes like 3D printing and CNC machining. Utilizing an injection molding machine can further enhance the efficiency of your production process.
Comparing Injection Molding to Alternative Manufacturing Processes
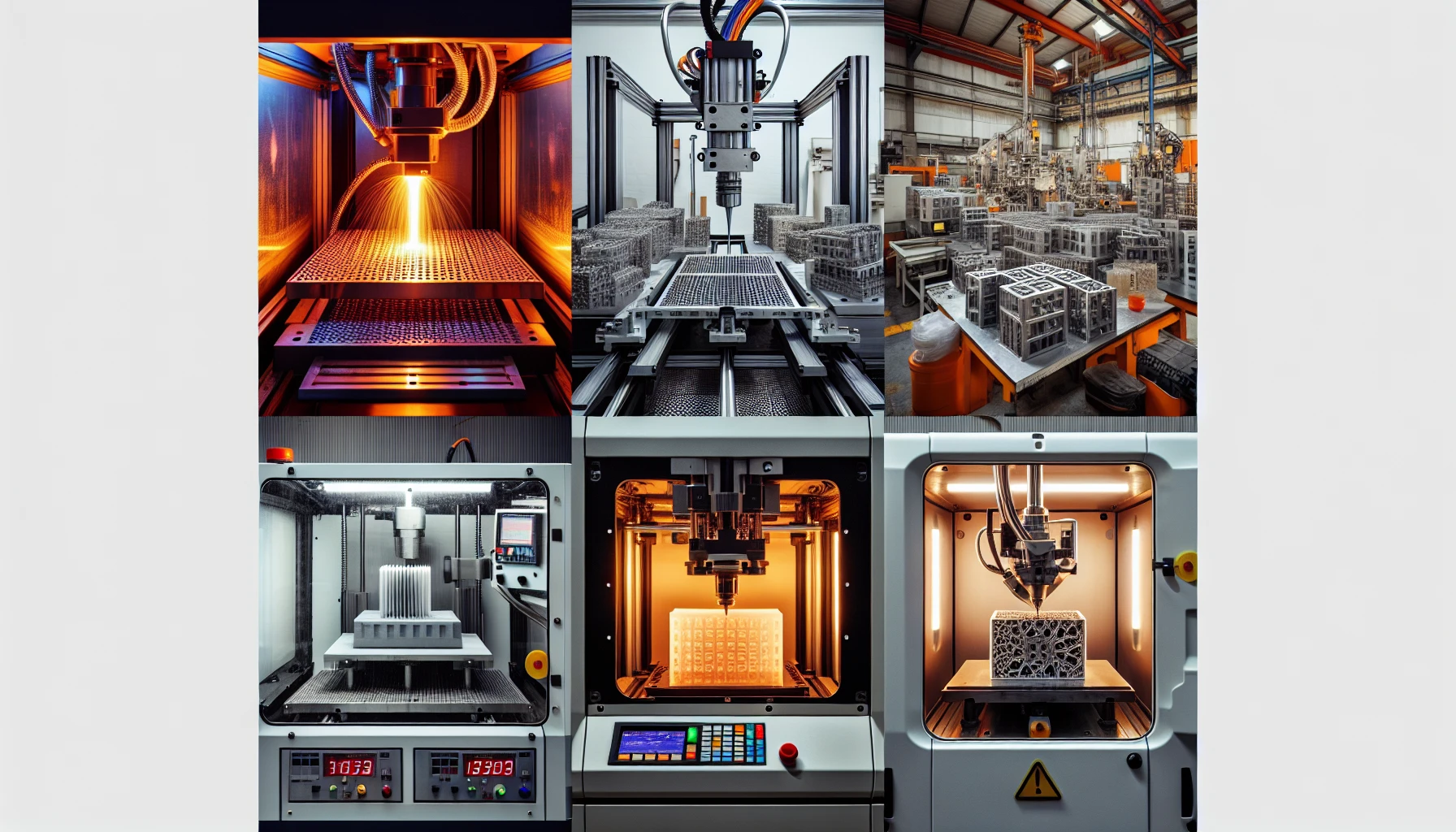
Considering alternative manufacturing processes is a necessary step in evaluating the cost-effectiveness of injection molding. In this section, we’ll compare injection molding to three popular alternatives: 3D printing, CNC machining, and blow molding. By understanding the advantages and disadvantages of each process, you can make an informed decision about which method is best suited for your specific project needs.
We’ll now analyze each of these alternative manufacturing processes in depth and compare them with injection molding in terms of cost, complexity, and production volume.
3D Printing
3D printing is a cost-effective option for low-volume production and complex geometries. Unlike injection molding, 3D printing builds objects layer by layer using a digital model, which allows for more intricate designs and internal features. However, 3D printing may not be suitable for high-volume production due to its size restrictions, rate, tolerances, and expense.
In terms of cost, 3D printing is generally cheaper than injection molding for complex geometries and low-volume production, as it does not require the expensive molds used in injection molding. However, for those seeking injection molding cheap options, it becomes more economical at the 40,000-50,000 part mark, making injection molding cheaper in the long run for high-volume production.
When it comes to quality, injection molded parts are typically considered to be of higher quality and strength than 3D printed parts.
CNC Machining
CNC machining can be more precise and cost-effective for prototype quantities and large runs, depending on the partner’s experience. This manufacturing process offers tighter tolerances than injection molding, resulting in more precise measurements. In terms of cost, CNC machining may be more economical for small quantities or prototypes due to lower tooling costs.
However, for large production runs, the cost-effectiveness of CNC machining depends on the complexity of the part and the partner’s proficiency. When comparing the cost of CNC machining with injection molding, it’s essential to consider the specific requirements of your project and the partner’s experience.
Blow Molding
Blow molding is a suitable alternative for hollow parts and containers but may not be ideal for solid parts. This manufacturing process involves heating a plastic tube and inflating it with air or gas to take the shape of a mold, forming a hollow plastic part. Blow molding is more suitable for producing simpler, hollow structures than injection molding, which is better suited for creating more intricate, solid parts that demand greater accuracy.
In terms of cost, blow molding generally has lower operational and tooling costs compared to injection molding. However, the choice between blow molding and injection molding will ultimately depend on the specific requirements of your project, such as the complexity of the part, production volume, and desired material properties.
Selecting the Right Injection Molding Partner
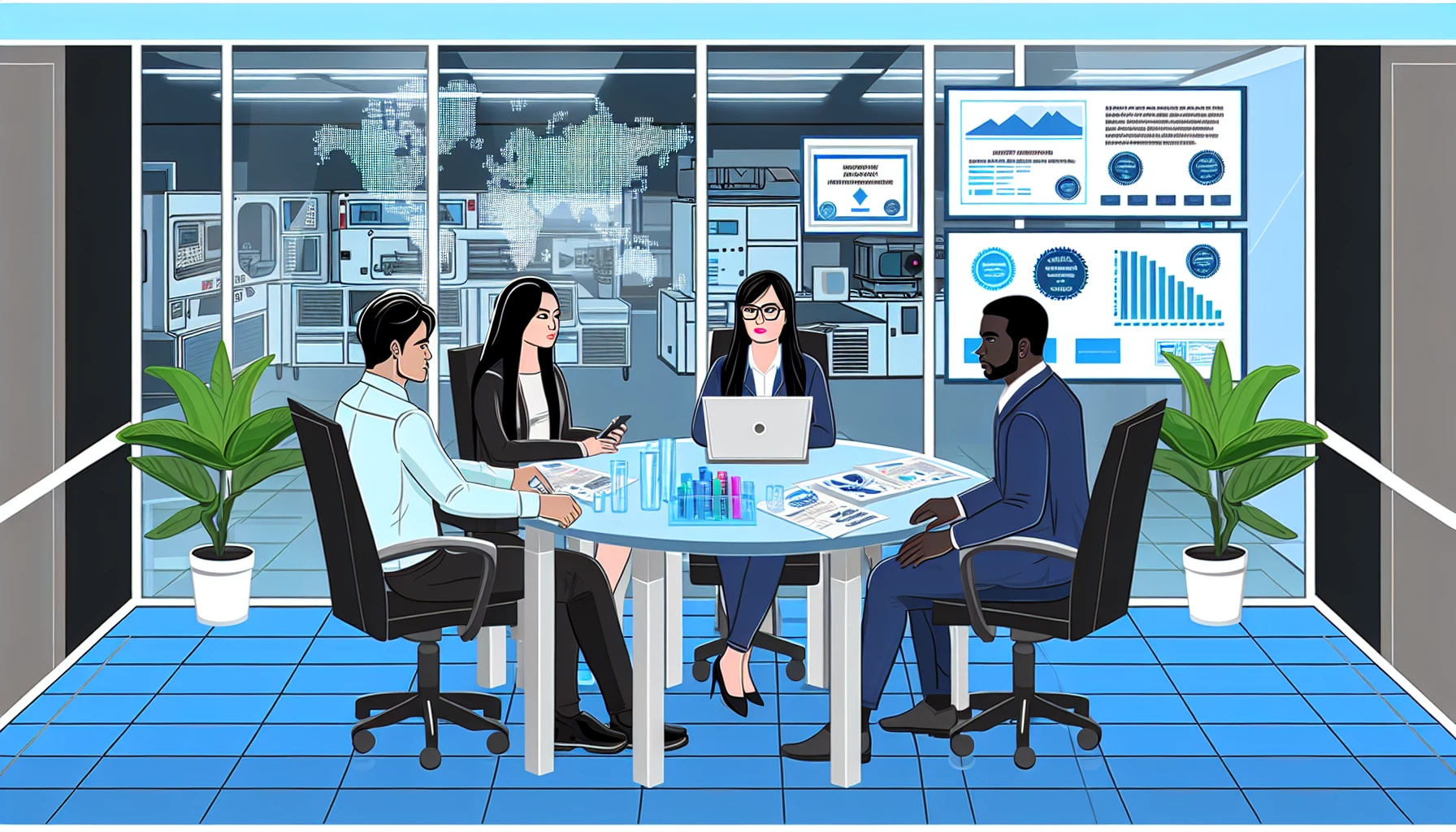
Choosing an appropriate injection molding partner is key to optimizing costs and guaranteeing the quality of your final product. In this section, we’ll discuss the importance of considering factors such as location, experience and expertise, and certifications when choosing an injection molding partner.
A careful evaluation of these factors will help you identify a partner who can meet your unique needs and assist in achieving your project goals. We’ll delve deeper into each of these factors to assist you in making an informed decision.
Location
The location of your injection molding partner can have a significant impact on shipping costs and lead times. It’s essential to consider both onshore and offshore options when selecting a partner. Working with a local partner can offer advantages such as optimized supply chain, cost savings, and support for local businesses and economies.
On the other hand, offshore injection molding partners can provide cost savings on piece prices and initial costs compared to domestic competitors, as well as a comprehensive range of manufacturing capabilities. However, it’s crucial to weigh the pros and cons of each option and take into account factors such as shipping logistics and regulations when making your decision.
Experience and Expertise
Partnering with experienced manufacturers is essential for optimizing costs and ensuring the quality of your injection molding project. An experienced injection molding partner should possess expertise in:
- Raw materials
- Custom injection molding
- Industry-specific accreditations
- Working with specific materials
- Certifications
- Quality control measures
- Mold tooling capabilities
- Various injection molding presses
When assessing the experience and expertise of an injection molding manufacturer, consider factors such as:
- Their industry experience
- Their portfolio of past projects
- The quality of their equipment and facilities
- Any relevant certifications and quality standards they hold
Certifications
Certifications like ISO, ITAR, and AS9100 are essential for ensuring that your injection molding partner adheres to industry standards and regulations. These certifications demonstrate a commitment to quality and safety and help ensure that your injection molding partner’s products and services meet the necessary standards.
When selecting an injection molding partner, it’s crucial to consider their certifications and verify that they have the appropriate qualifications to handle your project. This will help ensure that your injection molding project runs smoothly and results in high-quality, durable parts that meet your specific requirements.
Summary
In conclusion, optimizing injection molding costs involves considering factors such as material selection, mold design complexity, production volume, and labor and overhead expenses. By simplifying part design, optimizing material usage, and leveraging economies of scale, you can reduce costs while maintaining high-quality parts. Comparing injection molding to alternative manufacturing processes like 3D printing, CNC machining, and blow molding can also help you make informed decisions about the best method for your specific project needs. Finally, selecting the right injection molding partner who has the necessary experience, expertise, and certifications is crucial for ensuring project success and optimizing costs.
Frequently Asked Questions
What factors influence the cost of injection molding?
Costs of injection molding are influenced by material selection, complexity of mold design, production volume, and labor and overhead expenses.
How can I reduce costs in my injection molding project?
Reduce costs in your injection molding project by simplifying part design, optimizing material usage, and leveraging economies of scale.
How does injection molding compare to alternative manufacturing processes like 3D printing, CNC machining, and blow molding?
Injection molding is an efficient and cost-effective process for high-volume production of simpler parts, compared to alternative manufacturing processes like 3D printing, CNC machining, and blow molding which are more suitable for producing complex parts in low volumes.
What should I consider when selecting an injection molding partner?
When selecting an injection molding partner, consider location, experience and expertise, and certifications to make sure they can fulfill your project requirements and maximize efficiency.
How does production volume affect the cost of injection molding?
Increased production volumes generally lead to lower costs per part due to the advantages of economies of scale and the amortization of tooling and setup costs over a larger quantity.