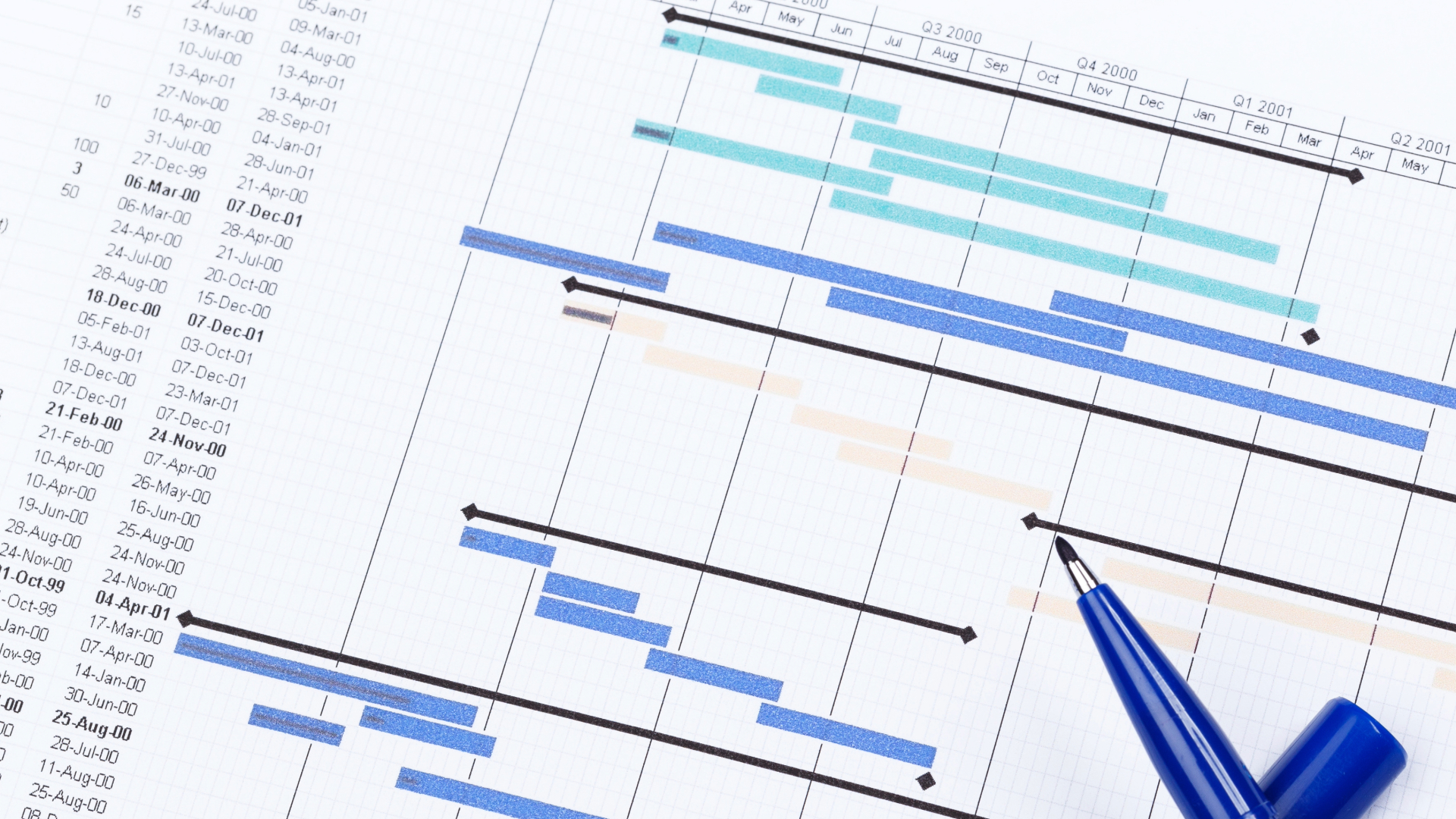
In manufacturing, timing is everything. For example, a recent industry survey found that 45% of manufacturers faced production delays due to material shortages (Source: National Association of Manufacturers, 2023 Manufacturing Outlook Survey).
The ability to meet production schedules and deliver on customer expectations hinges largely on one critical factor: material availability. Lead times—the period between placing an order and receiving materials—play a vital role in determining how well a manufacturing process flows.
Properly managing lead times can mean the difference between a successful project and costly delays. For example, a manufacturer that proactively managed lead times by collaborating closely with suppliers was able to meet customer deadlines and avoid downtime. On the other hand, another project suffered significant losses due to extended lead times and poor planning, resulting in missed deliveries and customer dissatisfaction. In this article, we’ll discuss why lead times matter and provide best practices for effectively planning for material availability.
Understanding Lead Times
Lead time is the time between placing an order and receiving materials. This period can vary widely depending on factors such as supplier location, material type, production capacity, and shipping logistics. Understanding the different components of lead time, including procurement, production, and transit, helps manufacturers plan accordingly and avoid potential disruptions.
The Impact of Lead Times on Manufacturing
Lead times directly affect the entire production schedule. When materials are not available when needed, production lines can be halted. This causes costly downtime and delays final product deliveries to customers. Long or unpredictable lead times can also lead to overstocking, which ties up capital and increases storage costs. By effectively managing lead times, manufacturers can achieve a more predictable flow, keep costs in check, and maintain the flexibility to respond to market demands.
Best Practices for Managing Lead Times
Build Strong Supplier Relationships
One of the most effective ways to manage lead times is by developing strong relationships with suppliers. A reliable supplier can provide more accurate lead time estimates and may prioritize your orders in times of high demand. By establishing long-term relationships, manufacturers can work collaboratively with suppliers to anticipate challenges, discuss forecasted needs, and even negotiate better terms for lead time reductions. For example, a manufacturer worked closely with a trusted supplier over several years, which enabled them to expedite orders during a critical production period, avoiding costly delays and ensuring on-time delivery.
Forecast Demand Accurately
Effective demand forecasting is crucial for managing lead times. By understanding anticipated production requirements, manufacturers can place orders in advance and minimize the risk of shortages. Forecasting tools like SAP Integrated Business Planning or Oracle Demantra, along with data analytics, can help identify demand patterns, allowing procurement teams to better align material orders with production schedules and reduce the impact of extended lead times.
Maintain Safety Stock
Keeping a buffer or safety stock of critical materials, typically around 10-15% of usual demand, can help mitigate the impact of unexpected delays. Safety stock acts as a cushion, ensuring production can continue even if lead times extend or unforeseen disruptions occur. However, it is important to strike the right balance—holding too much inventory can be costly, while holding too little can increase the risk of production stoppages.
Use Just-in-Time (JIT) Strategies Carefully
Just-in-Time (JIT) inventory management aims to minimize inventory levels by receiving materials only as they are needed in the production process. However, if the supply chain is not highly reliable, JIT can lead to significant disruptions and production delays. While this approach can reduce holding costs, it requires a highly reliable supply chain. For JIT to be successful, manufacturers must have absolute confidence in their suppliers’ ability to deliver materials on time, every time. Otherwise, any delay can have a significant ripple effect on production.
Leverage Technology and Real-Time Tracking
Technology can play a significant role in managing lead times. Using ERP (Enterprise Resource Planning) systems like Business Central, SAP or Oracle NetSuite, or supply chain management software, can provide real-time visibility into the status of orders and lead times. This level of visibility allows manufacturers to identify potential delays early and take corrective action before they impact production schedules. Real-time tracking also facilitates better communication with suppliers, helping to set realistic expectations and manage changes effectively.
In the competitive landscape of manufacturing, effectively managing lead times is essential for maintaining production efficiency, minimizing costs, and meeting customer expectations. By adopting best practices like building strong supplier relationships, forecasting demand accurately, leveraging technology, and maintaining safety stock, manufacturers can reduce the impact of lead times and keep their operations running smoothly. Lead times are a critical component of any manufacturing strategy, and proactive management is key to ensuring material availability and overall success.