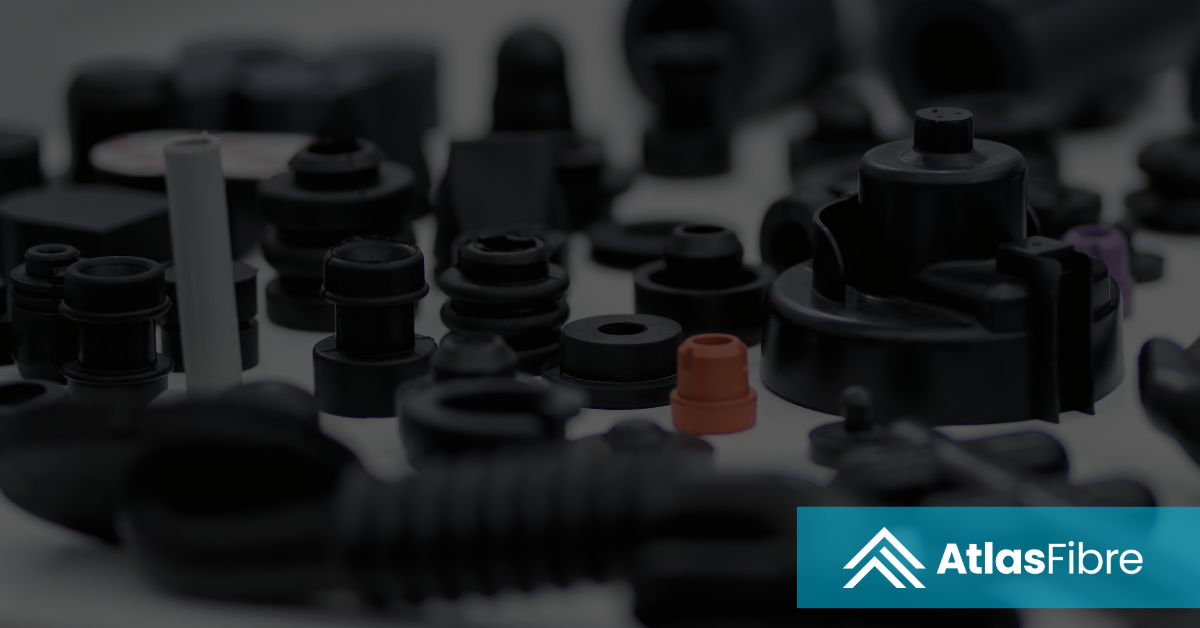
Why the Difference Matters for the Most Critical Industry Components
In the race to electrify everything—from vehicles and batteries to grid infrastructure—choosing the right material isn’t just important. It’s mission-critical.
If you’re designing or sourcing parts for electrified systems, there’s a high chance thermoset composites are already on your radar. These materials—often based on epoxies, phenolics, or polyesters—are prized for their strength, dimensional stability, and resistance to heat, chemicals, and electrical arcing.
But here’s the question you might not be asking: Should that part be machined or molded?
It might sound like a manufacturing detail. But the answer could be the difference between consistent performance over time—or catastrophic failure in the field.
Thermosets 101: What Makes Them Different
Unlike thermoplastics, which melt and remelt, thermosets undergo a chemical transformation during curing that makes them permanently hard and heat-resistant. Once set, they don’t soften again—making them ideal for high-performance applications where failure is not an option.
Think: busbars in EV battery packs, arc barriers in switchgear, or thermal insulators for power electronics. These aren’t applications that tolerate compromise.
Molded Parts: Economical but Limiting
Molding thermosets can be cost-effective—especially at scale. With the right tooling, manufacturers can produce high volumes of parts relatively quickly. But that efficiency comes at a price.
Here’s the tradeoff:
- Molded parts often require design concessions to accommodate tool constraints.
- Material properties can vary across complex geometries due to inconsistent fill and cure.
- High internal stresses during molding can compromise long-term durability, especially under thermal or electrical load.
In other words, molded parts are great for the right job—but not always the right fit when consistency and performance come first.
Machined Thermosets: Built for Demanding Conditions
Machined thermoset parts start from fully cured sheets, rods, or tubes. This material has already been through the heat and pressure cycle, giving it a homogenous structure with predictable performance throughout.
The benefits?
- Tight tolerances: CNC machining allows for precise, complex geometries that molded processes can’t always match.
- Consistency: No flow lines, voids, or weak spots from tooling. What you get is what the material is, through and through.
- Durability: Machined parts maintain their integrity under stress, load, and time—especially important in high-voltage or high-heat environments.
For engineers designing next-gen electrification systems, these aren’t just nice-to-haves. They’re often dealbreakers.
So… When Should You Machine?
If the part is exposed to:
- High voltages
- Significant temperature swings
- Long-term mechanical or thermal stress
- Strict tolerances or complex geometries
…machining is almost always the better choice.
Especially for low-to-mid volumes, prototypes, or parts that evolve during development, machining delivers both flexibility and reliability.
And when repeatability and consistency are mission-critical—as they often are in electrification—machining wins, hands down.
Final Thoughts: It’s Not Just a Manufacturing Choice. It’s a Performance One.
As industries push the limits of electrification, the materials and methods used to build components are coming under a microscope. And rightly so. What holds up in a test lab doesn’t always hold up in the field.
The durability of machined thermoset parts—especially in harsh electrical environments—makes them the go-to solution when performance has to be predictable.
Because at the end of the day, a molded part might meet spec.
But a machined part?
It exceeds it—every time.