Curious about taking your production to the next level with high speed machining? Understanding these sophisticated systems is key to leveraging their speed and precision. Our guide uncovers the principles of high speed machine technology, detailing the practices and tooling that drive efficiency and delineating the benefits they introduce to modern manufacturing.
Key Takeaways
High speed machining (HSM) relies on core factors like rigidity of the machine setup, precise tool balancing, and proper clamping methods to ensure accuracy, repeatability, and high-quality finishes.
Selecting the appropriate tool for HSM is critical, and involves considerations on cutter geometry, material composition of tools, and the holding mechanisms to ensure stability and minimize vibrations at high RPMs.
Optimization of feeds and speeds is crucial for HSM efficiency, with techniques like calculating chip load, adjusting for radial chip thinning, and innovative milling strategies like trochoidal milling enhancing productivity and precision.
Essentials of High Speed Machining
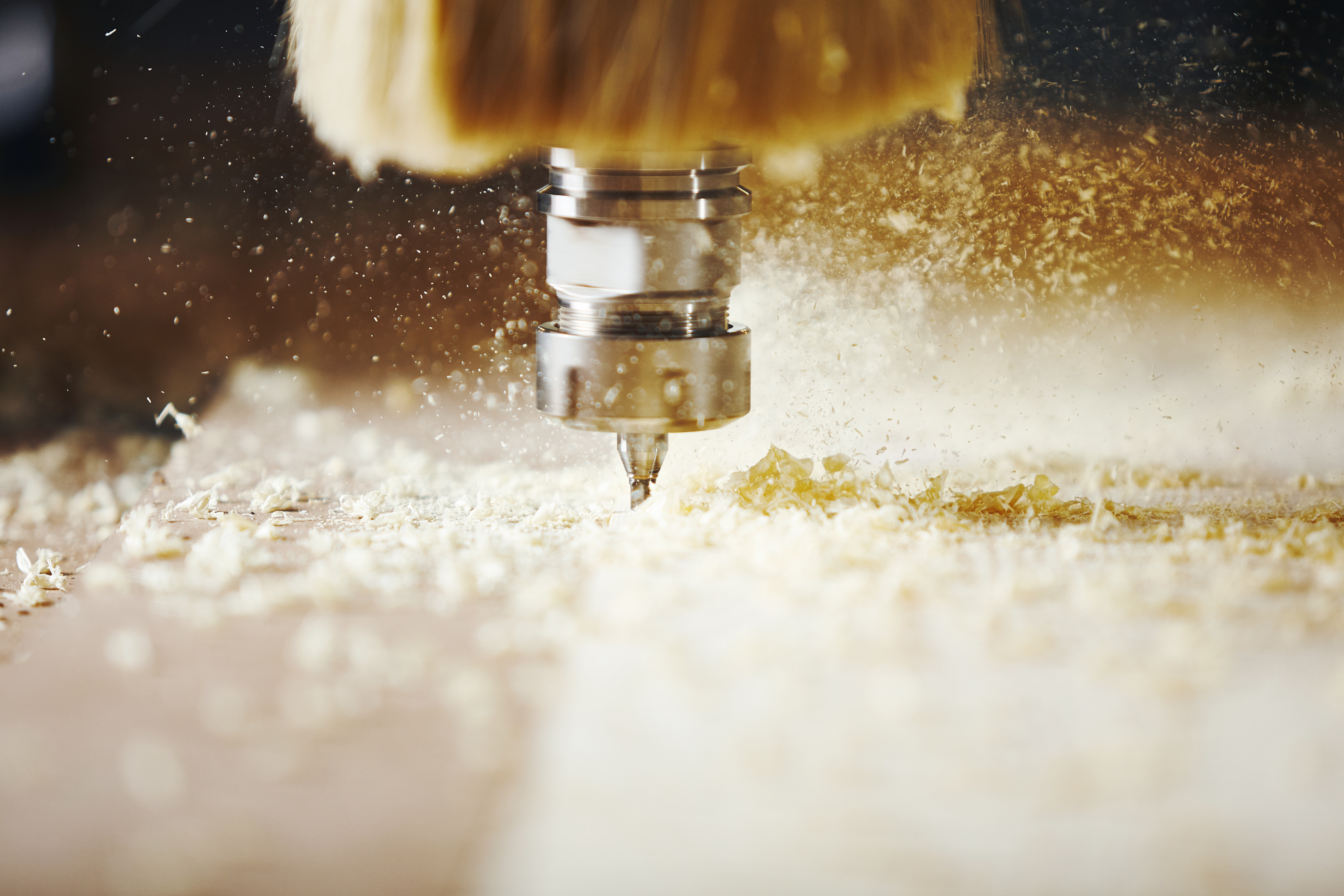
At the heart of a successful high speed machining operation lie three core factors: rigidity, tool balancing, and proper clamping methods. These essentials ensure the accuracy, repeatability, and quality surface finishes that distinguish HSM from traditional machining. They form the bedrock upon which high-speed, high-precision milling is built.
Rigidity in High Speed Machining
Within high-speed machining, rigidity extends beyond being a desirable trait to becoming an absolute necessity. A rigid machine setup minimizes tool deflection, thereby ensuring that the tool follows the programmed path with minimal deviation. This is crucial for achieving high-quality surface finishes and accurate parts.
Tailored toolholder designs and a stable work holding fixture further contribute to rigidity, reducing vibration and countering the bending forces that could compromise the precision of the machining process. The result? Lower cutting forces, reduced heat generation, and consistent adherence to precision engineering standards that uphold the integrity of the workpiece and the tool.
Tool Balancing for High Speed Machining
Picture driving a car with misaligned wheels. Regardless of how powerful the engine is, the ride is likely to be bumpy and inefficient. The same principle applies to high-speed machining. Without proper tool balancing, excessive vibration can lead to spindle damage and compromised part quality, no matter how advanced your CNC machines might be.
To achieve smooth operation and preserve the life of both machine and tooling, toolholders can be corrected for unbalance by either adding or removing material. Furthermore, high-speed applications often require toolholders to be balanced to a finer degree, ensuring desired fits and surface finishes without vibrations even above 10,000 rpm.
Proper Clamping Methods
Similar to how a painter requires a steady canvas to create a masterpiece, a high-speed machining operation also necessitates appropriate clamping methods. The choice of clamping method should be based on the workpiece’s geometry and material, as well as the specific machining operation. From dovetail vises to edge clamps and grippers, the right clamping technique can secure the workpiece during high-speed machining, preventing chatter and ensuring high-quality surfaces.
High Speed Machining Tool Selection
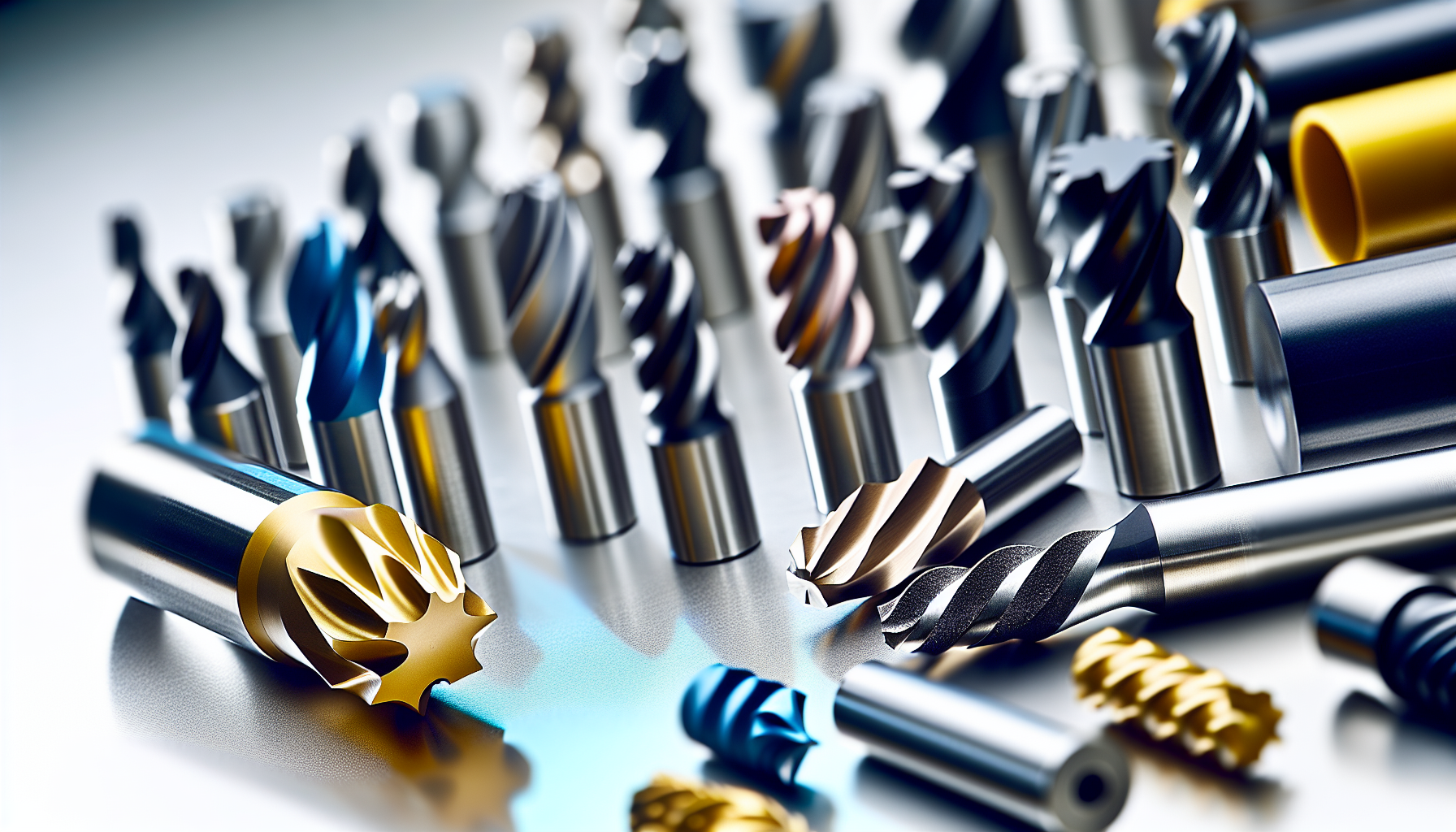
In the same way a master chef picks the perfect knife for every culinary task, a machinist needs to select the right tool for each high-speed machining task. Whether it’s a simple roughing operation or a complex finishing task, the right tool selection can make all the difference. This involves considering factors such as the cutter’s geometry, the tool material’s composition, and the holding mechanism. Each of these elements plays a crucial role in determining the tool’s performance and the quality of the finished part.
Cutter Geometry for High Speed Machining
Within high-speed machining, the longevity and stability of the cutting process hinge upon the geometry of the cutting tool. For instance, a larger corner radius on cutting tools disperses stress more effectively, thus contributing to improved tool life and a longer life for the overall process.
Additionally, a cutting edge designed with a slight rounding provides additional stability by distributing cutting pressure more evenly, particularly when machining materials like nylon. This helps in achieving the desired depth of cut without compromising the tool’s performance.
Material Composition of High Speed Machining Tools
In the context of high-speed machining, the tool’s composition holds equal importance to its form. Tungsten carbide, for instance, is widely used in HSM tools due to its ability to handle high surface feet per minute and its broad working range. Polished carbide endmills offer another advantage by allowing chips to slide off easily, providing a smooth, low-heat cut.
For applications requiring even higher cutting speeds, up to 4000 sfm, silicon nitride and other ceramic materials are suited due to their high-temperature tolerance. At the extreme end of high-speed machining, tools coated with polycrystalline diamond and Cubic Boron Nitride (CBN) can withstand even higher thermal loads, pushing cutting speeds above 4000 sfm.
Holding Mechanisms for High Speed Machining Tools
A proficient conductor’s role extends beyond leading the orchestra to making sure each instrument plays in sync. Similarly, in high-speed machining, the holding mechanism serves to ensure the vibration-free cutting and stability of the tool. High-speed machining requires specialized tool holders that maintain balance and prevent runout at high RPMs. Some examples of tool holders used in high-speed machining are:
HSK (Hohl-Schaft-Kegel) toolholder interface, which provides increased contact area and rigidity, contributing to better tool life and surface finishes in high-speed applications
CAT (Caterpillar) toolholder interface, which is widely used in the industry and offers good balance and stability
BT (Boring Tool) toolholder interface, which is commonly used in milling applications and provides good rigidity and accuracy
Using these specialized tool holders can greatly improve the performance and efficiency of high-speed machining operations.
Additionally, spindle speeders can:
Increase spindle speed, which is beneficial for executing small, detailed work on larger spindles
Ensure rigidity and stability of the spindle-tool connection
Pave the way for a seamless high-speed machining process
These smaller tools and strategies are instrumental in ensuring a successful high-speed machining process.
Optimizing Feeds and Speeds in High Speed Machining
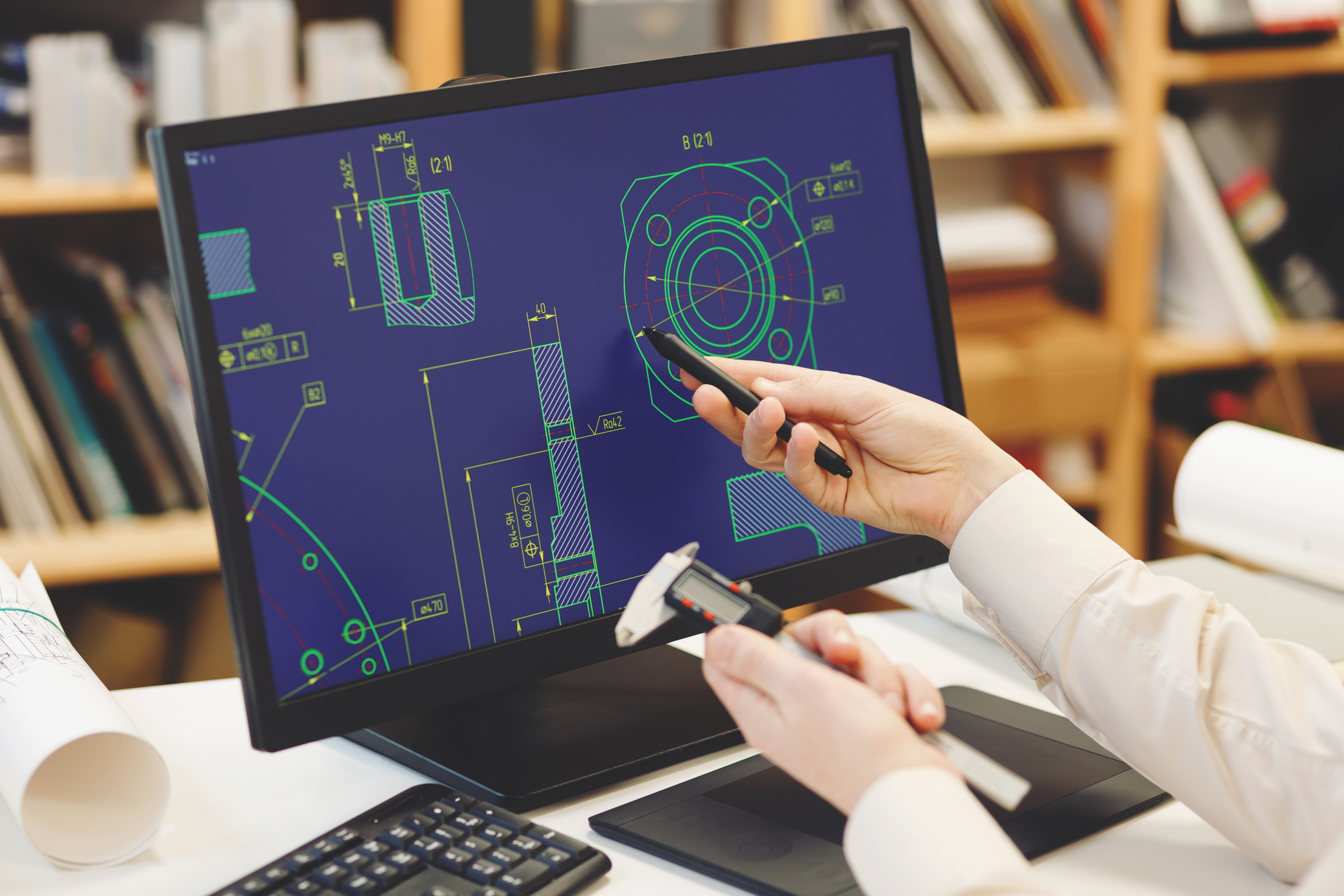
Shorter machining times and enhanced efficiency in high-speed machining are reliant on the optimization of feeds and speeds. Determining the best feeds and speeds involves considering a multitude of factors such as:
The machine
The spindle
The material
The tool
The work holding
The type of tool
The depth of pass
Through trial and test methods such as Tap Testing and Vibration Testing, one can optimize feed and speed settings, leading to a more efficient and productive machining process.
Calculating Chip Load
In machining, chip load holds a similar role to a patient’s pulse rate. It’s a vital sign that helps determine the health of your machining process. Chip load is the size or thickness of the chip that is removed with each flute per revolution. To calculate chip load, one can use the formula: Chip Load = Feed Rate (inches per minute) / (RPM x number of flutes).
For instance, using a feed rate of 500 inches per minute with a speed of 15,000 RPM and a 2-flute cutter results in a chip load of 0.017 inches. Understanding chip load is integral to determining the optimal feed rate and spindle speed in high-speed machining. It’s the vital sign that keeps your machining process running smoothly and efficiently.
Adjusting Chip Load
Knowing how to adjust chip load is similar to understanding how to shift gears in a car. Just as shifting gears allows you to control the car’s speed and power, adjusting chip load enables you to increase material removal rates and reduce cycle time, leading to a more efficient machining process. Optimizing chip load aims to maximize cubic inches of material removed, providing a more productivity-oriented approach and better economic sense.
One important factor to consider when adjusting chip load is radial chip thinning. This occurs when the width of cut is less than half the cutter’s diameter, necessitating an increase in feed rate to maintain the recommended chip load. In instances where spindle speed limits productivity, high feed endmills can be employed to exploit axial chip thinning and substantially increase the high feed rates. This is akin to shifting into high gear for a smoother and more efficient ride.
Trochoidal Milling and Other HSM Techniques
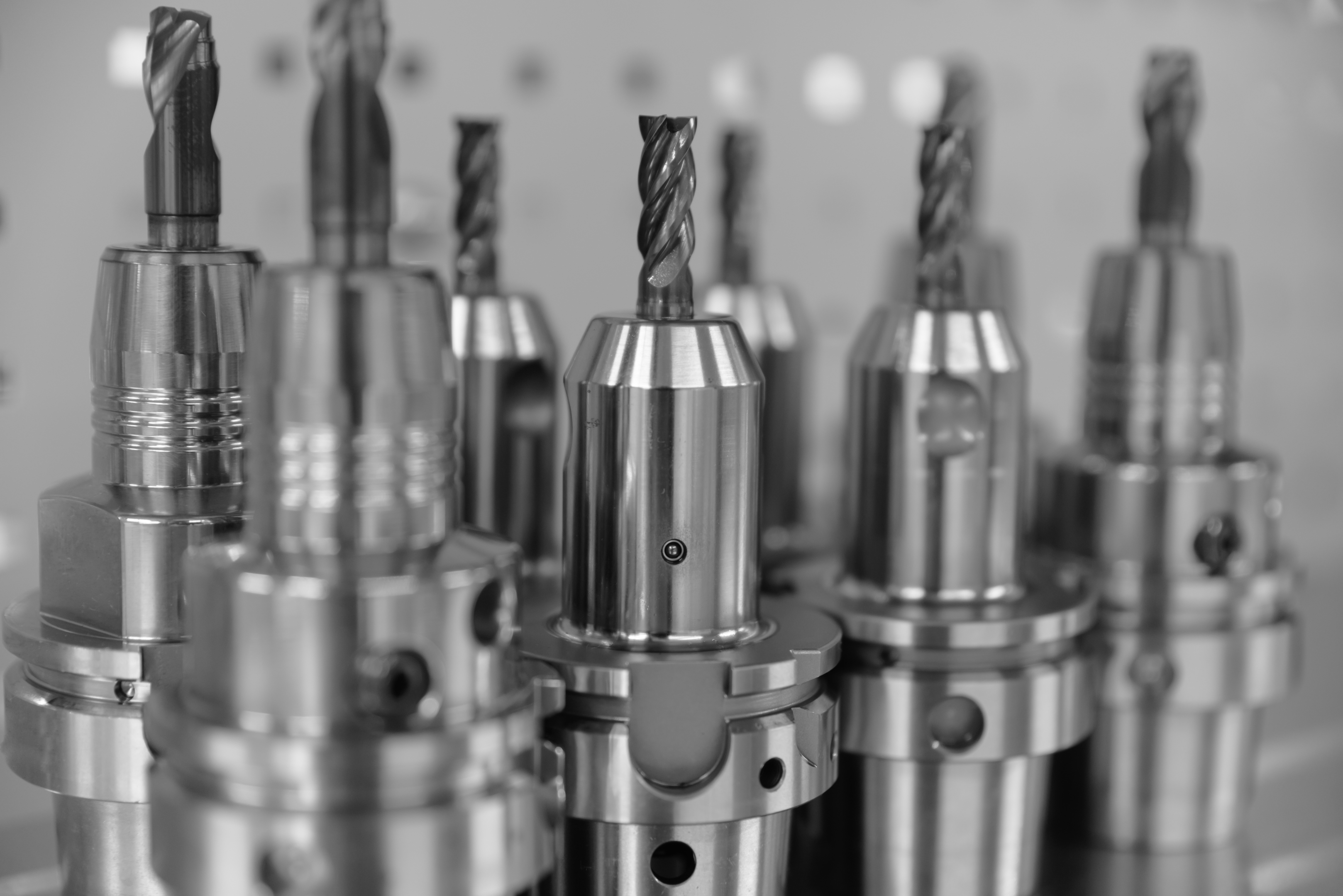
Innovation is the driving force of high-speed machining, including advanced high speed milling techniques like:
Trochoidal milling, which uses a spiral tool path to maintain constant chip thickness
Adaptive milling, which adjusts the cutting parameters in real-time based on the material and tool conditions
High-efficiency milling, which maximizes material removal rate while minimizing tool wear
have revolutionized the milling process. These techniques not only enhance the milling process but also save time by allowing the use of the same tool for slots of different sizes.
Other cutting-edge HSM techniques, such as Constant Tool Engagement Angle (CTEA) strategies like Volumill and Adaptive Clearing, use looping toolpaths to maintain a consistent tool engagement angle. This avoids over-engagement of cutters and potentially increases machining speeds. With advancements in computing, these complex HSM techniques have evolved to meet modern machining challenges, offering a potent combination of speed, precision, and efficiency.
Material Considerations in High Speed Machining
High-speed machining is not a universal solution. Just as an artist chooses different brushes for different strokes, a machinist must tailor HSM strategies to the specific material at hand. Techniques that work for composites may not suit thermoplastics, highlighting the need for a diverse approach to machining.
Beyond the technical requirements, the cost of material can also influence the machining process. Less expensive materials are often utilized for prototyping before machining parts from more expensive product. The strength-to-weight ratio often guides the selection between high-performance plastics, particularly in industries like aeronautics and space where this ratio is significant.
Machine Requirements for High Speed Machining
The effectiveness of high-speed machining is dependent on the machine’s capabilities. Some key machine requirements for HSM include:
Advanced spindle technologies
Robust structures
Efficient chip evacuation systems
Spindle-driven speeders
Hydrostatic and hydrodynamic systems
HSK spindle tapers
These features enhance high-speed machining by increasing rpm, maintaining precision, and improving toolholding rigidity.
High-speed machining centers are designed with the following features:
Robust structures, such as polymer granite bases, to withstand high-speed operations and maintain thermal stability
Positional feedback and advanced control systems that implement block look ahead for seamless toolpath execution to maintain precision
Efficient chip evacuation systems like oil mist/air blast or coolant systems to meet the demanding requirements of high-speed machining
These features equip machines to meet the demanding requirements of high-speed machining.
Benefits of High Speed Machining
High-speed machining provides numerous advantages over traditional machining methods. Here are some of the benefits:
Achieving high material removal rates
Improving productivity
Lowering manufacturing costs
Maintaining precision and quality
That’s the magic of HSM video – just sit back and watch.
Parts machined at high speeds, especially those made of aluminum, exhibit better dimensional accuracy and superior surface smoothness, crucial for parts necessitating high-quality finishes. The use of advanced cutting tools, coatings, and precise tooling minimizes tool wear and extends tool life. The faster cycle times in high-speed machining also contribute to reducing the overall cost of manufacturing parts. It’s a win-win situation that makes high-speed machining a highly attractive proposition for manufacturers.
Real-World Applications of High Speed Machining

High-speed machining extends beyond being just a theoretical concept; it is a practical solution revolutionizing industries globally. Initially developed for the aerospace industry, HSM strategies have been widely integrated into various CAM software, enhancing productivity in multiple sectors.
The automotive sector, for instance, employs HSM for the mass production of parts, significantly reducing cycle times to satisfy high consumer demand and maintain efficiency. The electronics industry uses HSM to manufacture intricate components necessary for consumer electronics, focusing on miniaturization and superior finishes. Similarly, the energy sector employs HSM for the precise and efficient creation of components such as turbine blades. Even the defense industry benefits from high-speed machining for the production of high-quality, custom parts.
It’s clear that HSM has a wide range of applications, making it an invaluable tool in the modern manufacturing landscape.
Summary
In the fast-paced world of modern manufacturing, high-speed machining stands out as a game-changer. From its core essentials of rigidity, tool balancing, and proper clamping, to the intricacies of tool selection, feed optimization, and advanced machining techniques, HSM offers a potent blend of speed, precision, and efficiency. With its myriad benefits and wide-ranging applications across industries, it’s clear that high-speed machining is not just a trend, but a transformative force shaping the future of manufacturing. It’s time to embrace the speed, harness the power, and reap the benefits of high-speed machining.
Frequently Asked Questions
What is a high speed mill?
A high-speed mill is a type of milling that involves fast, lighter cuts using high spindle speeds and specific tools. It replaces slow, heavy cuts with faster, lighter ones.
What is high speed cutting machine?
A high speed cutting machine is a tool that utilizes high feed rates and spindle speed to efficiently remove material while maintaining part quality and precision. This approach provides a faster cycle time and extended tool life.
What is the rpm for high speed machining?
For high speed machining, the recommended rpm is 15,000 or greater, depending on the cutter diameter.
Why is tool selection important in high-speed machining?
Tool selection is crucial in high-speed machining because it directly impacts the tool’s performance and the final part’s quality. Factors such as cutter geometry, tool material, and holding mechanism should be carefully considered to ensure optimal results.
What is chip load and why is it important in high-speed machining?
Chip load is crucial in high-speed machining as it determines the optimal feed rate and spindle speed by measuring the size of the chip removed with each flute per revolution. This understanding is essential for achieving efficient and effective machining processes.