Navigating the world of CNC machining requires a firm grasp of millable plastics. This article zeroes in on the most effective plastics for milling, detailing their specific strengths and how to machine them to perfection for your next innovation.
Key Takeaways
Millable plastics are selected for CNC machining based on their mechanical properties, including impact strength, wear resistance, and dimensional stability, providing precision and performance advantages in diverse industries like medicine, automotive, and aerospace.
Top millable plastics such as PEEK, Acetal, Polycarbonate, and HDPE are chosen for their superior characteristics like high temperature and chemical resistance, impact strength, and electrical insulation, fulfilling technical requirements while reducing overall costs.
Successful CNC machining of plastics involves managing heat generation, selecting appropriate cutting tools, and ensuring proper material handling, while customization techniques and recycling efforts enhance material properties and contribute to sustainability.
Understanding Millable Plastics
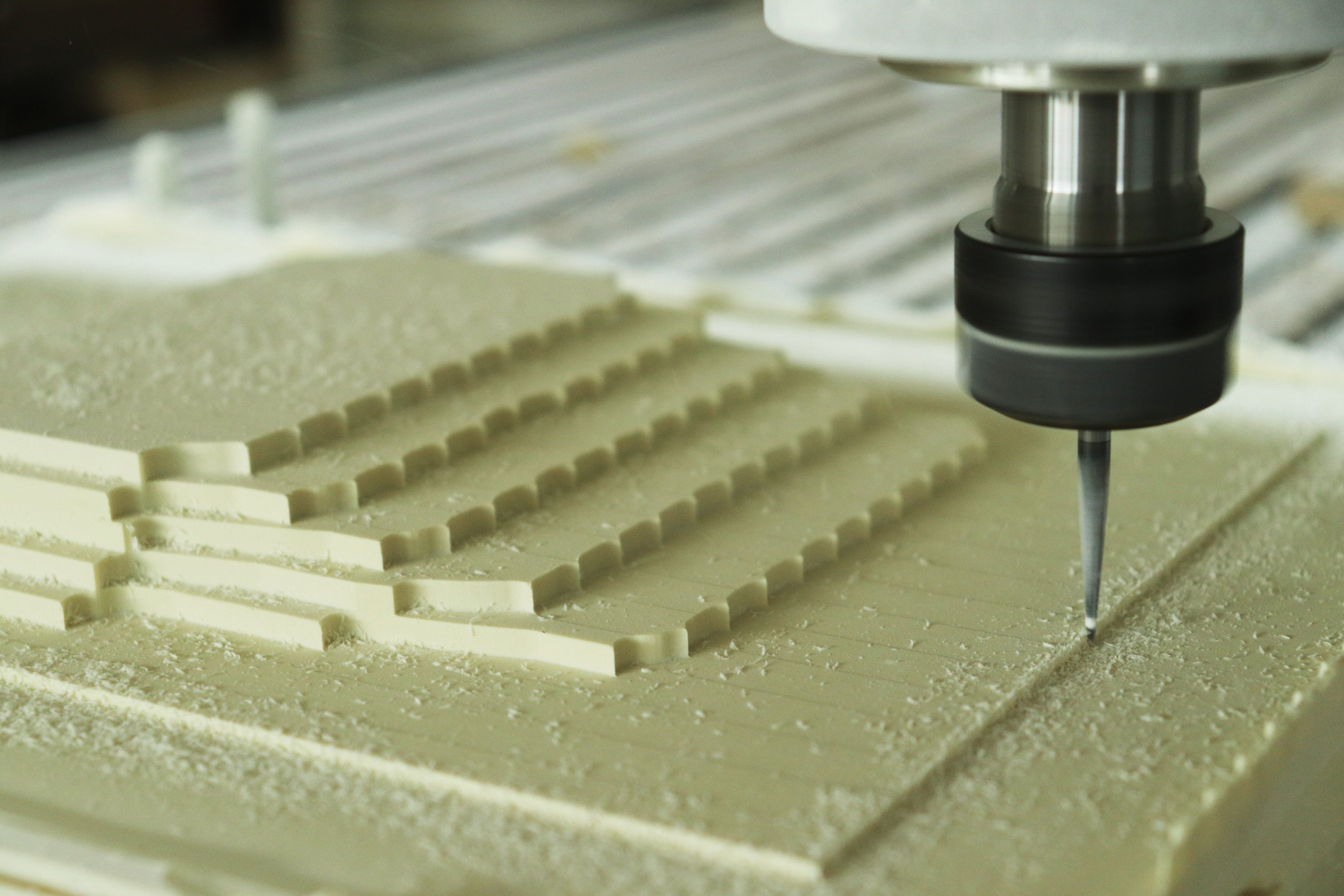
The allure of machining plastics over traditional materials like metals lies in their remarkable adaptability and the precision they afford CNC machined plastics. The process of selecting the right plastic materials is not just about achieving the desired aesthetics; it’s about ensuring the functionality, appearance, and durability of the end product. Whether in the realm of medicine, automotive, aerospace, or beyond, the choice of a millable plastic can be the cornerstone of innovation.
What Makes a Plastic Millable?
The utility of a millable plastic primarily lies in its machinability, which is determined by its mechanical properties. A plastic’s suitability for CNC machining hinges on its impact strength, wear resistance, and, crucially, its dimensional stability. However, these characteristics are not static; they must endure across a spectrum of temperatures and mechanical stresses to be truly effective.
For instance, annealing heat resistant thermoplastics before machining can greatly enhance their stability, akin to tempering steel to perfect its hardness.
Why Use Millable Plastics in CNC Machining?
The reasons to use millable plastics in CNC machining are not limited to their physical characteristics but also include economic considerations. Plastics like ABS offer a cost-effective alternative for prototyping and general-purpose applications, ensuring projects remain within budgetary constraints.
The vast array of CNC plastics ensures there’s a suitable material for almost every project, and their straightforward machining process, albeit with careful management of mill speeds, ensures their place in the manufacturing lexicon.
Top Millable Plastics for CNC Machining
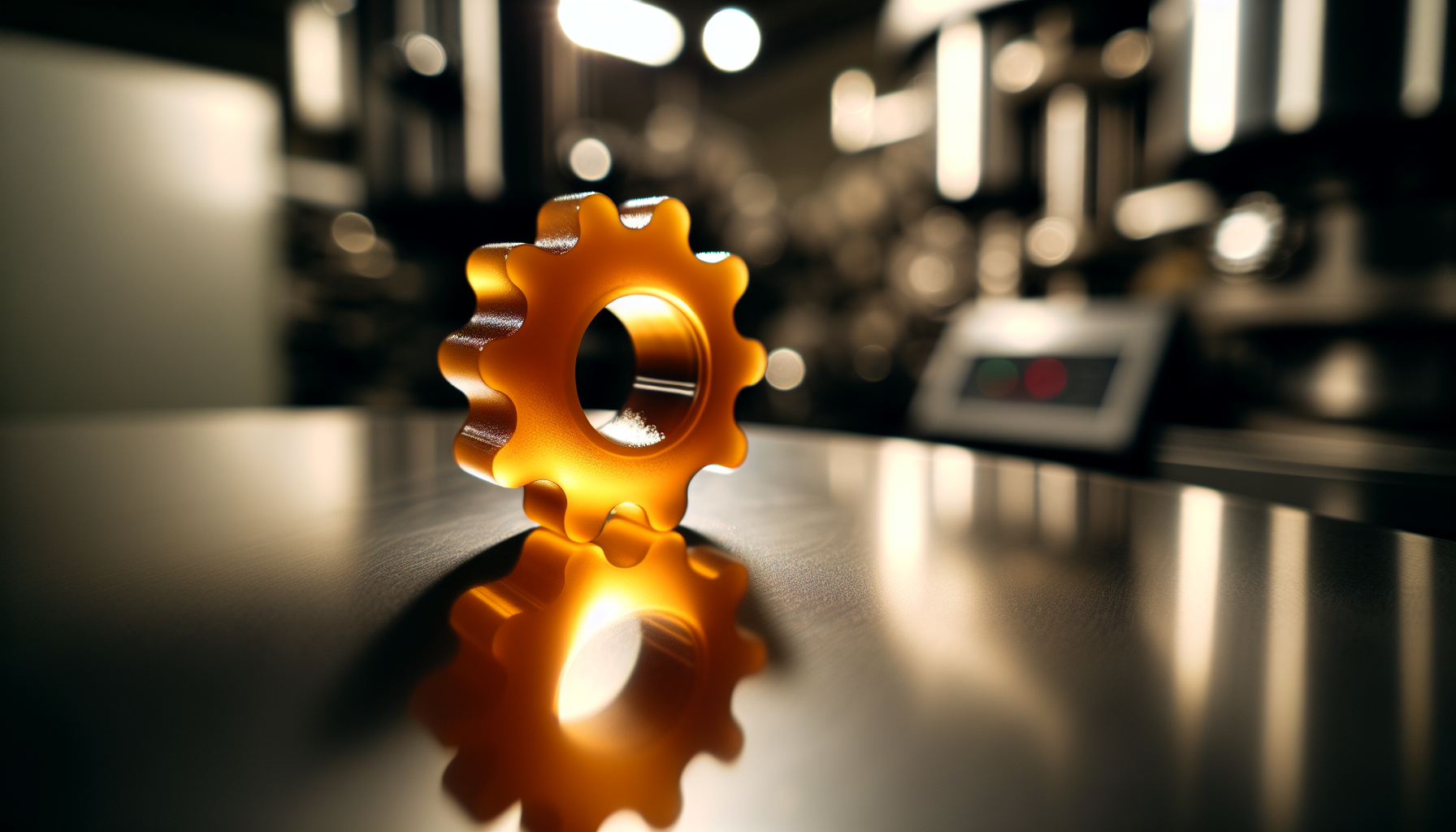
Certain plastics become the go-to materials in CNC machining when precision and performance are of utmost importance. Materials such as:
PEEK
Acetal
Polycarbonate
HDPE
CNC machined plastics are lauded for their superior impact strength, toughness, corrosion resistance, and resistance to electrical and environmental stresses. These low cost plastics not only fulfill stringent technical requirements but also contribute to lower lifetime freight costs due to their lighter weight, underscoring the practical benefits of opting for CNC machined plastics over heavier metals.
PEEK (Polyether Ether Ketone)
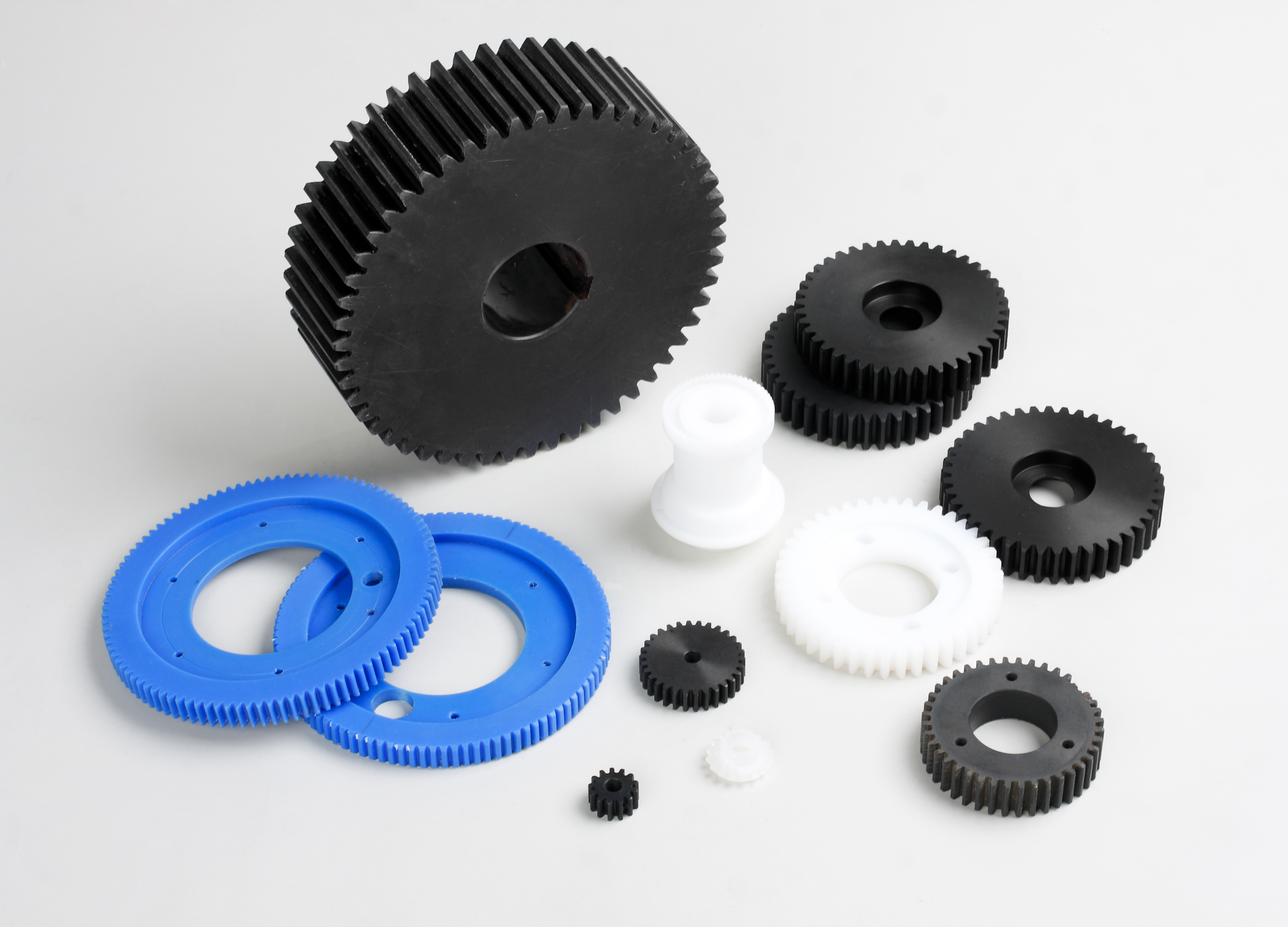
PEEK emerges as a paragon of high-performance thermoplastics, with its exceptional mechanical and good chemical resistance making it a stalwart in the most demanding environments. Its resilience to high temperatures, wear, and chemical interactions make it a material of choice for critical aerospace, medical, and automotive applications where failure is not an option.
Acetal (Delrin)
Acetal stands out for its machining ease, lending itself to precise fabrication that does not compromise its mechanical properties or dimensional accuracy. This strong plastic maintains its integrity even in the face of repeated impacts and varying temperatures, making it an ideal candidate for high-stress industrial applications.
Polycarbonate
Polycarbonate is the clear winner when transparency and durability are required in tandem. Its unique blend of optical clarity and impact resistance makes it a superior alternative to glass in many applications. Some of its key advantages include:
Toughness and resistance to breakage
Excellent optical clarity
High impact resistance
UV resistance
Ability to withstand higher temperatures
These qualities make polycarbonate a versatile and reliable choice for various industries and applications.
HDPE (High-Density Polyethylene)
HDPE’s reputation for strength and chemical resistance, coupled with its excellent electrical insulation properties, makes it a versatile player in a wide array of applications. Some common uses of HDPE include:
Fluid systems
Electrical insulators
Water pipes
Chemical tanks
Packaging materials
HDPE’s attributes are harnessed in industries that demand durability and resistance to moisture and chemicals without the weight penalty of metals.
Tips for Successfully Machining Millable Plastics
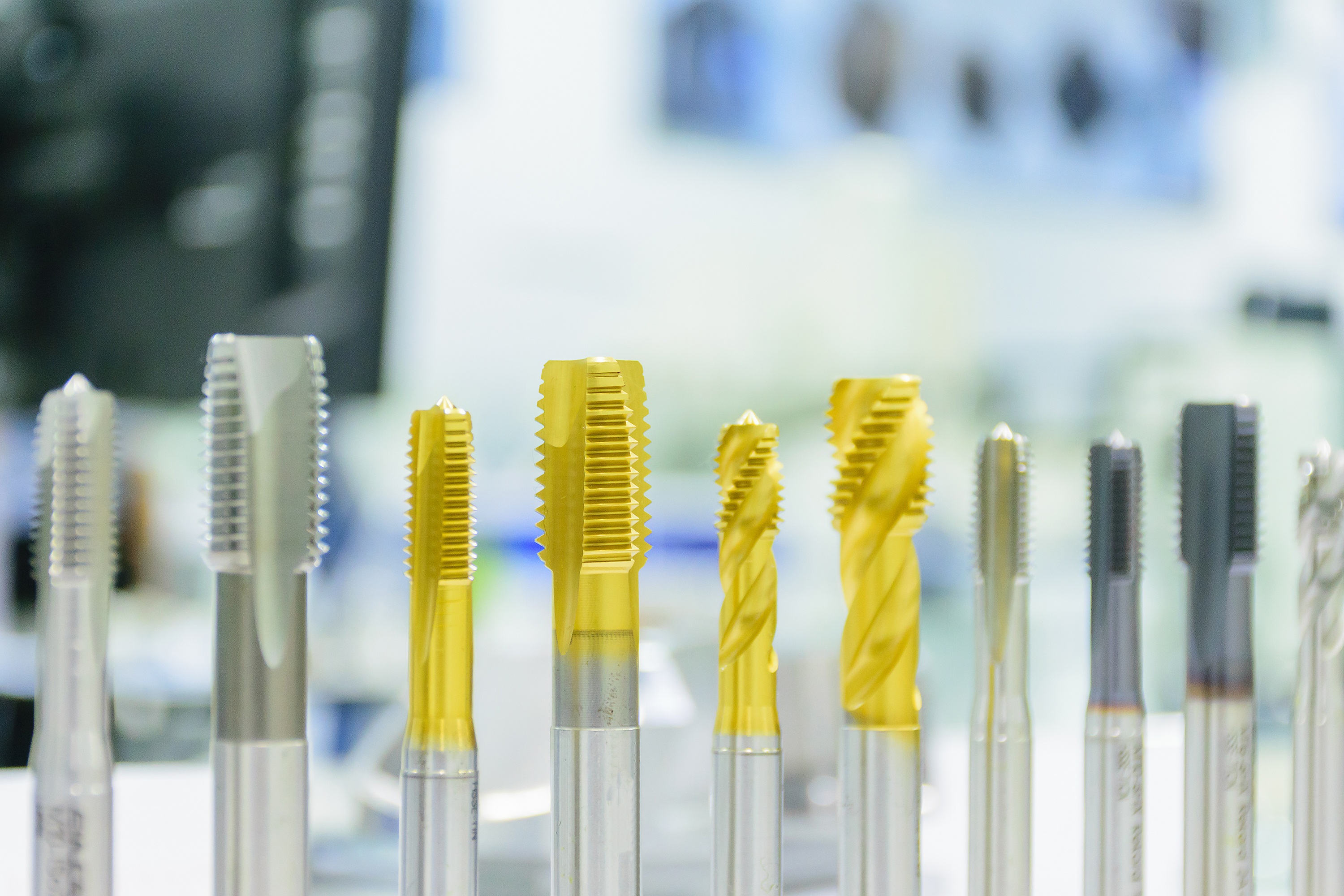
To achieve the precision associated with CNC machining, it’s not enough to just select the right materials, it’s also necessary to excel at machining them.
Given the sensitivity of some plastics to moisture and chemicals, a strategic approach is necessary to maintain the precision and robustness of the machined parts in the injection molding process.
Controlling Heat Generation
Managing heat effectively plays a crucial role in the machining of plastics, where the high coefficient of thermal expansion means even slight temperature changes can lead to significant dimensional shifts and stress cracking. Ensuring heat resistance in the process can help mitigate these issues.
Choosing the right cutting end mills, whether single-flute for low melting point plastics or multi-flute for those with higher heat tolerance, is essential in maintaining the integrity of the workpiece.
Selecting the Right Cutting Tools
The selection of cutting tools depends on the hardness and strength of the plastic, which in turn affect the surface finish and the lifespan of the tool. Selecting tools that match the material’s properties can significantly enhance the quality of the final product.
Ensuring Proper Material Handling
Proper material handling and storage are key to maintaining the excellent dimensional stability and longevity of CNC plastics after machining. Practices such as preconditioning materials like Nylon and ensuring effective heat removal during machining are paramount in preserving the quality of the machined parts.
Customizing Millable Plastics for Specific Applications

The flexibility of millable plastics makes it possible to customize them to meet the specific requirements of various applications. Techniques such as reinforcing with fillers, applying surface treatments, and blending with other polymers can significantly alter and enhance the properties of plastics, making them suited for even the most challenging tasks.
Reinforcing with Fillers
Incorporating fillers such as glass fibers or carbon into millable plastics can result in composite materials with enhanced mechanical properties and thermal stability. This strategy not only improves the plastics’ performance but also offers a cost-effective way to enhance their strength and resistance to wear.
Surface Treatments
Applying surface treatments like vapor polishing and scratch resistance coatings can greatly improve the look and function of millable plastics, as well as improve wear resistance. These treatments can:
Modify the surface energy of plastics
Improve their adhesion
Enhance paintability
Enhance overall performance in their final applications.
Blending with Other Polymers
Mixing various polymers can produce materials with customized properties, from increased toughness to altered thermal behavior. This approach allows manufacturers to engineer plastics that meet specific requirements, whether it’s for automotive, medical, or electronics applications.
Environmental Considerations and Recycling of Millable Plastics
In today’s environmentally conscious world, the sustainability of manufacturing processes and materials is being closely examined. The recycling of millable plastics presents an opportunity to mitigate waste and reduce environmental impact, with processes like mechanical reprocessing and closed-loop recycling that retain the quality of the plastics for future use.
Recycling Millable Plastics
Recycling is not only important from an environmental standpoint but is also a practical necessity, allowing millable plastics to be repurposed without losing their intrinsic properties. Transforming polymers back into their monomer forms or downgrading them into products like plastic lumber extends their lifecycle and reduces ecological footprints.
Eco-Friendly Alternatives
The pursuit of eco-friendly alternatives is significantly influencing the future direction of the plastics industry. Bio-based plastics, derived from renewable sources and often biodegradable, are gaining traction as solutions to reduce pollution and promote sustainable consumption.
Summary
From understanding the intricacies of millable plastics to exploring methods of customization and recycling, this guide has traversed the vast landscape of CNC machining plastics. Embracing the capabilities of these materials is more than a manufacturing decision; it’s a commitment to innovation, efficiency, and sustainability.
Frequently Asked Questions
What plastic is easiest to machine?
The easiest plastics to machine are usually polycarbonate, ABS, polyoxymethylene (POM), and high-density polyethylene due to their flexibility and good machining properties. These materials are commonly used in CNC machining for their ease of manipulation and cost-effectiveness.
What is the best plastic for tight tolerance machining?
Delrin is the best plastic for tight tolerance machining due to its high stiffness and rigidity, making it an excellent choice for CNC plastic machining parts.
What is the best plastic for CNC engraving?
The best plastic for CNC engraving is a harder plastic such as acrylic or ABS. These materials provide more consistent and precise engraving results.
What is the best plastic for milling?
The best plastic materials for milling are Acetal, PEEK, and PVC, as they have superior machining characteristics and offer good dimensional stability. Choose these for optimal milling results.
What are the main benefits of using PEEK in CNC machining?
The main benefits of using PEEK in CNC machining include high mechanical and chemical resistance, making it suitable for demanding applications in aerospace, medical, and automotive industries. Its ability to withstand heavy loads, high temperatures, and harsh chemicals without deforming makes it a valuable material choice.