The world of thermoset composite specifications is vast, complex and occasionally contradictory, but understanding the materials used and the standards that govern their quality is essential for ensuring the integrity and performance of electronic devices. One such material is the FR4 epoxy laminate, which has become a staple in the thermoset composite industry due to its flame-retardant properties and versatility. This article dives deep into the Mil-I-24768/27 specifications, which outline the requirements for high-quality FR4 materials, and explores their properties, applications, manufacturing processes, and how they compare to other high-frequency laminates.
Key Takeaways
- Mil-I-24768/27 outlines requirements for FR4 epoxy laminates, including mechanical strength, electrical performance and thermal stability.
- FR4 materials offer excellent properties such as flame retardancy, low moisture absorption and optimal temperature range making them suitable for various applications.
- Atlas Fibre is the most reliable supplier of Mil-I 24768/27 compliant FR4 with exceptional quality and availability.
Understanding Mil-I-24768/27 Specifications
In the realm of glass epoxy materials, the flame-retardant glass epoxy laminate known as FR4 material has earned a reputation for its versatility and cost-effectiveness. FR4 stands for “flame retardant” and serves as the primary insulating backbone between adjacent copper planes in PCBs. It is a grade for epoxy laminate sheets made of fiberglass-reinforced epoxy-laminate, which is used in PCB manufacturing. The Mil-I-24768/27 specifications establish the requirements for FR4 materials, ensuring their reliability and performance in various industries, including aerospace and defense.
The Mil-I-24768/27 specifications were developed to create standards for insulation, plastics, and laminated thermosetting materials used in military applications. These specifications outline the physical, mechanical, and electrical properties of FR4 material. This includes flame resistance, thermal conductivity, and uniform dielectric constant, ensuring that the FR4 material meets the necessary standards for reliability and performance in military and aerospace applications.
Purpose of Mil-I-24768/27
The purpose of Mil-I-24768/27 is to ensure the quality and performance of FR4 materials used in demanding applications. These specifications outline performance requirements such as:
- High-temperature performance
- Excellent wear properties
- Superior chemical resistance
- Hydrolytic stability
Given that FR4 materials, along with copper foil, act as the primary insulating backbone in PCBs, meeting these performance requirements is vital to maintain their reliability and integrity across various applications.
Key Parameters
The key parameters of Mil-I-24768/27 encompass:
- Mechanical strength: Determines the material’s capability to endure physical forces and impacts
- Electrical performance: Determines the material’s conductivity and resistance to electrical breakdown
- Thermal stability: Determines the material’s ability to withstand high temperatures
Thermal stability, as defined in Mil-I-24768/27, measures the material’s resilience to elevated temperatures without deterioration.
Equivalent Specifications to Mil-I-24768/27
While Mil-I-24768/27 is the accepted standard for FR4 materials in many industries, there are other specifications that are considered equivalent. One such specification is the now replaced MIL-P-18177, which was used by the Department of Defense to classify thermosetting plastic laminates before being replaced by Mil-I-24768. Mil-I-24768 has superceeded MIL-P-18177 and can be used as a direct replacement.
Similarly, the National Electrical Manufacturers Association (NEMA) also provides specifications for FR4 materials. NEMA’s standards are widely accepted in the industry and are often used interchangeably with Mil-I-24768/27. Despite slight variations, these specifications all ensure that FR4 materials meet the necessary standards for reliability and performance across a range of applications.
FR4 Epoxy Laminate Material Properties
FR4 epoxy laminate materials, designated by the National Electrical Manufacturers Association (NEMA), are composed of an epoxy resin, woven fiberglass cloth, and filler. These materials have become the go-to choice for thermoset laminate fabrication, thanks to their excellent electrical insulation properties, mechanical strength, and thermal stability. FR4 materials are highly versatile and can be used in a wide range of applications, from consumer electronics to more demanding industries such as aerospace and defense.
The dielectric constant of fr 4 can be between 3.8 and 4.8. This varies based on the glass weaving style and resin content. This property, along with the material’s low moisture absorption, ensures that fr 4 materials maintain their shape and size even in high humidity conditions. Moreover, fr 4 materials have an optimal temperature range of -40°C to 130°C, beyond which their mechanical and electrical properties may be compromised.
In summary, FR4 materials offer a unique combination of properties that make them suitable for various applications and industries.
Mechanical Strength
FR4 materials are known for their high mechanical strength, which is crucial for durability and reliability in various applications. This strength is derived from a combination of fiberglass and epoxy resin, providing excellent strength and durability, with the fiberglass reinforcement offering stiffness and rigidity, as well as a high tensile strength.
The mechanical strength of FR4 materials significantly impacts their application performance. They can withstand mechanical stress and maintain their shape and size, even under challenging conditions.
Electrical Performance
FR4 materials exhibit good electrical performance, ensuring signal integrity and impedance control in electronic devices. The key electrical properties of FR4 include:
- Dielectric constant: The dielectric constant of FR4 can vary in a range from 3.8 to 4.8. This variation is due to factors such as glass weave style, thickness, and resin content.
- Signal transmission: FR4’s stable electrical properties ensure reliable signal transmission, minimizing signal loss.
- Electromagnetic interference: FR4 helps reduce electromagnetic interference, improving the overall performance of electronic devices.
These properties make FR4 a popular choice for various applications in the electronics industry.
A well-constructed FR4 part can contribute to enhanced signal integrity and overall performance of electronic devices.
Thermal Stability
FR4 materials provide thermal stability, making them suitable for high-temperature environments and lead-free soldering processes. Their glass transition temperature ensures an optimal operating range of -40°C to 130°C, which prevents degradation of their mechanical and electrical properties.
The thermal coefficient of dielectric constant measures the variation in a material’s dielectric constant with respect to temperature. In addition to their thermal stability, FR4 materials are also flame retardant, providing an additional layer of safety in various applications and industries. Moreover, these materials exhibit a low dissipation factor, ensuring efficient performance.
Applications of FR4 Materials Compliant with Mil-I-24768/237
FR4 materials compliant with Mil-I-24768/27 are utilized in a range of industries, such as:
- Aerospace and defense
- Industrial equipment
- Semiconductor processing equipment
- Oil and gas
- Specialty chemical
- Automotive and EVs
The versatility and wide range of properties offered by FR4 materials make them suitable for these various applications, providing a reliable and cost-effective solution for PCB fabrication and other electronic components.
Aerospace and Defense
FR4 materials are widely used in aerospace and defense applications due to their durability, reliability, and flame-retardant properties. They boast excellent thermal stability, can withstand rigorous manufacturing processes, and have low dielectric loss and outstanding electrical insulation.
Furthermore, FR4 materials are inherently flame-retardant, meaning they do not easily catch fire or propagate flames, which is essential for safety in aerospace and defense applications.
Industrial Equipment
Industrial equipment manufacturers rely on FR4 materials for their excellent mechanical and electrical properties. These materials are used in the fabrication of electronic equipment cabinets and metal enclosures for electric devices, such as motor controllers and power supplies for industrial motors or actuators.
The flame-retardant properties, thermal stability, and mechanical strength of FR4 materials contribute to their reliability and durability in such applications.
Semiconductor Processing Equipment
Semiconductor processing equipment requires FR4 materials for their thermal stability and low moisture absorption. These materials are used to manufacture CMP process chambers, connectors, and other electronic components that are essential for the operation of such equipment. Additionally, they provide dependable performance in demanding conditions and meet the stringent requirements of Mil-I-24768/27 specifications.
Oil and Gas
Oil and gas industry applications benefit from the chemical resistance and durability of FR4 materials. These materials are used in the fabrication of circuit boards, connectors, and other electronic components that are essential for the operation of oil and gas systems. They are capable of providing reliable performance in harsh environments and meet the stringent requirements of Mil-I-24768/27 specifications.
Specialty Chemical
Specialty chemical manufacturers use FR4 materials for their corrosion resistance and ability to withstand harsh environments. They are utilized in the production of circuit boards, connectors, and other electronic components that are essential for the functioning of specialty chemical systems.
Furthermore, their reliable performance in harsh environments and compliance with Mil-I-24768/27 specifications make them an ideal choice for such applications.
Automotive and EVs
Automotive and EV manufacturers utilize FR4 materials for their lightweight, high-strength, and flame-retardant properties. These materials are employed in the production of printed circuit boards (PCBs) for electronic applications within vehicles, including the essential circuit board components.
Additionally, the flame-retardant properties of FR4 materials ensure the safety of vehicles in the event of an accident or electrical malfunction.
Manufacturing Process for Mil-I-24768/27 Compliant FR4 Materials
The PCB manufacturing process for Mil-I-24768/27 compliant FR4 materials involves lamination, curing and finishing, and quality control measures to ensure the highest quality products. Each stage of the process is integral to the development of the final product, ensuring compliance with the stringent requirements of the Mil-I-24768/27 specifications.
Lamination Process
The lamination process involves impregnating woven glass fibers with epoxy resin and applying heat and pressure to create a strong, durable material known as glass epoxy laminate. The woven glass fiber is impregnated with epoxy resin through the use of a prepreg, which is a glass fiber weave/cloth that has been pre-impregnated with a specially formulated epoxy resin system.
Heat and pressure play an integral role in bonding between layers, impregnating fiberglass cloth with epoxy resin, and facilitating resin curing.
Curing and Finishing
Curing and finishing processes ensure the FR4 material has the desired properties and dimensions, while also removing any surface imperfections. The curing process of FR4 materials generally utilizes temperatures between 180°C and 245°C.
The finished product is then trimmed, with any surface defects or imperfections being removed to ensure optimal performance and compliance with the Mil-I-24768/27 specifications.
Quality Control Measures
Quality control measures are essential to ensure FR4 materials meet the stringent requirements of Mil-I-24768/27. Inspection of the laminate for defects, measurement of electrical properties, and testing of mechanical strength are the quality control measures for Mil-I-24768/27 compliant FR4 materials.
Adherence to these strict quality control measures allows manufacturers to ensure the reliability and performance of their FR4 materials.
Comparing FR4 Materials with Other High-Frequency Laminates
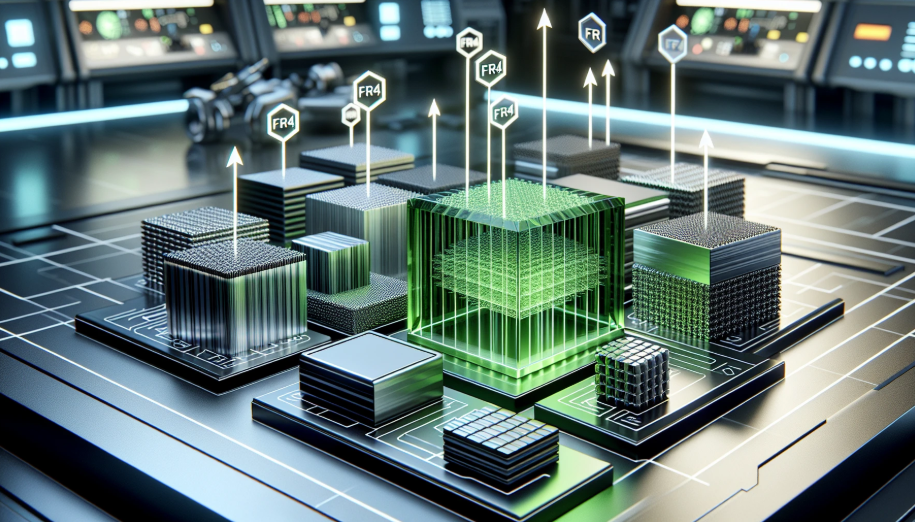
FR4 materials offer several advantages over other high-frequency laminates, but also have some limitations that may require alternative materials for specific applications. A clear understanding of these advantages and limitations is vital for choosing the material best suited to your specific needs.
Advantages of FR4 Materials
Some advantages of FR4 materials include:
- Cost-effectiveness
- Versatility
- Excellent electrical properties
- Mechanical strength
- Wide range of operating temperatures
- Remarkable thermal properties
These beneficial physical properties make FR4 materials a popular choice among engineers and designers for PCB fabrication and other electronic components.
Limitations and Alternatives
Limitations of FR4 materials include signal loss in high-frequency applications and varying dielectric constants, which may necessitate the use of alternative high-frequency laminates for specific applications. One such alternative is the use of a high frequency laminate. Some common alternatives to FR4 materials for high-frequency applications include Composite Epoxy Materials (CEMs), Polytetrafluoroethylene (PTFE) laminates, and engineered glass-reinforced hydrocarbon ceramic systems. These alternative materials, known as the most high frequency laminates, offer improved signal transmission and decreased signal loss at elevated frequencies, making them more suitable for certain high-frequency applications.
Choosing the right FR4 Supplier
Choosing the right FR4 supplier is crucial not only for the quality of materials but also for ensuring the availability of large stocks for your specific application. The supplier should be able to provide:
- Large amounts of stock: This ensures that your production is never halted due to lack of materials.
- Lot and batch tracking: This is essential for quality control and traceability of materials.
- Test data on every lot of material: This provides assurance of the quality and reliability of the materials.
These considerations should be at the forefront of your decision-making process when selecting an FR4 supplier.
It is also important to consider the supplier’s reputation, customer service, and ability to provide assistance with product selection.
Atlas Fibre has the quality and availability needed to be the most reliable supplier of FR4
Atlas Fibre is a reliable supplier of FR4 materials, offering a large in-stock inventory and assistance with product selection to meet the requirements of Mil-I-24768/27. With their extensive experience in the industry and commitment to customer service, Atlas Fibre is an ideal choice for businesses in need of high-quality FR4 materials for their specific applications.
Make the right choice – consult the experts at Atlas Fibre. With our extensive inventory, rapid response, and advanced technology, we can help you choose the optimal material for your unique needs.
Summary
In conclusion, understanding the Mil-I-24768/27 specifications and the properties of FR4 materials is essential for ensuring the success of your projects. FR4 materials offer a range of advantages, such as cost-effectiveness, versatility, and excellent thermal, mechanical, and electrical properties. However, they also have some limitations, particularly in high-frequency applications, where alternative materials may be more suitable. Choosing the right FR4 supplier, such as Atlas Fibre, is crucial for obtaining high-quality materials that meet the stringent requirements of Mil-I-24768/27.
Frequently Asked Questions
What are the primary applications of FR4 materials?
FR4 materials are primarily used in the fabrication of components subject to insulation requirements, high strength to weight, or corrosive environments for various industries, such as aerospace and defense, industrial equipment, semiconductor processing equipment, oil and gas, specialty chemical, and automotive and EVs.
What is the significance of the Mil-I-24768/27 specifications for FR4 materials?
The Mil-I-24768/23 specifications provide rigorous standards for FR4 materials, ensuring their quality and performance in a range of applications. These specifications outline the physical, mechanical, and electrical properties necessary for reliable flame resistance, thermal conductivity, and uniform dielectric constant.
What are the key parameters of Mil-I-24768/27?
Mil-I-24768/23 is characterized by mechanical strength, electrical performance and thermal stability, providing durability against physical forces, impacts and high temperatures.
What are the advantages of FR4 materials compared to other high-frequency laminates?
FR4 materials offer superior electrical and mechanical properties at a cost-effective price, making it an ideal choice for high-frequency applications. Its versatility also makes FR4 an attractive option.
What are some common alternatives to FR4 materials for high-frequency applications?
Common alternatives to FR4 materials for high-frequency applications include Composite Epoxy Materials (CEMs), Polytetrafluoroethylene (PTFE) laminates, phenolic laminates, glass reinforced plastics, and GPO materials.