Maximizing Durability and Efficiency with the Right Temperature-Resistant Materials
Have you ever wondered why some plastics can withstand higher temperatures while others cannot? Or why certain plastics are recommended for specific applications over others? The key lies in the plastics operating temperature of the plastic material.
The operating temperature of a plastic material is a crucial factor that determines its functionality and longevity. It refers to the maximum temperature range within which the plastic can function optimally without degrading or breaking down.
This blog post will delve into the world of plastics and their plastics operating temperatures. We will explore the concept of operating temperature, how it is measured, and the factors that influence it. We will also discuss different types of plastics and their respective plastics operating temperature ranges, as well as provide tips on how to select the right plastic based on its plastics operating temperature. Finally, we will share some real-world examples of successful applications of plastics in various temperature ranges.
Key Takeaways
- The operating temperature of a plastic is critical to its performance and durability, and it is influenced by factors such as the material’s properties, heat exposure, and environmental conditions.
- Testing methods like Maximum Service Temperature, Continuous Use Temperature, and Relative Thermal Index (RTI) are essential in determining the temperature range a plastic can withstand without significant degradation of mechanical or electrical properties.
- There are various plastic materials designed for specific temperature ranges, including low and high operating temperature thermoset composites and extreme temperature plastics, each with unique properties that serve distinct applications.
Understanding Plastics Operating Temperature
For effective use of plastics across various applications, it is imperative to comprehend their operating temperature. The operating temperature refers to the maximum operating temperature range within which the plastic can function without degradation, embrittlement, or breakdown. The performance and longevity of plastic materials are directly influenced by their operating temperature. If a plastic is subjected to temperatures outside of its optimal range, it can experience degradation, increased brittleness, or breakdown, leading to compromised functionality and reduced service life.
The primary factors that contribute to the operating temperature of plastics include material properties such as distortion, softening, expansion, and glass-transition temperature, as well as considerations like service life, melting point, degree of crystallinity, time and rate of temperature exposure, and part geometry.
Defining Operating Temperature
The performance of plastic materials is significantly impacted by the operating temperature. It is defined as the maximum ambient service temperature that a material can endure without experiencing significant degradation or loss of mechanical properties. As the temperature rises, the mobility of the amorphous regions of plastic materials increases, thereby affecting their performance. If plastic materials are utilized beyond their designated temperature range, they may undergo alterations in their characteristics.
For instance, elevated temperatures can cause the amorphous regions of the plastic to become mobile, potentially impacting its strength and flexibility. Conversely, excessively low temperatures can also affect plastic materials. The operating temperature range for plastic materials is determined through rigorous testing and precise measurements. Factors like softening and loss of stiffness are taken into account when establishing the operating temperature range.
Factors Influencing Operating Temperature
Several factors play a role in determining the operating temperature of a plastic material. Some of these factors include:
- Material composition: The composition of the plastic material can have a substantial influence on its operating temperature. Changes can occur due to mobility in amorphous regions at the glass transition.
- Polymer structure: The structure of the polymer also plays a role in determining the continuous use temperature.
- Additives: Additives can either expand the temperature range, enabling plastics to withstand higher temperatures, or make plastics more flexible by reducing the glass transition temperature.
These factors, among others, contribute to the overall operating temperature of a plastic material.
Processing methods, such as melting temperature, melt mold temperature, and other conditions, also play a significant role in influencing the operating temperature of plastics. Additionally, environmental conditions, such as ambient temperature, have a substantial influence on the operating temperature of plastics.
Measuring Plastics Operating Temperature: Test Methods and Standards
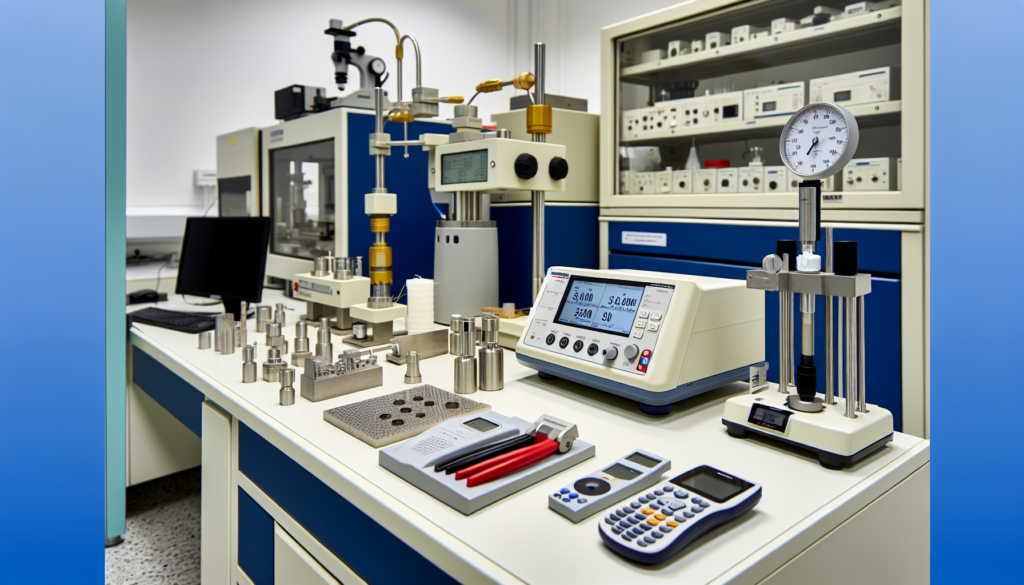
Various methods and standards are used to measure operating temperature. The Maximum Service Temperature refers to the highest temperature at which a material can be utilized without experiencing significant loss of its mechanical or electrical properties throughout the reasonable lifetime of the product. This temperature is determined through continuous use temperature measurement in degrees Celsius or Fahrenheit, in conjunction with references to tables that offer the maximum use temperature for various plastic types.
Continuous Use Temperature, on the other hand, refers to one of the two temperatures at which a plastic material can operate without experiencing changes in its properties, demonstrating its ability to sustain long-term performance under thermal stress. The Relative Thermal Index (RTI) serves as a metric for determining the highest operational temperature, measured in degrees centigrade, for a plastic, ensuring that specific essential properties remain within acceptable limits. This standardized measure facilitates the comparison of heat resistance among various plastic materials.
Maximum Service Temperature
Maximum service temperature is defined as the highest temperature at which a material can be used without significant loss of properties. It is established based on the form of supply according to EN 14706:2005 and EN 14707:2005 + A1:2007. The insulation layer thickness can only decrease by 5% of its original value at its maximum service temperature. This requirement ensures the effectiveness and safety of the insulation. The ASTM D794 test is utilized to ascertain max temperature.
Continuous Use Temperature
In plastics, the continuous use temperature is the point at which the polymer starts to degrade, embrittle, and break down over time. This differs from maximum service temperature, which is the highest temperature at which a material can operate temporarily without significant degradation of mechanical or electrical properties. Techniques used to ascertain the continuous use temperature of plastic include the Relative Thermal Index (RTI) test, UL 746 calculation, and mechanical tests such as Heat Deflection Temperature (HDT) and Vicat softening.
The factors that influence the continuous use temperature include:
- Distortion
- Softening
- Expansion
- Service life
- Thermal properties
- Time and rate of exposure to elevated temperature
- Part geometry
- Glass-transition temperature
- Melting point
- Degree of crystallinity
When subjected to temperatures beyond their continuous use temperature, plastics may undergo a reduction in strength and stiffness, and may exhibit increased brittleness and susceptibility to hardening, particularly in extremely cold environments.
Relative Thermal Index (RTI)
Based on property loss, the Relative Thermal Index (RTI) serves as a comparative measure of a material’s continuous use temperature. The indication provided by this is the temperature at which a material can undergo aging for 100,000 hours. It also ensures that at least half of the initial property being measured is maintained. The RTI is determined by assessing the deterioration of properties in the plastic material as it is subjected to a maximum continuous use temperature over time.
Specifically, the RTI measures the electrical insulation properties of the material. The established industry guidelines for quantifying RTI entail subjecting a material to a sequence of incrementally elevated temperatures and evaluating its electrical insulation properties using a test method.
Common Plastics and Their Operating Temperature Ranges
Operating temperature ranges vary among different types of plastics. For instance, thermoset plastics such as polyurethane, epoxy, and phenolic are known for their ability to withstand high temperatures. In very high temperature applications, materials like polyimides, which can reach up to 550–600 °F, are commonly utilized.
On the other hand, thermoplastics exhibit a broader operating temperature range in comparison to thermoset plastics, allowing them to endure different temperatures within the range of -200°C to +260°C. This provides versatility for utilization across a wider array of applications.
Thermoset Plastics vs Thermoplastics
Significant differences in properties and uses exist between thermoset plastics and thermoplastics. A thermosetting plastic is characterized as a polymer that irreversibly solidifies when subjected to heat. In contrast, a thermoplastic is defined as a type of plastic composed of polymer resins that soften when heated and solidify when cooled.
Thermoset plastics exhibit a higher level of durability at high temperatures due to their inability to be remolded or reheated after the initial forming, thus maintaining their shape.
In contrast, thermoplastics have the capability to be reheated and remolded after the initial forming process. For instance, PTFE (Teflon) has a range from -200°C to +260°C, PE-UHMW can range from -260°C to +80°C, and polycarbonate has an ideal thermoforming temperature range of about 300 to 500°F.
Typically, thermoset materials generally exhibit higher Relative Thermal Index (RTI).
Low Operating Temperature Thermoset Composites
Low operating temperature thermoset composites encompass materials such as CE, G10, and FR4, specifically engineered for use in environments with temperatures typically not exceeding 140°C (284°F).
CE thermoset composites exhibit:
- Low density
- Corrosion and chemical resistance
- Strain and flame resistance
- Good insulating properties
- High strength-to-weight ratio
- High stiffness-to-weight ratio
- Minimal water absorption
- Higher bending and tensile strengths in comparison to epoxy resin.
High Operating Temperature Thermoset Composites
High operating temperature thermoset composites display the following characteristics:
- Good dimensional stability
- Outstanding insulating and electrical properties
- Moisture resistance
- Excellent flammability rating
- UL listed
In particular, G11 thermoset composites demonstrate enhanced mechanical strength at elevated temperatures compared to G10, illustrating their ability to effectively endure high operating environments.
Low-Temperature Plastics
Low-temperature plastics exhibit properties such as thermal expansion rate, resistance to extreme cold temperatures, and a chemical structure that enables them to perform effectively in low-temperature applications. For instance, fluoropolymers, among other low-temperature plastics, are well-suited for static seals at low temperatures due to their entangled long chain molecular structure. Prevalent varieties of low-temperature plastics encompass PTFE, PFA, PVC, PE, and ABS. These materials are recognized for their appropriateness in low-temperature environments.
Low-temperature plastics are favored for applications operating below 150°C due to their ability to:
- Maintain a wide working temperature range
- Withstand extremely high and low temperatures
- Provide resistance to liquid oxygen at temperatures as low as -40°C
These characteristics make them well-suited for a range of applications that encompass both low and high-temperature extremes.
High-Temperature Plastics
High-temperature plastics, such as:
- PEI (Polyetherimide)
- PEEK (Polyether Ether Ketone)
- PTFE (Polytetrafluoroethylene)
- PAI (Polyamide-imide)
- PPS (Polyphenylene Sulfide)
- PBI (Polybenzimidazole)
Exhibit remarkable properties such as heat resistance, superior strength, stiffness, and chemical resistance. These materials are capable of enduring temperatures of up to 300°C, retaining excellent wear resistance, remaining unaltered by chemicals and radiation, and are particularly suitable for challenging environments. Ultem is an alternative designation for Polyetherimide.
High-temperature plastics are frequently utilized in various applications, including:
- Metal replacement
- Medical implants
- Electric Vehicle (EV) batteries
- Automotive industry
- Aerospace industry
- Electrical industry
- Medical industry
- Mechanical engineering sector
- Oil and gas sector
Extreme Temperature Plastics
Extreme temperature plastics exhibit characteristics such as high heat resistance, high strength, stiffness, and chemical resistance, which render them suitable for high-temperature applications. Plastics designed for temperatures above 300°C include Polyetherimide (PEI), Polyether Ether Ketone (PEEK), Polyamide-imide (PAI), Polytetrafluoroethylene (PTFE), Polyphenylene Sulfide (PPS), and Polybenzimidazole (PBI).
Extreme temperature plastics are considered suitable for applications above 300°C due to their engineered ability to maintain properties at such high temperatures, which is crucial for specific industrial and technological applications.
Tips for Selecting the Right Plastic Based on Operating Temperature
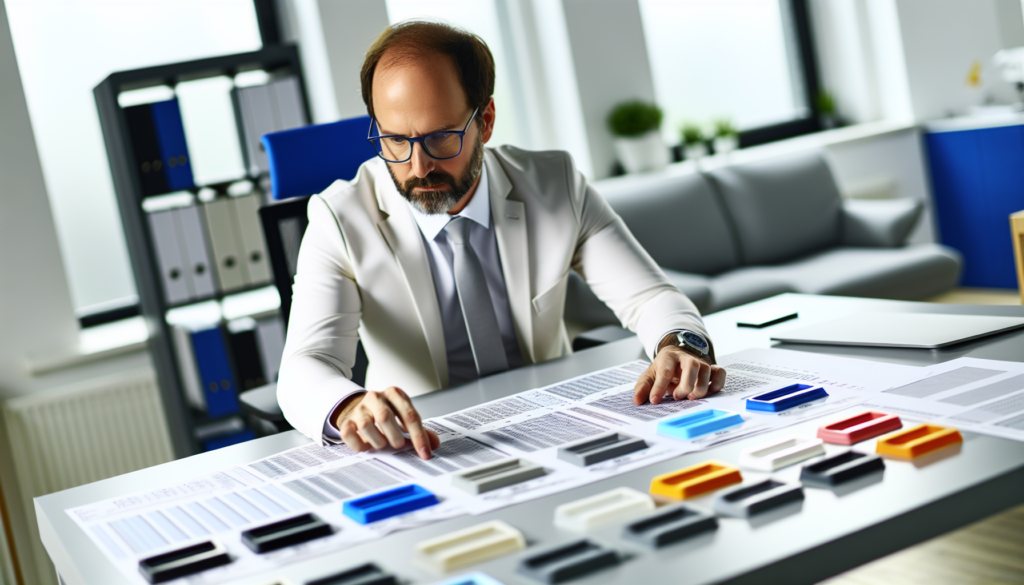
To ensure optimal performance and longevity, it’s essential to select the right plastic material based on its operating temperature. It involves assessing the application requirements, balancing the performance and cost, and considering the environmental factors. The selection of plastics for different applications is influenced by the operating temperature. High heat levels can have notable effects on thermoplastics, while excessively low temperatures can also impact their performance.
Some high-temperature plastic materials that are cost-effective include:
- Polybenzimidazole (PBI)
- Ultem (Polyetherimide)
- PEI
- PEEK
- PTFE
- PAI
- PPS
The price of plastic materials may fluctuate based on raw material costs and market demand.
Key environmental considerations that should be taken into account when selecting plastic materials include the efficiency of recycling infrastructure, the sustainability of materials, and the potential for using recycled plastics.
Assessing Application Requirements
Assessing the application requirements is a crucial step in selecting a plastic material. This includes determining:
- The temperature range suitable for the application
- The mechanical specifications needed for the plastic material
- The impact of electrical properties on selection
As each application has its unique requirements, the chosen plastic material should be capable of meeting these requirements effectively.
For instance, robust engineering plastics with elevated impact and tensile strength are appropriate for industrial cams, gears, and couplings. It is crucial to choose plastics with the requisite thermal properties, strength, and chemical resistance to prevent component failure. Furthermore, the electrical properties of plastics, including electrical conductivity and insulating properties, play a significant role in the selection process based on operating temperature.
Balancing Performance and Cost
Another critical aspect of selecting the right plastic material is balancing performance with cost. While high-performance plastics typically command a higher price due to their elevated specifications and the necessity for specialized manufacturing processes, there are cost-effective substitutes available. These substitutes include:
- High-Density Polyethylene (HDPE)
- Chlorotrifluoroethylene (E-CTFE)
- Bioplastics derived from cornstarch, sugarcane, or cellulose
- Materials such as bamboo, hemp, and mushroom-based materials
Additionally, polypropylene and ASA are viable alternatives for specific applications.
Considering Environmental Factors
When choosing a plastic material, one should also consider environmental factors like humidity, UV exposure and chemical resistance. Humidity can have various effects on the operating temperature of plastics. Elevated humidity levels can result in the absorption of moisture by plastics, leading to dimensional changes and material expansion. Additionally, the absorbed moisture can function as a plasticizer, lowering the plastic’s glass transition temperature and strength.
UV exposure can potentially lead to the deterioration of plastics, which is a significant consideration in conjunction with factors like heat. Plastics, which are commonly considered chemically inert, have the potential to emit volatile organic compounds (VOCs) into their surroundings and are susceptible to thermal degradation when exposed to elevated temperatures for prolonged periods.
Case Studies: Successful Applications of Plastics in Various Temperature Ranges
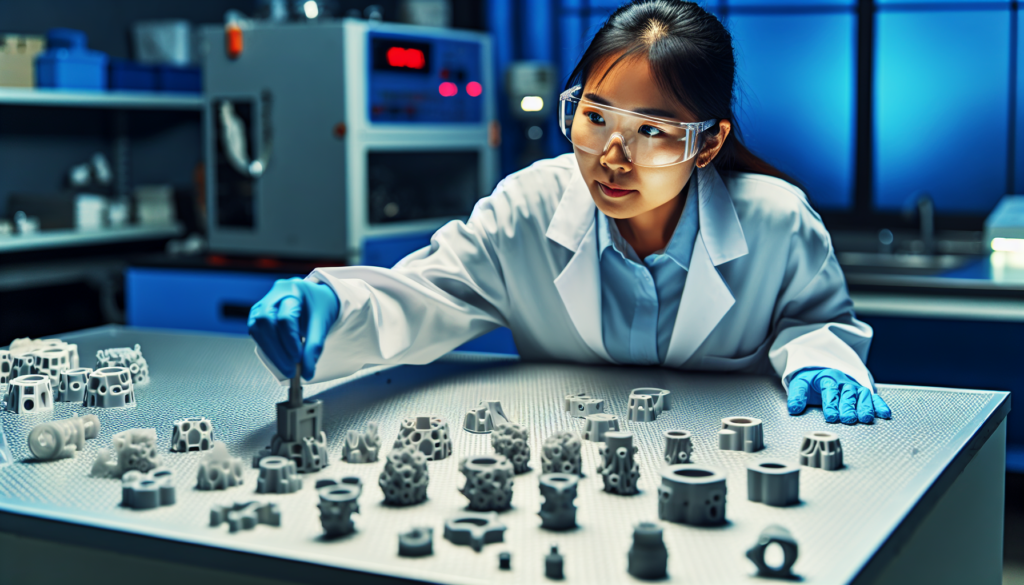
Practical insights into the utilization of plastics with different operating temperatures in various applications can be gained through real-world examples. These examples include:
- The use of low-temperature plastics in insulation boxes
- High-temperature plastics in automotive components
- Extreme temperature plastics in aerospace materials
Low-Temperature Application: Insulation Boxes
Low-temperature plastics like Polyethylene Terephthalate (PET or PETE), Polystyrene (PS), and ABS (Acrylonitrile Butadiene Styrene) are frequently utilized in the production of insulation boxes. These plastics guarantee effective thermal protection by significantly reducing heat flow, thereby minimizing the loss of heat from the packaged product.
Certain specific grades or types of low-temperature plastics recommended for use in insulation boxes include:
- PTFE
- PFA
- PVC
- PE
- ABS
Low-temperature plastic insulation boxes have been effectively utilized in a range of applications, including:
- maintaining consistent temperatures for food and beverages
- repurposing waste items for home insulation
- operating efficiently in industrial settings with temperatures as low as -200°C.
High-Temperature Application: Automotive Components
High-temperature plastics, such as polyurethane and polycarbonate, are employed in automotive applications such as gears and hot fuel systems because of their exceptional heat-resistant properties, which enable them to withstand the high temperatures commonly found in engine environments. Prevalent high-temperature plastics used in automotive components encompass:
- Polyvinyl chloride (PVC)
- Polypropylene (PP)
- Polycarbonate
- ABS
Furthermore, materials like PPS and PEEK are engineered to endure high engine temperatures, with PPS capable of withstanding temperatures up to 424°F and PEEK managing short-term exposure to temperatures as high as 310°C. Automotive components that are manufactured using high-temperature plastics encompass gears, hot fuel systems, intake manifolds, valve covers, and plastic fuel tanks.
Extreme Temperature Application: Aerospace Materials
Extreme temperature plastics are extensively used in aerospace materials for various applications. Some commonly used high-temperature plastics in aerospace materials include:
- Polyetherimide (PEI)
- Ultem®
- Radel® R
- PEEK
- DuPont™ Vespel®
- KYNAR
- PVDF
- G11
These plastics are chosen for their ability to maintain mechanical properties at elevated temperatures, provide high-temperature insulation for sensitive components, and resist degradation.
For instance, PEI is used for components like air and fuel valves, food tray containers, and interior parts, while the others serve in roles such as semi-structural components due to their lightweight and high-temperature resistance in aerospace and defense applications. The utilization of extreme temperature plastics, such as PEEK, in aerospace applications presents challenges in terms of cost and the sensitivity of aerospace components to extreme temperatures, humidity, vibration, and shock.
Summary
Selecting the right plastic material based on its operating temperature is crucial for ensuring optimal performance and longevity. Throughout this blog post, we’ve delved into the world of plastics and their operating temperatures. We’ve explored the concept of operating temperature, how it is measured, and the factors that influence it. We’ve also discussed different types of plastics and their respective operating temperature ranges, as well as provided tips on how to select the right plastic based on its operating temperature.
By understanding these concepts and applying them in your selection process, you can ensure that you choose the right plastic material that can withstand the operating temperature of your specific application. Whether you’re working with insulation boxes, automotive components, or aerospace materials, selecting the right plastic material can significantly impact the performance, efficiency, and longevity of your application.
Frequently Asked Questions
What temperature can plastic withstand?
Plastic can withstand a range of temperatures, but it typically has a melting point of 70°C (158°F) to over 200°C (392°F), with some types like polyethylene melting at 105°C to 135°C (221°F to 275°F).
Does plastic melt at 140 degrees?
Some common plastics like polyethylene and polypropylene can melt at around 130 to 140 degrees Celsius. Different types of plastic may have different melting points.
What is the difference between thermoset plastics and thermoplastics?
Thermoset plastics solidify irreversibly when heated, while thermoplastics soften when heated and solidify when cooled. This allows thermoplastics to be reshaped multiple times, while thermoset plastics cannot be reshaped.
What factors should be considered when selecting a plastic material based on its operating temperature?
When selecting a plastic material based on its operating temperature, consider factors such as specific needs, performance requirements, production and disposal costs, environmental impact, as well as strength, durability, flexibility, and temperature resistance. These factors are crucial for making the right decision.
What are some examples of high-temperature plastics and their applications?
High-temperature plastics such as PEI, PEEK, PTFE, PAI, PPS, and Ultem are commonly used in various industries like automotive, aerospace, electrical, and medical for applications requiring resistance to high temperatures, including metal replacement and medical implants.