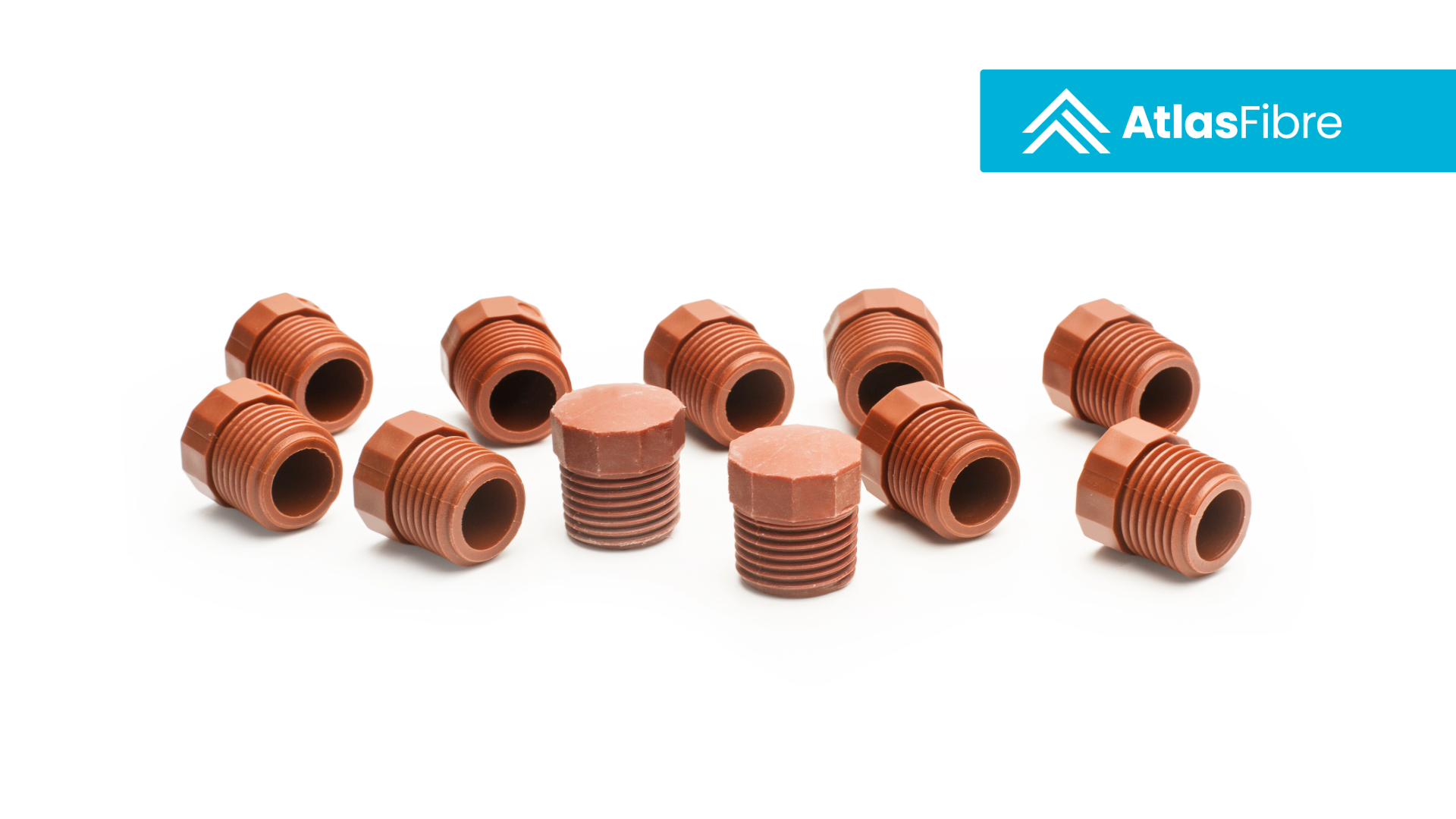
When it comes to sleeve bearings, durability is key.
Traditional materials can wear out quickly under extreme conditions, leading to costly downtime and repairs. Thermoset composite laminate materials offer a superior alternative, providing exceptional strength, wear resistance, and long-lasting performance. Discover why these advanced composites are the ideal choice for sleeve bearings in challenging markets and demanding applications.
Key Takeaways
- Composite sleeve bearings are known for their high load capacity, making them suitable for heavy-duty applications.
- Thermoset composites, such as cotton phenolic, can withstand much higher loads than many thermoplastic materials.
- Thermoset composite materials are a reliable choice for sleeve bearings in a wide range of applications, offering advantages in terms of load-bearing capacity, durability, and thermal insulation.
What is a Sleeve Bearing?
An Introduction to Sleeve Bearings
A sleeve bearing, also known as a bushing or plain bearing, is a type of bearing that facilitates linear or rotational movement between two parts. It consists of a metal, plastic, or fiber-reinforced composite sleeve that reduces vibrations and noise by absorbing friction between two moving parts using a sliding motion. Various industries use sleeve bearings for their lower cost, minimal maintenance, reduced noise at low speeds, and easier installation. Companies particularly value these bearings for their simplicity and effectiveness in applications where high precision isn’t critical but reliability and durability are essential.
Basic Functionality and Design
The basic functionality of a sleeve bearing is to reduce friction between metal components through the lubricating material on the sliding surface. The design of a sleeve bearing typically consists of a cylindrical or flanged sleeve with a smooth inner surface that allows for linear or rotational movement. Manufacturers typically make the sleeve from durable materials like bronze, steel, or stainless steel, and they may add lubricant plugs or oil-impregnate it to reduce friction and wear. This design ensures that the bearing can handle radial loads effectively while providing a stable and smooth operation. The simplicity of a plain bearing design makes it a versatile choice for various applications, from industrial machinery to automotive components.
Why Thermoset Composite Materials Are an Ideal Choice for Sleeve Bearings
Composite sleeve bearings, also known as bushings, plain bushings, or journal bearings, offer an efficient and reliable solution for high-load, low-friction applications. Composite sleeve bearings offer high load capacity, making them suitable for heavy-duty applications.. Their unique properties make them a superior choice compared to traditional thermoplastic bearings, especially when it comes to demanding environments that require high compressive strength and low creep.
Unlike ball bearings or roller bearings that rely on rolling action, sleeve bearings function with a sliding linear or rotational movement. This difference in motion provides unique advantages, particularly when used in high-load or high-stress applications. Additionally, you can lubricate thermoset composite sleeve bearings with materials such as oil, self-lubricating additives, or even water to ensure smooth and continuous operation.
Superior Radial Load-Bearing Capabilities
Engineers choose thermoset composites for sleeve bearings primarily for their superior load-bearing capacity. Thermoset composites, such as cotton phenolic, can withstand much higher loads than many thermoplastic materials.
For example, in marine applications, cotton phenolic composite tubes can serve as an alternative to marine brass sleeved shaft stern bearings. These composite bearings offer excellent durability while maintaining cost-effectiveness.
A Sleeve Bearing Tailored for Application-Specific Requirements
Every sleeve bearing application is unique and requires careful consideration of several key factors. For optimal performance, sleeve bearings are often paired with hard steel shafts, which enhance their durability and load-bearing capabilities.
Here are some important engineering considerations for ensuring an optimal fit for sleeve bearings:
Running Clearance
Running clearance refers to the space between the shaft and the bearing. It’s essential to maintain the appropriate clearance to ensure smooth operation. A recommended guideline is 0.001” of clearance per inch of shaft diameter, with a base minimum of 0.005”. For example, a shaft with a diameter of 5.000” would require a clearance of 0.010” (5.000 * 0.001 + 0.005 = 0.010). Therefore, the bearing should have an internal diameter (ID) of 5.010” for optimal performance.
Journal Bearing Swelling Allowance
Thermoset composites may experience some swelling due to environmental factors such as moisture or temperature changes. An additional allowance for radial swelling should be made at a rate of 0.010” per inch of the bearing wall thickness. For instance, if the inner diameter of your shaft is 5.010” and the casing diameter is 5.500”, the swelling allowance would be approximately 0.003”. This should be factored into the bearing’s outer diameter (OD), meaning the bearing should have an OD of 5.497”.
Longitudinal Growth Allowance
In cases where the sleeve bearing is tightly enclosed on both ends, it’s important to account for longitudinal growth, which may occur as the bearing expands. For such applications, an allowance of 0.005” per inch of captured bearing length should be made. For example, if the bearing enclosure is 6.575” long, a longitudinal growth allowance of 0.033” should be factored in. Therefore, the bearing should have a length of 6.542” (6.575 – 0.033 = 6.542).
Thermal Management and Self Lubricating Sleeve Bearings
Thermoset composite sleeve bearings also provide excellent thermal insulation, which can be a valuable asset in high-heat environments. Thrust washer designs are also crucial in managing axial and radial loads, ensuring the bearing’s stability and performance. However, to ensure optimal bearing life and performance, it’s important to manage temperature effectively. Flowing lubricating oil or water through the bearing can help cool it down, minimizing heat-related expansion and ensuring the bearing maintains its hardness. Cooled bearings will perform better and have a significantly extended lifespan. Custom materials can also be manufactured to support the development of components like self lubricating sleeve bearings.
Choose Innovative Material for Dynamic Parts
Thermoset composite materials are a reliable choice for sleeve bearings in a wide range of applications, offering advantages in terms of load-bearing capacity, durability, and thermal insulation. By carefully engineering running clearance, swelling allowance, and longitudinal growth, these bearings can be customized to meet the specific needs of high-load applications. Their ability to be lubricated with oil, additives, or water further extends their versatility, ensuring smooth, reliable performance even in challenging environments. Whether for marine use or industrial equipment, composite sleeve bearings are a durable and cost-effective option worth considering.
Self-Lubricating Sleeve Bearings: A Special Case
Self-lubricating sleeve bearings are a special type of sleeve bearing that contains a compound layer that ensures smooth operation and extends the service life of the bearing. These bearings are designed to operate maintenance-free for extended periods and are ideal for applications where external lubrication is not feasible. The self-lubricating feature is particularly beneficial in environments where regular maintenance is challenging or where contamination from lubricants must be avoided. By incorporating materials that release lubricants over time, these bearings maintain low friction and wear, ensuring consistent performance and reliability.
Advantages of Self-Lubricating Composites
Self-lubricating composites used in sleeve bearings offer several advantages, including:
- Reduced Friction and Wear: The self-lubricating layer minimizes friction between moving parts, reducing wear and extending the bearing’s lifespan.
- Increased Load Capacity and Shock Load Resistance: These bearings can handle higher loads and absorb shocks better than traditional bearings, making them suitable for heavy-duty applications.
- Improved Corrosion Resistance and Electrical Conductivity: The materials used in self-lubricating composites are often resistant to corrosion and can provide electrical insulation, enhancing their durability in harsh environments.
- Thin Wall Design Options for Compact Applications: The ability to design bearings with thin walls allows for use in compact spaces without compromising performance.
- Misalignment Compensation and Vibration Damping: Self-lubricating bearings can accommodate slight misalignments and dampen vibrations, improving overall system stability.
- Consistent Coefficient of Friction and Reduced Noise, Vibration, and Harshness (NVH): These bearings maintain a consistent coefficient of friction, reducing noise and vibration, which is crucial for applications requiring quiet operation.
These advantages make self-lubricating sleeve bearings an ideal choice for a wide range of industrial applications, including automotive, manufacturing machinery, and appliances. Their ability to operate without external lubrication and their enhanced performance characteristics ensure they meet the demands of modern engineering challenges.