Thermosets are special materials that stay strong in extreme environments. Examples of these materials, also known as thermosetting plastics or thermosetting polymers, include epoxy, polyurethane, phenolics, and amino resins. Thermosets are made through a curing process that hardens the material into a durable form that remains set, even when heat is reapplied. Their ability to resist heat and cold makes them essential for keeping things working well in all kinds of weather conditions, especially airplanes, cars, and electronics.
If your business is seeking a durable and cost-effective material alternative, this complete guide will help you better understand what happens to thermosetting plastic when cooled or heated.
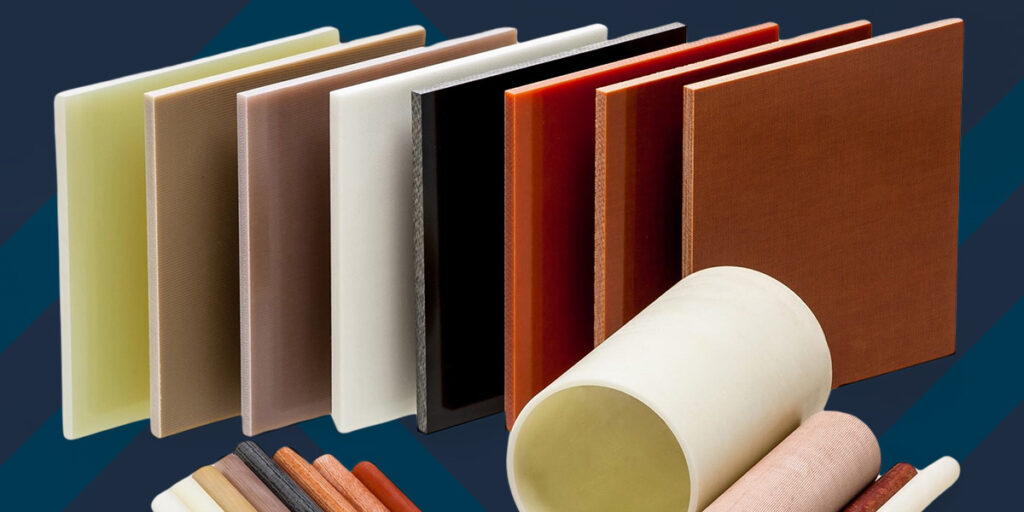
Properties of Thermosets
What happens to thermosets when heated during the curing process is they undergo a chemical reaction called cross-linking. This cross-linking creates a network of strong chemical bonds that give thermosets their characteristic stability. That’s why thermosets can withstand heat better than thermoplastics and are used in a wide range of industries.
The properties of thermoset composites that make them valuable include:
- Heat resistant: Depending on the material, thermosets can withstand temperatures up to 428 degrees Fahrenheit (220 degrees Celsius) without deforming. Additionally, thermosetting polymers don’t melt, making them ideal for applications where heat resistance is crucial.
- Chemical resistant: They are resistant to many chemicals and contain no metals, making them suitable for harsh environments where exposure to corrosive substances happens often.
- Flame resistant: Some thermoset composites are formulated to be resistant to flames as well as heat and chemicals. They help slow the spread of fire.
- Dimensional stability: Thermosets maintain their shape and size even when exposed to temperature fluctuations, ensuring structural integrity over time.
- Durability: Due to the interlinking molecular structure and chemical compositions, most thermoset composites are durable and lightweight with a high strength-to-weight ratio.
- UV resistant: Thermosets are ideal for applications exposed to the elements, including UV light. Their UV resistance helps ensure color fastness and integrity while withstanding significant wear and tear.
- Non-magnetic: Because thermosets lack metal, they’re safe to use around magnetic and sensitive electronic equipment without interfering with radio or microwave transmissions.
- Low water absorption: Thermoset materials used in wet and humid environments provide great insulation and high mechanical strength as they absorb no water.
Benefits of Thermosets
Thermosets overcome many limitations of other polymer plastics and materials, which is why they’re a commonly used alternative material. These are some examples of thermosets’ advantages:
- Economical: Due to simpler processing techniques, thermoset parts provide a cost-effective material option for many industries. They can be formulated into various colors, reducing the need for painting or protective coating for aesthetics.
- Longer life span: With a higher resistance to heat, chemicals, steam, and corrosion, thermoset products have a long life span, reducing replacement and maintenance costs.
- Minimal deformation: Their structural integrity and mechanical strength make thermosets resistant to deformation, so they’re often used for sealed goods.
- Design flexibility: Thermoset composites can be fabricated into several shapes with thin or thick-walled designs for improved structural integrity. After formation, the strong chemical bonds ensure they retain their shape.
- Energy efficiency: Due to their excellent dielectric strength and low thermal conductivity (check the thermal conductivity of popular composites), thermosets can contribute to energy savings in various applications.
- Aesthetics: In-mold painting (IMP) with thermosets offers high-quality finishes with excellent adhesion and resistance to chipping or cracking.
Thermosets vs. Thermoplastics
Thermosets and thermoplastics are two main types of polymers with distinct characteristics. The main difference between the two is how they react to heat. Thermosets undergo irreversible chemical changes when heated, while thermoplastics can be reshaped due to reversible physical changes. This makes thermoplastics better for applications needing more flexibility in shaping, while thermosets offer heat resistance and durability.
Here are other differences between thermosets and thermoplastics:
- Material behavior: Thermosets solidify upon heating, while thermoplastics soften into a liquid form that can be remolded.
- Strength: Although thermoplastics offer the versatility of remolding, thermosets are stronger, more heat-resistant, and rigid.
- Chemical composition: Thermoplastic polymers consist of molecules that can be rearranged repeatedly, while thermosets form a cross-linked networking during curing.
- Applications: Thermoplastics like polyethylene, polypropylene, and PVC are suitable for mild environments. Conversely, thermosets are preferred for high-temperature and durable applications.
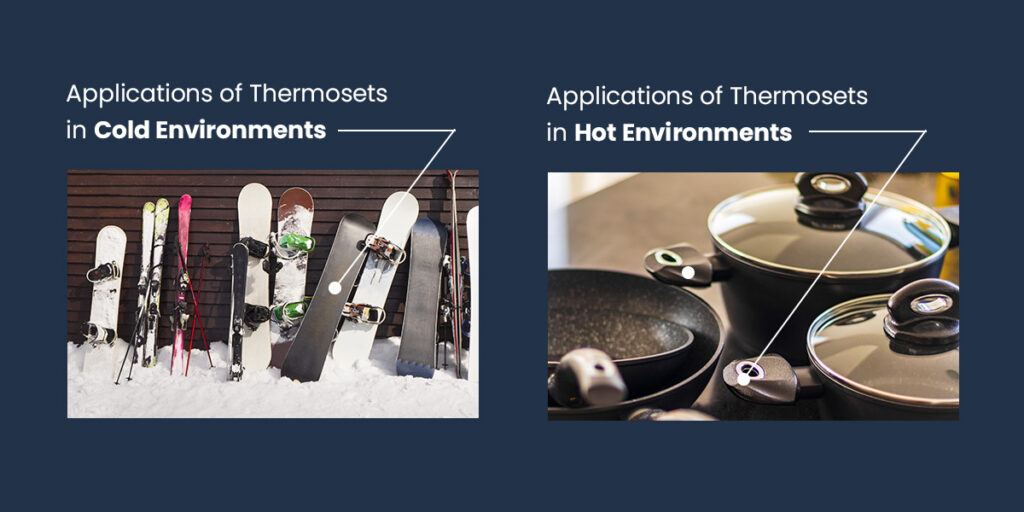
Applications of Thermosets in Cold Environments
Thermosets are cold-resistant due to their ability to maintain strength and durability without compromising performance. In these applications, thermoset parts are used to withstand cold environments:
- Aerospace industry: Thermoset materials are used in aircraft components that must withstand low temperatures at high altitudes.
- Cold storage facilities: Insulation panels and containers made of thermosets maintain low temperatures and prevent heat transfer.
- Automotive industry: A few parts, such as bumpers and exterior trims, use thermosets because they are resilient to cold and wet conditions.
- Arctic exploration equipment: Thermoset materials play an important role in equipment used in arctic environments.
- Electrical applications: Thermosets provide great electrical insulation properties to cables in cold environments where stable electrical performance is essential.
- Medical equipment: Some medical devices and equipment require reliability and stability in freezing temperatures.
- Outdoor sporting equipment: Products like skis, snowboards, and winter gear benefit from thermoset materials’ ability to withstand cold temperatures.
- Cryogenics: Cryogenic equipment experiences prolonged exposure to extreme cold, so they need insulation and protection.
Applications of Thermosets in Hot Environments
Applications of thermosets in hot environments include:
- Automotive industry: Thermoset materials are used in under-the-hood components, such as intake manifolds and valve covers, that are exposed to high temperatures from the engine.
- Oil and gas industry: Thermosets appear in pipelines, valves, and offshore structures that endure high temperatures and pressure in oil and gas processing.
- Electronics industry: Electronic components, like circuit boards and LED lighting, generate heat and, therefore, need thermal stability and protection that thermosets can provide.
- Household appliances: Ovens, cookware, and other heat-exposed appliances benefit from the heat resistance and durability of thermoset materials.
- Industrial machinery: Machine components exposed to high temperatures in manufacturing processes, such as molds and tooling, require durable materials such as thermosets.
- Renewable energy sector: Thermoset materials are applied in solar panels, wind turbine components, and geothermal systems that operate in high-temperature environments.
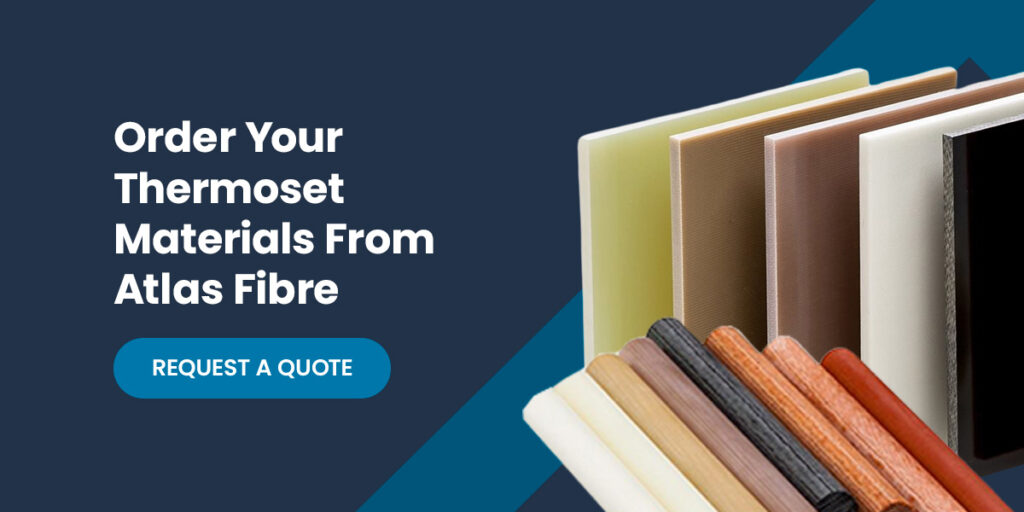
Order Your Thermoset Materials From Atlas Fibre
Compared to thermoplastics and metals, thermoset materials have longer life spans and are an energy-efficient and cost-effective alternative. They’re a reliable solution for many environmental conditions, especially extreme temperatures; humid and wet areas; and corrosive environments. These unique properties make thermosets suitable for a wide range of industries.
Atlas Fibre provides thermoset composite materials for various markets. Whether you need sheets, rods, tubes, precision blanks, or fabricated parts, our team can provide the material or help you with fabrication and assembly services.
Get a fast and free quote on your custom parts. If you have questions about what materials are right for your organization, get in touch with us today. We look forward to connecting with you.