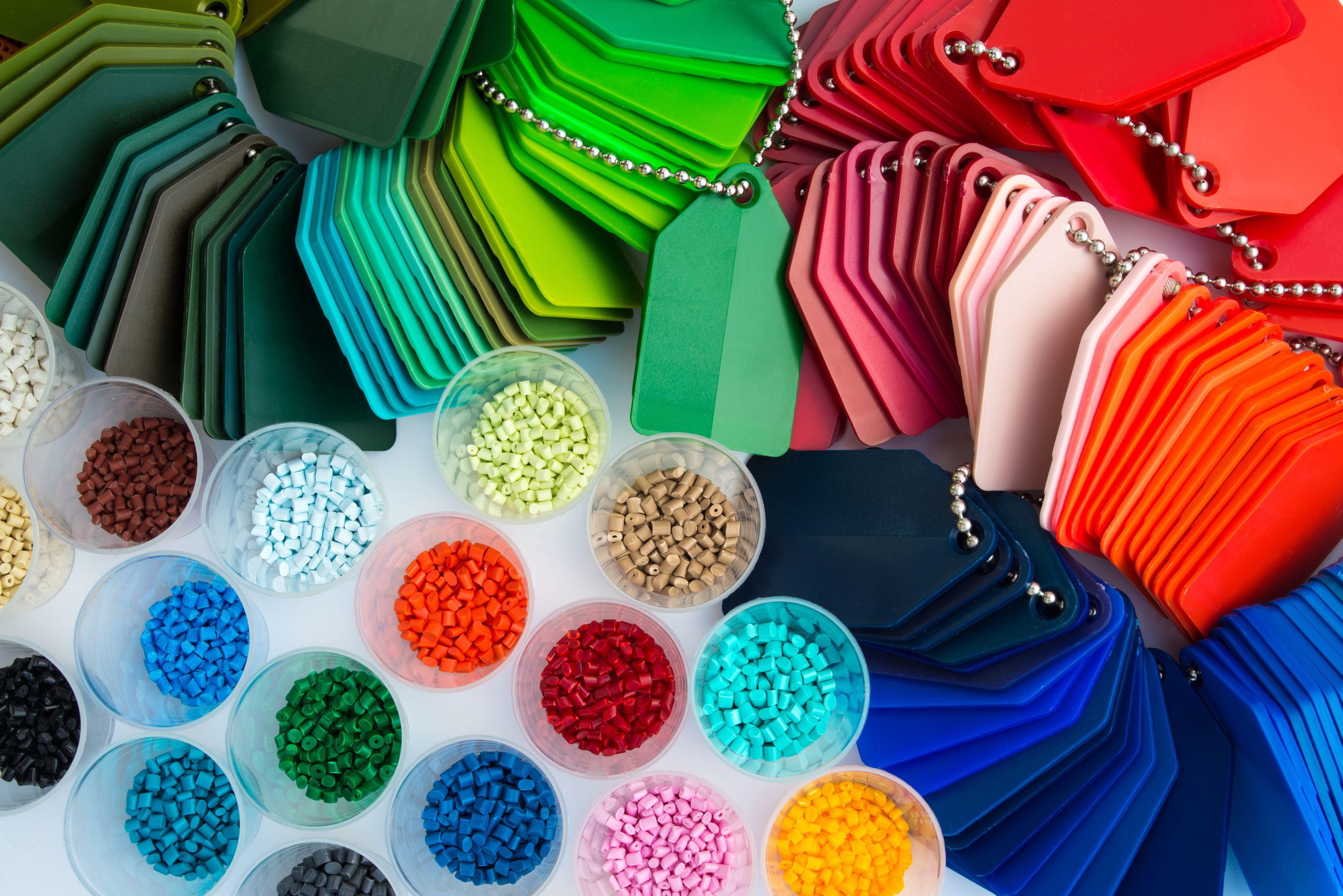
In the dynamic world of plastics, two classes of polymers dominate the landscape: thermoset plastics and thermoplastic materials. While they may seem similar at first glance, their differences in material properties are crucial, especially when considering their applications in various industries. Discover the key distinctions between these two types of polymers and explore their uses across different sectors.
Thermoset vs. Thermoplastic: What’s the Difference?
The primary difference between thermosetting plastics and thermoplastic materials lies in their behavior when exposed to heat. This behavior is dictated by their chemical structures, which influence how they are processed, utilized, and even recycled.
Thermosetting plastics are polymers that form irreversible chemical bonds during the curing process. Thermosetting resins undergo a chemical reaction that results in a phase change to a solid form, which is essential for the cross-linking process that strengthens the material. This process results in a three-dimensional network of bonded molecules, creating strong covalent bonds between polymer chains. Once cured, thermosetting polymers cannot be remelted or reshaped, making them highly stable under high temperatures and resistant to deformation. This cross-linking provides thermoset plastics with high strength, rigidity, and exceptional resistance to heat and chemicals, making them ideal for use in extreme temperature environments.
In contrast, thermoplastic materials consist of linear or slightly branched polymers without permanent cross-links. Thermoplastics transition from a solid state at room temperature to a soft and eventually fluid state when heated, a process known as the glass transition temperature. This lack of cross-linking allows thermoplastics to be reheated, melted, and reshaped multiple times without altering their chemical structure. This adaptability allows thermoplastics to be molded into the desired shape through techniques like compression or injection molding and extrusion. Thermoplastic materials are generally more flexible and impact-resistant than thermoset plastics, making them suitable for a wide range of applications.
The Characteristics and Applications of Thermosetting Plastics and Their Curing Process
Due to their high strength, thermal stability, and chemical resistance, thermosetting plastics are typically used in demanding applications where durability is critical. Thermoset materials are known for their high strength, thermal stability, and chemical resistance. Here are some of the primary industries and applications where thermosetting polymers are the material of choice:
Automotive and Transportation: Thermosetting plastics are utilized in air intake manifolds, disc brake pistons, and various panels in vehicles and heavy machinery. Thermoset polymers are utilized in air intake manifolds, disc brake pistons, and various panels in vehicles and heavy machinery. Their durability and ability to maintain structural integrity at elevated temperatures ensure they can withstand the stresses of automotive environments.
Electrical and Electronics: Due to their excellent insulating properties and resistance to high temperatures, thermosetting polymers are commonly used in electrical housings, components, and insulators.
Construction: Thermosetting plastics find their place in adhesives, sealants, and insulation materials. They are also used in panels and housings for construction equipment, offering long-lasting performance even under extreme temperatures.
Aerospace and Defense: Thermosetting plastics are integral to components that must endure extreme conditions, making them vital in the aerospace and defense sectors where high temperature resistance is essential. Their durability and ability to maintain structural integrity at elevated temperatures ensure they can withstand high temperatures and the stresses of automotive environments.
Chemical Processing: In the chemical processing industry, thermosetting polymers are preferred for pipes, fittings, and cell covers due to their outstanding resistance to corrosive substances and their ability to perform under high temperature conditions.
The Characteristics and Applications of Thermoplastic Materials
Thermoplastic materials are known for their versatility, ease of processing, and recyclability. Thermoplastic resins are unprocessed polymer-based materials derived from petroleum byproducts. These characteristics make them ideal for various applications across numerous industries:
Packaging: Thermoplastic materials are commonly found in food and beverage packaging, thanks to their flexibility and the ease with which they can be molded. Injection molding is a common technique used to shape thermoplastic materials into various forms for packaging.
Consumer Goods: From toys to lamps and office supplies, thermoplastic materials are integral to many everyday items due to their ability to be easily reshaped and their attractive finishes.
Automotive: Thermoplastic materials provide lightweight alternatives to metals in vehicles, such as in gas tanks and piping systems, contributing to improved fuel efficiency and adaptability under high temperature conditions.
Medical and Biomedical: The chemical resistance and sterilizability of thermoplastic materials make them suitable for medical equipment and laboratory tools.
Construction and Plumbing: Thermoplastic materials are extensively used in piping systems and insulation materials due to their resistance to corrosion, ease of installation, and ability to withstand a wide range of temperatures. The molding process allows thermoplastic materials to be shaped into pipes and insulation materials, providing resistance to corrosion and ease of installation.
Choosing the Right Polymer for the Job
Understanding Material Properties
Both thermosetting plastics and thermoplastic materials offer unique advantages depending on the application. The manufacturing process for each type of polymer involves different techniques and considerations, such as tooling, production time, and material choice. Thermosetting plastics excel in environments where durability, stability under extreme temperatures, and chemical resistance are paramount. Thermoset injection molding is used for applications requiring durability under high temperatures, such as in various consumer goods and industrial applications. Thermoplastic materials, on the other hand, are favored for their recyclability, flexibility, and versatility across industries. The injection molding process is commonly used for thermoplastic polymers, allowing for efficient production of high-quality parts.
Understanding the differences between these two types of polymers is crucial for plastics professionals. Whether selecting materials for automotive components, electrical housings, or consumer goods, knowing when to choose thermoset plastics versus thermoplastic materials can make all the difference in the performance and longevity of the end product.