Demanding industrial conditions require materials that refuse to fold under extreme heat. High temperature plastic shines in such scenarios, excelling where ordinary polymers fail. Expect insights into their capabilities, such as enduring elevated temperatures without losing mechanical strength. This guide is crafted for those who prioritize performance when the temperature climbs using high temperature plastic.
Key Takeaways
High temperature plastics are classified into amorphous and crystalline materials, with crystalline plastics offering superior mechanical strength, stiffness up to their glass transition temperature (Tg), lower friction, and excellent chemical resistance, making them suitable for industrial applications.
Continuous operating temperature, melting point, and heat deflection temperature (HDT) are crucial properties of high temperature plastics, impacting their long-term performance in high-heat applications. Materials like PTFE and PAI are favored for their ability to retain physical properties despite extended exposure to high temperatures.
Companies like Atlas Fibre lead in precision machining and custom manufacturing of high-performance plastics and thermoset composite materials, providing specialized solutions for industries that require precision components with high thermal resistance and mechanical properties.
Understanding the Plastics Pyramid: Amorphous vs. Crystalline
In the world of engineering plastics, we find the plastics pyramid. This classification system differentiates between amorphous and crystalline materials according to their molecular structure.
Amorphous plastics, which include varieties like polystyrene, have the following characteristics:
They soften gradually as temperatures rise, lacking a defined melting point.
They’re known for their clarity and ease of processing.
They are less robust compared to their crystalline counterparts when it comes to mechanical strength and chemical resistance.
Contrastingly, crystalline or semi-crystalline plastics, such as polyamide, boast a sharp melting point and maintain their strength and stiffness up until they hit their glass transition temperature (Tg), above which they become more malleable yet maintain a structured form due to the presence of crystalline regions. This group of high performance plastics, including the likes of polyethylene and polypropylene, is revered for its toughness, low coefficient of friction, and superior chemical resistance, giving it an edge in a plethora of industrial applications.
Decoding High Temperature Plastics
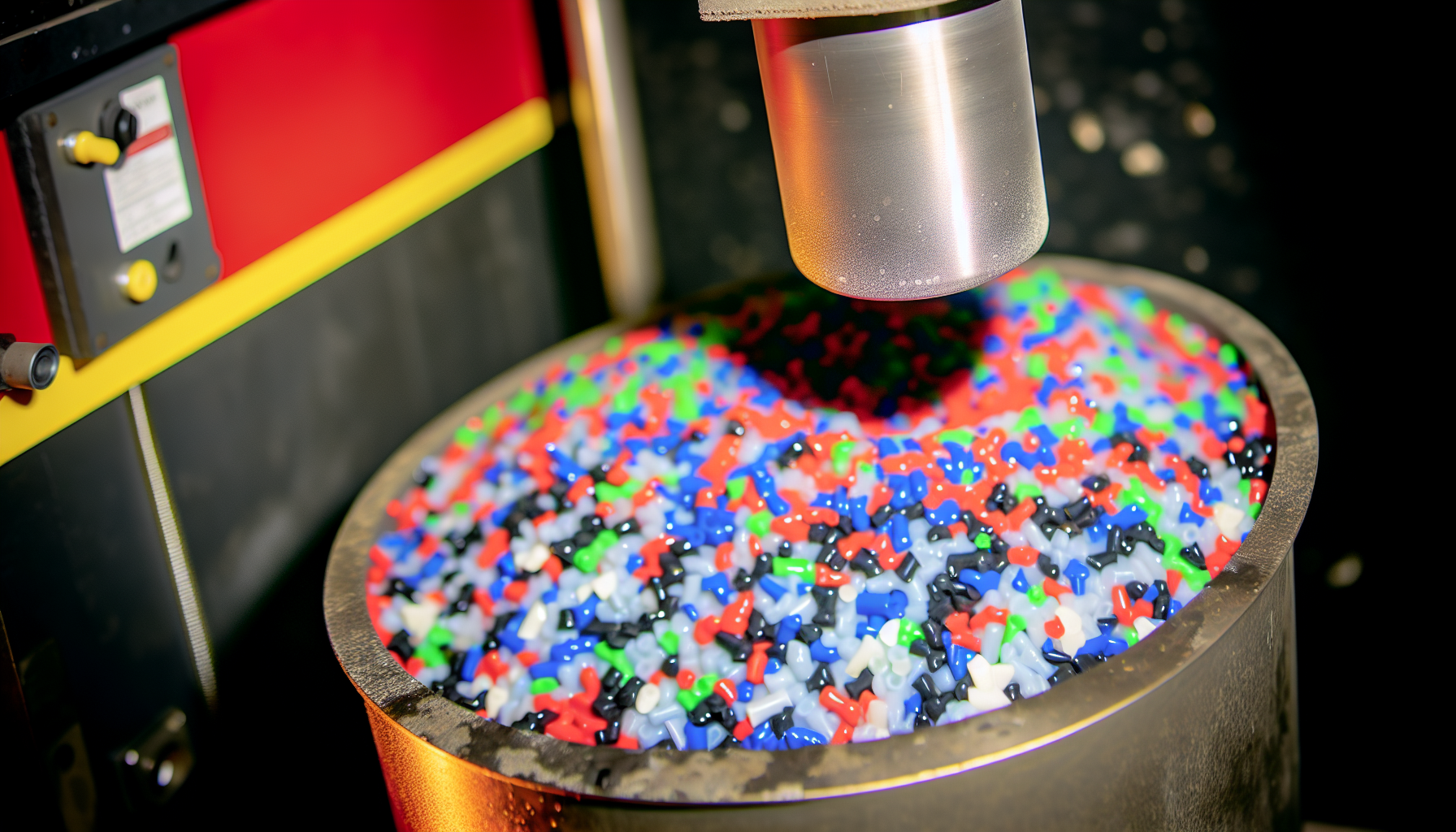
High temperature plastics refer to a group of heat resistant materials known for their ability to uphold structural integrity at high temperatures. Parameters such as heat deflection temperature (HDT), continuous service temperature, and melting point are the yardsticks by which these materials are measured. They are the heat resistant plastic champions, capable of performing under conditions that would compromise the integrity of other plastics.
The prowess of high performance thermoplastic materials is not limited to their capacity to withstand high temperatures; their mechanical properties, thermal resistance, and chemical resilience at these elevated temperatures are also paramount. In the subsequent subsections, these critical parameters will be thoroughly examined to uncover why specific plastics are considered superior in the thermal hierarchy.
The Importance of Continuous Operating Temperature
Envision a material withstanding a metaphorical decade-long fever without breaking a sweat. This exemplifies the continuous operating temperature, demonstrating a material’s long-term resilience against relentless heat. Specifically, it’s the highest ambient temperature a material can handle while retaining at least half of its initial physical properties after an impressive 100,000 hours, or over 11 years, of constant service. With extreme heat resistance, these materials prove to be invaluable in various industries and applications.
Materials like PTFE, with a continuous service temperature reaching up to 260°C, showcase a remarkable ability to remain stable under heat stress, although they may soften, which shouldn’t be mistaken for a loss in mechanical strength. This resilience is why plastics such as PAI, with continuous operating temperatures up to 270°C, are so prized in high-performance applications that demand longevity in the face of extreme temperatures.
Melting Point and Heat Deflection Temperature
As we shift focus from enduring heat to resisting pressure, the melting point and heat deflection temperature (HDT) prove to be pivotal indicators of a plastic’s resilience. HDT specifically gauges the temperature at which a plastic will start to deform under a specified load, rendering it a critical consideration for parts that will face light loads in high-heat scenarios. This parameter helps differentiate between various high temperature plastics by their ability to maintain rigidity when things get hot.
Yet, the melting point isn’t the only temperature-related transition worth noting. The glass transition temperature (Tg) signals a transformation in behavior—from ductile to brittle—which is central to understanding how a plastic will perform across different temperature ranges. It’s these thermal properties that inform the design and material selection for components that must operate reliably under the stress of high temperatures.
Chemical and Wear Resistance at Elevated Temperatures
Beyond mere heat resistance, high temperature plastics must often contend with aggressive chemicals and abrasive conditions. Semi-crystalline plastics shine in this arena, offering:
Chemical resistance that amorphous plastics can’t match, particularly under high temperatures and continuous loads
Superior stress-cracking resistance, making them ideal for applications involving recurring loads
Lower coefficients of friction and better wear resistance, making them the material of choice for parts in mechanical functions and machine designs.
These plastics are not just tough; they are chemically stoic, remaining inert in the face of harsh chemicals. PEEK, for instance, retains its properties in aggressive environments with excellent hydrolysis and steam resistance, positioning it as an indispensable polymer in fields ranging from medical devices to aerospace components. PPS, with its inherent flame resistance and balance of mechanical and thermal properties, demonstrates the kind of versatility required for a range of high-stakes industrial applications.
Atlas Fibre: Precision Machining of High Performance Plastics
Atlas Fibre, a name associated with specialized solutions and unparalleled expertise, leads in precision machining and custom manufacturing of high-performance plastics. This company’s dedicated machine shop is a hive of advanced CNC technologies, where each custom part is crafted with meticulous attention to detail. With an impressive 120,000 square feet of fabrication space, Atlas Fibre’s production capabilities are robust, ensuring high-quality parts that are as reliable as they are precise.
Atlas Fibre’s commitment to quality extends to its service, with a direct manufacturing approach that safeguards intellectual property and adheres to stringent quality controls. The company’s responsiveness, exemplified by its instant online quoting and same-day shipping for in-stock orders, underscores its dedication to customer satisfaction. When it comes to navigating the complexities of high-performance polymers, Atlas Fibre emerges as a trusted partner for industries seeking nothing less than excellence.
Thermoset Composite Materials: Beyond Thermoplastics
Moving beyond thermoplastics, we come across thermoset composite materials such as:
G10
FR4
G11
G3
These materials, known as heat resistant material, are lauded for their thermal resistance and stamina under extreme conditions, making them ideal for applications where thermoplastics might falter. Atlas Fibre, a titan in the industry, brandishes the largest inventory of thermoset composite materials in North America, setting the standard for supply and specialization in this field.
These specialty thermosets, including advanced epoxy resins, are employed in high-performance composites for sectors such as aerospace and automotive, where they deliver exceptional properties required by the demanding nature of these industries. With custom formulation and fabrication services, these materials can be tailored to meet the unique requirements of any high-temperature application, providing solutions that are as innovative as they are resilient.
G10 and FR4: High Performance Thermoset Workhorses
G10 and FR4 are the stalwarts among thermoset composites, with their glass-epoxy makeup granting them an esteemed status in high-temperature environments. The strength and dimensional stability these materials exhibit across a wide temperature spectrum are nothing short of impressive, making them indispensable in applications that demand high insulating capabilities and moisture resistance. G10, in particular, thrives in electric rotor insulation and terminal boards, while FR4 finds its purpose in the fire retardancy and insulation required for aerospace components and circuitry.
The versatility of these materials is showcased in their ability to maintain excellent mechanical properties under thermal stress, which is why they are often selected for connectors, standoff posts, and other components where structural integrity and electrical insulation are critical. G10 and FR4 embody the fusion of performance and reliability, serving as a testament to the capabilities of high-performance thermoset materials.
G11 and G3: Advanced Engineering Applications
G11 and G3 represent the next echelon of thermoset composites, engineered to endure the rigors of advanced engineering applications. G11 maintains its structural integrity well beyond the 300°F mark, making it a prime candidate for continuous operation in environments that would degrade lesser materials. G3, composed of woven glass cloth and high-temperature phenolic resin, can handle sustained temperatures of 350°F (175°C), showcasing a resilience that’s essential for high-temperature applications.
The applications for G11 and G3 are diverse, ranging from arc barriers and electrical insulators to high-strength structural components and parts within the high-demand oil and gas industry. The exceptional heat resistance and electrical insulation properties of these materials make them invaluable in sectors where failure is not an option, solidifying their reputation as advanced engineering marvels.
The Elite Five: Top Heat Resistant Plastics
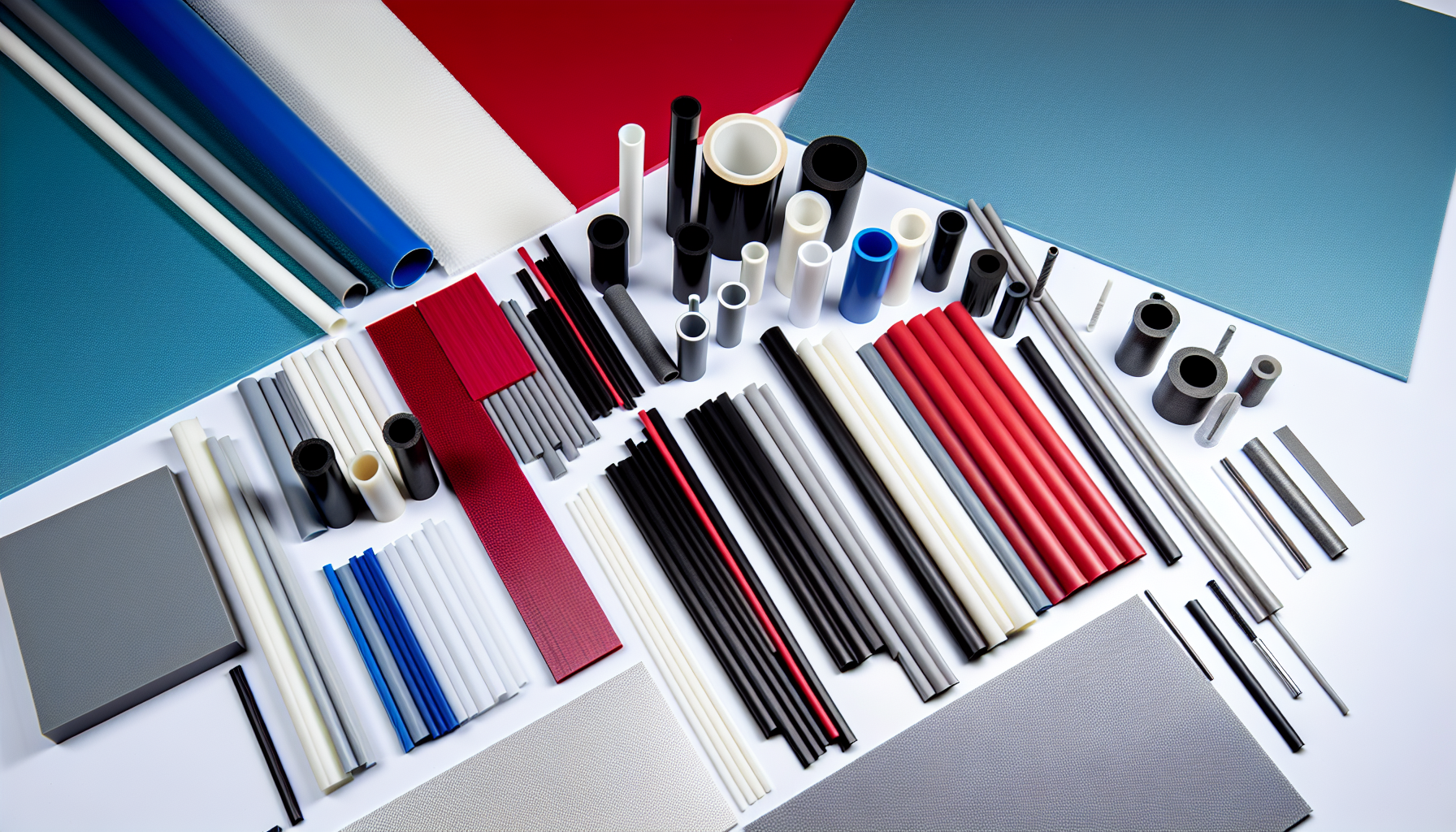
Among the vast array of heat resistant plastics, five materials are prominent for their exceptional ability to withstand extremely harsh thermal environments. These elite top 5 heat resistant plastics—PEI, PEEK, PTFE, PAI, and PPS—offer a spectrum of properties that cater to specialized applications, from aerospace to industrial heavy lifting. Each of these high-performance polymers brings its own unique strengths to the table, setting the bar high for what we can expect from engineering plastics.
Polyetherimide (PEI): The Aerospace Favorite
Polyetherimide, or Ultem, sits among the high echelons of aerospace materials, revered for its:
Dielectric strength
Resilience in the face of extreme heat With a continuous operating temperature of 340°F (171°C), PEI demonstrates its capability to maintain strength and rigidity under the duress of thermal stress, making it an invaluable asset in the aerospace industry. Its resistance to solvents and flames enhances its suitability for applications like:
Aircraft interior sheeting
Jet engine components where safety and performance are paramount.
Engineers in aerospace reach for PEI when they need a material that can handle the extraordinary demands of flight and space exploration. Its high glass transition temperature ensures that even in the upper echelons of the atmosphere, PEI components retain their integrity and functionality. This amorphous polymer, alongside others like PMMA and PC, illustrates the diversity and capability of high-performance plastics in challenging environments.
Polyether Ether Ketone (PEEK): Medical and Oil and Gas Marvel
Polyether Ether Ketone, better known as PEEK, is a material that has proven its mettle across various demanding sectors, most notably in the medical field and oil and gas industries. Its key properties include:
Resistance to high temperatures—retaining properties above 482°F (250°C)
Resilience against radiation, chemicals, and hydrolysis
Ability to be autoclaved without degrading
These properties make PEEK a go-to material for devices that must endure rigorous sterilization processes, such as spinal implants and other fixation devices. PEEK’s durability and reliability in critical medical applications are well-established.
Beyond the operating room, PEEK’s robustness is equally valued in the oil and gas sector, where components must resist harsh conditions and maintain performance over time. Its versatility is showcased through applications that span from the depths of the earth in drilling components to the delicate intricacies of catheters. PEEK’s presence in these industries is a clear indicator of the extraordinary capabilities engineered into high-performance polymers.
Polytetrafluoroethylene (PTFE): The Non-Stick Pioneer
Polytetrafluoroethylene, or Teflon, has made a name for itself as the quintessential non-stick material. Its chemical inertness and exceptionally low friction make it the ideal candidate for applications where non-stick properties are essential, such as cookware coatings and chemical storage containers. PTFE’s innate wear resistance adds to its allure, allowing it to excel in roles that involve high wear or high friction scenarios.
The versatility of PTFE extends into its function as an additive, where it elevates the lubricity of other plastics. This property is particularly beneficial in applications such as bearings and gears that are subjected to continuous motion and stress, proving that PTFE is more than just a household name for cookware—it’s a pivotal player in the realm of high-performance polymers.
Polyamide Imide (PAI): Industrial Heavyweight
Polyamide Imide stands as an industrial colossus, with a mechanical strength that sets it apart from its counterparts. Exhibiting not just high tensile strength but also impressive flexural strength, PAI is a powerhouse in demanding applications where durability is key. Its resilience to gamma radiation enhances its utility in environments where radiation exposure is a concern, such as in nuclear facilities or industrial applications that require frequent sterilization.
The automotive industry, in particular, benefits from PAI’s robustness, incorporating it into parts that contribute significantly to vehicle strength and longevity. But it’s not just cars that reap the advantages of PAI’s superior properties; its overall robustness is sought after in a wide array of industrial settings, further cementing its status as a material of choice for those who demand metal-like durability in a lightweight, high-performance package.
Specialty Thermosets: Custom Solutions for Extreme Heat
When off-the-shelf materials falter under the blistering demands of extreme heat, specialty thermosets rise to the occasion. These custom-engineered materials are specifically tailored for applications where thermal stability, stiffness, and impact strength are non-negotiable. Epoxy resins, for instance, when cured with anhydrides, become powerhouses of high-temperature stability, capable of facing the most daunting thermal challenges head-on.
In the construction industry, these advanced thermosets contribute to the creation of components and surfaces that can resist corrosive substances and high temperature conditions without breaking a sweat. Designed to operate under very high temperatures, specialty thermosets retain their dimensional stability and corrosion resistance, ensuring their mechanical properties provide a reliable foundation for structures and systems that are exposed to severe conditions.
Enhancing Plastic Performance: Additives and Fillers
In the realm of high-temperature plastics, additives and fillers act as secret ingredients, turning good materials into extraordinary ones. Their role in enhancing the performance of plastics under high-temperature conditions cannot be overstated, as they improve thermal stability, chemical resistance, and mechanical strength. Thermal stabilizers and antioxidants, for instance, are additives that equip plastics with the resilience to counteract the degrading effects of heat and oxidation.
Fillers such as chopped glass fiber strands and ceramic powder can elevate the thermal resistance of plastics, but they may also influence their mechanical strength, underscoring the delicate balance between enhancing and preserving a material’s intrinsic properties. Glass and carbon fibers, in particular, not only augment the rigidity and toughness of thermoplastics but also contribute to their thermal deflection and electrical conductivity, showcasing the multifaceted benefits of these enhancements.
Selecting the Right Material for High Temperature Resistance
Given the wide array of high-temperature plastics available, choosing the right plastic materials requires thoughtful consideration. Environmental factors such as exposure to chemicals and water play a decisive role, as they can influence a material’s maximum continuous operating temperature and overall performance. The mechanical strength required at elevated temperatures is another critical factor, especially when considering the potential need for additives or fillers to bolster a material’s capabilities.
Cost, too, is a key consideration. Although high-performance polymers like PEI (Ultem®) and PAI (Torlon®) offer exceptional properties, they come with a corresponding price tag, and budget constraints must be weighed against performance requirements. For specialized applications, such as aerospace components that must endure prolonged exposure to high temperatures, the investment in specialty polymers like Torlon® is often justified by their superior performance and longevity.
Summary
Navigating the world of high-temperature plastics is like exploring a landscape where innovation meets endurance. From the foundational knowledge of the plastics pyramid to the cutting-edge applications of specialty thermosets, this guide has traversed the spectrum of materials that underpin critical industrial and technological advancements. Whether it’s the precision machining prowess of Atlas Fibre or the elite performance of PEEK and PAI, the common thread is clear: high-temperature plastics are pivotal in pushing the boundaries of what’s possible, and their strategic selection is central to the success of applications that operate in the heat of the moment.
Frequently Asked Questions
What is the highest temp plastic?
The highest temperature plastic is Polytetrafluoroethylene (PTFE) Plastic, which has a melting point of 620°F (327°C) and maintains its strength at temperatures as low as -450°F (-268°C).
Can plastic withstand 300 degrees?
Yes, there are high performance plastics that can withstand temperatures ranging from over 150 °C to over 300 °C, depending on the operating conditions.
How does Atlas Fibre contribute to the high-temperature plastics industry?
Atlas Fibre contributes to the high-temperature plastics industry through precision machining of high-performance plastics and maintaining a large inventory of thermoset composite materials, which allows for custom manufacturing solutions. This enables the industry to access specialized materials and customized manufacturing options.
What are some considerations when selecting a high-temperature plastic for an application?
When selecting a high-temperature plastic for an application, it’s crucial to consider environmental factors, mechanical strength requirements, budget constraints, and the specific demands of the application, such as long-term exposure to extreme temperatures or chemical exposure. These factors will help determine the most suitable material for the application.