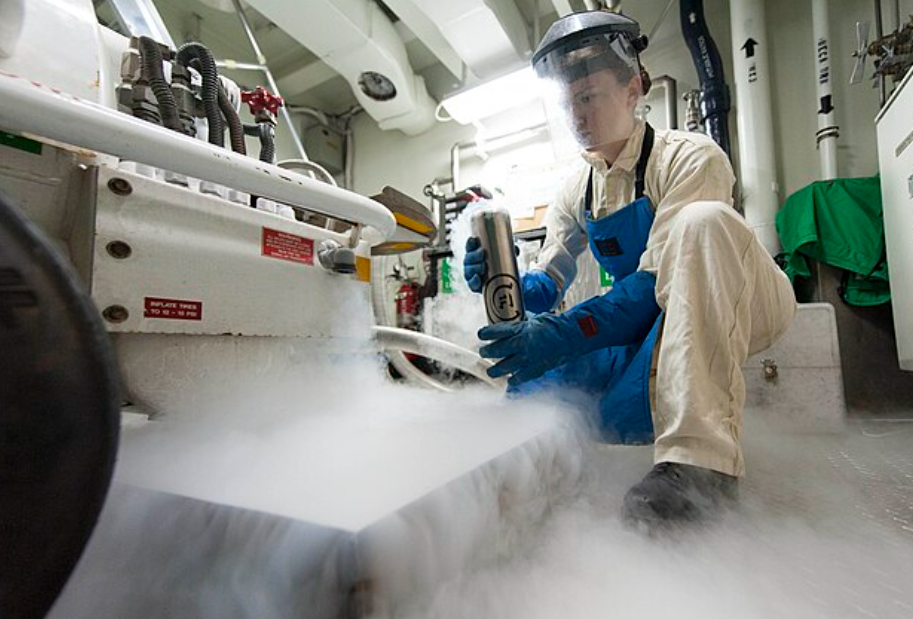
Performance, Properties, and Applications
When it comes to materials that must perform under extreme conditions, cryogenic epoxies stand out. The main reason? Their ability to function effectively at ultra-low temperatures. Among these, glass epoxy grades such as G10, FR4, and G11 are particularly noteworthy.
While they do not physically degrade when exposed to cryogenic temperatures, there is a measurable decline in their mechanical performance beginning at -55°C. Explore some of the challenges associated with cryogenic epoxies and why they deserve a closer look.
The Challenge of Testing Cryogenic Epoxies
Many commercial cryogenic epoxies are rated for a minimum operating temperature of -55°C, which is an important consideration during their development and testing. However, this rating is often more reflective of test equipment limitations rather than the actual capabilities of the material. In reality, high-quality cryogenic epoxy grades can operate far below this threshold, withstanding temperatures as low as -155°C to -270°C—well within the range of liquid helium.
G10-CR and G11-CR: A Deeper Look
Composite manufacturers specifically design G10-CR and G11-CR to endure cold temperatures, even though G10 and G11 are standard materials in the industry. However, it’s important to note that these materials are not identical to their standard versions. At cryogenic temperatures, the moduli (Young’s, shear, and bulk) of G10-CR and G11-CR increase, which can make these materials more brittle. This brittleness, in turn, can reduce their mechanical properties by as much as 20%.
Engineers formulate cryogenic epoxies with lower moduli, enabling them to maintain mechanical integrity even at the low temperatures associated with liquid gases.
Performance and Properties of G10-CR and G11-CR
G10-CR retains excellent electrical characteristics and physical properties at cryogenic temperatures as low as -270°C, with a continuous operating temperature of up to 140°C. Its low thermal conductivity value of 7.0 x 10^-4 calories/second/cm²/(°C/cm) makes it an efficient insulator, ideal for use in environments where minimizing heat transfer is crucial. G10-CR meets the standards for NEMA G-10, MIL-I-24768/2, Type GEE, and IEC-60893-3-1 EP GC 201.
G11-CR offers even higher physical properties than G10-CR at cryogenic temperatures, with the same excellent electrical characteristics. It can operate continuously up to 180°C, making it suitable for applications requiring a broader temperature range. Like G10-CR, G11-CR also features a low thermal conductivity value of 7.0 x 10^-4 calories/second/cm²/(°C/cm), ensuring its effectiveness as an insulator. This material meets the standards for NEMA G-11, MIL-I-24768/3, Type GEB, and IEC-60893-3-1 EP GC 203.
Cryogenic epoxies such as G10-CR and G11-CR are essential for applications requiring materials that can perform under extreme cold. While they differ from their standard counterparts, their ability to maintain mechanical and electrical properties at temperatures as low as -270°C makes them invaluable in industries ranging from aerospace to scientific research. With their excellent insulating properties and durability, cryogenic epoxies are a critical component in the development of advanced technologies that must operate in the harshest of environments.