If you’re evaluating materials for chemical-intensive applications, PEEK chemical compatibility is crucial. This article demystifies how PEEK stands up to a spectrum of chemicals, underlines its suitability for different environments, and offers a concise guide for selecting the right material.
Key Takeaways
PEEK polymer displays excellent resistance to a wide range of chemicals including acids, bases, and solvents, but it has limitations when exposed to sulfuric acid (concentrations >10%), methylene chloride, DMSO, and THF.
Temperature significantly affects the chemical compatibility and durability of PEEK; it shows stability at both high and low temperatures, with a max service temperature for Ketron 1000 PEEK at 250°C.
While PEEK generally outperforms common plastics like PVC and polyethylene in chemical resistance, it does have known incompatibilities with strong oxidizers and certain solvents; alternative materials should be considered based on specific environmental and chemical exposure.
Unveiling the Chemical Resistance of PEEK
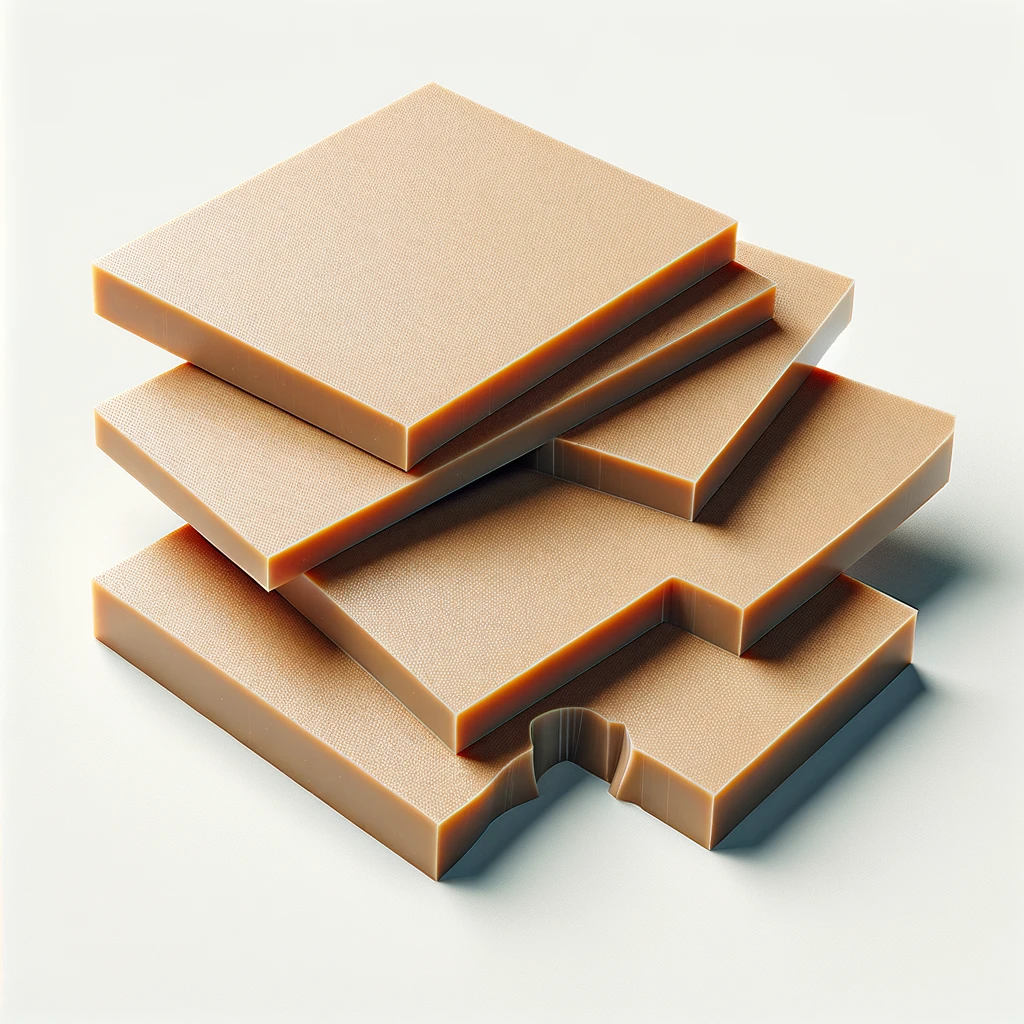
Recognized for its excellent chemical resistance across a variety of substances, PEEK polymer stands tall amongst other materials. This includes organic and inorganic compounds, showcasing its remarkable resistance to common substances such as acetic acid, methanol, and hydrochloric acid up to 37% over a 48-hour assessment period. While it may not be as chemically inert as PTFE, the robust resistance of PEEK to many harsh chemicals is what enables its utility in corrosive environments.
PEEK’s chemical resistance is more than just a feature; it forms the foundation of its widespread use in harsh environments. Imagine a material that can resist a wide range of chemicals – it opens up a world of possibilities. PEEK’s impressive resistance is more than a mere fact; it evidences the material’s versatility and utility.
Resistance to Acids and Bases
When it comes to resistance to acids and bases, PEEK is a showstopper. It exhibits excellent resistance to a wide range of acids, including acetic acid at concentrations of both 20% and 80%, hydrochloric acid at concentrations up to 37%, and hydrobromic acid. Its resistance extends to basic substances too, maintaining excellent resistance, doing particularly well with ammonia, ammonium hydroxide, and potassium hydroxide (caustic potash).
However, it’s important to note that while PEEK is a superhero in the face of acids and bases, it does have its kryptonite. PEEK is less resistant to sulphuric acid (also known as sulfuric acid) at concentrations greater than 10%, where it can be significantly damaged. Furthermore, it maintains integrity even at concentrations of 10% and 50% in temperatures up to 100°C (212°F) when exposed to sodium hydroxide. The key takeaway here is that while PEEK shows excellent resistance to many acids and bases, there are certain exceptions to consider.
Solvent Stability
PEEK’s impressive performance continues when it comes to solvent stability. Exhibiting high resistance to common solvents such as acetone, benzene, and methanol, PEEK is a reliable material in industrial applications. A shining example of its resilience is its excellent resistance to ethylene glycol, a solvent widely used in industrial applications.
However, like any superhero with its weakness, PEEK may swell when exposed to solvents like methylene chloride, dimethyl sulfoxide (DMSO), and tetrahydrofuran (THF). Swelling is a signal that caution should be exercised when using these solvents for cleaning PEEK, as they can affect the material’s integrity. Recognizing these limitations is vital to avoid unexpected damages to PEEK components.
Handling Halogens and Oxidizers
PEEK’s performance in the presence of halogens and oxidizers is a mixed bag. It is highly resistant to chlorine when in the form of dry gas; however, it suffers severe degradation with exposure to chlorine water and anhydrous liquid chlorine. Bromine also poses a considerable challenge to PEEK, causing severe degradation.
Despite these limitations, PEEK exhibits excellent resistance to concentrations of hydrogen peroxide up to 30%, showcasing its potential as an oxidizer-resistant material. However, for applications involving aggressive halogens, oxidizers like sodium peroxide, and those that exceed PEEK’s compatibility, alternative materials must be selected.
It’s all about finding the right material for the right environment.
The Impact of Temperature on PEEK Compatibility
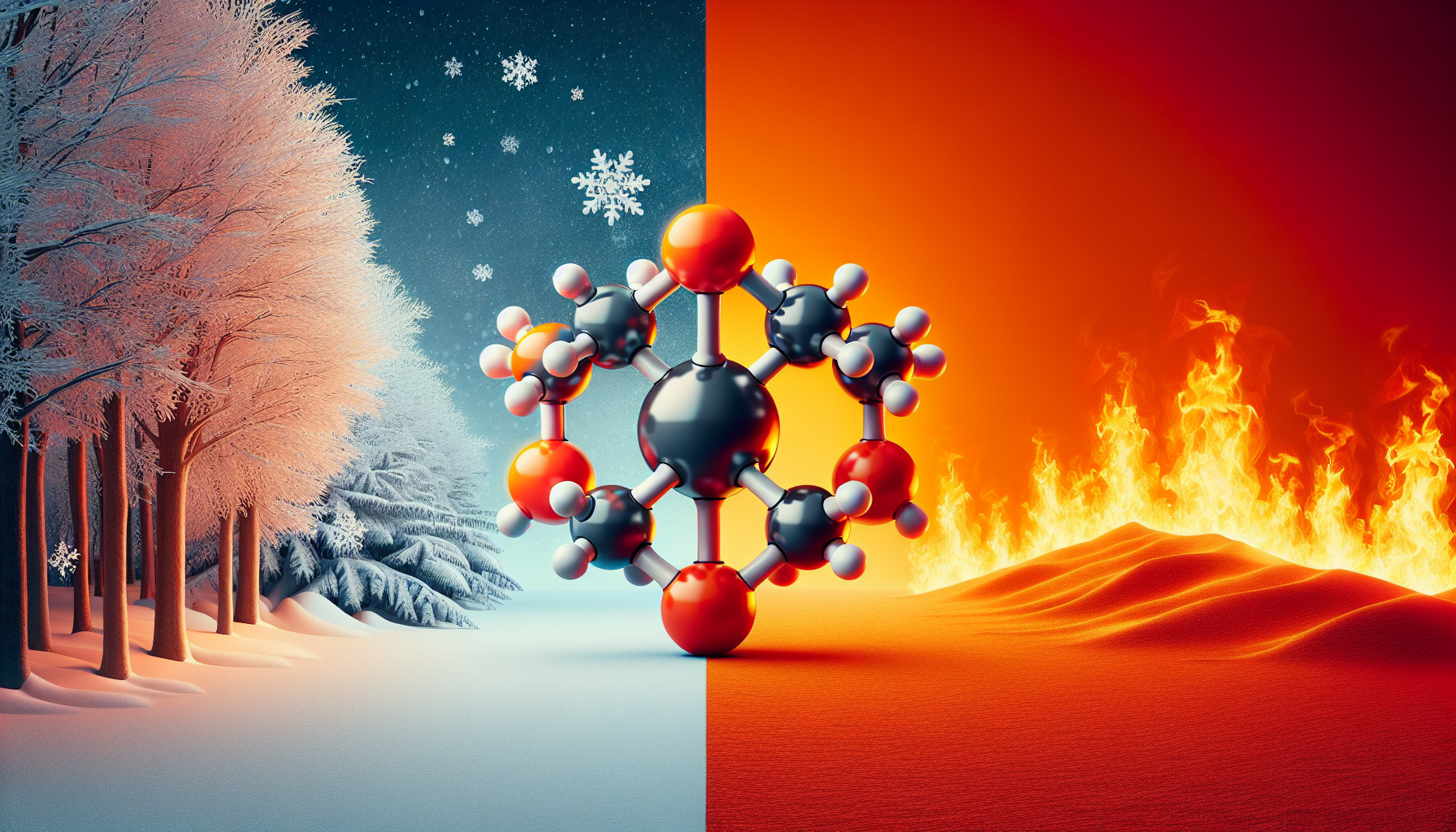
Temperature plays a significant role in the chemical compatibility of PEEK. With a melting temperature of 340°C as per ISO 11357-1/-3 and 644°F according to ASTM D3418 testing, PEEK demonstrates superior dimensional stability when subjected to temperature fluctuations. This lower coefficient of linear thermal expansion compared to materials like PTFE enhances its thermal stability across various temperatures.
Temperature’s effect on PEEK’s compatibility goes beyond impacting its performance; it also directly affects its durability and sustainability. A material that maintains its integrity despite fluctuating temperatures is a material built for the long run, built to resist, and built to last.
Low-Temperature Performance
PEEK’s performance at low temperatures is nothing short of impressive. Unlike many polymers, PEEK maintains strong chemical resistance even at low temperatures. For instance, it demonstrates stability without significant degradation when exposed to carbonic acid at low temperatures.
Even ammonium chloride at low temperatures has minimal impact on PEEK’s material properties, signifying its high resistance. The takeaway here is that PEEK’s impressive low-temperature performance is more than a mere feature, it’s an advantage that distinguishes it from many other materials.
High-Temperature Resilience
Equally impressive is PEEK’s resilience in high-temperature scenarios. Ketron 1000, a standard unfilled grade of PEEK, has a maximum allowable service temperature of 250°C or 320°F. This makes it suitable for high temperature applications. This resilience is evidenced further by the fact that PEEK tubing can safely withstand exposure to 20-30% nitric acid for system passivation purposes without degrading, a process that is detrimental to many other common plastics such as PVC.
However, resilience doesn’t imply invincibility. PEEK is attacked by higher concentrations of nitric acid, demonstrating an upper limit to its chemical resistance capability in elevated temperatures. Furthermore, despite undergoing alterations in its chemical structure when exposed to solvents like toluene, benzene, and THF, PEEK remains resistant to thermal attack, maintaining its physical properties after exposure to most solvents tested. Hence, even though PEEK excels in high-temperature scenarios, recognizing its limitations is equally important.
Comparing PEEK to Other Polymers
PEEK isn’t the only polymer on the block, but it certainly stands out. Known for its robust mechanical strength, PEEK’s tensile strength values of 90-100 MPa outperform PTFE’s 25-35 MPa, inferring metal-like durability suitable for strenuous applications. The structural integrity of PEEK is maintained under heavy loads, stress, and impact due to its superior creep resistance when compared to other common engineering plastics.
Moreover, PEEK displays a low coefficient of linear thermal expansion relative to other common engineering plastics, enhancing its thermal stability across various temperatures. When exposed to aggressive chemicals that may cause wear, PEEK’s high abrasion resistance is advantageous, making it a more robust option than materials like polypropylene, which exhibit lower abrasion resistance. It’s safe to say that PEEK is in a league of its own.
Benchmarking Against Common Plastics
When benchmarked against common plastics like PVC and polyethylene, PEEK’s chemical compatibility shines bright. It outperforms these materials when exposed to acetic acid, lactic acid, oxalic acid, and even phosphoric acid, showing no degradation at various concentrations. Even in the face of oleic acid, where PVC and polyethylene can soften or degrade, PEEK remains unaffected, ensuring its integrity in environments where these acids are present.
PEEK also flexes its muscles in the presence of a range of alcohols, such as ethyl and methyl alcohols, whereas PVC can become brittle or crack when exposed to these chemicals. The crucial point here is that PEEK’s chemical compatibility doesn’t just surpass other polymers, but it also guarantees its consistent performance across a variety of conditions.
Specialty Applications
PEEK’s unique properties and high resistance to various chemicals make it suitable for specialty applications. Its resistance to ferric chloride, for instance, is rated as good (B), demonstrating its applicability in scenarios where exposure to this chemical is expected, and where common plastics like PVC would not suffice due to corrosion. It also showcases excellent (A) chemical resistance in the presence of potassium carbonate, underlining its utility when high chemical resistance is essential for optimal performance.
Furthermore, research into the functionalization of PEEK surfaces has aimed to boost its osteoinductive and antimicrobial properties, further augmenting its role in specialized medical applications. From general use to specialized applications, PEEK’s superior properties make it a reliable choice.
Real-World Applications of PEEK’s Chemical Compatibility
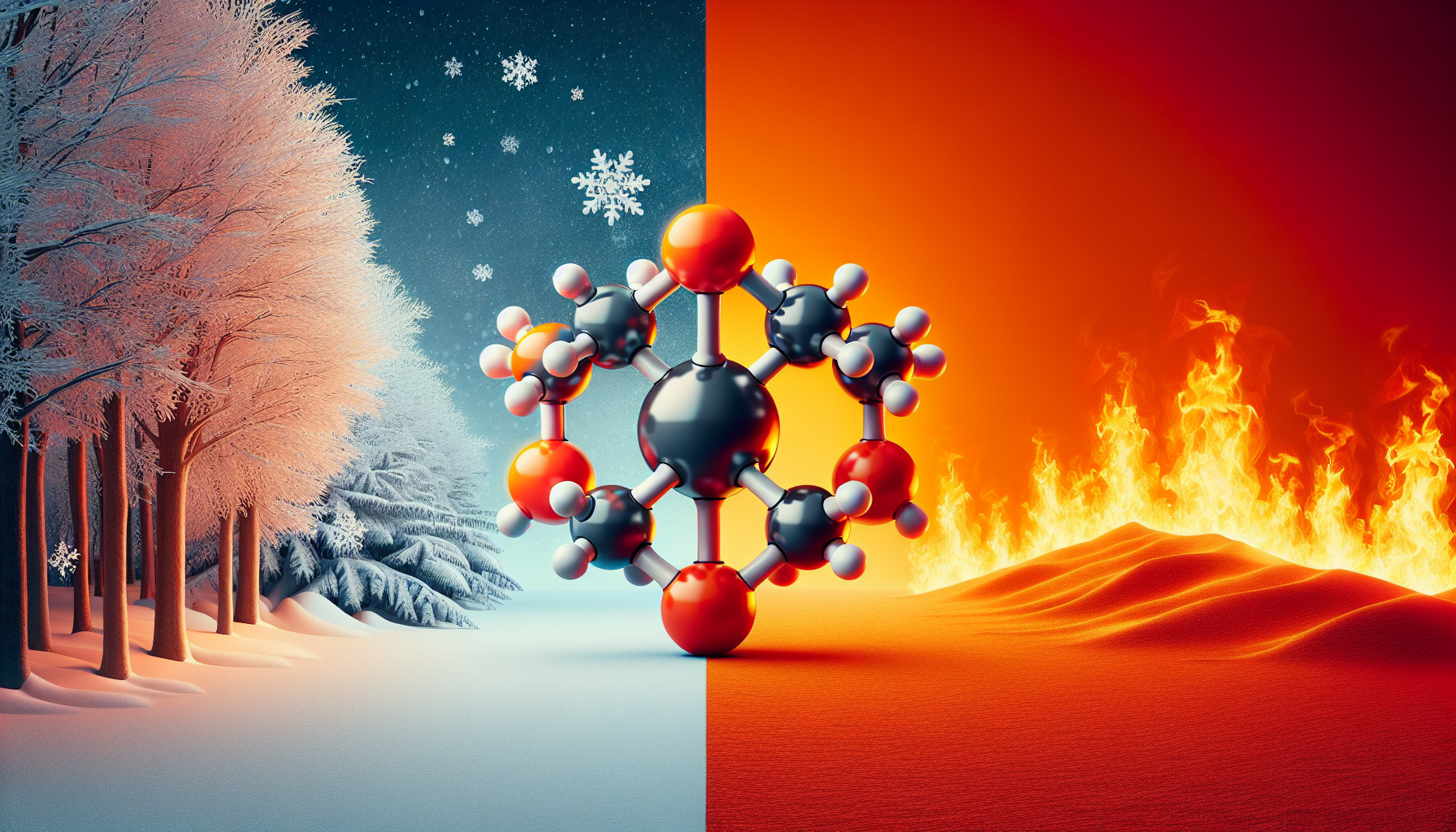
The real-world applications of PEEK’s chemical compatibility are vast and varied. For example, Ketron® TX PEEK was used to replace nacelle slider track mechanisms in aircraft, extending their lifespan and efficiency. Its high-temperature resistance and stability in jet engine environments contribute to its importance in aerospace applications.
In the automotive industry, PEEK’s robust chemical resistance makes it ideal for parts that encounter lubricants, coolants, and fuels. Whether it’s in producing seals, gaskets, and bearings for aerospace and automotive sectors, or in spine surgery, orthopedic surgery, and maxillofacial surgery in the field of medicine, PEEK’s chemical compatibility is making a real-world impact.
Medical and Pharmaceutical Use
In the medical and pharmaceutical sector, PEEK is making waves. Its biomechanically favorable properties have led to its use in various surgical fields including spine surgery, orthopedic surgery, and maxillofacial surgery. Specialized PEEK materials like PEEK-LT1, PEEK-LT2, and PEEK-LT3 have been developed to replicate bone and cartilage, making them valuable for medical implants.
Beyond skeletal repairs, the medical uses of PEEK extend further as these materials are being explored for a variety of other biomedical applications. The compatibility of PEEK with 3D printing technologies has also sparked scientific interest, potentially leading to advancements in personalized medical devices and implants. It’s no wonder that PEEK is a rising star in the medical field.
Aerospace and Automotive Sectors
PEEK’s remarkable performance also extends to the aerospace and automotive sectors. Its ability to resist various automotive fluids, including lubricants, coolants, and fuels, particularly in under-the-hood applications, makes it an asset in the automotive industry. In the aerospace sector, PEEK’s low outgassing properties are crucial as they prevent interference with sensitive equipment and instruments.
PEEK is used to manufacture critical components such as seals, gaskets, and bearings due to its chemical robustness and sustained performance, serving both aerospace and automotive sectors. It’s clear that PEEK’s chemical compatibility is playing a pivotal role in shaping the future of these industries.
Guidelines for Ensuring Optimal Performance
Ensuring optimal performance of PEEK components is crucial for the longevity of its applications. It goes beyond merely using the material; it’s about maintaining it. From cleaning and maintenance practices to storage considerations, proper care processes are essential for preserving PEEK’s integrity and performance.
These guidelines are more than just suggestions; they are crucial steps towards preserving the functionality and integrity of PEEK. After all, a material is only as good as the care it receives.
Cleaning and Maintenance
Cleaning and maintenance of PEEK materials require a gentle approach. Here are some recommendations:
Use soft cloths or brushes for cleaning PEEK components.
Use mild detergents for cleaning PEEK components.
Citric acid is a compatible and safe cleaning agent for PEEK, causing no significant harm to the material.
PEEK surfaces can also be effectively and safely cleaned using methods like the Sympro cleaning system and ultrasonic baths, as well as with soft to medium-hard toothbrushes. However, conventional air-abrasion with powders such as alumina and sodium carbonate can lead to increased surface roughness; therefore, such procedures should be approached with caution or avoided in favor of alternative gentle methods.
Before permanently installing PEEK equipment, it is crucial to test the chemical compatibility with planned cleaning agents under the specific conditions they will be used in.
Storage Considerations
When it comes to storage considerations, PEEK materials need to be:
Kept in cool, dry places
Kept away from incompatible chemicals and abrasive materials
Not in contact with abrasive materials during storage
Not subjected to cleaning methods that can significantly alter its surface characteristics, potentially impacting biofilm formation.
Storage areas for PEEK must be kept clean to avoid contamination that could compromise its material properties and subsequent application performance. Furthermore, in environments likely to have fluctuating temperatures, careful consideration must be given to the location where PEEK is stored to maintain optimal performance.
In summary, storing PEEK is as important as its application.
Navigating the Limitations of PEEK Compatibility
PEEK, as impressive as it is, does have its limitations. Understanding these limitations is crucial for selecting alternative materials when necessary. PEEK is vulnerable to strong bases such as sodium hydroxide and sodium silicate at high concentrations and temperatures. Strong oxidizers like concentrated sulfuric acid and concentrated nitric acid can compromise the structural integrity of PEEK.
Stress cracking is another concern when PEEK is exposed to halogens like chlorine under stress conditions. Moreover, continuous exposure to incompatible chemicals can lead to gradual degradation, affecting the mechanical properties of PEEK. Recognizing these limitations is the first stride towards identifying appropriate alternatives when PEEK is not up to the task.
Known Incompatibilities
There are certain chemicals that PEEK is known to be incompatible with. For instance, it demonstrates severe incompatibility when exposed to strong oxidizers such as chromic acid, wet bromine gas, wet chlorine gas, and fluorine. Amorphous PEEK is also less stable when subjected to organic solvents like chloroform, tetrahydrofuran (THF), toluene, benzene, and acetone, which can alter its chemical structure.
There is also no available data on PEEK’s resistance to hydrofluoric acid, suggesting that PEEK’s compatibility with this chemical is unknown and potentially variable. In contact with benzene sulfonic acid, benzoic acid, carbon bisulfide, and chlorosulfonic acid, PEEK also shows severe effects, underscoring its incompatibility with these aggressive chemicals. Knowing these incompatibilities is essential for maintaining PEEK’s integrity and performance.
Selection Criteria for Alternative Materials
When PEEK’s compatibility fails, it’s important to know how to select suitable alternative materials. Factors such as long-term stability in specific chemical environments, cost-effectiveness, and supplier credibility should be considered. Alternatives should be selected based on their ability to withstand conditions across the expected range of operating temperatures, especially when PEEK is compromised by chemicals, causing effects like swelling or attacks.
Selecting alternative materials is more than just finding a substitute. It’s about identifying a material that:
Delivers excellent performance
Provides cost benefits
Supports sustainable practices like recycling and reusability
Is sourced from a reliable supplier with a track record of solid after-sales support
It’s about ensuring optimal performance, even when PEEK isn’t the best fit.
Summary
In conclusion, the chemical compatibility of PEEK is a testament to its versatility and wide range of applications in various industries, from aerospace and automotive to medical and pharmaceutical. Its excellent resistance to a wide array of acids, bases, and solvents, combined with its robust mechanical strength, thermal stability, and dimensional integrity, make it a material of choice for demanding applications. However, like any material, PEEK has its limitations and incompatibilities, and it’s essential to understand these to ensure optimal performance and longevity of PEEK components.
Frequently Asked Questions
Which chemical is compatible with PEEK?
PEEK is compatible with most solvents used in HPLC, except for concentrated nitric acid and sulfuric acids, although it can withstand 20-30% nitric acid when passivating a system. Methylene chloride, DMSO, and THF may cause swelling in PEEK.
Is PEEK chemical compatibility with DMSO?
Yes, PEEK is chemically compatible with DMSO and does not adversely affect PEEK fittings. Therefore, it can be used with DMSO without concerns.
What is chemical compatibility chart?
A chemical compatibility chart is a tool used to determine the suitability of materials for use with different chemicals, helping to ensure safe and effective use.
What is PEEK’s resistance to acids and bases?
PEEK possesses excellent resistance to a wide range of acids and bases, although it is less resistant to sulfuric acid at concentrations higher than 10%.
How does temperature impact PEEK’s chemical compatibility?
Temperature significantly affects PEEK’s chemical compatibility. PEEK exhibits strong resistance at various temperatures, but may have limitations when exposed to certain chemicals.